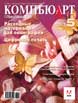
Влияние печатно-технических свойств ОРТП на качество печати и тиражестойкость офсетного декеля
Набухание краскопередающего слоя в растворителях и краске
Твердость и толщина резинового краскопередающего слоя
В ранее опубликованных статьях этих же авторов «Почему “разбиваются” печатные машины» и «Как повысить тиражестойкость офсетного декеля» в КомпьюАрт № 3 и 4’2007 рассматривалось влияние жесткости и упругоэластических свойств офсетных резинотканевых пластин (ОРТП) на качество печатной продукции и тиражестойкость офсетного декеля, а также были даны рекомендации по подбору офсетного декеля в условиях ограниченной информации о показателях деформационных свойств ОРТП и поддекельных материалов. В настоящей статье будет рассмотрена роль печатно-технических свойств ОРТП в офсетном печатном процессе, а также влияние этих свойств на качество печатной продукции и тиражестойкость офсетного декеля.
Под печатнотехническими свойствами ОРТП традиционно принято понимать свойства их верхнего резинового краскопередающего слоя. Сведения об этом слое до начала 90х годов ограничивались только природой используемых каучуков и характеристикой бумаг, формирующих краскопередающую поверхность резинотканевых пластин в процессе вулканизации. Однако анализ работы ОРТП отечественного и зарубежного производства показал, что существенную роль в нарушении стабильности офсетного печатного процесса, снижении тиражестойкости декеля и повышении времени простоя печатного оборудования также играют печатнотехнические свойства бумаги, красок и увлажняющего раствора.
Набухание краскопередающего слоя в растворителях и краске
Печатнотехнические свойства ОРТП, как ранее показали проведенные ВНИИ полиграфии исследования, определяются свойствами компонентов, входящих в резиновую композицию их краскопередающих слоев, — в первую очередь свойствами каучуков. Для изготовления краскопередающих слоев ОРТП в нашей стране и за рубежом1 используются в основном бутадиеннитрильные каучуки (СКН), свойства которых зависят от содержания в их молекуле нитрилакриловой кислоты (НАК). Эта кислота определяет степень набухания СКН в керосине и краске. Для определения оптимального по набуханию в краске и керосине каучука исследовались образцы слоев, изготовленных на каучуках СКН с содержанием НАК 18, 26, 30 и 40%.
Исследования показали, что с увеличением содержания НАК набухание каучуков СКН в керосине уменьшается (от 1,5 мг/см2 для СКН18 до 0,2 мг/см2 для СКН40, то есть в 7,5 раз), а набухание в краске увеличивается от 0,1 мг/см2 для СКН18 до 1,3 мг/см2 для СКН40. Различная степень набухания бутадиеннитрильных каучуков в этих средствах оказывает определяющее влияние на поведение ОРТП в процессе печатания, что подтвердили наблюдения за их работой в производственных условиях.
Высокая степень набухания в керосине печатающего слоя пластины типа Б2 (до 6 мг/см2), состоящего из бутадиеннитрильного СКН26 и бутадиенстирольного СКН30 каучуков, приводит к образованию рельефа на поверхности ОРТП высотой 0,50,6 мм, повышению давления печати и расслоению верхних слоев резинотканевого каркаса пластины. Применение же минимально набухающего в керосине каучука СКН40 позволило более чем на порядок
(с 6 до 0,2 мг/см2) снизить набухание пластины Дк, исключило ее расслоение и образование рельефа, что значительно повысило качество печати и тиражестойкость декеля.
Максимальное набухание каучука СКН40 (до 1,3 мг/см2) в компонентах краски по сравнению с каучуками СКН18, 26, и 33 (0,10,8 мг/см2) не вызывало образования видимого рельефа на поверхности пластин Дк, но проявлялось в увеличении ее липкости и, как следствие, в повышенном накапливании бумажных волокон, пыли и частиц мелового слоя. Все эти волокна и частицы в процессе печатания спрессовывались на поверхности пластины, образуя твердое покрытие, плохо воспринимающее краску и «обдавливающее» офсетный декель.
Такие явления наблюдались при использовании в декеле не только отечественных ОРТП, но и полотен ведущих зарубежных фирм. Характерно, что во всех случаях в сопровождающих документах отсутствовали показатели печатнотехнических свойств пластин, а также четкие рекомендации по использованию их при печати на различающихся по свойствам поверхности бумагах разными по композиционному составу красками. Это фактически исключало возможность комплексной оптимизации процессов офсетной печати на полиграфических предприятиях.
Таблица 1. Число компонентов краскопередающего слоя ОРТП, взаимодействующих с компонентами красок
Компоненты красок |
Офсетные резинотканевые пластины |
||||
Голубая фирмы Сow (Великобритания) |
Тип Пм
|
Тип Дк |
Образец на СКН-33 |
||
без обработки |
обработан хлорамином |
||||
Масло МП-3, 10%-ный раствор в гептане |
1 |
3 |
5 |
4 |
3 |
Льняное масло, 10%-ный раствор в гептане |
1 |
2 |
4 |
3 |
3 |
Алкид Д 4100, 10%-ный раствор в гептане |
1 |
4 |
4 |
3 |
3 |
Малеиновый ангидрид, 3%-ный раствор в толуоле |
1 |
4 |
4 |
4 |
3 |
Смола РЛ-41, 3%-ный раствор в толуоле |
2 |
4 |
3 |
2 |
2 |
Растворитель РПК-280 |
1 |
4 |
4 |
3 |
2 |
Канифоль, 3%-ный раствор в РПК-280 |
Изменения не обнаружены |
Изучение процесса набухания краскопередающих слоев отечественных и зарубежных ОРТП в компонентах краски в лабораторных и производственных условиях позволило предположить, что изменение поверхности резины происходит за счет ее химического взаимодействия с красками. Исследование этого процесса было выполнено с применением метода тонкослойной хроматографии. В ходе исследований краскопередающие резиновые слои истирались в порошок и смачивались компонентами красок, после чего на силуфольных пластинах в хроматографе наблюдалось изменение цветовой гаммы капель. Это свидетельствовало о взаимодействии каждого компонента краски с одним или более компонентами каждой изученной композиции краскопередающих слоев ОРТП. Исследовались пластины Дк, лицензионная ОРТП Пм и опытные образцы ПМН1 на основе новых каучуков СКН33 в сравнении с наиболее стабильно работающей на наших предприятиях голубой пластиной фирмы Cоw (Великобритания). Результаты исследований (табл. 1) показали, что от одного до пяти компонентов резиновой композиции краскопередающих слоев исследованных ОРТП вступают в химическую реакцию с компонентами красок, в результате чего изменяются состав и свойства как резины, так и краски. Это приводит к изменению печатнотехнических свойств резины и краски, что, в свою очередь, резко снижает качество печатных оттисков, а иногда вообще исключает возможность печатания.
Для повышения стабильности офсетного печатного процесса необходимо свести к минимуму число компонентов резиновой композиции печатающего слоя ОРТП, которые вступают в химическую реакцию с компонентами печатных красок, используя каучуки с оптимальными значениями набухания в смывочных растворах (0,61,0 мг/см2) и в связующих печатных красок (0,60,8 мг/см2). Близкие значения набухания имеет отечественный каучук СКН33, который применяется для изготовления краскопередающих слоев резинотканевых пластин нового поколения ПМН1 и ПМН2.
Отечественные резины СКН и зарубежные NBR на основе бензо и маслостойких бутадиеннитрильных каучуков используются для изготовления краскопередающих слоев ОРТП, предназначенных для листовой и рулонной печати на бумаге и картоне только традиционными печатными красками. Для печатания УФкрасками за рубежом разработаны специальные офсетные резинотканевые пластины с печатающим слоем на основе резины EPDM (этиленпропилендиенмономер)3. При печатании на невпитывающих материалах (пленка, монометаллическая фольга и др.) применяются специальные ОРТП с печатающим слоем, изготовленным из полиизобутилена.
Все три перечисленных типа ОРТП в настоящее время предлагаются на рынке полиграфических материалов, однако их не всегда можно верно идентифицировать по рекламным материалам инофирм изза некачественного перевода проспектов на русский язык, отсутствия в них показателей печатнотехнических свойств ОРТП или изза недостаточно высокой квалификации менеджеров по продажам.
Таблица 2. Характеристики ОРТП для УФ-красок
Фирма-производитель (страна) |
Наименование ОРТП |
Толщина ОРТП, мм |
Печатно-технические свойства краскопередающего слоя ОРТП |
Деформационные свойства ОРТП при давлении печати 80 Н/см2 (8 кГс/см2) |
||||||
Толщина краскопередающего слоя, мм |
Твердость в ед. Шора А0 |
Микрогеометрия поверхности (шероховатость, Ra, мкм) |
Набухание в смеси УФ-краски и смывочного средства, мг/см2 |
Суммарная деформация сжатия (жесткость Е сум), % |
Доли деформации ОРТП в суммарном сжатии Есум, % |
|||||
Еупр |
Еэл |
Еост |
||||||||
Kinyo (Япония) |
Air Excel Apollo UV (темно- сиреневая) |
1,97 |
0,30 |
79 |
1,5 |
0,04 |
4,3 |
69,4 |
7,8 |
22,8 |
Fujikura (Япония) |
FS-100 UV (серая) |
1,94 |
0,40 |
82 |
1,1 |
1,02 |
4,4 |
68,2 |
6,8 |
25,0 |
FS-70 (синяя) |
1,94 |
0,30 |
79 |
1,0 |
19,46 |
4,7 |
70,0 |
7,2 |
22,8 |
|
Phoenix (Германия) |
Ruby (красная) |
1,96 |
0,40 |
78 |
1,0 |
1,04 |
5,5 |
61,6 |
9,4 |
29,0 |
Reeves (Италия — США) |
Vulkan UV (фиолетовая) |
1,96 |
0,35 |
80 |
0,7 |
2,33 |
4,5 |
69,7 |
7,9 |
22,4 |
Vulkan combo (голубая) |
1,96 |
0,35 |
80 |
0,7 |
23,0 |
5,1 |
72,1 |
10,2 |
17,7 |
|
Cow-Dunlop (Великобритания) |
TR Turquoise (синяя) |
1,95 |
0,25 |
76 |
1,0 |
23,9 |
5,8 |
72,3 |
8,6 |
19,1 |
С проблемой выбора ОРТП для печатания УФкрасками столкнулись технологи фирмы «ЭПО» при подборе резинотканевых пластин для рулонной машины Gallus T250. Использование резинотканевых пластин старого поколения Ruby фирмы ITG (Германия) с низкими показателями деформационных свойств (табл. 2) в тяжелых условиях печатания на этой рулонной машине приводило к резкому снижению тиражестойкости декеля изза его недостаточной устойчивости к механическим нагрузкам. При этом к печатающей поверхности резинотканевой пластины претензий не было.
С целью повысить тиражестойкость декеля на Gallus T250 по рекомендации фирмизготовителей были испытаны современные ОРТП TR Turquoise фирмы CowDunlop (Великобритания) и FS70 фирмы Fujikura (Япония). Деформационные характеристики этих пластин были измерены в лабораторных условиях (см. табл. 2), и полученные показатели в полной мере соответствовали современным требованиям. При этом данные пластины были рекомендованы для печатания как УФотверждаемыми, так и традиционными красками. Однако при печатании УФкрасками фирмы Hostmann Steinberg (Германия) и использовании смывочного средства UV Wash компании Xsys Print Solution было отмечено повышенное набухание верхнего краскопередающего слоя ОРТП и резкое снижение качества оттисков, в результате чего пластины были сняты с машины через два и четыре дня соответственно. Изза неудовлетворительных печатнотехнических свойств эти пластины выходили из строя быстрее, чем пластины старого поколения Ruby.
В связи с этим для определения величины набухания краскопередающих резиновых слоев ОРТП по методике ТУ 23590050242644796 были исследованы все испытанные в печати на машине Gallus T250 и рекомендуемые инофирмами резинотканевые пластины. При этом вместо керосина марки ТУ 38.401581, используемого для определения набухания краскопередающих слоев традиционных ОРТП на основе резин НКС и NBR, применялась смесь УФкраски (50%) и смывочного средства (50%).
Полученные результаты (см. табл. 2) позволили обоснованно выбрать ОРТП с оптимальным набуханием и улучшенными, по сравнению с пластиной Ruby, деформационными свойствами. Такой пластиной оказалась FS100 (серая) фирмы Fujikura (Япония). Она обеспечивает высокое качество печати и значительно повышает тиражестойкость офсетного декеля на этой машине.
Пластины, рекомендуемые инофирмами для печатания как УФотверждаемыми, так и традиционными красками, показали на порядок большее набухание краскопередающего слоя в смеси УФкрасок и смывочного средства и не выдержали испытания при печатании УФкрасками. Вместе с тем необходимо отметить, что все испытанные современные ОРТП на основе резины ЕРDМ, то есть предназначенные для печатания только УФкрасками, имели более низкие показатели деформационных свойств по сравнению с традиционными пластинами на основе каучуков НКС (см. табл. 2). Даже лучшие из испытанных ЕРDМпластин имели долю упругой деформации (Е упр) не более 6869% и долю остаточной деформации не менее 2225%. Повидимому, в настоящее время такие показатели являются потолком для ОРТП с краскопередающим слоем из ЕРDМ.
Проведенные в лабораторных и производственных условиях испытания ОРТП убедительно показали, что степень набухания краскопередающих слоев является важнейшей характеристикой печатнотехнических свойств ОРТП. Поэтому этот показатель должен обязательно присутствовать в сопровождающем ОРТП документе.
![]() |
![]() |
Твердость и толщина резинового краскопередающего слоя
Важными показателями печатнотехнических свойств ОРТП являются также толщина резинового краскопередающего слоя и его твердость. Последняя зависит от состава резины, в частности от введенных в нее добавок. В зависимости от особенностей поверхности и от жесткости запечатываемых материалов, верхний монолитный резиновый слой, как правило, имеет твердость от 65 до 85 единиц Шора А.
Очень важна толщина этого слоя, которая в идеале должна быть минимальной (0,100,15 мм), чтобы минимизировать искажения самых тонких печатающих элементов на оттиске вследствие поперечной деформации (расширения при сжатии монолитной резины с коэффициентом Пуансона µ=0,5). Препятствием при этом являются офсетные ткани, применяемые для изготовления резинотканевого каркаса ОРТП. В настоящее время самые тонкие из них позволяют снизить толщину краскопередающего слоя с 0,60 до 0,250,30 мм. Слои тоньше 0,200,25 мм передают при печати на оттиск структуру верхнего слоя ткани, поэтому оптимальная толщина краскопередающих слоев ОРТП при использовании ткани сегодня составляет 0,300,35 мм.
В процессе совершенствования конструкции резинотканевого каркаса ОРТП, то есть при замене в нем тканей на новые материалы и применении новых технологий, толщина монолитных слоев резины будет уменьшаться. Так, в середине 50х годов прошлого столетия в каркасе ОРТП один или два монолитных резиновых слоя были заменены на микропористые слои.
Толщина краскопередающего слоя должна обязательно приводиться в сопровождающем ОРТП документе. Однако при отсутствии этого показателя в документации грамотный технологполиграфист всегда сможет определить его значение с помощью микроскопа или лупы со шкалой.
Поверхностные свойства краскопередающего слоя
Еще одной важной характеристикой краскопередающего слоя ОРТП являются его поверхностные свойства. До середины 90х годов микрогеометрия поверхности ОРТП, как правило, формировалась в процессе вулканизации с помощью микроталька с определенной дисперсностью частиц и прокладочных бумаг с определенной микрогеометрией поверхности. При изготовлении ОРТП поверхность сырой (невулканизированной) резины краскопередающего слоя опудривалась микротальком и обертывалась бумагой, после чего резинотканевое полотно вулканизировалось в вулканизационном котле в течении 78 часов при температуре около 150 °C. После вулканизации поверхность краскопередающего слоя полностью повторяла микрогеометрию поверхности бумаги с Ra = 1,01,2 мкм и была практически гладкой. Пожалуй, только ОРТП японского производства имели полученную неизвестным способом матовую поверхность с Ra = 0,81,5 мкм.
В середине 90х годов европейские и североамериканские фирмы также перешли на выпуск ОРТП с матовой поверхностью, причем технология получения такой поверхности была строго засекречена. К этому времени в России были разработаны офсетные резинотканевые пластины нового поколения ПМН1 и ПМН2, но с гладкой поверхностью, сформированной по старой технологии. Поэтому возникла необходимость в определении преимуществ матовой печатающей поверхности ОРТП и в поиске способа получения такой поверхности. В рамках этой работы во ВНИИ полиграфии были выполнены исследования поверхностных свойств ОРТП фирм Reeves и Dow (США) с матовой и гладкой поверхностью.
При исследовании свойств матовой печатающей поверхности ОРТП измерялись показатель микрогеометрии Ra и величина краевого угла смачивания, который характеризует краскопередающую способность печатающего слоя. Таким образом определялось влияние микрогеометрии печатающей поверхности ОРТП на изменение ее смачиваемости, то есть на изменение величины краевого угла смачивания Q.
Зависимость равновесного краевого угла смачивания (Qm) на шероховатой поверхности от коэффициента шероховатости описана уравнением Венцеля — Дерягина:
cosQm = kЅcosQ0,
где Qm — равновесный краевой угол смачивания на шероховатой поверхности; k — коэффициент шероховатости; cosQ0 — равновесный краевой угол смачивания на гладкой поверхности.
Результаты исследования приведены в табл. 3, из котрой видно, что чем меньше значение Ra, тем меньше величина краевого угла смачивания и лучше красковосприятие. Это объясняется большей степенью развитости шлифованной поверхности пластин, имеющей меньшее значение Ra (0,8 мкм).
Таблица 3. Влияние микрогеометрии печатающей поверхности ОРТП на изменение ее смачиваемости
Тип ОРТП |
Шероховатость Ra , мкм |
Величина краевого угла смачивания, град. |
|
Нешлифованная поверхность |
Шлифованная поверхность |
||
Dow 8894 |
3,00 |
|
70-80 |
Dow 9500 |
1,94 |
|
65-70 |
Dow 8500 |
1,88 |
75-80 |
|
Dow 8894 |
1,42 |
|
60-65 |
Vulcan 714 |
0,80 |
50-55 |
55-60 |
Исследование печатающей матовой поверхности ОРТП под микроскопом показало, что она кардинально отличается от гладкой поверхности изготовленных клеевым способом пластин, которые имеют нерегулярную, неоднородную структуру с включением частичек талька и наполнителей резиновой композиции. Матовая же поверхность ОРТП имеет равномерную регулярно ориентированную микроструктуру без каких бы то ни было посторонних включений.
Печатающая резиновая поверхность ОРТП является полимерным материалом, характеристики которого связаны с химическим составом и наличием на его поверхности активных, способных вступать в реакцию функциональных групп. Такие реакции, протекающие на поверхности полимерных материалов, относятся к поверхностным явлениям, возникающим в результате взаимодействия контактирующих фаз. В поверхностных слоях ОРТП при контакте с печатной краской взаимодействуют фазы, имеющие различные связи атомов и молекул, в результате чего образуются поля ненасыщенных межатомных межмолекулярных сил. Поверхностные явления особенно четко проявляются в телах с высокоразвитой матовой поверхностью, что, повидимому, способствует более полному и равномерному распределению краски на матовой печатающей поверхности ОРТП по сравнению с ОРТП с гладкой поверхностью.
Известно, что полимеры претерпевают изменение своих физикохимических свойств под воздействием таких факторов, как температура, агрессивные среды, облучение, а также различные механические воздействия. В связи с этим одним из условий выбора метода модифицирования печатающей поверхности ОРТП было сохранение максимально стабильного состояния резинового слоя и однородности его свойств. Это исключило способ химического воздействия на поверхность краскопередающего слоя ОРТП. Предпочтение было отдано механическому способу модификации печатающей поверхности ОРТП — шлифованию, при котором не происходит химического изменения структуры резины, что подтверждается сохранением цвета шлифованной поверхности (не вызывается деструкция полимера), а также отсутствием изменения физикохимических (степени набухания) и деформационных свойств. Процесс шлифования печатающей поверхности проводится в нормальных условиях: температура 2025°С, влажность — 6065%, при этом кратковременные механические воздействия — сжатие, трение, срез — не приводят к структурным изменениям резины печатающего слоя.
В результате был создан ассортимент шлифованных пластин ПМН1 и ПМН2 с различными показателями микрогеометрии печатающей поверхности (Ra) для печатания широкого ассортимента полиграфической продукции на различных по жесткости и шероховатости бумагах и картонах с гладкой и тисненой поверхностью:
- ПМН1 с Ra = 0,50,7; 0,81,0 и 1,21,8 мкм;
- ПМН2 с Ra = 0,50,7; 1,21,8 и 2,03,5 мкм.
Таблица 4. Свойства поверхностного слоя ОРТП
Пластины Conti Air |
Микрогеометрия поверхности, мкм |
Твердость в ед. Шора А0 |
Изменение массы при набухании краскопередающего резинового слоя в керосине в течение 1 ч, мг/см2 |
|
Ra |
Rz |
|||
Prisma |
0,6-0,7 |
2,3-3,0 |
81 |
0,7 |
FSR |
0,8-0,9 |
4,0-4,4 |
82 |
0,8 |
UV black |
0,9-1,0 |
4,3-4,5 |
80 |
0,5 |
Ebony |
1,0-1,2 |
4,6-5,0 |
79 |
0,7 |
Crystal |
1,1-1,3 |
4,5-5,0 |
80 |
0,8 |
Plano |
1,3-1,4 |
6,3-6,5 |
83 |
0,6 |
Gournal |
3,5-4,3 |
9-12 |
76 |
0,6 |
Показатели твердости и шероховатости поверхностей ОРТП достаточно часто приводятся в рекламных материалах инофирм, однако изза отсутствия сведений о выборе ОРТП по этим показателям пластины выбираются полиграфистами зачастую без их учета. Проведенные испытания отечественных ОРТП ПМН1, ПМН2, пластин немецкой фирмы Conti Air (табл. 4) и других ОРТП позволили выработать следующие рекомендации по использованию показателей твердости и шероховатости при выборе пластин для различных видов печатных работ:
- для изготовления высококачественной печатной продукции на высокогладких сортах бумаги и картона следует использовать пластины с шероховатостью Ra = 0,50,9 мкм и твердостью поверхности от 78 до 85 единиц Шора А;
- для изготовления массовой печатной продукции на всех видах бумаги оптимальны пластины с шероховатостью Ra = 0,91,2 мкм и твердостью поверхности 7080 единиц Шора А;
- для изготовления высококачественной и массовой печатной продукции на низкогладких сортах бумаги и картона оптимальны пластины с шероховатостью
Ra = 1,11,4 мкм и твердостью поверхности 6578 единиц Шора А; - для изготовления высококачественной печатной продукции на бумаге и картоне с тисненой или отделочной поверхностью следует использовать пластины с шероховатостью Ra = 3,54,3 мкм и твердостью поверхности 6070 единиц Шора А.
* * *
Надеемся, что настоящий цикл публикаций убедил читателей в том, что офсетная резинотканевая пластина является сложным техническим изделием, комплекс деформационных и печатнотехнических свойств которого оказывает значительное влияние на качество печатной продукции и экономичность производства. К сожалению, производители ОРТП очень неохотно и ограниченно включают в свои технические и рекламные материалы важные характеристики этих пластин, что наносит серьезный ущерб качеству печатной продукции, тиражестойкости офсетного декеля и долговечности печатного оборудования. Между тем продажа ОРТП без документации с указанием значений показателей их печатнотехнических и деформационных свойств аналогична продаже печатных машин без технического паспорта.
Неправильный выбор ОРТП является основной причиной того, что декельные материалы и печатные машины выходят из строя задолго до их физического износа, а качество печатной продукции снижается. Иногда даже создается впечатление, что отсутствие в технической документации необходимых данных по декельным материалам не случайно, а направлено на искусственное увеличение продаж полиграфических материалов и печатных машин.
1 Из рекламных материалов 2006 года фирмы Kinyo (Япония) известно, что на основе резины NBR (акрилонитрил-бутадиен) изготавливаются краскопередающие слои ОРТП для офсетных машин с холодной и горячей сушкой, для листового офсета, в том числе для печатания некоторыми видами УФ-красок.
2 Старые пластины типа Б и Дк приводятся для сравнения величин минимального и максимального набухания ОРТП.
3 Сведения из рекламных материалов фирмы Kinyo (Япония).
![]() |
![]() |