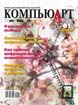
Управление качеством полиграфической продукции
Печатный процесс. Axis Control. Часть 1
![]() |
![]() |
Николай Сапошников, руководитель отдела цифровых технологий ООО «Гейдельберг-СНГ» |
Игорь Гузяков, канд. техн. наук |
Что необходимо сделать для оптимизации печатного процесса
О настройке основных параметров системы контроля (Prinect Axis Control)
О контрольных шкалах на оттиске
Методика контроля печати при выполнении заказа
Эталонные значения для красок и бумаг
В перечне предлагаемых компанией «Гейдельберг» продуктов, позволяющих не только осуществить построение цифрового Workflow типографии, но и в дальнейшем формализовать все процессы и процедуры типографского производства, особое место занимают продукты Prinect, способные упростить и сделать более эффективным и рентабельным процесс печати. Применительно к листовой офсетной печати это Prinect PRESS Center — операционная система с дистанционным управлением подачей краски для печатных машин серии Speedmaster; Prinect Auto Register — система автоматической приводки; Prinect Image Control — колориметрическая система контроля и управления цветом; Prinect Axis Control — интегрированная в Prinect PRESS Center стандартная система спектрофотометрических измерений (рис 1).
Рис. 1
В настоящей статье речь пойдет о работе системы Prinect Axis Control в условиях производства.
Никакая автоматизированная система контроля качества печати не может гарантировать качественную печать сама по себе. Измерения, выполняемые системой, и вносимые ею поправки могут приблизить результат к эталонным значениям, но этого недостаточно, чтобы признать его удовлетворительным. Добиться высокого качества печатной продукции — это только половина дела. Важно правильно определить цену этого качества и постараться до минимума сократить затраты на его достижение. Максимальный экономический эффект может быть достигнут только в том случае, когда качество контролируется в интегрированном рабочем потоке. Этот поток охватывает весь процесс производства печатной продукции. Мы будем рассматривать два основных этапа — допечатную подготовку и печать. Обусловлено это тем, что данные процессы уже сегодня могут быть формализованы и стандартизованы в большинстве типографий различного профиля.
Рассмотрение всех процедур по оптимизации печатного процесса будем осуществлять на базе Prinect Axis Control, Prinect Image Control и других систем Heidelberg.
Что необходимо сделать для оптимизации печатного процесса
Основные требования таковы:
1. Для заданных условий печати необходимо определить величину растискивания и с учетом этого отрегулировать процесс изготовления печатных форм.
2. Необходимо добиться стабильной работы машины и установить оптимальные эталонные значения для основных красок. Как минимум раз в год необходима перенастройка всех параметров печатной машины.
3. Провести оптимизацию предварительной подачи краски и характеристических кривых:
- печатные секции необходимо привести в состояние, при котором обеспечивается требуемый уровень предварительной подачи краски до начала печати;
- путем установки необходимой ширины зазоров для красочных зон следует настроить характеристические кривые процесса нанесения краски так, чтобы результат печати соответствовал выбранному стандарту.
4. Провести настройку красочных зон в соответствии с заранее заданными значениями красочного покрытия. Необходимо правильно отрегулировать красочные зоны в соответствии со значениями, которые предоставляет Prinect Prepress Interface или Plate Image Reader.
5. Если осуществлять контроль через Prinect Axis Control, то ручное вмешательство в регулировку красочных зон не допускается, поскольку является помехой для работы системы и приводит к снижению качества цвета.
6. Проверка параметров красочного аппарата. При этом печатник проверяет состояние зеленого индикатора на дисплее Prinect CP2000 Center и минимизирует подачу увлажняющего раствора для обеспечения высокого контраста отпечатка и отсутствия отмарывания.
Когда оптимальные условия печатного процесса достигнуты, необходимо добиться, чтобы величина расхождения фактических цветов с эталонными составляла менее пяти единиц — ΔE < 5. Для этого потребуется отпечатать приблизительно 130 оттисков. Система Prinect Axis Control контролирует цвет при достаточно малой величине расхождения. О величине ΔE подробно рассказывается в статье «Контроль качества в строгом режиме» (см. КомпьюАрт № 9’2009).
Если оказывается, что на первом снятом с машины оттиске величина ΔE > 5, заново проверяется характеристическая кривая, которой обеспечивается подача краски в соответствии с заданным стандартом.
![]() |
![]() |
О настройке основных параметров системы контроля (Prinect Axis Control)
На производстве должна быть предоставленная поставщиком калибровочная карта с данными, адаптированными к условиям типографии. Естественно, что первая калибровка выполняется персоналом Heidelberg Service. После этого каждые три месяца требуется повторная калибровка. Правильная установка параметров измерительной процедуры является важным фактором для сравнения результатов, полученных с помощью разных устройств. В процессе калибровки рассматриваются:
1. Источник освещения оттиска:
- D50 — стандартный источник естественного освещения (дневной свет) с красноватым оттенком;
- D65 — стандартный источник естественного освещения с синеватым оттенком;
- A — стандартный источник, соответствующий свету лампы накаливания; имеет красноватый оттенок;
- С — стандартный источник, соответствующий естественному освещению, но при отсутствии ультрафиолетовой составляющей.
Отметим, что в Европе в качестве стандартного источника освещения для полиграфической отрасли принят источник D50.
2. Observer — угол наблюдения. Для параметра Observer можно выбирать между двумя стандартными значениями — 2° и 10°. По умолчанию для офсетной печати принят угол наблюдения 2°.
3. Filter — применение поляризационного фильтра. Для параметра Filter возможен выбор между двумя настройками — polarized и unpolarized.
Поляризационные фильтры удаляют блики, появляющиеся в результате отражения света от поверхности красочного слоя, поэтому при применении фильтра измерение влажных и сухих оттисков дает практически одинаковые результаты. Поляризационный фильтр влияет исключительно на измерение оптической плотности. При измерении значений Lab фильтр не применяется.
В системе Prinect Axis Control, поскольку поляризационный фильтр в ней не установлен, измерения всегда выполняются в режиме unpolarized. Измерив в «неполяризованном» режиме спектральные величины, система выполняет вычисление «поляризованной» плотности.
4. Необходимо выбрать фильтр для измерения плотности, при этом можно выбирать между следующими стандартными фильтрами: DIN 16536 NB, ANSI A, ANSI T. Для работы в Prinect Axis Control рекомендуются настройка DIN 16536 или AnsiT (используется в Северной Америке).
![]() |
![]() |
О контрольных шкалах на оттиске
Prinect Axis Control позволяет с помощью команды Service —>Archive—>Color Control Bar Archive создать список наиболее часто используемых шкал, которые можно разделить на два вида:
- для традиционного монтажа используйте контрольные шкалы CPC;
- для цифрового монтажа применяйте шкалы Prinect (рис. 2) или Prinect FOGRA.
Важно отметить, что неиспользуемые шкалы не следует удалять безвозвратно. Их нужно лишь переместить в список unused color control strips. Такие шкалы больше не присутствуют в меню выбора, но в случае необходимости их можно активировать заново.
Рис. 2
Для применяемых серии красок и типа бумаги необходимо выбрать красочный набор с подходящими эталонными значениями.
![]() |
![]() |
Методика контроля печати при выполнении заказа
Подготовка тиража к печати
Для печатников установлен стандартный алгоритм действий при запуске тиража с применением системы контроля печати, который выглядит следующим образом:
1. Установка формата материала.
2. Назначение краски печатным секциям с использованием буквенных обозначений.
3. Печать 130 пробных оттисков, снять лист. Перед этим необходимо убедиться в том, что красочные аппараты находятся в стабильном режиме.
4. Установка параметров проведения измерений: условия, тип материала, допуск.
5. Измерение белизны бумаги.
6. Назначение эталонного цвета. При этом нужно взять значения из подходящего красочного набора в базе данных или с помощью специальной функции взять значения с образца, то есть значения, полученные путем измерений.
7. Выбор и позиционирование контрольной шкалы. При наличии соединения с Prinect Prepress Interface и получении через него необходимой информации о позиционировании шкалы измерительная головка занимает нужное положение автоматически.
8. Необходимо убедиться в достоверности данных, представленных как в графическом, так и в численном выражении. Если достоверность их вызывает сомнение, еще раз проверить все выполненные настройки!
9. Передать в печатную машину поправки, рекомендованные системой.
После двух- или трехкратного применения поправок достигается соответствие фактических цветов эталонным.
Рис. 3. Экран Measurement/Adjustment recommendations. Поправки, вычисленные алгоритмом системы для каждой красочной зоны
на основе величин ΔЕ, характеризуют расхождение между фактическими и эталонными цветами
При печати тиража
Для качественной печати периодически снимаются, измеряются листы и применяются контрольные поправки. При необходимости можно вручную корректировать эталонные значения.
Внесение изменений в процессе печати
При условии тщательного соблюдения правил и рекомендаций дальнейшее приближение фактических цветов к эталонным в процессе печати будет происходить по следующему сценарию.
На первом, подготовительном этапе на пути приближения к эталонному цвету выполняются следующие действия: регулировка предварительной подачи краски, настройка красочного аппарата сначала с помощью характеристической кривой, а затем с помощью заранее заданных для печати данного заказа значений содержания краски. При этом происходит предварительное заполнение красочных аппаратов краской, после чего в течение некоторого времени они стабилизируются. Начало печати возможно только по достижении устойчивого режима.
После тщательного выполнения всех предварительных действий расхождение между фактическими и эталонными цветами (ΔЕ) должно составлять приблизительно 5.
Рис. 4. Оптимальная настройка печатного процесса с помощью заранее заданных значений
Чтобы снизить величину расхождения до (ΔЕ) до 2, потребуется внести приблизительно три контрольные поправки. После этого величина расхождения для отдельных зон должна оставаться стабильной на протяжении печати всего тиража. При этом необходимо учитывать, что в больших тиражах условия печати подвержены изменениям.
Зоны, находящиеся вне пределов печати, необходимо блокировать, так как для контроля качества они не играют никакой роли. По той же причине следует блокировать зоны, в которых краска присутствует только на контрольной шкале.
Если на первом снятом для измерения листе обнаруживается расхождение ΔЕ>10, при том что предварительная подача краски отрегулирована и выполнена предварительная настройка с помощью данных из Prinect Prepress Interface или Plate Image Reader, то необходимо перепроверить настройки печатной машины. Если имеет место избыточность или недостаточность нанесения краски, следует откорректировать характеристическую кривую и настройки предварительной подачи.
Особую озабоченность должна вызывать избыточность нанесения краски, выявленная при изучении первого снятого листа. Возможно, в таком случае необходимо произвести смывку, перенастроить машину, выбрав другие значения параметров, и запустить печать заказа заново. Красочный аппарат представляет собой заполненный краской резервуар, и снижение уровня подачи краски происходит медленно, особенно при печати заказов с низким цветовым содержанием, поэтому пока не будет достигнут более низкий уровень подачи краски, потребуется отправить в брак немало листов.
Если в репродуцировании эталонной плотности невозможно добиться устойчивости, то, скорее всего, это происходит из-за того, что красочный аппарат не стабилизирован. Это объясняется следующими возможными причинами:
- ранее зоны были отрегулированы вручную;
- изменилась скорость вращения дукторного цилиндра или режим работы раскатного цилиндра красочного аппарата;
- характеристическая кривая компенсации скоростного режима не соответствует изменившейся скорости печати;
- произошло изменение скорости подачи или состава увлажняющего раствора;
- лист был снят преждевременно.
![]() |
![]() |
Эталонные значения для красок и бумаг
Красочные наборы
Необходимые для контроля качества эталонные значения хранятся в красочном наборе. Каждый такой набор обязательно содержит данные:
- для белого цвета бумаги;
- для основных красок;
- для поля баланса по серому.
Кроме того, в нем могут содержаться значения Lab для дополнительных красок.
Измерение материала, используемого в текущем заказе, — необходимое условие для контроля качества. На основе измеренного значения производится коррекция колориметрических данных, записанных в этот красочный набор.
В комплекте с Prinect Axis Control поставляются стандартные красочные наборы, обозначенные Heidelberg. Они соответствуют различным сериям красок и предоставляют для них усредненные значения. Таким образом, для достижения качественного результата крайне важно, чтобы для красок и бумаг, используемых в собственном производстве, создавались собственные красочные наборы.
Как создается красочный набор
Открыв базу данных красочных наборов, можно создать копию существующего набора и сохранить ее под новым именем. Причем имя должно быть понятным, например в нем должно отражаться название используемой серии красок.
Затем выбирается класс, соответствующий качеству используемой бумаги. На выбор предлагаются следующие классы бумаг: глянцевая, матовая мелованная, немелованная.
Выбирается лист, который будет служить образцом для снятия эталонных значений. Желательно, чтобы это был свежеотпечатанный оттиск, на который нанесены используемые краски. На этом образце сначала измеряется белый цвет бумаги, затем цвет плашки, а потом, если это необходимо, серое поле. Также нужно измерить белизну бумаги.
Ввод эталонных значений, соответствующих стандарту DIN ISO 12647
Чтобы добиться соответствия печатного процесса требованиям DIN ISO, в красочный набор необходимо внести цвет, который является ближайшим к тому, что определен стандартом. Затем, если необходимо, этот цвет можно откорректировать в процентном соотношении.
Между установленным для красочного набора эталонным значением и значением, зафиксированным в DIN ISO, существует расхождение ΔЕ0. На эту величину уменьшается предельно допустимое расхождение ΔЕ, равное 5.
Цвета дополнительных красок из каталога
Для дополнительных красок существуют коллекции цветов в виде каталогов. Можно напечатать такой каталог, измерить нужный образец и добавить полученное значение в красочный набор.
Для использования цветов-образцов необходимо, чтобы материал, на котором печатается каталог, был точно таким же, как тот, на котором печатается тираж. Кроме того, перед печатью каталога обязательно должна быть измерена белизна бумаги. Вообще, при использовании дополнительных красок рекомендуется печатать образец и вносить данные в красочный набор только после его визуальной оценки. Это дает возможность учитывать отклонения, связанные с принадлежностью краски к разным партиям, а также толщину красочного слоя, нанесенного на бумагу.
Если заказ повторный
Для печати повторных заказов можно считать данные с контрольного листа из предыдущего заказа и занести их в красочный набор.
Поскольку по техническим причинам измерения всегда проводятся в режиме без поляризационного фильтра, результаты измерений получаются разными в зависимости от того, является ли лист влажным или сухим. Следовательно, контроль качества цвета свежеотпечатанных оттисков с помощью значений, считанных с давнего, сухого оттиска, может сопровождаться некоторыми отклонениями, если сравнивать его результаты с печатью предыдущего заказа.
Изготовление серии отпечатков для определения эталонных значений
Для определения эталонных значений всегда необходимо изготавливать серию отпечатков, чтобы можно было найти такое значение, с помощью которого в поле плашки достигается самое высокое значение плотности, при том что растискивание остается умеренным и поле с 70-процентным тоном не заполняется краской полностью. При соблюдении двух этих условий обеспечивается высокий контраст отпечатков.
Для определения эталонных значений нужно отпечатать несколько листов, поднимая уровень подачи краски от очень низкого до самого высокого, а затем измерить плотность на поле плашки и на поле 70-процентного тона. По формуле Мюррея — Дэвиса вычисляется максимальный контраст печати:
,
где К — контраст печати, выраженный в процентах; Dv — плотность поля плашки; D70 — плотность поля с содержанием краски 70%.
На том листе, где контраст получается самым высоким, подача краски является оптимальной, а следовательно, цвет соответствующей краски является эталонным и его можно занести в красочный набор.
Когда можно менять эталонные значения
Если необходимо, содержащиеся в красочном наборе эталонные значения могут быть изменены, для чего существуют следующие способы:
- изменение эталонных значений при подготовке заказа — непосредственно в процессе подготовки заказа можно вручную изменять эталонное значение плотности, приближая его к идеальному с шагом 0,01. При этом автоматически корректируются соответствующие значения Lab;
- OK sheet — при наличии печатного листа, признанного удовлетворительным после визуальной проверки, что часто происходит при согласовании печати с заказчиком. Данный лист может быть принят в качестве нового стандарта, после чего процесс нанесения краски контролируется уже не с помощью красочного набора и записанных в него значений, а через значения, взятые с этого принятого за эталон листа;
- Zonal transfer — перенос зон. С листа, признанного удовлетворительным, можно выполнять перенос одних зон в другие, что особенно удобно, когда на одном листе размещаются несколько копий одного изображения. Однако необходимо учитывать, что переносится усредненное для выбранных зон значение, а не фактический профиль. Если машина оборудована устройством переворота листа, для двусторонней печати можно использовать функцию Transfer to other side — перенос зон на оборотную сторону;
- для проведения измерений и контроля качества эталонный цвет можно корректировать в процентном отношении. После внесения изменений и подтверждения результат их выводится на дисплей как новое расхождение относительно эталона.
Рис. 5. Идеальное представление cерии отпечатков. На приведенном примере максимальная величина контраста достигается при D = 1,17
Рис. 6. Окно Measurement/reference values с кнопками функций OK sheet, Zonal transfer и Change by percentage
Независимое друг от друга изменение значений плотности и значений Lab невозможно, поскольку значения обоих этих параметров вычисляются из спектральных характеристик света, отраженного от поверхности цветового поля и считанного измерительной головкой.
Если изменяется толщина красочного слоя, то вместе с ней изменяется и коэффициент отражения, что, в свою очередь, приводит к изменению отраженного спектра и соответственно вычисленных из спектральных характеристик значений плотности и Lab. Иногда на листе, который визуально оценивается как удовлетворительный, тем не менее, обнаруживаются серьезные расхождения с эталоном. Причины этого могут быть следующие:
- неверно выбран красочный набор, а следовательно, для контроля качества используются неподходящие эталонные значения;
- на незапечатанной области листа не измерена белизна бумаги;
- неверно заданы параметры измерительной процедуры или неверно выбран класс бумаги.
Методы контроля
Для хроматических красок CMY система Prinect Axis Control предлагает на выбор контроль или плашек отдельных красок, или серого баланса.
При контроле плашек проводятся измерения сплошного тона каждой отдельной краски. Черная краска и все дополнительные краски всегда контролируются по плашке.
Во втором случае баланс красок CMY контролируется с помощью серых полей, запечатанных ахроматическими красками при следующем их содержании: С = 70%, М = 60%, Y = 60%.
Имеются специализированные шкалы (среди них — Prinect 6GS), предназначенные для контроля серого баланса. Они устроены так, что содержат только сплошные поля CMY в ограниченном числе красочных зон.
Рис. 7. Вид окна программного модуля составления отчетов о проходящих тиражах
У контроля качества путем контроля серого баланса есть следующие преимущества:
- в процессе печати тиража обнаруживаются самые малые цветовые флуктуации и сдвиги;
- контролируется цветовой баланс — важнейший фактор, влияющий на визуальное восприятие отпечатка.
Контроль серого баланса выявляет малейшие изменения в параметрах, характеризующих условия печати, процесс нанесения краски и приводку.
Генерирование отчетов и протоколирование
Данный программный модуль дает возможность документировать все случаи внесения поправок. Вместе с вычисленными системой коррекционными значениями записываются даты, вследствие чего соответствующие значения можно загружать по сети. Для применения модуль необходимо лицензировать и активировать.
Описанные нами методики применения Prinect Axis Control, системы начального уровня (она работает только с контрольными шкалами), уже помогают сократить производственные расходы, повысить эффективность производства. В следующей статье мы рассмотрим более сложную систему контроля качества Prinect Image Control, гибкость и возможности которой позволяют интегрировать ее в общий рабочий поток типографии и организовать замкнутую систему управления цветом и качеством.
![]() |
![]() |