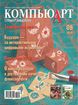
Контроль печатного процесса
История вторая: контроль печатных форм
История третья: программное обеспечение
История первая: печатник
Перед печатником стоит вполне определенная цель — клиент типографии и конечный пользователь отпечатанной продукции должны быть удовлетворены качеством напечатанного изображения. Для получения качественной продукции необходима стабильность ее свойств, поэтому печатник прежде всего должен знать, какие именно свойства нужны и каковы их допустимые отклонения.
Печатная машина позволяет наносить краску в нужных местах печатного листа, поэтому необходимо выделить два свойства:
- цвет изображения;
- положение изображения на печатном листе.
Больше печатник ни на что повлиять не может. Поэтому если печатнику нечем контролировать цвет, кроме собственного зрения, то качество будет страдать. Почему? Потому что нет стабильности. Если у печатника есть инструмент для измерения цвета, но на пульте нет норм печати, то качество страдает, потому что нет стабильности. Печатник просто не знает, к чему ему стремиться.
Итак, задача технолога — найти в стандарте или узнать из тестов нормы по печати и оформить их таким образом, чтобы печатнику не составило труда запомнить их наизусть. Что это значит? Цифры должны быть запоминающимися, а подложки объединены в группы. Пример подобного оформления приведен в табл. 1 (нормы по стандарту ISO 12647-2; начиная с 2004 года в этом стандарте уже нет денситометрических норм).
Таблица 1. Нормы по печати согласно стандарту ISO 12647-2
Бумага |
Краска |
L = подложка — |
Допуск для 68%
|
Максимальный разброс — |
Мелованная, 80-150 г/м2, |
C |
55 |
±1 |
±2 |
M |
48 |
±1 |
±2 |
|
Y |
89 |
±1 |
±2 |
|
K |
16 |
±1 |
±2 |
|
Координата L |
C |
80 |
±1 |
±2 |
M |
77 |
±1 |
±2 |
|
Y |
92 |
±1 |
±2 |
|
K |
69 |
±1 |
±2 |
|
Немелованная, |
C |
60 |
±1 |
±2 |
M |
56 |
±1 |
±2 |
|
Y |
89 |
±1 |
±2 |
|
K |
31 |
±1 |
±2 |
|
Координата L |
C |
80 |
±1 |
±2 |
M |
77 |
±1 |
±2 |
|
Y |
92 |
±1 |
±2 |
|
K |
68 |
±1 |
±2 |
Конечно, стандарт ISO 12647 не вынуждает нас выбросить денситометры. Они хороши для контроля стабильности печатного процесса, то есть когда мы на приладке проверяем попадание в стандарт по ΔE, то потом подписной лист уже можно измерять любым из имеющихся денситометров, я подчеркиваю — любым, независимо от стандарта измерения оптической плотности (ISO, DIN, ANSI) и даже наличия/отсутствия поляризационного фильтра. Именно об этом сказано в параграфе 4.3.2.3 примечания 4 стандарта ISO 12647-2: «Сначала печатник получает корректные значения Lab плашек на печати и затем измеряет их при помощи денситомет-ра на подписном листе. Полученные оптические плотности используются в качестве целевых значений в процессе печати оставшегося тиража».
Таким образом, для контроля печатного процесса мы можем использовать и денситометры и спектрофотометры. По состоянию на 2010 год компания X-Rite имеет в модельном ряду две линейки денситометров — X-Rite DensiEye 100/700 и X-Rite 504/508/518. Они различаются по цене, доступным функциям и возможности апгрейда: денситометр X-Rite 504 всегда можно улучшить до спектрофотометра X-Rite 528/530.
Оптическая плотность — всем известная величина, поэтому ограничусь несколькими комментариями. Вопервых, оптическая плотность с 2004 года уже не упоминается в стандарте ISO 12647-2. Отсюда вывод — оптическая плотность как контролируемый параметр остается только для проверки стабильности печати после утверждения подписного листа по колориметрическим показателям. Вовторых, оптическая плотность бывает разная, то есть рассчитывается по разным стандартам. Имеются в виду наборы из четырех зональных светофильтров по каждой краске. Самые популярные — это ISO Status E и ISO Status T, европейский и американский стандарты соответственно. Каким из них пользоваться — принципиального значения не имеет, но важно, чтобы нормы оптической плотности и измеренная плотность относились к одному стандарту. Очень рекомендую при измерении и сравнении оптических плотностей узнать, установлен ли поляризационный фильтр и какому стандарту соответствуют плотности — ISO Status E или ISO Status T.
Теперь нужно ответить на два вопроса:
- как получить координаты Lab, указанные в стандарте ISO 12647-2?
- как сделать это максимально прос-то, ведь спектрофотометр показывает три числа вместо одного у денситометра?
Печатнику удобно работать по одному показателю — оптической плотности, а не по трем координатам Lab. С оптической плотностью всё просто — есть номинальное значение, например C = 1,4. Если на оттиске С = 1,56, то печатник знает, что на бумагу передается много краски и что нужно снижать ее подачу на 0,16 единиц оптической плотности. И он понимает, на сколько единиц ему нужно снижать зональную или общую подачу краски. Таким образом, с помощью одного показателя C = 1,56 он мгновенно рассчитал, что нужно делать с подачей краски на машине.
А теперь берем нормы Lab из стандарта ISO. По голубой краске на бумаге типа 1 (мелованная, 115 г/м2), на белой подложке по стандарту ISO координаты Lab = 55; –37; –50. На оттиске Lab = 58,40; –38,28; –46,49. Кто сможет ответить в течение трех секунд, что надо делать печатнику? Варианты ответа: увеличить подачу краски, уменьшить подачу краски, заменить краску. Справились? Хорошо, печатник увеличил подачу краски — и вы вспомнили, что нужно контролировать еще и ΔE. Вы переключаете функции спектрофотометра на относительные измерения, и теперь на оттиске ΔL = –1,13; Δa = 4,69; Δb = –2,03; ΔE = 5,17. Каковы теперь действия печатника, и сколько времени у вас ушло на ответ?
Откровенно говоря, не представляю, как можно печатать по координатам Lab из стандарта ISO, не имея функции BestMatch спектрофотометра X-Rite SpectroEye. Лучше всего эту функцию увидеть в работе. Ведь ее основное преимущество заключается в удобстве использования.
Эталонные значения Lab из стандарта можно скачать с сайта xrite.com и записать непосредственно в прибор. У X-Rite это называется «Работы». То, что нам нужно, называется P1WBU07 — это означает: P1 — Paper type 1 (бумага типа 1); WB — White Backing (белая подложка под измеряемый лист); U — Unpolarized (без поляризационного фильтра); 07 — стандарт ISO 12647-2:2004/Amd:2007 с поправками 2007 года. Затем мы измеряем тиражную бумагу и одну из плашек C, M, Y, K — прибор сам определяет, какой это цвет. Результат выдается в виде ΔE и оптической плотности, то есть мы одновременно видим и колориметрический показатель ΔE, и оптическую плотность, привычную и удобную для всех печатников.
Итак, благодаря функции BestMatch мы получаем следующее:
- печатник видит один параметр ΔD вместо трех — ΔL, Δa, Δb;
- прибор рассчитывает не только текущее ΔE, но и предсказывает, какое ΔE будет, если откорректировать подачу краски;
- с помощью функции BestMatch в SpectroEye можно контролировать не только триаду, но и смесевые цвета Pantone;
- это, пожалуй, самый удобный способ печатать по цветопробе — контролировать можно не только плашки C, M, Y, K, но и C+M, M+Y, Y+C, C+M+Y, 40C, 40M, 40Y, 40K, 80C, 80M, 80Y, 80K и любые другие. То есть если клиент просит попасть именно в цветопробу, то процедура следующая: используя функцию BestMatch, измеряем в качестве эталона контрольное поле на цветопробе, а в качестве образца — контрольное поле на оттиске. Хочу заметить, что такое сравнение можно выполнять только по спектральным данным (что и делает BestMatch) так как в струйном цветопробном принтере применяются пигменты, отличные от офсетных.
Что в результате? Ориентируясь на показатель ΔD, печатник может сказать, уменьшать или увеличивать подачу краски и на сколько, так как этот параметр для него привычен. Но, тем не менее, величина ΔD рассчитывается исходя из спектральных данных, поэтому с помощью функции BestMatch можно контролировать не только триаду, но и смесевые краски.
История вторая: контроль печатных форм
Офсетные печатные формы надежнее всего контролировать с помощью специальных приборов, фотографирующих пластину и автоматически анализирующих изображение. Такие приборы обладают большей точностью и повторяемостью измерений относительной площади растровых точек на форме, чем денситометры. Небольшое примечание: растровые точки на оттиске необходимо измерять с помощью денситометра/спектрофотометра с поляризационным фильтром и по стандарту ISO Status E, и, строго говоря, теперь это называется не «растискивание» и «процент растровой точки», а «приращение величины тона» и «величина тона».
Есть два прибора для измерения офсетных форм от компании X-Rite — PlateScope и ICPlate. Преимущество PlateScope — в более высокой повторяемости измерений (благодаря камере высокого разрешения), цветном экране и интерфейсе USB. В свою очередь, X-Rite ICPlate меньше стоит, более компактный и мобильный и работает на обычных пальчиковых батарейках. Оба прибора одинаково хорошо справляются с гибридным и стохастическим растрированием и с визуально низкоконтрастными беспроцессными офсетными формами. Для контроля измерения можно посмотреть на фактическое изображение с камеры.
![]() |
![]() |
История третья: программное обеспечение
На первое место по перспективности поставлю программное обеспечение X-Rite PressOptimizer, планируемое к поступлению в продажу в конце года. Рекламный проспект X-Rite начинается так: «Вся полиграфическая индустрия гудит, как пчелинный рой, со словами вроде “стандарт”, “спецификация”, ISO, G7, SWOP, PSO, Japan Color — что всё это значит, и как мне достичь этого? Что еще более важно — зачем?»
Факт остается фактом: в настоящее время количество типографий, использующих рекомендации ISO 12647-2, невелико. И я скажу почему: стандарты ISO пишутся не для удобного и эффективного внедрения технологий, а для постулирования сложившихся норм. Язык стандартов, мягко говоря, не способствует пониманию их сути. Поэтому и возникли спецификации BVDM PSO и Gracol G7. Различаются они незначительно, но содержат в описании очень полезные практические рекомендации относительно достижения требований стандарта и качественной печати. Обе они утверждают, что контроль за воспроизведением полутонов (читай — растискивание) более важен, чем 100-процентное воспроизведение плашек.
На этом этапе у печатников возникает резонный вопрос: как я могу управлять растискиванием? Например, давление печати выставлено корректно, увлажнение настроено, подача краски тоже — и при этом приращение уровня тона не соответствует стандарту. Что делать? Именно для этого и существуют кривые предкомпенсации в растровых процессорах при выводе пластин. На скриншоте вы можете увидеть, что в приличном RIPе есть как минимум три кривые. Первая — это кривая линеаризации вывода пластин, вторая — кривая предкомпенсации для получения нужной (например, по стандарту ISO) кривой тонопередачи, третья — для быстрой ручной коррекции, если необходимо.
Как правильно провести все технологические тесты для определения кривых предкомпенсации, оптимального уровня подачи краски и бинарного наложения (треппинга)? Именно в этом и помогает программа X-Rite PressOptimizer. На втором скриншоте программы показаны все этапы технологических тестов, вдобавок ко всему снабженных понятным описанием в один-два абзаца каждого из требований стандарта ISO 12647-2. Вся процедура представлена в виде мастерапомощника, когда шаг за шагом выполняются все этапы технологической настройки допечатных и печатных процессов:
- вывод тест-формы на CtP;
- контроль пластины;
- печать и контроль оттисков;
- анализ первого теста;
- определение оптимальной подачи краски;
- ?генерация компенсационной кривой градационного ???процесса;
- применение этой кривой в CtP;
- вывод второй тест-формы;
- контроль пластины;
- печать и контроль оттисков;
- генерация отчета;
- определение попали/не попали в стандарт.
В табл. 2 указаны возможности разных программ X-Rite и поддержка ими различных приборов.
Таким образом, группа программ от X-Rite PrintCheck Reader до PressOptimizer помогает в нелегком деле внед-рения стандартов, причем необязательно ISO. Вы можете создать собственный стандарт, исходя из ваших реально используемых бумаг и красок.
Таблица 2. Возможности программы X-Rite
![]() |
![]() |
Литература
- The Certified Six Sigma Green Belt Handbook R. A. Munro, M. J. Maio, M. B. Nawaz, G. Ramu, D. J. Zrymiak. American Society for Quality, 2007.
- ISO 12647-2:2004/Amd 1:2007, параграф 4.3.2.3, примечание 4, http://www.iso.org/iso/iso_catalogue/catalogue_tc/catalogue_detail.htm?csnumber=43977.
- Синяк М. Еще раз о контроле. http://www.compuart.ru/Archive/CA/2004/9/2/.
- Крылов А. Контроль качества в строгом режиме. http://www.compuart.ru/Archive/CA/2009/9/11/.
- Гудилин Д. Денситометрия в офсетной печати. http://www.compuart.ru/article.aspx?id=8351&iid=337
- http://www.xrite.com/product_overview.aspx?ID=764&Action=support&SoftwareID=817.
- ISO 12647-2:2004/Amd 1:2007, параграф 4.3.5.1, примечание 3, ISO 12647-2.
- http://www.xrite.com/documents/literature/en/L7-481_PrintCheck_and_PressOptimizer_en.pdf.
- http://www.bvdm-online.de/Aktuelles/Downloads.php
- http://www.bvdm-online.de/Aktuelles/Downloads.php?Action=Form&FileID=249.
- http://www.idealliance.org/industry_resources/branding_media_and_color/g7.
- http://files.idealliance.org/G7/PressOpGuide/Sheetfed_Offset/G7_Press_Guide.pdf.
![]() |
![]() |