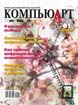
О современном производстве штанцевальных форм
Ничего не поделаешь, но в немецко-русских словарях твердое слово Stanze (штамп) стоит между глаголом stänkern (вонять)
и существительным der Stapel (куча). А теперь поиграем
в слова, соединяя их по смыслу. Итак, курильщик, доставая
из пачки последнюю сигарету и закуривая ее, дымит на весь коридор, а из выброшенных пачек на свалках крупных мегаполисов образуются огромные кучи. Чем не сюжет
для социальной рекламы?
О сигаретах мы вспомнили неслучайно, ведь, по словам генерального директора фирмы «Растр-технология» Евгения Кульбацкого, именно крупные производители табачных изделий определяют сегодня требования к штампованной продукции
с точки зрения дизайна и защиты от контрафакта. И главную роль в этом должен играть высокий технологический уровень изготовления штанцевальных форм.
Можно предположить, что по уровню сложности за упаковкой сигарет идет упаковка духов, колготок и, конечно, бело-черно-красная упаковка останкинских пельменей.
КомпьюАрт: Выгодно ли сегодня в России заниматься производством вырубных форм для изготовления упаковки?
Евгений Кульбацкий: Емкость российского рынка бумажнокартонной упаковки в настоящее время оценивается примерно в 1,1 млн долл. в год с постоянной тенденцией к росту.
Вырубные, а правильнее говорить — штанцевальные, формы можно, конечно, делать и «на коленке», используя молоток, пассатижи и лобзик. Так и происходит в типографиях, имеющих ремонтные цеха. В них прос-тое оборудование позволяет сделать штанцформу для не претендующего на качество заказчика. Но для работы с серьезными или точными заказами необходимо высокое качество штанцформы, которое достигается большими инвестициями в развитие производства.
Самым сложным является изготовление штампа для сигаретной упаковки. Для организации такого уровня производства требуется порядка 2 млн евро инвестиций. Если же делать элитную упаковку, то эту сумму нужно удвоить. Например, лазерная установка для раскроя неметаллических заготовок стоит около 500 тыс. евро, а водорезка для эжекторной резины —150 тыс. евро. Теперь серьезному заказчику также нужно предъявить сертификат ISO 9001/2008. При таком подходе достигается гарантированная точность высечки и тиражестойкость штанцформы от миллиона циклов.
КА: Давайте дадим определение штанцевальной формы с точки зрения ее изготовления.
Е.К.: Под штанцевальными подразумевают формы, изготовленные из стальных линеек, носителями для которых являются фанера, пластик, а также другие композиционные материалы. Формы подразделяются на плоские (рис. 1) и ротационные (рис. 2). У ротационных большая скорость работы по сравнению с плоскими, но зато плоские формы дают более сложный крой, биговку, тиснение (йогуртовые или пивные лотки и уже упоминавшаяся сигаретная упаковка).
Также существуют и технические штанцформы, которые сегодня переживают подъем. Они нужны для вырубки нетрадиционных материалов: пленки, резины, кожи, например для автомобильной промышленности. Но вернемся в полиграфию.
Рис. 1. Плоская штанцформа
Рис. 2. Ротационная штанцформа
КА: А в нашей стране больше применяется ротационная или плоская высечка, например при производстве гофротары?
Е.К.: В России, как и в Италии и Испании, наблюдается крен в сторону ротации. В Германии больше плоской высечки. Любопытно отметить, что в российских предприятиях по производству гофротары установлено оборудование для ротационной высечки от разных производителей. Для него требуются формы с разным диаметром цилиндров — всего порядка 60 диаметров. В то же время в США процесс высечки стандартизован — нужен всего один диаметр цилиндра.
Евгений Кульбацкий, канд. физ.-мат. наук, генеральный директор фирмы «Растр-технология»
КА: Технологу типографии, который составляет чертеж будущего изделия, и механику, меняющему ножи, не помешает напомнить конструкцию штанцевальной формы…
Е.К.: На схеме штанцформа показана в разрезе вместе с ответной поверхностью и обрабатываемым материалом (рис. 3). Здесь важно пояснить, что обычно штанцевальная форма поставляется в комплекте оснастки, в который также входит оснастка для секций удаления облоя и разделения заготовок.
Рис. 3. Схема штанцформы
Лист картона 1 подается между штанцевальной формой, опирающейся на несущую металлическую плиту 2, и ответной металлической контрпластиной 3, закрепленной на поверхности ответной плиты 4. На поверхности контрпластины 3 закреплены ответные элементы штанцформы 5 и 6.
При взаимном перемещении плит пресса происходит соприкосновение штанцформы и контрпластины по кромкам режущих линеек (ножей) 7, которые высекают внешний контур кроя заготовки. Для выталкивания картона с лезвия ножей применяется эжекторный материал (резина) 8. Одновременно с высечкой происходят также процессы бигования и рельефного тиснения картона: биговальная линейка 9 формирует профиль биговки посредством вдавливания картона в канал биговальной матрицы 5, а клише (матрица) 10, закрепленное на специальной вставке 11 в основании штанцевальной формы 12, формирует на картоне рельеф при контакте с контрклише (матрицей) 6.
Кроме перечисленных деталей, в основание штанцформы могут быть вмонтированы и другие детали, например так называемые T-образные гайки 13 для крепления штанцформы или цилиндрические штифты 14 с резиновыми кольцами 15, предназначенные для позиционирования при монтаже контрбиговальных матриц.
Процесс заказа комплекта оснастки показан на рис. 4.
Рис. 4. Заказ комплекта оснастки
КА: На каком оборудовании в типографиях происходит высечка изделий, и каков уровень автоматизации этого процесса?
Е.К.: Начну с автоматизации. Несколько технологических операций — от печати до склеивания — в принципе, могут объединяться для выполнения в одной автоматической линии. Аппараты подобного типа принято называть inline. Такое построение операций в автоматическую поточную линию характерно для производства картонных коробок в промышленных масштабах большими тиражами (например, табачная упаковка). В случае выпуска картонажными предприятиями большой номенклатуры различных коробок при сравнительно больших тиражах более целесообразным является использование машин, выполняющих отдельные операции: печать, отделку (например, горячее тиснение фольгой), штанцевание с удалением отходов и разделением заготовок, фальцевание со склеиванием и т.д. Такие машины принято называть offline. Штанцевание, совмещенное с автоматическим удалением отходов и разделением заготовок, чаще выполняют на offline штанцевальных автоматах, которые можно разделить на ротационные и плоско-высекальные.
Для плоской высечки наибольшее применение получили тигельные машины, как самые универсальные. Напомню, что тигелем принято называть подвижную металлическую плиту, несущую обрабатываемый материал, а талером соответственно — неподвижную плиту, несущую штанцевальную форму. По этому принципу построено большинство тигельных штанцавтоматов, в которых штанцформа закреплена на неподвижном талере. Однако есть и машины, в которых движется плита, несущая штанцформу, либо движутся обе несущие поверхности. Но объединяющим для всех подобных аппаратов является принцип действия: контакт плоской штанцформы с плоской контрплитой одновременно по всей поверхности. Замечу, что в плане изготавливаемого под конкретный тираж штанцевального инструмента inline- и offline-машины имеют принципиально различающиеся секции тигельной высечки. Так, в первом случае владелец машины заказывает в специализированной компании только штанцевую форму и контрбиговальные элементы (матрицы или пластину). Последующие операции удаления отходов и разделения заготовок выполняются в такой машине с помощью машинной перенастраиваемой оснастки. В случае же листовых offline-машин, имея в своем распоряжении набор машинной оснастки для всех секций машины (кроме штанцевальной), оператор пресса, в принципе, может воспользоваться им, если конфигурация внешней границы высекаемого кроя упаковки достаточно проста (как правило, прямоугольной формы). В противном случае возникает необходимость в услугах специалистов по изготовлению штанцевальной оснастки.
Схожие процессы происходят и при штанцевании на ротационных машинах. Ротационная, так же как и плоская, форма состоит из основания (фанерные полуцилиндры), вставленных в прорезанные в нем пазы стальных линеек различного типа и приклеенных на поверхность основания эжекторных материалов.
КА: Давайте на примере конкретной упаковки продемонстрируем возможности технологии штанцевания.
Е.К.: Процесс производства складных коробок из картона и гофрокартона представляет собой совокупность выполняемых в строго определенной последовательности наиболее распространенных в полиграфии технологических операций (рис. 5): печать изображения и текста, отделка внешней запечатанной поверхности, штанцевание, удаление технологических излишков материала (отходов, облоя), отделение друг от друга индивидуальных заготовок коробок (раскроя), фальцевание, склеивание швов, стапелирование и упаковка заготовок коробок.
Рис. 5
КА: Теперь поговорим о качестве. Что такое качественная высечка, и какие материалы лучше использовать при изготовлении штанцформ?
Е.К.: В понятие «качество» по отношению к штанцформам и ответным частям вкладывается совокупность их свойств и параметров, позволяющих потребителю получить упаковку с такими заданными характеристиками, как:
- геометрические размеры;
- сопротивляемость изгибу (по линиям биговки, рицовки, перфорации);
- отсутствие внешних дефектов от воздействия оснастки.
И всё это при максимально возможной производительности штанцевального оборудования. Кроме того, обязательным компонентом качества нужно считать применение при изготовлении штанцформы и ответной части материалов и технологий, оптимальным образом удовлетворяющих требуемой точности их изготовления, а также необходимой тиражестойкости. Хороший производитель оснастки должен предложить клиенту оптимальный вариант ее исполнения, минимизирующий издержки.
Установка TwinLas 2115-R DC (Marbach) для раскроя неметаллических заготовок стоимостью 500 тыс. евро
Сегодня на мировом рынке предлагаются разнообразные хайтек материалы и технологии, гарантирующие превосходное качество получаемой упаковки, длительный срок ее службы и максимальную производительность штанцевального оборудования (рис. 6).
Рис. 6. Штанцевальные формы с различными основаниями: 1 — фанера, 2 — сталь (Sandwich), 3 — многослойная стеклоткань с наполнителем (Duramar)
Наиболее распространенным материалом для основания штанцформ является фанера твердых пород дерева (береза, клен, бук). Она получила широкое распространение благодаря дешевизне, хорошей обрабатываемости (механическим или лазерным излучением) и экологической безопасности. Сегодня ведущие российские производители штанцформ применяют лазерную технологию обработки фанеры.
Но фанера как материал обладает рядом серьезных недостатков:
- неоднородность структуры (сучки, полости) приводит к появлению дефектов пазов, прорезаемых лазерным лучом;
- существенно отличающаяся от стали зависимость геометрических размеров от влажности и температуры приводит к несовпадению штанцформы с ответной частью;
- малая прочность, позволяющая при условии сохранения качества штанцформы менять линейки в одном основании, обработанном на лазерном комплексе, не более одного раза.
Перечисленные дефекты фанеры заставляли специалистов искать альтернативные материалы с того момента, как стали применяться лазеры (начало 70-х годов прошлого века).
Технико-экономические характеристики штанцевальных форм с основанием из различных материалов
Тип основания штанцформы |
Примерная стоимость, евро (для сравнения) |
Тираже- стойкость, млн ударов |
Относительная стоимость замены линеек после 1 млн ударов, % |
Возможное число замен линеек |
Фанера |
~1000 |
1-2 |
70 |
Не более 1 |
Duramar |
~2500 |
5-10 |
30 |
4-5 |
Sandwich |
~4500 |
10-30 |
17 |
>10 |
Первой была применена сталь. Стальное основание получило название «сэндвич» (sandwich) из-за своей структуры «сталь — компаундная смола — сталь». Высокая стоимость «сэндвичей» стимулировала разработку и внедрение неметаллических материалов Pertinax, Permaplex, акрилового стекла и др. Но наибольшее распространение получил материал Duramar, появившийся на рынке в начале 1990-х годов. Duramar представляет собой многослойную стеклоткань с наполнителем из полиэстра. Этот материал высокопрочен, а его физические свойства по изменению геометрических размеров при изменении температуры схожи со свойствами стали. Пробивка пазов в материале Duramar производится ЧПУ-автоматами водоструйной резки, поскольку при лазерном прожигании пазов образуются высокотоксичные газы.