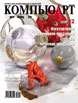
Тампонная печать: формы и краски
Изготовление печатных форм тампонной печати
Технология изготовления стальных форм тампонной печати
Технология изготовления фотополимерных форм тампонной печати
Состав красок для тампонной печати
Механизмы отверждения красок для тампонной печати
Выбор краски и ее подготовка к печати
Тампонная печать применяется для нанесения изображений на объекты сложной геометрической формы, в том числе на разнообразные сувениры: кружки, ручки, брелоки, пепельницы и т.п.
Изготовление печатных форм тампонной печати
Тампонная печать является разновидностью офсетной печати и позволяет использовать печатную форму глубокой, плоской или высокой печати. Наибольшее применение в тампонной печати получили формы с углубленными печатающими элементами, изготовленные на ленточной стали и на стальных или фотополимеризующихся пластинах. Процесс печатания с таких форм предусматривает нанесение печатной краски на всю поверхность печатной формы, а затем ее удаление с пробельных элементов ракелем.
Основные технические требования к печатной форме тампонной печати:
- печатная форма должна быть изготовлена на пластине, соответствующей формату воспроизводимого изображения с учетом размера полей (обычно ширина полей — 15-30 мм);
- стальная формная пластина должна иметь твердость 40-70 ед. по Роквеллу, а фотополимеризующаяся — 20-30 ед. по Роквеллу;
- поверхность формной пластины должна иметь чистоту 10-12 класса;
- глубина печатающих элементов должна находиться в пределах 15-40 мкм.
Применение ракеля для удаления краски с пробельных элементов требует чистоты поверхности и ее высокой устойчивости к истиранию. Требования к печатным формам для тампонной печати определяются также их назначением и условиями, в которых они будут работать.
Изделия, запечатанные тампонным способом
![]() |
![]() |
Технология изготовления стальных форм тампонной печати
Стальные печатные формы тампонной печати изготавливаются из стальных заготовок или из ленточной стали.
Печатные формы на стальных пластинах применяют для воспроизведения штриховых изображений и отличаются очень высокой тиражестойкостью (до 2-3 млн оттисков).
Технологический процесс изготовления печатных форм на стальных пластинах включает следующие операции:
- изготовление заготовки для формной пластины;
- обезжиривание и декапирование;
- нанесение и сушка копировального слоя;
- экспонирование пластины;
- проявление и окрашивание копии;
- химическое дубление копии;
- ретушь копии и обмазка пластины лаком;
- травление;
- удаление обмазки и копировального слоя;
- контроль качества печатной формы.
Стальные пластины могут как изготавливаться непосредственно на производстве, так и приобретаться у специализированных фирм. Необходимо отметить, что некоторые фирмы производят полностью подготовленные к экспонированию пластины с уже нанесенным копировальным слоем.
При изготовлении пластины на своем производстве сначала необходимо сделать ее заготовку. Все стадии этого процесса должны обеспечивать получение формных пластин с необходимыми чистотой поверхности и параллельностью плоскостей.
Экспонирующее оборудование и вспомогательные материалы
Стальные пластины, как правило, изготавливают из закаленной инструментальной стали с малым содержанием хрома, имеющей твердость 60-70 ед. по шкале Роквелла. Обычно это углеродистые (СТ55, СТ60, СТ65, СТ70, СТ50Г, СТ60Г, СТ65) или легированные (13Х, 9ХС, ХВСГ, ХВГ) марки стали. Также можно применять легированную конструкционную сталь. В некоторых случаях используют латунь.
При производстве формы из относительно мягких материалов, например из меди или латуни, для повышения твердости ее поверхностного слоя можно применять гальваническое наращивание хрома или никеля на заготовку либо на готовую форму.
Установка для химического травления
После выбора материала будущей формы приступают к изготовлению заготовки пластины. Этот процесс выполняют, как правило, с помощью металлообрабатывающего оборудования. Из стального бруска фрезеруют заготовку, снимают заусенцы, а со всех ребер — фаски. После снятия фасок заготовку со всех сторон шлифуют. Затем проводят термообработку, закаляя заготовку в масле до твердости 60-70 ед. по Роквеллу. После термообработки заготовку шлифуют по двум плоскостям. Далее проводят термообработку на старение: в течение 24 часов заготовку пластины варят в масле при температуре свыше 100 °С. Благодаря этой операции достигается снятие внутренних напряжений в металле, которые могут вызвать деформацию пластины при последующих операциях изготовления формы, связанных с нагревом. На заключительных операциях изготовления заготовок выполняют чистовую шлифовку на параллельность сторон и лекальную обработку. При чистовой шлифовке рабочую плоскость заготовки доводят до 8-9-го класса чистоты, а затем при лекальной обработке — до 10-12-го класса чистоты. Доводку рабочей поверхности выполняют, как правило, вручную на шабровочных плитах с применением полировальных паст. Заключительные операции изготовления заготовки пластины для форм тампонной печати обеспечивают создание ровной и гладкой поверхности, необходимой для хорошего снятия ракелем печатной краски с пробельных элементов формы в процессе печатания.
Когда заготовка для пластины готова, можно приступать к работе над печатной формой тампонной печати. Изготовление формы начинают с обезжиривания поверхности пластины кашицей из мела и венской извести или щелочным раствором с помощью щетки. Затем пластину декапируют раствором соляной кислоты и промывают водопроводной водой. Сразу после этого пластину высушивают под струей воздуха комнатной температуры или подогретого до температуры не выше 50 °С.
Следующая операция — нанесение копировального слоя — может осуществляться различными способами: распылением, центрифугированием или окунанием. Для изготовления печатных форм на стальных пластинах с углубленными печатающими элементами используют негативные копировальные слои на основе природных веществ растительного и животного происхождения и на основе синтетических полимеров. Наиболее часто применяют копировальные растворы на основе поливинилового спирта и желатина. Одним из существенных недостатков хромированных копировальных слоев является их нестабильность, то есть изменение рабочих свойств с течением времени, вызванное эффектом темнового дубления. Это обстоятельство вынуждает готовить подобные копировальные растворы и наносить их на пластины непосредственно в процессе изготовления формы.
Печать на цилиндрическом изделии
Для нанесения копировального раствора методом окунания необходимо иметь следующее оборудование и приспособления: ванну для нанесения слоя, держатель пластины, подставку для сушки и сушильный шкаф.
Обезжиренную и высушенную пластину помещают в держатель, который должен соответствовать пластине по размеру и быть изготовленным из стойкого к коррозии материала. Пластина покрывается копировальным слоем посредством окунания в ванну, также изготовленную из стойкого к коррозии материала, например из нержавеющей стали. Для экономии расхода копировального раствора ее основание должно быть узким. Пластину погружают в копировальный раствор вертикально. После того как она полностью погрузится в раствор, ее медленно вынимают и устанавливают на подставку. Следует обратить внимание на то, что скорость выемки пластины и вязкость копировального раствора оказывают влияние на толщину копировального слоя, от которой, в свою очередь, зависит время экспонирования и проявления, а также стойкость к травящему раствору. Чтобы избежать затеков по краю пластины, на подставку предварительно кладут фильтровальную бумагу. Пластину ставят на эту бумагу и прислоняют обратной стороной к стенке уголка. Время от времени следует поворачивать пластину в вертикальное положение, чтобы бумага впитывала накопившийся на краю копировальный раствор. Когда натек копировального слоя прекратится, пластину оставляют до ее полного высыхания. Часто для ускорения процесса сушки применяют сушильный шкаф, где копировальный слой высушивается при повышенной температуре.
После формирования на поверхности пластины копировального слоя производится экспонирование пластины через фотоформу в копировальной раме. Копировальная рама должна позволять экспонировать пластины толщиной до 10 мм. В качестве фотоформ используются позитивы с нечитаемым (зеркальным) изображением. Для изготовления фотоформ рекомендуется применять матированную фототехническую пленку. В процессе экспонирования пластины через позитивную фотоформу под вакуумом происходит задубливание копировального слоя на пробельных элементах.
Полученную копию проявляют, удаляя незадубленный копировальный слой с печатающих элементов. Далее копию переносят в ванну с раствором метилвиолета и окрашивают. Благодаря покраске достигается лучший контраст, что облегчает контроль пластины. Интенсивность окраски зависит от времени нахождения копий в красящем растворе. Нормальное окрашивание происходит в течение 10-30 с.
После окрашивания пластины производится химическое дубление копировального слоя для увеличения его стойкости к травящему раствору. Далее копию промывают струей воды и высушивают воздухом. Высохшая копия термически обрабатывается, а затем выполняются ее обмазка лаком и ретушь.
Подготовленную вышеописанным способом копию подвергают травлению раствором хлорного железа или 62%-ной азотной кислотой. При этом копию погружают в ванну с травящим раствором. Ванна должна быть изготовлена из синтетического материала и снабжена крышкой, чтобы по возможности уменьшить испарение раствора. В процессе травления рабочую поверхность копии периодически протирают тампоном в течение 5-20 мин в зависимости от требуемой глубины печатающих элементов формы. Качество процесса травления контролируют с помощью лупы. Время травления определяют по предварительному тесту. Оно зависит от состояния травящего раствора и его температуры, а также от требуемой глубины печатающих элементов формы. Обычно глубина травления для элементов изображения с тонкими линиями составляет 18 мкм, для остальных частей изображения — 22-25 мкм. По завершении травления форму промывают водой и удаляют лак и копировальный слой. Лак удаляют растворителем, копировальный слой на основе поливинилового спирта — нагретым концентрированным едким натром, на основе желатина — венской известью, а слой на основе ортонафтахинондиазидов — щелочным раствором или ацетоном.
В настоящее время стальные пластины редко применяются при изготовлении форм тампонной печати из-за их высокой стоимости. Вместо стальных пластин в последнее время начали использовать ленточную сталь. Среди ее достоинств — меньшая стоимость, возможности пробивать в стальных листах отверстия и использовать штифтовой метод приводки при многокрасочной печати. Твердость ленточной стали составляет около 50 ед. по Роквеллу, а тиражестойкость печатных форм — 200-300 тыс. оттисков. Процесс изготовления печатных форм на ленточной стали аналогичен вышеописанному.
![]() |
![]() |
Технология изготовления фотополимерных форм тампонной печати
Печатные формы на фотополимерных пластинах могут быть использованы для воспроизведения как штриховых, так и растровых изображений тиражами от нескольких сотен до нескольких десятков тысяч оттисков. Фотополимерные печатные формы тампонной печати — это формы, у которых пробельные элементы сформированы из фотополимеров — высокомолекулярных соединений, полученных в результате полимеризации под действием УФ-излучения.
Тампонная печатная машина
Фотополимерные пластины имеют многослослойную структуру, включающую основу, фотополимерный слой и защитную пленку. В качестве основы в фотополимерных пластинах применяется полиэфирная пленка, алюминиевая или стальная подложка. Использование стальной подложки позволяет закреплять формы в печатной машине магнитным способом.
Формирующий изображение слой образуют фотополимеризующиеся материалы, в состав которых обычно входят пленкообразующие полимеры, сшивающие агенты, фотоинициаторы и целевые добавки. Для изготовления фотополимерных пластин широко применяются полиамиды, которые обладают хорошими физико-химическими свойствами, в частности устойчивостью к истиранию. Сшивающие агенты в фотополимеризующихся композициях образуют нерастворимую трехмерную структуру. Состав и строение сшивающих агентов определяют механизм процесса структурирования и физико-химические свойства фотополимерных форм. Фотоинициаторы, входящие в состав фотополимеризующейся композиции, а также наполнители, красители, термоингибиторы и другие компоненты гарантируют достижение и сохранность необходимых свойств формы. Толщина фотополимерного слоя может составлять от 25 до 200 мкм.
Защитная пленка предохраняет фотополимерный слой от повреждений. Перед началом изготовления печатной формы ее снимают.
Технологический процесс изготовления печатных форм на фотополимерных пластинах при воспроизведении штриховых изображений включает следующие операции:
- экспонирование пластины через позитивную фотоформу;
- экспонирование сетки-растра;
- вымывание печатающих элементов;
- сушку;
- дополнительное экспонирование или термообработку.
При изготовлении фотополимерных печатных форм к фотоформе предъявляются очень жесткие требования:
- оптическая плотность печатающих элементов не должна быть ниже 3,0;
- плотность вуали на пробельных элементах не должна превышать 0,06.
Изображение на фотоформе должно быть зеркально-перевернутое (не читаемое со стороны эмульсии), ее геометрические размеры должны соответствовать формату пластины. Фотоформу рекомендуется изготавливать на фототехнической пленке с матовым эмульсионным слоем.
Перед началом изготовления формы с пластины снимается прозрачная защитная пленка, а фотоформа устанавливается по штифтам в экспонирующей установке (копировальной раме).
Контакт между фотоформой и фотополимерной пластиной в экспонирующей установке обеспечивается при помощи механического или вакуумного прижима. При механическом прижиме затруднен, а часто и невозможен плотный контакт пластины и фотоформы, что в первую очередь сказывается на качестве форм при воспроизведении изображений с мелкими элементами, в том числе растровыми. Отсутствие контакта вызывает дефект подкопирования. В настоящее время только около половины представленных на рынке установок оборудованы вакуумным прижимом.
В качестве источников света в копировальных рамах применяются лампы, излучающие свет с длиной волны 360-380 нм. Это могут быть металлогалогенные или люминесцентные лампы. Копировальные установки различаются по количеству и мощности установленных ламп, а также по формату. Ввиду малого формата копировальные установки для изготовления форм тампонной печати выпускаются в настольном варианте.
Современные модели экспонирующих установок, кроме вакуумного прижима, дополнительно оснащены индикацией величины этого прижима, декомпрессионным вентилем (для быстрого сброса вакуума) и программным цифровым таймером. Эти установки позволяют менять диапазон времени экспонирования в широких пределах, а возможность программирования облегчает работу оператора. На таких установках возможно копирование фотоформы не только на фотополимерные, но и на тонкие стальные пластины.
При экспонировании пластины через фотоформу в копировальной раме происходит формирование пробельных элементов. УФ-излучение проходит через прозрачные участки диапозитива и полимеризует слой по всей его толщине, причем в нижней части слоя пробельные элементы расширяются за счет светорассеивания и отражения от основы. В результате печатающие элементы приобретают различную глубину: мелкие — меньшую, а крупные — большую.
Затем с целью создания опоры для ракеля производят экспонирование сетки-растра. Сетка-растр — это растровый диапозитив с круглой прозрачной точкой, изготовленный на фототехнической пленке с матовым эмульсионным слоем. Он необходим для формирования на печатающих элементах опорных точек, которые препятствуют опусканию ракеля в углубления печатающих элементов. В противном случае ракель удалит краску не только с поверхности пробельных элементов, но и из глубины печатающих элементов, что приведет к неравномерности красочного слоя на оттиске. При этом по всей поверхности печатающих элементов создаются мельчайшие пробельные элементы в виде точек. В качестве сетки-растра используется диапозитив с линиатурой 80-150 лин./см с относительной площадью растровой точки 80-90%. Чтобы при печатании эти точки заливались краской, они должны иметь диаметр 40-60 мкм. Время экспонирования сетки-растра должно быть примерно равно времени экспонирования диапозитива изображения.
Далее формную пластину подвергают вымыванию, при этом с печатающих элементов удаляется неполимеризованный материал. Пластину помещают в вымывной раствор при температуре 22-26 °С и протирают плюшевой щеткой. Время вымывания — 1-2 мин, причем не рекомендуется превышать это время (особенно в случае использования водовымывных пластин), так как при более длительном вымывании происходит набухание фотополимера, что приводит к быстрому разрушению растровых точек и к снижению тиражестойкости печатной формы. Вымытую пластину ополаскивают свежей порцией вымывного раствора и высушивают под вентилятором. Затем осуществляют контроль изготовленной формы с помощью 8-10-кратной лупы.
С целью повышения прочности и устойчивости к истиранию пластину подвергают дополнительной засветке в течение 6-10 мин и термообработке. Термообработка осуществляется при температуре 80 °С для водовымывных пластин и 100-120 °С — для спиртовымывных пластин в течение 10-15 мин.
Рабочее помещение, где изготавливаются печатные формы, должно быть защищено от пыли и УФ-света, а также оборудовано вентиляцией. Готовые печатные формы, изготовленные на фотополимерных пластинах, хранят в пакете из синтетической пленки, чтобы они не высыхали. Оптимальные условия хранения форм: влажность воздуха — 55%, температура — 18-22 °С.
![]() |
![]() |
Печатный процесс
Нормальное протекание печатного процесса в тампонной печати возможно при выполнении следующих условий:
Аф ≤ Кк ≤ Ат — при переходе краски с печатной формы на тампон;
Ат ≤ Кк ≤ Ап — при получении оттиска на изделии,
где Аф — адгезия краски к форме, Кк — когезия краски, Ак — адгезия краски к тампону, Ап — адгезия краски к поверхности изделия.
Адгезия — это параметр, характеризующий прочность соединения двух разнородных тел, в частности степень прилипания краски. Когезия же характеризует прочность тела, например печатной краски. На величину когезии краски оказывают влияние ее вязкость и толщина красочного слоя.
Ход процесса печатания в значительной мере зависит от уровня автоматизации печатного оборудования. При печатании на ручном станке печатник щеточкой наносит на край формы небольшое количество краски. При протягивании ракеля по поверхности печатной формы краска заполняет углубленные печатающие элементы и одновременно удаляется с пробельных элементов. Отсутствие краски на пробельных элементах является критерием оценки корректности выбора и точности установки ракеля. Поскольку ширина ракеля несколько меньше ширины формы, на ее краях остается некоторое количество краски, которую убирают вручную ватным тампоном, смоченным в растворителе. После этого тампон опускается на печатную форму, забирая при контакте с ней часть краски из печатающих элементов, а затем снова поднимается. Изделие, на котором печатают изображение, при помощи каретки печатного станка подводится под тампон, который опускается и входит в контакт с поверхностью запечатываемого изделия, передавая красочное изображение. После этого запечатанное изделие вынимают.
![]() |
![]() |
Краски для тампонной печати
В практике тампонной печати применяют офсетные и типографские краски с добавлением сиккатива, а также трафаретные краски. Данные краски обеспечивают достаточную четкость и оптическую плотность изображений, однако их применение ограничено из-за длительного высыхания и абразивности пигмента. При печатании на ручных и полуавтоматических машинах эти краски в какой-то мере могут удовлетворить нужды производства.
Наилучшие же результаты обеспечиваются при использовании специальных красок для тампонной печати, которые отличаются от трафаретных более мелкими пигментами и большей насыщенностью. Краски для тампонной печати должны иметь высокую кроющую способность, быть липкими, текучими и обладать специальными печатно-техническими свойствами.
![]() |
![]() |
Состав красок для тампонной печати
Краски для тампонной печати включают следующие компоненты: красящее вещество, связующее вещество, вспомогательные вещества и растворители.
В качестве красящих веществ могут использоваться красители и пигменты. Красители являются растворимыми, находятся в красках в виде молекул и не рассеивают свет, благодаря чему краски на основе красителей прозрачны. Однако наиболее широкое применение нашли пигменты, которые применяются при производстве как кроющих, так и прозрачных красок.
Важнейшей составной частью краски является связующее, которое соединяет красящее вещество с запечатываемой поверхностью. Связующее вместе с вспомогательными веществами определяет физико-механические и физико-химические свойства красочной пленки. Соединение связующего с запечатываемой поверхностью может происходить в результате следующих процессов:
- действие электрических или молекулярных сил;
- диффузия связующего в набухшую или растворенную поверхность запечатываемого изделия;
- механическое закрепление на шероховатой поверхности изделия;
- химическая реакция между связующим и запечатываемой поверхностью.
В красках для тампонной печати используются связующие на основе таких веществ, как алкидная смола, акриловая смола, ацетобутилцеллюлоза, эпоксидная смола, полиэфир, полиуретановая смола, сополимеры винилхлорида и др. Для удовлетворения разнообразных требований, предъявляемых к печатной краске, связующее часто получают из нескольких составляющих.
Вспомогательные вещества улучшают характеристики печатной краски или придают ей новые свойства. Например, для улучшения эластичности красочной пленки вводят пластификаторы, для улучшения стойкости к истиранию — парафин, специальные добавки также могут повышать глянец красочной пленки или, наоборот, придавать ей матовость.
Растворители — это летучие, низковязкие химические вещества, которые переводят связующее в растворимую форму. Растворители должны хорошо растворять связующее и вспомогательные вещества, а их летучесть обеспечивает быстрое высыхание краски. Хотя для выполнения этих требований обычно вполне достаточно применения одного растворителя, в состав красок часто вводят их смесь.
![]() |
![]() |
Механизмы отверждения красок для тампонной печати
В зависимости от состава краски для тампонной печати она может закрепляться на поверхности запечатываемого изделия одним из перечисленных способов:
- окислительная полимеризация;
- испарение летучего растворителя (физическая сушка);
- взаимодействие отвердителя со связующим краски;
- фотохимическая реакция;
- воздействие тепла.
При окислительной полимеризации закрепление происходит за счет взаимодействия краски с кислородом воздуха. Время закрепления красочной пленки при этом составляет от нескольких минут до нескольких часов.
Когда краска закрепляется вследствие испарения летучего растворителя, в ее составе не происходит изменений, за исключением удаления растворителя. Если на красочную пленку нанести растворитель, то она вновь станет жидкой. Время закрепления красочной пленки тоже составляет от нескольких секунд до нескольких минут.
Закрепление благодаря взаимодействию отвердителя со связующим краски характерно для двухкомпонентных красок. Перед печатанием в их состав добавляют специальный отвердитель, с момента введения которого начинается реакция полимеризации. Процесс отверждения происходит в два этапа. На первом этапе краска закрепляется за счет испарения растворителя, при этом окончательная прочность красочного слоя не достигается. Время испарения растворителя составляет от нескольких секунд до нескольких минут. На втором этапе краска закрепляется за счет химического взаимодействия отвердителя со связующим краски, при этом достигается окончательная, очень высокая прочность красочного слоя. Время закрепления красочной пленки на этом этапе составляет от нескольких часов до двух-четырех суток. За счет термообработки время этого процесса может быть значительно сокращено. После окончательного закрепления краску нельзя растворить никаким растворителем. Время, в течение которого может производиться печатание, определяется жизнестойкостью краски и составляет, как правило, около восьми часов. Решающее влияние на длительность процесса оказывает содержание отвердителя в краске. Двухкомпонентные краски позволяют наносить одну краску на другую только в течение 15 часов, после чего становится невозможной полимеризация, необходимая для соединения двух красочных слоев. Двухкомпонентные краски применяются в тех случаях, когда к красочной пленке предъявляются особые требования в отношении износостойкости, стойкости к агрессивным средам или адгезии к инертным поверхностям. Следует также принять во внимание, что высокие показатели стойкости красочной пленки можно получить при условии достаточной стойкости поверхности изделия к воздействиям среды.
В качестве связующего в двухкомпонентных красках чаще всего используются полимеры, содержащие гидроксильные группы на базе полиэфира, полиакрилата или эпоксидной смолы, которые химически сшиваются (полимеризуются) вследствие введения отвердителя на базе изоцианата. Исходные продукты смолы (полимеры) и отвердителя должны быть растворимы в соответствующем растворителе, а продукт после сшивки — уже нерастворим, что улучшает прочность красочного слоя.
Закрепление краски в результате фотохимической реакции характерно для УФ-отверждаемых красок, которые, помимо красящего вещества, содержат олигомер, мономер и фотоинициатор, но не содержат растворителя. Отверждение краски происходит только под действием ультрафиолетового облучения. Главным достоинством таких красок является то, что они не высыхают в машине. УФ-отверждаемые краски позволяют получить достаточно прочные красочные слои. Время закрепления красочного изображения этим способом составляет от нескольких десятых до нескольких секунд.
Закрепление под воздействием тепла свойственно термоотверждаемым краскам, содержащим в качестве связующего вещества термоактивную смолу. Отверждение краски происходит в основном за счет нагрева. Такие краски, как УФ-отверждаемые, практически не высыхают в машине, а красочные слои имеют высокую прочность. Время закрепления красочного изображения составляет от нескольких единиц до нескольких десятков секунд.
![]() |
![]() |
Выбор краски и ее подготовка к печати
При выборе красок для тампонной печати необходимо учитывать свойства материала запечатываемого изделия и условия его эксплуатации. Прежде всего необходимо следовать рекомендациям изготовителя красок.
На некоторых материалах не удается получить удовлетворительной адгезии красочной пленки. В этих случаях поверхность изделий необходимо активировать посредством обработки открытым газовым пламенем или коронным разрядом. Выбор способа обработки обычно определяется формой запечатываемого изделия. Так, пленочные изделия удобнее обрабатывать коронным разрядом, а сложные по конфигурации изделия — открытым газовым пламенем.
При печатании на изделиях из новых, ранее не применявшихся материалов необходимо провести испытание смачиваемости краской их поверхности. С этой целью и для подбора соответствующей краски используют универсальный растворитель и тест-карандаш. При проведении испытания на поверхность изделия наносят каплю растворителя, а также проводят по поверхности тест-карандашом. Если капля растворителя воздействовала на поверхность изделия, оставив на ней след, а тест-карандаш оставил четкий ровный след, то активация поверхности перед печатанием необязательна. Если же растворитель не оставил на поверхности изделия никакого следа, а след от тест-карандаша собирается в капельки (то есть не смачивает поверхность), то для обеспечения нормальной адгезии краски перед печатанием поверхность изделия необходимо активировать. Для окончательного подбора краски необходимо провести пробную печать и испытание эксплуатационных свойств нанесенного красочного изображения.
Как правило, изготовители поставляют краски готовыми для печати. Однако часто возникает необходимость в коррекции вязкости краски, величина которой должна составлять около 8 с. Для измерения вязкости красок в тампонной печати используют так называемый вязкошпатель. Перед измерением вязкости краску следует тщательно перемешать и при необходимости ввести разбавитель, после чего опять тщательно перемешать. Для определения вязкости в емкость с краской опускают вязкошпатель, чтобы он заполнился краской до нужного уровня (уровень А). Затем вязкошпатель вынимают из краски, и она начинает вытекать. Необходимо замерить время вытекания краски от первого до пятого отверстия (расстояние В) с помощью секундомера. Вязкость краски характеризуется временем ее вытекания.
Краски для печатания должны быть гомогенными и тщательно перемешанными. Разбавление краски следует проводить аккуратно, так как введение слишком большого количества разбавителя может вызвать разделение пигмента и связующего и появление осадка. Выбор правильной пропорции разбавления краски обычно производится опытным путем. Если краска оказывается слишком сильно разбавленной, то прочность красочной пленки может значительно уменьшаться, особенно при сушке посредством обдува теплым воздухом. При этом уменьшается кроющая способность, а также может измениться тон краски. Если же вязкость краски слишком велика, то это приводит к образованию тяжей.
При использовании двухкомпонентных красок их вначале смешивают с отвердителем в необходимой пропорции, а затем вводят разбавитель для достижения заданной вязкости.
Если краска высыхает слишком быстро, то она может подсыхать на печатной форме и терять способность связываться с запечатываемой поверхностью. Для увеличения времени высыхания краски могут применяться замедлители высыхания, но если в краску введено излишнее количество замедлителя, то она не будет обладать достаточной липкостью, вследствие чего пленка краски может не переноситься с тампона на запечатываемую поверхность. Это происходит из-за того, что адгезия краски к поверхности силиконового тампона больше, чем к запечатываемой поверхности. Устранить подобное явление может обдув воздухом тампона, благодаря чему часть растворителя из краски улетучивается и краска становится более липкой, то есть вязкость краски (в следовательно, и когезия) при обдуве увеличивается, а адгезия к тампону уменьшается.
При введении в состав красок специальных добавок необходимо убедиться в их совместимости с краской.
В процессе выбора краски и определения формы тампона и его твердости следует принимать во внимание глубину печатающих элементов на форме, которая обычно составляет 15-35 мкм. При глубоких печатающих элементах краска должна быть относительно текучей, но не тиксотропной, а тампон должен иметь остроконечную форму и быть мягким. При неглубоких печатающих элементах краска может быть тиксотропной, а тампон — плоским и обладать большой твердостью. При относительно большой глубине печатающих элементов на форме и малой текучести краски возможен малый выход краски из печатающих элементов, так как когезия красочной пленки оказывается значительно меньше, чем ее адгезия к тампону.
При переносе краски с тампона на запечатываемую поверхность часть краски остается на тампоне, а другая переходит на изделие, то есть происходит расщепление красочного слоя. Параметры этого процесса в значительной мере зависят от скорости печатания. Для получения стабильных качественных результатов печати очень важно, чтобы остающееся на тампоне количество краски было минимальным и чтобы его величина не изменялась в процессе печатания.
Учитывая вышеизложенное, можно сделать вывод, что при выборе краски нельзя следовать только указаниям изготовителей красок — необходимо принимать во внимание и конкретные условия печатания, и характеристики печатной машины или станка.
![]() |
![]() |