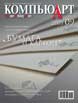
Офсетные полотна с компрессионным слоем
Зачем нужен компрессионный слой
Упруго-эластические свойства компрессионного слоя
После изобретения литографии Алоизом Зенефельдером плоская печать около ста лет оставалась прямым способом переноса краски на оттиск непосредственно с печатной формы. Офсет как способ непрямой плоской печати начал разрабатываться во второй половине XIX века, а первые плоскопечатные и ротационные офсетные машины появились в первом десятилетии ХХ века. Главным отличием плоской офсетной печати от литографии было использование для переноса краски промежуточной поверхности — офсетного цилиндра, обтянутого эластичным офсетным полотном. Благодаря эластичности офсетного полотна обеспечивалась качественная печать на твердых и неровных поверхностях без повышения износа печатной формы.
Сначала офсетные полотна изготавливались путем вулканизации резины. Точность изготовления при этом была низка, ибо таких понятий, как допуск на толщину или плоскостность, не знали в принципе. Однако рост требований к качеству печати, совершенствование печатной техники, разработка новых полимерных композиций со временем привели к прогрессу в области изготовления офсетных полотен, которые постепенно превратились из второстепенного аксессуара в продукты самых современных технологий.
Сжатие офсетного полотна без компрессионного слоя
Зачем нужен компрессионный слой
Первые резиновые офсетные полотна имели существенный недостаток — они выпучивались под действием давления (рис. 1), что обусловливалось упругостью резины. Результатами выпучивания были увеличение площади печатной зоны и возникновение таких дефектов печати, как скольжение (смазывание печатных элементов на оттиске) и дробление (двоение печатных элементов на оттиске). Теоретически выпучивание и увеличение печатной зоны можно минимизировать путем очень точного выставления зазоров между цилиндрами, однако на практике даже самые незначительные отклонения в толщине запечатываемого материала, печатной формы или офсетного полотна, а также погрешности печатающего механизма приводят к неконтролируемым изменениям площади печатной зоны. Поэтому уже в начале прошлого столетия стали разрабатываться способы стабилизации геометрических размеров офсетного полотна в зоне печатного контакта.
Сжатие офсетного полотна с компрессионным слоем
Решением проблемы стало включение в состав офсетного полотна компрессионного (сжимаемого) пористого слоя, способного деформироваться за счет выдавливания воздуха из пор, причем при деформации одного участка компрессионного слоя не происходит изменения объемов других участков, то есть выпучивание отсутствует (рис. 2).
В первом патенте на офсетное полотно с компрессионным слоем, принадлежащем компании Dunlop и датируемым 1918 годом, предлагался слой с открытыми порами. В 1935 году патентную заявку на полотно с промежуточным компрессионным слоем с закрытыми порами сделала британская компания Cow. В 50х годах офсетные полотна с промежуточным компрессионным слоем представила на рынок немецкая компания ContiTech.
Как показала практика эксплуатации офсетных полотен, компрессионный слой позволяет не только стабилизировать качество печати, но и повысить срок его службы за счет уменьшения нагрузок на другие слои офсетного полотна.
![]() |
![]() |
Структура полотна
Современное офсетное полотно состоит из нескольких тканевых слоев и лицевого слоя (рис. 3). Компрессионный слой помещается между слоями ткани. Тканевые слои образуют каркас, придающий жесткость офсетному полотну и предотвращающий его растяжение. Обычно используются хлопчатобумажные и синтетические ткани. В процессе изготовления полотна ткань калибруется в специальном валковом устройстве и из нее удаляются остатки воздуха.
Структура офсетного полотна с компрессионным слоем
Поверхностный слой офсетного полотна изготавливается из каучуков, которые должны отвечать следующим требованиям:
• хорошая способность воспринимать краску;
• стойкость к компонентам краски, смывочного раствора и других печатных и вспомогательных химикалиев;
• стойкость к механическим нагрузкам: сжатию, истиранию и т.п.
Поверхность офсетного полотна подвергается механической обработке: шлифованию и полированию. Гладкость поверхности должна быть такой, чтобы, с одной стороны, обеспечивалась хорошая краскопередача, а с другой — чтобы лист не прилипал и легко отделялся от нее.
![]() |
![]() |
Упруго-эластические свойства компрессионного слоя
Упругоэластические свойства компрессионного слоя характеризуются его сжимаемостью, которую принято оценивать по характеристической кривой зависимости деформации полотна от давления в зонах его контакта с формным и печатным цилиндрами (рис. 4).
Закрашенная зеленым область графика обозначает определенное эмпирическим путем в процессе исследований оптимальное давление печати 80100 Н/см2, при котором достигается максимальный перенос краски на глянцевые и матовые бумаги.
Характеристическая кривая 1 соответствует офсетному полотну без компрессионного слоя. Как видно на диаграмме, такое полотно обеспечивает оптимальное давление лишь в небольшом диапазоне деформаций. Отклонения толщин формы, бумаги или самого полотна ведут к недостаточному или избыточному давлению, что может привести к неравномерной оптической плотности отпечатка, к непропечатке или к повышенному износу формы, офсетного полотна и даже механизмов печатной машины. Положительным качеством офсетного полотна без компрессионного слоя является небольшая остаточная деформация.
Структура офсетного полотна с компрессионным слоем
Характеристическая кривая 2 соответствует офсетному полотну с компрессионным слоем, имеющим открытые и связанные между собой поры. Такое полотно обеспечивает оптимальное давление печати в большем диапазоне деформаций, чем первое полотно, однако по мере эксплуатации этот диапазон уменьшается в силу значительной пластической деформации компрессионного слоя. Для компенсации усадки полотна приходится повышать давление печати. Подобные полотна были широко распространены в 70е годы прошлого века, но сегодня большинство производителей отказались от их изготовления.
Характеристическая кривая 3 соответствует офсетному полотну с компрессионным слоем, имеющим закрытые несвязанные между собой поры. Как следует из диаграммы, полотно обеспечивает оптимальное давление в большом диапазоне деформаций и характеризуется гораздо большей стабильностью, чем второе полотно. В современных офсетных полотнах диаметр закрытых микропор составляет 5070 мкм.
Некоторые производители изготавливают компрессионный слой посредством внедрения в материал сфер из стекла или пластика. Такие компрессионные слои характеризуются очень низкой остаточной деформацией, однако их упругость оставляет желать лучшего.
Сжимаемость компрессионного слоя регулируется изменением его толщины и варьированием размеров микропор и давления в них.
Параметры офсетных полотен и методы их измерения
Характеристики офсетных полотен и методы их измерения описаны в стандартах DIN 16621 «Printing blankets for indirect planography» (офсетные покрышки для непрямой плоской печати) и ISO/DIS 12636 «Graphic technologyblankets for offset printing» (покрышки для офсетной печати).
Согласно DIN 16621 офсетное полотно, относительная деформация которого при нагрузке 100 Н/м2 больше 4,5%, следует считать компрессионным; если же деформация равна или меньше 4,5 %, такое полотно компрессионным не является.
Для тестирования сжимаемости офсетных полотен в стандарте ISO/DIS 12636 предложено два метода:
• сжатие образца полотна площадью 700 мм2 (используется производителями офсетных полотен из США и Японии);
• воздействие на образец полотна штампом площадью 100 мм2 (используется европейскими производителями офсетных полотен).
К сожалению, многие важные для практиков величины в стандартах DIN 16621 и ISO/DIS 12636 не нормированы, поэтому изготовители полотен разрабатывают собственные нормативы. Например, компания ContiTech в 1990 году установила следующие допуски для своих полотен:
• отклонение по толщине — не более 0,02 мм ;
• отклонение от плоскостности — ± 0,015 мм ;
• остаточная деформация — не более 2 % или 0,04 мм ;
• относительная сжимаемость — 7,59,0% (в зависимости от марки полотна) с допуском ±2%.
В материале использованы
иллюстрации компании ContiTech.
![]() |
![]() |