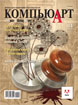
Во глубине печатных форм…
Несомненным достоинством глубокой печати является ее высокая скорость, достигаемая благодаря использованию красок на основе летучих растворителей, обеспечивающих достаточно быстрое их закрепление. Глубокая печать дает наиболее точное воспроизведение на оттиске цветовых и градационных параметров изображений оригинала, что позволяет воспроизводить однокрасочные и многокрасочные оригиналы буквально с фотографической точностью.
Сегодня глубокая печать применяется при производстве крупных и средних тиражей упаковки для кондитерских и мучных изделий, мороженого. Особенно прочны позиции глубокой печати в сегменте, где требуется нанесение клея для холодной склейки, что на флексографских машинах выполнить невозможно.
Среди потребителей такой упаковки — крупные западные пищевые концерны (Nestle, Mars, Cadbury и т.д.), производящие шоколадные батончики и мороженое. Это может служить дополнительным аргументом для компаний, рассматривающих возможность покупки машин глубокой печати.
К глубокой печати можно отнести также глубокую автотипию и металлографию.
В настоящее время формы глубокой печати изготавливают преимущественно по технологии «компьютер — печатная форма» с использованием электронномеханических и лазерных гравировальных автоматов в качестве устройств вывода систем допечатной подготовки изданий.
Форма глубокой печати представляет собой стальной цилиндроснову длиной до 3,5 м, на который нанесен основной слой меди (рис. 1) толщиной 2 мм и тонкий рабочий слой (тиражная рубашка) толщиной 100 мкм. Для прочного сцепления основного медного слоя с поверхностью стального цилиндра методом гальванического осаждения создают тонкий слой никеля. Между основным и рабочим медным слоем наносят тончайший (около 1 мкм) разделительный электропроводный слой, например серебряный. Для увеличения тиражестойкости готовые печатные формы покрывают тонким слоем хрома (58 мкм).
Рис. 1. Структура поверхности формы глубокой печати
Цилиндроснова является базой для поверхности, на которой формируется изображение в процессе гравирования или травления. Имеются два типа цилиндровоснов: полые цилиндры и цилиндрывалы.
Полые цилиндры состоят из полого тела в виде стальной трубы и находящихся на краях стальных фланцев, запрессованных в ее тело. Стальные фланцы имеют расточенные отверстия. В печатной машине цилиндр устанавливается на ось, которая входит в отверстия стальных фланцев.
Полые цилиндры имеют меньшие размеры и легче, чем цилиндрывалы, отличающиеся более низкой стоимостью. Основной их недостаток состоит в том, что им присущи характерные погрешности, возникающие при размещении цилиндров на разных осях в процессе их подготовки, гравирования и печатания. При этом каждая ось привносит свои погрешности. Полые цилиндры часто используются для печатания на упаковочных материалах и в производстве других специальных видов печатной продукции.
Цилиндрывалы представляют собой единое целое со своей осью. В процессе подготовки к печати оси цилиндров устанавливаются в подшипники печатной машины. Оси цилиндров имеют так называемые цапфы, фиксируемые на каждом конце посредством горячей тугой посадки.
Основным преимуществом цилиндроввалов является то, что одна и та же высококлассная несущая поверхность подшипника работает как в печатной машине, так и при нанесении покрытий, подготовке цилиндров и их гравировании. Это обеспечивает высокую точность и стабильность печати. В настоящее время цилиндрывалы применяются в газетножурнальном производстве, для печатания на упаковочных материалах и специальной продукции.
Для печатания на упаковочных материалах могут использоваться алюминиевые цилиндрыосновы. Небольшая масса цилиндров значительно сокращает транспортные расходы и облегчает обращение с ними на производстве. В этих цилиндрах для большей стабильности фланцы с установочными отверстиями изготавливаются из стали.
Для изготовления небольших цилиндровоснов для печатания на упаковочных материалах применяются специальные пластмассы, цилиндры из которых могут заменить стальной полый цилиндр. С помощью специальной химической обработки их поверхность становится электропроводной и поэтому может быть покрыта медью. Полые цилиндры данного типа имеют небольшую массу, что делает их удобными в работе и хранении, а кроме того, очень дешевыми по затратам на транспортировку.
Внешняя сторона цилиндраосновы обрабатывается на токарном станке, который быстро вращает цилиндр вокруг его оси, в то время как резец перемещается по поверхности цилиндра, снимая с нее верхний слой. При этом снимается тонкая длинная стальная или медная стружка и остается обработанная поверхность с узором мелкой резьбы. Торцы цилиндра растачиваются под цапфы. Допуск на биение поверхности цилиндра составляет 1012 мкм.
В процессе печатания наибольшее давление ракельного ножа приходится на края цилиндра, поэтому для уменьшения его износа торцы цилиндров скругляют (радиус кривизны примерно 56 мм), а концам цилиндра придают форму небольшого конуса длиной примерно 10 мм с углом наклона 2°.
Цилиндроснова должен обладать высокой жесткостью и обеспечивать минимальный прогиб, то есть отклонение центра цилиндра от его геометрической оси под давлением печатного цилиндра.
Длинные цилиндры должны обладать большей структурной жесткостью, чем короткие. Например, прогиб длинного цилиндра, используемого для печатания газетножурнальной продукции, не должен превышать 0,15 мм.
При излишнем прогибе может возникнуть множество проблем, включая неравномерную печать и образование морщин на запечатанном материале, преждевременный износ деталей печатной машины, вибрации, меньший срок службы цилиндров и увеличение износа ракельного ножа.
С увеличением скорости печатания усиливаются ограничения на прогиб цилиндра. Прогиб в наибольшей степени зависит от двух параметров — диаметра и толщины стенок цилиндра, а также от его длины, конструкции и диаметра осей.
При печатании на повышенных скоростях должна быть обеспечена хорошая балансировка цилиндров. Разбаланс измеряется произведением массы тела на смещение его центра тяжести от оси вращения. Цилиндр может оказаться разбалансированным вследствие неоднородности любого из материалов, которые применяются при его изготовлении, или изза перераспределения масс, возникающего в результате его механической обработки.
Разбалансированные цилиндры ограничивают скорость печатания, поскольку они создают излишние вибрации, приводят к увеличению шума, износу подшипников и самих цилиндров, неравномерной работе ракельного ножа и неравномерной печати, а также оказывают негативное воздействие на механические узлы печатной машины.
Процесс балансировки выполняется посредством перераспределения масс цилиндра таким образом, чтобы его центр тяжести совместился с осью вращения. Для этого в торцах цилиндра сверлятся отверстия, которые затем закрываются пробками, имеющими большую или меньшую массу по отношению к материалу, который оказался высверленным. Балансировка новых цилиндров является одной из конечных операций их производства.
Подготовка формного цилиндра — длительный и сложный процесс, при котором используется гальванооборудование для наращивания на цилиндры медного, никелевого и хромового слоев, оборудование для механической обработки цилиндров: проточки и шлифования основного медного слоя и полирования поверхности тиражной рубашки, а также тележки и подъемные устройства для транспортировки и установки формных цилиндров.
Подготовка новых формных цилиндровоснов отличается большой длительностью (осуществляется в течение нескольких суток). На поверхности стального цилиндра нарезают рваную резьбу и после химической обработки (обезжиривания и декапирования) осаждают в гальванованне тонкий слой никеля. Операцией декапирования, то есть травления слабыми растворами кислот (серной, соляной и др.), с металлической поверхности перед электролитическим покрытием удаляют пленки окислов, образовавшихся в результате подготовительных работ. Благодаря этому электролитически осаждаемый в гальванованне металл прочно сцепляется с основой. На него в другой гальванованне наращивают относительно толстый основной слой меди.
Процесс наращивания этого слоя неоднократно прерывают для механической обработки поверхности с целью сохранения цилиндрической формы получаемого отложения.
Основной слой меди тщательно полируют на специальном станке и химическим способом осаждают на его поверхности тончайший (менее 1 мкм) слой серебра. Затем на этот слой наращивают электролитическим способом тонкий рабочий слой меди с последующим его шлифованием и полированием.
Подготовка цилиндровоснов, бывших в употреблении, занимает в несколько раз меньше времени. Она заключается в отделении старого медного рабочего слоя, обезжиривании основного слоя, его серебрении и наращивании рабочего слоя с последующим полированием. Электролитические процессы проводятся в автоматизированных гальванованнах при непрерывном вращении цилиндров и их полном погружении в электролит.
Цилиндроснова проходит через гальваноотделение в нескольких случаях. Вопервых, когда цилиндр, используемый для выполнения некой печатной работы, готовится к нанесению нового изображения для следующей печатной работы; вовторых, когда процесс печатания большого тиража прерывается для того, чтобы обновить слой хрома для предупреждения износа выгравированного изображения.
Печатающие элементы на формах глубокой печати в современных технологических процессах получают тремя основными методами: прямого электронномеханического или лазерного гравирования, непрямого (косвенного) лазерного гравирования с последующим химическим травлением.
Если цилиндры подлежат химическому травлению или электронномеханическому гравированию, тиражная рубашка изготавливается из меди, а если прямому лазерному гравированию — то из цинка. Толщина слоя цинка, который наносится на цилиндры, подлежащие лазерному гравированию, составляет около 55 мкм.
В печатной машине на форму набрызгивается или наносится валиком жидкая краска, излишки которой удаляются ракелем. Использование ракеля предопределило важную особенность форм глубокой печати — регулярную структуру пробельных элементов, служащих опорой для ракеля и предотвращающих удаление краски из печатающих элементов.
Печатающим элементом на форме глубокой печати является углубленная ячейка, от объема и размера которой зависит тональность оттиска.
На цилиндре глубокой печати выполняемые резцом или лазерным лучом углубления не могут соединяться между собой, тем более накладываться одно на другое, так как между соседними печатающими элементами обязательно должны оставаться перемычки, служащие опорой для ракеля. Таким образом, при гравировании для всего диапазона изменения тонов резец обязательно должен выйти из материала после образования каждой точки. При гравировании для изменения тона объем печатающего элемента меняется за счет изменения как глубины, так и площади его рабочей поверхности. Размеры пробельных перемычек для всех тонов также различны.
Печатающие элементы на цилиндре глубокой печати, образованные при электронномеханическом гравировании, имеют вид правильной четырехгранной пирамиды, основание которой располагается на поверхности цилиндра (рис. 2). Поверхность скошенных стенок печатающих элементов гладкая, что обеспечивает лучшее восприятие краски бумагой и устраняет осаждение остатков краски в углублениях печатающих элементов. Иллюстрационный и текстовый материал гравируются одновременно.
Рис. 2. Фрагмент формы глубокой печати после электронно-механического гравирования: а — светлых; б — серых; в — черных тонов
Для электронномеханического гравирования цилиндров глубокой печати успешно используются резцы с алмазными наконечниками.
Форма ячеек определяется профилем режущего инструмента, причем получаемые грани ячейки в направлении развертки образуют угол от 90 до 145°.
Режущий инструмент совершает синусоидальное колебательное движение с постоянной частотой в непосредственной близости от поверхности вращающегося цилиндра (рис. 3). Чем глубже входит резец в медный слой, тем более широкой и глубокой получается ячейка. Как только резец входит на меньшую глубину, ячейка становится более узкой и мелкой. Это приводит к трапецеидальной форме гравируемых ячеек в основании.
Рис. 3. Схема гравирования цилиндра алмазным резцом
Для обычных условий печатания размеры гравируемых ячеек изменяются в пределах от 30 до 350 мкм, а их глубина может достигать 130 мкм. Диапазон используемых линиатур находится в пределах от 20 лин/см (50 lpi) до 200 лин/см (500 lpi), «угол поворота» растровой структуры изменяется от 30 до 60°.
Ввиду растрового характера гравируемого изображения текст имеет несколько рваный контур. Поэтому если не принимать специальных мер повышения краевой резкости, то переход от белого к черному на гравированном цилиндре визуально будет представлять собой неровный зубчатый край. Поскольку ячейки ромбовидной формы соприкасаются в вершинах, вдоль края образуются «зазубрины». Для визуального выравнивания края очень часто в смежном ряду вдоль края гравируют ячейки меньшего размера. При необходимости эта операция осуществляется как в вертикальном, так и в горизонтальном направлении (рис. 4).
Рис. 4. Дополнительные ячейки для выравнивания края: а — горизонтального; б — вертикального; в — наклонного
Как и в других способах печати, в технологиях глубокой печати линиатура растра определяется количеством рядов ячеек, приходящихся на дюйм или сантиметр.
Глубина и размер по диагонали гравируемой ячейки находятся в определенной взаимосвязи: если при неизменной частоте гравирования изменить частоту вращения цилиндра, то форма и расположение ячеек меняются. При больших частотах вращения получается удлиненная, а при малых — сжатая сеть ячеек. Возникающий при этом угол «поворота растра» служит предпосылкой для снижения эффекта растискивания краски. С этой точки зрения для гравирования форм для различных красок предпочтительными являются следующие виды растра (рис. 5): для голубой и пурпурной — с удлиненными (рис. 5а) или сжатыми элементами (рис. 5б), для желтой — более грубый (рис. 5в), для черной — более тонкий (рис. 5г). Например, при заданном растре 70 лин/см эффективная линиатура соответствующих растров выглядит следующим образом: удлиненный/сжатый — 70, грубый — 58, тонкий — 100 лин/см. Использование тонкого растра существенно улучшает качество воспроизведения шрифтов.
Рис. 5. Растры для различных красок
Прямое лазерное гравирование заключается в абляции лазерным лучом формного материала на участках, соответствующих будущим печатающим элементам формы. Текстовая и изобразительная информация записывается непосредственно на цинковом слое посредством использования тепловой энергии пульсирующего лазерного луча. Каждый импульс лазерного излучения формирует одну ячейку за счет локального испарения цинка. Образующиеся пары материала удаляются с обрабатываемой поверхности с помощью управляемого воздушного потока, и следующие ячейки растровой структуры могут быть сформированы с такой же точностью. Воздушный поток через фильтры направляется в пылесборник. Лазерный луч как бесконтактный инструмент не подвержен какомулибо износу, а следовательно, гарантируется равномерность записи по всей поверхности цилиндра, что, в свою очередь, обеспечивает абсолютную повторяемость.
Покрытые цинком цилиндры гравируются в формовыводном устройстве инфракрасным лазером мощностью в несколько сот ватт. Возможна установка одной или двух лазерных головок: в первом случае максимальная скорость гравирования составляет 70 тыс. ячеек в секунду, что почти в 10 раз выше, чем при электронномеханическом гравировании; во втором случае скорость гравирования достигает 140 тыс. ячеек в секунду.
Благодаря возможности динамического регулирования мощности излучения и диаметра луча передача градаций может осуществляться за счет как изменения глубины ячеек, так и варьирования их площади (рис. 6).
Рис. 6. Фрагмент формы глубокой печати после прямого лазерного гравирования с передачей полутонов за счет варьирования: а — глубины и площади ячеек (полуавтотипный растр); б — глубины ячеек (традиционный растр глубокой печати)
Рис. 7. Формирование макроячеек при прямом лазерном гравировании путем комбинирования обычных ячеек
Возможно также формирование несколькими точками макроячеек (рис. 7). При максимальной линиатуре растра 220 лин/см это позволяет оптимизировать форму ячеек в зависимости от выполняемого заказа.
Достоинствами лазерного гравирования являются:
очень высокая скорость гравирования;
высокое разрешение записи;
возможность варьирования параметров растра.
Оптимизируя параметры формы под конкретный заказ, удается добиться не только повышения качества печати, но и экономии краски, а также сокращения времени на подготовку машины к печати. Недостаток у прямого лазерного гравирования один — очень высокая стоимость оборудования.
При непрямом (косвенном) лазерном гравировании происходит абляция масочного термочувствительного или светочувствительного слоя. Принцип такой цифровой технологии изготовления форм глубокой печати напоминает процесс цифрового экспонирования фотополимерных печатных форм для флексографии: покрытая маскирующим слоем поверхность формы экспонируется лазером, удаляющим маску с будущих печатающих элементов. Маскирующий слой (специальный черный лак) наносится инжекторным способом в отдельных установках. После нанесения лака необходима его сушка в течение 5 мин. В экспонирующих устройствах используются твердотельные, волоконные и полупроводниковые лазеры мощностью до 100 Вт. Для увеличения производительности процесса экспонирования применяются многолучевые системы. Максимальное разрешение записи — 5080 dpi. После экспонирования маски производится травление цилиндра, смывка поверхности формы и, наконец, ее хромирование.
К основным достоинствам косвенного лазерного гравирования можно отнести возможность использования тех же цилиндров, что применялись, например, для электронномеханического гравирования.
Рис. 8. Возможность улучшения качества изображения знаков
Рис. 9. Схема процесса получения форм глубокой печати по технологии «компьютер — печатная форма» методом прямого электронно-механического гравирования
Принципиальное отличие косвенного лазерного гравирования от электронномеханического — возможность создавать более четкие края букв за счет дополнительной контурной обводки (рис. 8а) или неполного воспроизведения ячеек (рис. 8б).
Процесс изготовления форм глубокой печати методом прямого электронномеханического гравирования состоит из следующих основных операций (рис. 9):
- механическая обработка стального цилиндраосновы на токарном станке;
- никелирование поверхности цилиндраосновы методом электролитического осаждения металла в гальванованне;
- наращивание основного медного слоя на цилиндроснову электролитическим способом в гальванованне;
- нанесение разделительного слоя на основной медный слой в специальной установке;
- нанесение рабочего медного слоя (тиражной рубашки) на цилиндроснову электролитическим способом в гальванованне;
- шлифование и полирование рабочего медного слоя на шлифовальнополировальном станке;
- передача цифрового файла, содержащего данные о цветоделенных изображениях полноформатного печатного листа, в растровый процессор изображения;
- обработка цифрового файла в РИП (прием, интерпретация данных, растрирование изображения с заданной линиатурой и типом растра);
- формирование (гравирование механическим резцом) углубленных печатающих элементов в рабочем медном слое цилиндра на электронномеханическом гравировальном автомате;
- получение пробного оттиска и проведение технической корректуры формы (при необходимости) на пробопечатном станке;
- хромирование медного рабочего слоя электролитическим способом в гальванованне;
- полирование поверхности формы глубокой печати на шлифовальнополировальном станке.
После операции гравирования, при необходимости, изготавливают пробные оттиски на тех же запечатываемых материалах, которые будут использоваться при печатании тиража, а также с применением печатных красок, которые по своим характеристикам сравнимы с тиражными красками. Для полноценной цветопробы газетножурнальной продукции требуется многосекционный пробопечатный станок. Большинство пробопечатных станков глубокой печати моделируют только однокрасочные печатные машины. Вместо печатного цилиндра используется барабан большого диаметра, покрытый резиновым полотном, на котором размещается запечатываемый материал. Формный цилиндр, для которого выполняется проба, приводится в контакт с барабаном или барабан подводится к цилиндру. На запечатываемый материал приходится два или три оборота барабана.
Излишки краски на поверхности формного цилиндра удаляются лезвием ракельного ножа, который действует, как в машинах глубокой печати.
С появлением методов цифровой обработки изображений и программного управления цветом многие типографии при выпуске газетножурнальной продукции отказались от пробопечатного станка, а стали использовать широкоформатные струйные принтеры.
Пробный оттиск выполняется для всех новых работ при печатании на упаковочных материалах и печати бесконечно повторяющихся узоров.
Если пробный оттиск не отвечает ожиданиям заказчика, требуется корректура. В некоторых случаях необходим более чем один цикл пробы и корректуры. Корректура выполняется вручную высококвалифицированными работниками. Поэтому проба и корректура цилиндров являются наиболее дорогостоящими и длительными операциями в процессе изготовления цилиндров.
Корректура на гравированном цилиндре может выполняться как до хромирования, так и после него. Перед любой операцией «плюс корректура» по хрому поверхность цилиндра, то есть пробельные элементы и поверхность стенок ячеек, должна быть закатана защитной краской. Затем ячейки в тех местах, которые не требуют корректурных исправлений, полностью закрываются лаком. Эта операция выполняется с помощью кисти и называется выкрыванием.
Затем проводят операцию «плюс корректура» путем стравливания хрома из незащищенных участков, удаляя до 57 мкм хрома в зависимости от толщины хромового покрытия. Далее производится травление меди хлорным железом до достижения требуемой глубины ячейки. Время выполнения операций «плюс корректура» зависит от химического состава травящего раствора. Когда корректура закончена, защитные слои лака и краски смываются соответствующим растворителем.
В начале операции «минус корректура» поверхность вокруг корректируемого участка выкрывается защитным лаком с помощью кисти. Затем участок корректуры обезжиривается, чтобы наносимый металл прочно сцепился с поверхностью пленки.
Корректурный процесс предназначен для удаления лишних печатающих элементов или повреждений цилиндра. Это электролитический процесс, в котором используется медный электрод, покрытый материалом, впитывающим электролит. Поверхность цилиндра является катодом, а ручной электрод — анодом. Медь наносится на медную поверхность, а осаждение на поверхность хрома требует предварительного нанесения никелевого подслоя. Эта операция может выполняться и в печатной машине.
Рис. 10. Схема процесса получения форм глубокой печати по технологии «компьютер —печатная форма» методом прямого лазерного гравирования
Процесс изготовления форм глубокой печати методом прямого лазерного гравирования включает следующие операции (рис. 10):
- механическая обработка поверхности стального цилиндраосновы на токарном станке;
- никелирование поверхности цилиндраосновы методом электролитического осаждения металла в гальванованне;
- наращивание основного медного слоя на цилиндроснову электролитическим способом в гальванованне;
- наращивание рабочего слоя цинка на цилиндроснову электролитическим способом в гальванованне;
- шлифование и полирование рабочего цинкового слоя на шлифовальнополировальном станке;
- передача цифрового файла, содержащего данные о цветоделенных изображениях полноформатного печатного листа, в растровый процессор изображения;
- обработка цифрового файла в РИП (прием, интерпретация данных, растрирование изображения с заданной линиатурой и типом растра);
- формирование (гравирование методом абляции цинка лазерным лучом) углубленных печатающих элементов в рабочем слое цилиндра на лазерном гравировальном автомате;
- очистка поверхности цилиндра в специальном устройстве;
- хромирование цинкового слоя электролитическим способом в гальванованне;
- полирование поверхности формы глубокой печати на шлифовальнополировальном станке.
Системы прямого лазерного гравирования более стабильны и предсказуемы, чем устройства механического гравирования с несколькими гравировальными головками, поскольку лазерные системы обеспечивают получение одинаковой толщины стенок и оптимальной формы ячеек по всей площади гравирования. Благодаря геометрической точности лазерного гравирования для заданной растровой структуры перенос краски точно определяется параметрами растровой структуры. Это ускоряет наладку печатной машины, включая точную регулировку подачи красок и растворителей.
Рис. 11. Схема процесса получения форм глубокой печати по технологии «компьютер — печатная форма» методом абляции масочного слоя с последующим химическим травлением
Процесс изготовления форм глубокой печати методом непрямого (косвенного) лазерного гравирования масочного слоя с последующим химическим травлением состоит из следующих основных операций (рис. 11):
- механическая обработка стального цилиндраосновы на токарном станке;
- никелирование поверхности цилиндраосновы методом электролитического осаждения металла в гальванованне;
- наращивание основного медного слоя на цилиндроснову электролитическим способом в гальванованне;
- нанесение разделительного слоя на основной медный слой в специальной установке;
- нанесение рабочего медного слоя (тиражной рубашки) на цилиндроснову электролитическим способом в гальванованне;
- шлифование и полирование рабочего медного слоя на шлифовальнополировальном станке;
- передача цифрового файла, содержащего данные о цветоделенных изображениях полноформатного печатного листа, в растровый процессор изображения;
- обработка цифрового файла в РИП (прием, интерпретация данных, растрирование изображения с заданной линиатурой и типом растра);
- нанесение термочувствительного слоя полимера на поверхность формного цилиндра инжекторным способом в специальной установке;
- лазерная запись изображения на поверхности формного цилиндра путем абляции масочного термочувствительного слоя в лазерном гравировальном автомате;
- химическое травление меди раствором хлорного железа в специальной ванне;
- удаление масочного слоя путем промывки, очистки и обезжиривания поверхности формного цилиндра в устройстве очистки;
- хромирование поверхности формного цилиндра электролитическим способом в гальванованне.
В качестве масочного слоя могут применяться светочувствительные материалы, которые наносятся тонким слоем на медную поверхность цилиндра и покрывают ее водорастворимым защитным слоем. После высушивания защитного слоя формный цилиндр готов к лазерному экспонированию. Лазер в процессе экспонирования воздействует на светочувствительный слой на участках, соответствующих пробельным элементам. После проявления изображения и промывки поверхности формы ее подвергают химическому травлению хлорным железом. Затем удаляют защитный слой и хромируют форму аналогично вышеописанному процессу.
Современные технологические процессы изготовления форм глубокой печати практически полностью автоматизированы. Оборудование для обработки цилиндров, никелирования, меднения, хромирования, шлифования и других операций объединяется в поточные линии, а громоздкие и тяжелые формные цилиндры последовательно передаются с одной операции на другую с помощью подвижных подъемниковтранспортеров.
Большинство операций выполняется в этих машинах с той или иной степенью автоматизации, включая кнопочное управление. В автоматической ванне меднения, например, оператору следует только предварительно задать длину и окружность цилиндра, выбрать требуемую толщину покрытия и нажать кнопку запуска. Далее ванна выполнит все необходимые операции, такие как регулировка анодов, заполнение резервуаров электролитов, расчет необходимых амперчасов, управление выпрямителем, а также подаст оператору сигнал, когда работа будет закончена. Такой же уровень автоматизации имеет современное оборудование для подготовки, нанесения покрытий и отделки цилиндров.
В современной мировой практике около 90% форм глубокой печати изготавливается методом электронномеханического гравирования, так как другие методы требуют более дорогостоящего оборудования.