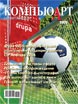
Проблемы воспроизведения 1%-ной точки во флексографии
Удержание 1% на флексографских формах
В последнее время во флексографском производстве предпринимаются попытки воспроизведения 1%-ной растровой точки. Существует множество различных мнений по этому поводу. В настоящей статье мы попробуем изложить свое видение возможности, а самое главное — необходимости подобного воспроизведения, способов контроля, а также всех плюсов и минусов репродуцирования 1%-ной точки.
Первая мысль, которая приходит в голову при вопросе о воспроизведении 1%-ной точки, — это какое количество информации содержит в себе однопроцентная область. В большинстве случаев ответ будет: очень малое, что связано в основном со спецификой дизайна или сюжета.
К сожалению, удержание такого уровня деталировки на формах, а также последующее воспроизведение на запечатываемом материале содержит больше негативных, нежели позитивных, моментов. В первую очередь это связано с резким повышением требований к качеству воспроизведения на всех без исключения стадиях производства.
1% на пленке
Воспроизведение менее чем 2-процентного растрового элемента всегда являлось и продолжает оставаться критическим элементом во всей производственной цепочке, особенно при использовании старых фотонаборных автоматов и неотрегулированных процессов проявления. Это означает, что процессы экспонирования и проявления должны быть хорошо настроены и доступны для контроля. Более того, контрольно-измерительное устройство должно быть в состоянии контролировать подобную точку не только согласно техническому описанию, но и практически.
Рис. 1. Структура негативной пленки
Обратимся к негативной фотоформе, которая чаще всего используется при репродуцировании в флексографии. Существует два типа пленок: прозрачная и матовая. От качества пленки зависит стабильность результатов изготовления флексографских печатных форм.
Структура пленок весьма сложная и включает несколько слоев (рис. 1), основными из которым являются:
- полиэстровая основа (PET) с толщиной от 100 до 175 мкм;
- дополнительный слой для улучшения сцепления эмульсии и последующего слоя;
- эмульсия — основной компонент пленки, на котором формируется изображение. Содержит кристаллы галогенида серебра и выпускается по традиционной технологии. Ее толщина вместе с защитным слоем составляет порядка 4 мкм;
- защитный слой — наносится на эмульсию: в чистой пленке — один раз, в матовой — дважды, причем во второй раз со специальными матовыми компонентами;
- противоореольный слой толщиной 3-5 мкм. Используется как для предотвращения образования ореолов при копировании, так и для дополнительной защиты.
Оба типа пленок имеют одинаковую структуру с единственным различием — матовая пленка имеет второй защитный слой с матовыми микрочастицами. Он состоит из тех же частиц, но размером уже 7 мкм. Это значит, что чувствительность обеих пленок теоретически должна быть одинаковой, однако для матовых пленок она немного ниже из-за дифракционных эффектов, возникающих во время формирования изображения. Как показывает практика, эта разница незначительна, но, тем не менее, ее нужно учитывать и корректировать при экспозиции.
Рис. 2. Снимок колец Ньютона (автор Winnie Summer)
Противоореольный слой содержит частицы порядка 2 мкм и предотвращает появление колец Ньютона (рис. 2). Эти кольца представляют собой интерференционные максимумы и минимумы, в классическом случае появляющиеся вокруг точки касания слегка изогнутой выпуклой линзы и плоскопараллельной пластины при прохождении сквозь них света. В случае контактно-копировальных работ кольца можно наблюдать при контакте зеркальной и прозрачной (или двух прозрачных) поверхностей. В монохроматическом свете кольца Ньютона представляют собой темные и светлые контуры, а в белом свете оказываются радужными.
Матовая составляющая также очень важна при изготовлении фотополимерных печатных форм, так как помогает удалять воздух при копировании в контактно-копировальных рамах. Это гарантирует качество репродукционного процесса.
Матовые пленки также характеризуются количеством и размером частиц, используемых при изготовлении эмульсии.
Кроме того, важным показателем является резкость пленки. В свое время эта тема активно обсуждалась применительно к офсетной печати, а сейчас вновь приобрела актуальность, но уже для флексографского производства, когда необходимо получить растровый элемент с как можно более четкими краями.
В настоящее время используются «мягкие» (Rapid access) и «жесткие» пленки. Пленки Rapid Access — стандартный тип негативных пленок во флексографии. Они широко применяются и доказали свое преимущество, особенно на предприятиях с не очень строгими параметрами производственной среды, благодаря достаточно большой широте проявления. В сравнении с «жесткими» пленками они менее чувствительны к температурным колебаниям, времени проявления, состоянию проявляющего раствора и т.д. «Жесткие» пленки, наоборот, обладают очень малой широтой и чувствительны к перечисленным выше изменениям, но имеют одно важное отличие — очень четкие края растровых элементов и большую оптическую плотность, нежели «мягкие» пленки. Растровые элементы, получаемые на них, называются соответственно «мягкая» и «жесткая» точки (рис. 3).
Рис. 3. Вид «мягкой» (а) и «жесткой» (б) растровых точек на фотоформе
Четкость контура точек оказывает влияние на изображение, формирующееся на фотополимерной пластине: растровые элементы будут четче и будут иметь меньшее растискивание при четком контуре растрового элемента.
![]() |
![]() |
Контроль пленки
Для контроля пленки большинство компаний используют денситометры проходящего света разных компаний-производителей. При этом контролировать можно как растровый процессор, так и, косвенно, процесс проявления. Не стоит забывать, что эти два процесса (запись скрытого изображения и его последующее проявление) всегда влияют на качество фотоформы и неразрывно связаны друг с другом. Именно поэтому следует всегда проверять получаемые фотоформы, а не только пытаться внести предыскажения в собственные настройки растрирующих процессоров по калибровочным шкалам. При больших форматах цветоделенных фотоформ имеет смысл контролировать плотность не в одном участке пленки, а в нескольких.
Рис. 4. Схема денситометра «на просвет»
Схематически денситометр «на просвет» показан на рис. 4 и представляет собой достаточно простую конструкцию. Свет от источника 2 отражается от зеркала 1 и разворачивается зеркалом 3 под углом 90°. Затем он проходит через тепловой фильтр 4, фиксированную апертуру 6 (которая может иметь различный диаметр или представлять собой щель) и достигает оцениваемой пленки 7, помещенной на прозрачный стол 5. Ослабленный свет поступает в световод 8, еще раз проходит через тепловой фильтр 9 или один из окрашенных фильтров 10 и наконец достигает светоприемника 11. Наиболее распространенные модели денситометров на рынке — D 200-II бывшей компании GretagMacbeth (больше не производится) и 361 T от X-Rite.
В настоящее время международные стандарты и технологические инструкции рекомендуют различные референтные данные для контроля производства фотоформ. Напомним, что классическая плотность для офсетной печати должна находиться в диапазоне от 3,3 до 3,8 D, что является вполне обоснованным для последующего изготовления фотополимерных форм.
Для флексографского производства значения плотности более высокие — 4,2-4,5 D, иногда доходящие до 6 D. Они должны быть одинаковы по всей поверхности фотоформы, а абсолютная разница между «чистой» пленкой (основа + вуаль) и экспонированным участком должна быть более 4 D.
Чистая основа должна иметь при этом ортохроматическую плотность менее 0,05 D и плотность в ультрафиолетовом свете — менее 0,01 D. Максимальная плотность в обоих диапазонах должна превышать 4 D. Именно поэтому в последнее время производители стали внедрять калибровочную карту с двумя калибровочными полями: для обычной калибровки и для дополнительной калибровки ультрафиолетового канала (рис. 5).
Рис. 5. Пример калибровочной карты
Контроль минимальной плотности с использованием ультрафиолетового диапазона необходим для правильной экспозиции печатных форм. Чем меньше плотность, тем больше ультрафиолетовых волн будет проходить, тем более предсказуемы результаты копирования и тем проще регулировать весь процесс с точки зрения точности воспроизведения растровых элементов.
Измерительный прибор, с помощью которого выполняется оценка, должен быть калиброван в соответствии с рекомендациями компании-производителя. Важно также иметь калибровочный стандарт (калибровочную карту) в хорошем состоянии, с неистекшем сроком эксплуатации. На первый взгляд это может показаться не очень значительным, так как стандарт хранится по всем правилам и эксплуатируется редко. Однако, как только встает задача стандартизации предприятия по ISO 9000, то первый вопрос касается именно актуальности калибровочных стандартов для контрольно-измерительного оборудования.
![]() |
![]() |
Копирование 1%-ной точки
В случае использования 1%-ной растровой точки сильно повышается риск возникновения проблем на стадии копирования, особенно при попытке воспроизвести света в диапазоне 0,7-0,9%. Здесь даже малое различие (количество пикселов, из которых состоит точка, плотность вуали и даже пыль) на негативной пленке даст большую разницу на печатной форме.
Считается, что при менее 0,9% на пленке (при чтении денситометром) репродукционный процесс переходит в непредсказуемую и плохо контролируемую фазу. При этом достигается критический уровень чувствительности при обнулении прибора по пленке.
При измерении относительной площади растрой точки нулевой уровень всегда берется исходя из пленки, а денситометр всегда делает измерение оптической плотности, а затем переводит ее в проценты. К сожалению, обычный разброс плотности при репродуцировании может варьироваться от 0,05 до 0,08, и не только от пленки к пленке, но и на разных участках фотоформы.
Например, фотоформы А и Б, сделанные с одного файла, а затем измеренные, покажут соответственно 0,05 пропускной способности и 0,08 D, то есть количество энергии, прошедшей сквозь пленку A, будет больше, нежели прошедшей сквозь Б. Тем не менее эти две пленки будут приняты за 100%, так как денситометр был обнулен по ним. В светах измерения минимальных точек будут подобны, так как точки имеют одинаковую форму и одинаковый размер 1%, но в плане абсолютного пропускания света пленка А (с плотностью 1,90 D на 1%) пропустит больше света, чем пленка Б (с плотностью 2,09 D на том же 1%), и, определенно, будет больше подходить для копирования 1%, нежели пленка Б.
Другая тенденция прослеживается при абсолютном измерении плотности в светах (напомним, что речь идет о негативной пленке). Как было показано выше, относительная площадь растровых элементов, считанная денситометром, является хорошим показателем, но относятся лишь к определению пропускной способности материала и равенству оптических свойств на всем протяжении пленки. Любая разность в плотностях фотоформ будет иметь последствия на дальнейших этапах.
Можно с уверенностью сказать, что существует только один путь: используя денситометр «на просвет», убедиться в корректности полученной фотоформы — определить, сколько света (энергии) прошло, измерив света в абсолютной плотности и в процентах.
Для установления «пороговой» точки оптической плотности, при которой возникают потери, был проведен ряд исследований негативных фотоформ с различной разрешающей способностью изображения, и на их основании выведены эмпирические зависимости. Для той же самой относительной площади в 1% диапазон оптических плотностей составил от 1,82 до 2,13 D.
В качестве экспериментальных печатных форм были выбраны ASAHI AFP SH 1,70 мм при стандартных условиях производства. Было отмечено, что везде, где наблюдалась плотность выше 2,00 D, были обнаружены проблемы с переносом изображения (потерей точек). Последующие эксперименты подтвердили, что именно плотность 2,00 D является критической величиной для традиционных условий производства печатных форм.
При переэкспонировании пластин (16” — 24” — 32” на экспонирующей раме AFP) было установлено, что плотность 2,30 D является лимитом, выше которого репродукционные свойства утрачиваются, то есть увеличение времени не ведет к какому-либо улучшению стабильности свойств растровой точки.
По результатам проведенных экспериментов можно сформулировать основную рекомендацию для пользователей: дважды тестировать пленку, измеряя сначала процентное содержание, а потом плотность в светах. При этом плотность, естественно, должна быть в районе 2,00 D.
В табл. 1 представлены значения плотности и соответствующие им значения относительной плотности.
Таблица 1. Соответствие оптической плотности значениям относительной площади растровых элементов
Оптическая плотность |
1,90-2,00 |
1,50 |
1,27 |
1,00 |
0,34 |
0,09 |
0,04-0,06 |
Относительная площадь растровых элементов, % |
1 |
3 |
5 |
10 |
50 |
90 |
100 |
![]() |
![]() |
Удержание 1% на флексографских формах
Давно было замечено, что наилучшее воспроизведение растрового элемента флексоформ достигается между 20 и 30 мкм. Размер точки соотносится почти один в один с исходным значением, естественно при соблюдении жестких условий производства. Ниже 20 мкм сегодня практически невозможно аккуратно перенести точку с фотоформы на печатную пластину.
Однако основной вопрос заключается не в понимании физических возможностей печатной пластины, а в проверке того, что фотоформа лишена проблемных зон. Оптическая плотность прозрачных полей — вот основной вопрос. Когда она высока, то сильно влияет на физическое прохождение света, а значит, и на качество получаемой печатной формы.
Разрешающая способность и соответствующая линиатура растра, а также состояние растровых точек должны приниматься во внимание при любой оценке и сравнениях, так как даже самое малое различие может сделать некоторые точки непригодными для копирования.
Другими словами, любое отклонение от соблюдения жестких требований может негативно сказаться на переносе информации, а «выпадение точки» стать одним из самых распространенных дефектов при копировании. Все это, к сожалению, происходит из-за отсутствия так называемых запасов прочности у пленки. Естественно, при использовании технологии CtP многие из перечисленных трудностей не возникают, однако при традиционной технологии репродуцирования
1%-ная точка может стать источником огромного количества проблем при отсутствии явной необходимости ее воспроизведения.
![]() |
![]() |
Контроль печатных форм
После получения результата на флексографской печатной форме нужно убедиться, что сформированное изображение достаточно хорошо для последующего цикла воспроизводства. Существует два способа контроля получаемых результатов:
- визуальный — достаточно простой и надежный способ для начального этапа контроля поверхности формы, но недостаточный для получения более детальной информации, документирования и повторения проверки;
- инструментальный — обычно такая оценка должна проводиться с помощью инструментального микроскопа и/или измерительного устройства, например VipFlex компании X-Rite (рис. 6).
Рис. 6. Измерительное устройство VipFlex
Однако использование только микроскопа, даже со специальным электронным оснащением по захвату изображения, не имеет достаточно преимуществ из-за продолжительности процесса наведения и фокусировки. Именно поэтому специальные программно-аппаратные решения так необходимы.
Этот метод используется для точной оценки качества большинства печатных форм, за исключением форм с алюминиевой обратной стороной и сливов. С помощью приборов можно не только получать числовые данные измерений, но и, например, масштабировать критические элементы изображения либо делать цифровую фотографию. В качестве дополнительных привлекательных опций можно выделить возможности нахождения относительной площади растровых элементов, определения линейных размеров элемента изображения и линиатуры растра в автоматическом режиме.
Программно-аппаратное обеспечение обладает определенной гибкостью, а измерения можно проводить в ручном режиме, что особенно важно при использовании его на производстве с не очень стабильным производственным процессом или когда по ряду причин программное обеспечение не в состоянии правильно распознать печатные элементы. Типичная ситуация показана на рис. 7, где малый размер точек сочетается с недостаточным качеством изготовленной формы. На рисунке отчетливо видно, какое изображение программа получает с поверхности.
Немаловажную роль здесь играет и толщина флексографской формы, так как более толстую форму будет сложнее контролировать в силу значительного различия высоты печатных и пробельных элементов.
Тем не менее комбинация обоих методов и наличие микроскопа и программно-аппаратной базы наиболее предпочтительно, поскольку будет обеспечивать все возможные комбинации контроля.
![]() |
![]() |
Печать 1%-ной точки
Если предположить, что при 1 и 2% мы имеем то же самое количество растискивания при печати, то наблюдатель (заказчик), наверно, не увидит разницы на конечном оттиске. Поэтому печать 1%-ной точки не даст сколь-нибудь значимого улучшения качества, так как разница между двух- и однопроцентным содержанием будет незаметна.
Стоит также напомнить о феномене, который можно регулярно наблюдать при печати. Поскольку структура и форма 1%-ной точки «тонка», риск получить большее растискивание и видимый дефект изображения больше, чем при 2%. На рис. 8 отчетливо видно отсутствие разницы между 1, 2, 3, 4 и 5%-ными точками. К сожалению, этот эффект типичен для флексографской печати.
Рис. 7. Цифровая фотография 1%-ного поля
Рис. 8. В светах 1%-ная точка для пурпурной и черной красок воспроизводится как 3 или 5%-ная
Данный эффект отражен в стандарте ISO 12647-6 (2006), где рекомендуемый диапазон воспроизводимых растровых элементов разделен по типам запечатываемых материалов. Однако не только материал играет роль при передаче заданного диапазона: влияние оказывает также тип флексографской формы, который напрямую зависит от запечатываемого материала, технического состояния печатной машины и т.д.
Стоит обратить внимание на тот факт, что, согласно тому же ISO, только пленочный материал может обеспечить необходимую базу для качественного воспроизведения широкого диапазона тона — от 2 до 90%. На практике будет невозможно воспроизвести тот же самый диапазон на шероховатых материалах, особенно на различных картонах и/или на скоростных флексомашинах (табл. 2).
Таблица 2. Воспроизводимый диапазон относительной площади растровых элементов (согласно ISO 12647-6)
Тип запечатываемого материала |
Картон (сильно шероховатые материалы) |
Немелованная бумага |
Мелованная бумага |
Пленка/фольга |
Относительная площадь растровых элементов, % |
От 8 до 75 |
От 5 до 75 |
От 3 до 85 |
От 2 до 90 |
Таблица 3. Воспроизводимый диапазон линиатуры растра (согласно ISO 12647-6)
Тип запечатываемого материала |
Картон (сильно шероховатые материалы) |
Немелованная бумага |
Мелованная бумага |
Пленка/фольга |
Линиатура растра, лин./см |
От 14 до 33 |
От 18 до 40 |
От 45 до 54 |
От 36 до 60 |
Ограничения также налагает линиатура запечатываемого материала и форма растровой точки. Именно поэтому ISO рекомендует использовать опробованные параметры, приведенные в табл. 3. При выходе за эти рамки производство столкнется с ограничениями, касающимися четкой системы контроля и обеспечения практически идеальных условий производства фото- и печатных флексоформ, слаженной работы технолога и печатника, контроля всех без исключения параметров печатной машины, тщательного подбора форм под запечатывемый материал, а не наоборот и т.д. Подобный подход, безусловно, классический, но на многих производствах он требует дополнительных инвестиций в оборудование, производственные помещения и обучение персонала.
Многие из приведенных в статье данных являются империческими, но общемировая тенденция достаточна очевидна: выход производства на иной качественный уровень всегда сопряжен со строгим соблюдением технологических инструкций и стандартов, а также четким пониманием технологических возможностей предприятий.
Использованная литература
1. ANSI CGATS.9-2007 Graphic technology — Graphic arts transmission densitometry measurements: Terminology, equations, image elements and procedures.
2. ISO 12647-6 (2006) Graphic technology — Process control for the production of half-tone colour separations, proofs and production prints. Part 6. Flexographic printing.
![]() |
![]() |