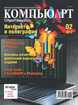
Контроль качества допечатной подготовки изданий
На различных этапах процесса допечатной подготовки изданий проводится контроль за выполнением наиболее важных технологических операций. Для контроля верстки полос изданий и корректорской вычитки текста служат отпечатки, получаемые на одноцветных (черно-белых) электрофотографических или струйных принтерах. Качество обработки цветных изображений проверяют на экране монитора компьютера графической станции и по изображениям, полученным на устройствах цифровой цветопробы. В первом случае говорят о так называемой мягкой цветопробе, которая обычно используется в процессе обработки изобразительной информации или для предварительной оценки изображений после их обработки. «Мягкая» цветопроба в силу того, что цветовой охват монитора существенно уже возможностей печатного процесса, не может в полной мере дать представление о будущем печатном оттиске. Во втором случае получают так называемую твердую цифровую цветопробу на цветных принтерах или аналоговую цветопробу с цветоделенных фотоформ с помощью контактно-копировальной установки и ламинатора.
Для инструментального контроля качества фотоформ и печатных форм используют денситометры, а для измерения цветных характеристик изображений (оригиналов, оттисков, цветопробных отпечатков) — спектрофотометры.
Наиболее полную оценку качества допечатной подготовки изданий осуществляют на пробопечатных станках, на которых изготавливают с печатных форм оттиски, аналогичные тиражным оттискам в печатной машине.
Одним из важнейших направлений повышения качества печатной продукции является создание единых автоматизированных технологических комплексов, включающих оборудование, расходные материалы и контрольноизмерительную технику. Недооценка любой составляющей неизбежно приводит к существенному ухудшению качества продукции, что и наблюдается в настоящее время в отечественной полиграфии. Прежде всего это относится к практическому применению средств автоматизированного контроля.
Современная полиграфическая промышленность широко использует колориметрические приборы на всех технологических стадиях, поскольку иначе невозможно достоверно и оперативно получать информацию о качестве изображений — оригиналов, цветопроб и оттисков. Кроме того, колориметрия обладает таким свойством, как объективность, что особенно важно для согласования с заказчиком допустимых отклонений цвета на оттиске по сравнению с цветопробой. Не менее существенны названные преимущества во взаимоотношениях репроцентра с типографией, особенно если они находятся далеко друг от друга.
Каждой технологической стадии воспроизведения оригинала соответствует определенная операция контроля, выполняемая при помощи специальной измерительной техники и программноаппаратных средств (рис. 1).
Рис. 1. Средства контроля в процессе изготовления оттиска
Современные международные стандарты и нормативные материалы регламентируют проведение таких операций, в результате чего достигается требуемое качество печатной продукции.
Далее кратко описаны операции контроля и соответствующие стандарты по каждой стадии в отдельности:
1. На стадии ввода оригинала должны корректироваться измеренные цветовые координаты элементов изображения, что обусловлено недостаточной точностью аналогоцифрового преобразования устройств ввода. Эта задача решается с помощью стандартизованных шкал IT8.7/1 и IT8.7/2, выполненных на прозрачной и непрозрачной основе соответственно. Эти шкалы разработаны CGATS — комитетом по технологическим стандартам в полиграфии, входящим в международную организацию по стандартизации ISO. После считывания шкалы в устройстве ввода программное обеспечение сравнивает измеренные данные по каждому полю шкалы с соответствующими стандартными значениями. В результате получается корректирующая таблица, позволяющая компенсировать искажения, вносимые при вводе оригинала. Такая таблица соответствия (пересчета) цветовых характеристик изображения цветовому пространству конкретного устройства ввода (вывода) называется ICCпрофилем (монитора, сканера, печатной машины). При этом также переводят цветовые координаты из системы RGB в унифицированное пространство XYZ, что дает возможность упростить дальнейшую обработку массивов, обеспечивающую подготовку цветоделенных фотоформ и вывод изображения на экран монитора, а также на цветопробное устройство.
В тех случаях, когда в распоряжении пользователя имеется контрольная шкала со значительными отклонениями цветовых характеристик от стандартных значений, поступают следующим образом. Каждое поле шкалы измеряют спектрофотометром, и полученные результаты вводят в компьютер, где они используются вместо файла стандартных значений.
2. На стадии цветокоррекции производится так называемое сжатие цветового охвата оригинала, что объясняется недостаточно высоким уровнем спектральной чистоты триадных красок по сравнению с цветными фотоэмульсиями. Такая операция необходима, иначе часть цветового содержания оригинала, выходящая за пределы цветового охвата печатного процесса, неизбежно теряется, что в большинстве случаев равносильно явному браку.
Понятно, что корректное сжатие цветового охвата, как часть цветокоррекции, можно осуществить на основе определения цветовых характеристик конкретного печатного процесса, которые зависят не только от паспортных данных красок, но и от параметров производственного оборудования, а также от его фактического состояния — степени износа, качества регулировки механизмов и др.
Для определения цветовых характеристик печатного процесса предназначена шкала стандарта IT8.7/3, содержащая 928 элементов, каждый из которых образован наложением четырех красок (голубая, пурпурная, желтая, черная), взятых в различных процентных соотношениях. Эта шкала воспроизводится в печатном процессе, после чего спектрофотометром измеряют цветовые координаты всех полей ее оттиска. Измеренные данные служат основой для корректного сжатия цветового охвата оригинала, а также позволяют провести калибровку устройств получения видео и цветопробы под конкретный печатный процесс.
3. Качество фотоформ должно отвечать требованиям технологического процесса изготовления печатных форм. Эти требования определяются способом печати, применяемой технологией и материалами. При визуальном контроле должно быть установлено:
- отсутствие царапин, заломов, посторонних включений и других механических повреждений;
- наличие на фотоформе названий красок;
- соответствие углов наклона растровой структуры заданным величинам для каждой краски;
- соответствие линиатуры растровой структуры заданной;
- несовмещение изображений на фотоформах одного комплекта по крестам — не более 0,02% от длины диагонали. Это значение учитывает допуски на повторяемость при лазерном экспонировании и величину деформации пленки;
- наличие на фотоформе контрольных меток и шкал.
Процесс получения фотоформ контролируют денситометром проходящего света, с помощью которого измеряют относительные площади участков служебной шкалы, располагаемой за полем изображения. Такая шкала, как правило, содержит 11 участков со значениями относительных площадей S от 0 до 100% с шагом 10%. Определяются также оптические плотности D неэкспонированного участка шкалы (S = 0) и участка максимального почернения (S = 100%) – величины Dmin и Dmax. В соответствии с международным стандартом ISO 126472 копировальные свойства фотоформ считаются удовлетворительными при выполнении условий: Dmin ≤ 0,15;
Dmax ≥ 3,50. Кроме того, если зона размытости краев растровых точек не превышает 1/40 шага линиатуры, то качество экспонирования и химикофотографической обработки материала оценивается положительно. Для точной калибровки устройства записи фотоформ измеряют относительные площади растровых участков шкалы с номинальными значениями S = 10, 20 ... 90%. Отклонения измеренных значений от номинальных позволяют вводить соответствующие поправки в процесс получения фотоформ. Допустимыми считаются отклонения в пределах ±2%.
4. При визуальном контроле печатных форм к ним предъявляются следующие требования:
- формат печатной формы должен соответствовать техническим характеристикам печатной машины;
- форма не должна иметь никаких механических повреждений: царапин, инородных включений, трещин, воздушных пузырьков, грязи;
- на форме должны быть воспроизведены все кресты и метки, необходимые для совмещения красок в процессе печатания, фальцовки и резки;
- за пределами приводочных крестов должны располагаться шкалы оперативного контроля формного и печатного процессов;
- печатная форма должна иметь маркировку по краске;
- изображение на печатной форме должно располагаться в соответствии с требованиями по ширине поля клапана печатной машины;
- на пробельных элементах должен быть полностью удален копировальный слой. Особое внимание необходимо уделять участкам изображения с относительной площадью растровых элементов более 80%.
Оперативный контроль качества при производстве офсетных печатных форм осуществляется при помощи шкалы UGRA Plate Control Wedge. Она позволяет определять и оценивать экспозицию (время экспонирования), разрешающую способность, градационную передачу и воспроизведение растровых элементов на печатной форме. Шкала дает возможность не только объективно оценивать качество печатных форм, но и определять причины отклонений от технологических норм. Шкала состоит из пяти участков:
- полутоновые поля с оптической плотностью от 0,15 до 1,95 D для определения времени экспонирования;
- концентрические окружности из позитивных и негативных линий толщиной от 4 до 70 мкм для контроля разрешающей способности, длительности экспонирования и режима обработки. По элементу, на котором воспроизведены и позитивные и негативные линии (и они имеют одинаковую толщину) определяют разрешающую способность печатной формы;
- поля с линиями, расположенными под углом 0, 45, 90°, и поле D, которое содержит все три типа линий, позволяют контролировать скольжение и дробление при печати;
- поля с относительной площадью растровых точек от 10 до 100% (линиатура 60 лин/см) для контроля градационной передачи на печатной форме и оттиске и растискивания при печати;
- поля с мелкими растровыми элементами в светах (от 0,5 до до 5%) и тенях (от 95 до 99,5%). По ним определяют диапазон воспроизводимых на печатной форме величин растровых точек.
5. Визуальный контроль оттисков позволяет провести оценку отдельных показателей качества, таких как неравномерность тона плашки или больших однородных тоновых участков и деталей изображения. Глаз быстро улавливает даже малейшие нарушения в плавности тональных и цветовых переходов, например, на изображении неба. Большинство людей легко замечают даже малейшие искажения памятных цветов, например, на изображении лиц. Психология зрения играет немалую роль в оценке качества изображений на оттиске, но необходим объективный инструментальный контроль. Средства инструментального контроля качества печатного процесса существенно зависят от вида применяемых красок.
Для триадных красок используются денситометры отраженного света в сочетании со специальными контрольными шкалами. Посредством денситометра на оттиске шкалы определяется ряд показателей качества цветовоспроизведения:
- оптическая плотность заливки;
- растискивание;
- относительный контраст печати;
- красковосприятие;
- цветовой баланс по серому;
- ахроматичность и отклонение цветового тона.
Для нетриадных красок (Pantone, смесевые и т.д.) технология измерений иная. Поскольку оптические параметры светофильтров, применяемых в денситометрах, жестко согласованы со спектральными характеристиками триадных красок, для нетриадных красок приходится применять устройства измерения цвета, среди которых наибольшее распространение получили спектрофотометры. Эти приборы позволяют измерять цветовые координаты полей контрольной шкалы на ее оттиске в равноконтрастной колориметрической системе Lab и рассчитывать для каждого поля шкалы отклонения от соответствующих установленных значений (ΔЕ). Как показано в работах ведущих научных центров FOGRA (Германия), ВНИИ полиграфии и других, допустимое значение ΔЕ для массовой офсетной печати равно 5. При этом различие в цвете двух образцов наблюдатель едва воспринимает, что дает основание использовать эту величину как критерий качества печати.
Для объективного контроля качества фотоформ используются денситометры для работы в проходящем свете, печатных форм — денситометры для работы на отражение, а для контроля качества цветных изображений (цветопробных и тиражных оттисков) — денситометры для работы в отраженном свете и спектрофотометры.
Денситометры — это приборы, служащие для определения оптической плотности. При этом оптическая плотность не является непосредственным результатом измерения, так как в действительности измеряется коэффициент светопропускания τ или отражения ρ. Оптическая плотность — результат математического преобразования этих параметров:
Современный допечатный процесс предъявляет к денситометрам очень высокие требования по надежности и точности измерения плотностей. Качество измерительных приборов вносит существенный вклад в результат подготовки издания. К денситометрам предъявляются следующие основные требования:
- объективность результатов измерения — результат измерения не должен зависеть от визуального впечатления;
- высокая точность — значение плотности не должно зависеть от типа прибора и должно характеризовать действительное пропускание (отражение) измеряемого тона;
- высокая чувствительность — прибор должен обеспечивать точное измерение разницы плотностей в 0,010,02 D;
- воспроизводимость результатов измерения — измерения одного и того же объекта, выполненные в разное время, должны давать один и тот же результат с точностью ±(0,010,02) D;
- минимальное различие данных, полученных на разных денситометрах, — для одного и того же объекта измерения два прибора должны показывать одинаковые результаты;
- независимость от колебаний в источнике измерительного света — принцип функционирования прибора должен быть таким, чтобы результаты измерений не зависели от колебаний;
- надежность во всем диапазоне измерений.
Процесс измерения оптической плотности (рис. 2) складывается из двух стадий:
- определение коэффициента пропускания (отражения);
- перерасчет коэффициента пропускания (отражения) в оптическую плотность (логарифмирование).
Обе стадии проходят в денситометре. Некоторые типы денситометров указывают и плотность, и коэффициент пропускания (отражения).
Любое измерение — сравнение с какойлибо принятой единицей. Измеряемая плотность сравнивается с тоном, имеющим нулевое поглощение, то есть с белым тоном. При измерении в проходящем свете это исходный световой поток, освещающий измеряемый объект.
В современных денситометрах для работы в проходящем свете (рис. 3) измерения осуществляются следующим образом. Свет от источника, обычно лампы накаливания 2, отражается от рефлектора 1, разворачивается зеркалом 3, проходит через теплофильтр 4, задерживающий часть тепла, диафрагму 6 определенного диаметра и попадает на контролируемый участок фототехнической пленки 7, расположенной на предметном столе денситометра 5. Далее ослабленный световой поток проходит по световоду 8 через инфракрасный 9 или один из цветных светофильтров 10 и попадает на фотоприемник 11. Прежде в качестве фотоприемника использовались фотоэлектронные умножители, сейчас кремниевые полупроводниковые элементы.
Рис. 2. Схема измерений оптической плотности в денситометре, работающем на пропускание: Л — лампа; z — фотоэлектрические преобразователи
В зависимости от количества света, прошедшего через фотоматериал, фотоэлемент модулирует электрический импульс, который пересчитывается логическим блоком в значение оптической плотности, а также в относительное значение площади растровых элементов:
• на диапозитивной фотоформе:
на негативной фотоформе:
где Dp — оптическая плотность растрового элемента; Dc — оптическая плотность участка максимального почернения; D0 — оптическая плотность неэкспонированного участка (вуали).
Для установки денситометра на 0 осуществляют замер прозрачного участка подложки фотоматериала.
Светофильтры 10 (см. рис. 3) имеют спектральные характеристики, согласованные с характеристиками источников света, которые используются при дальнейшем копировании контролируемой фотоформы.
Рис. 3. Схема денситометра для работы в проходящем свете
В допечатных процессах применяются фотопленки трех типов, имеющих максимальную светочувствительность в различных зонах спектра: обычные (несенсибилизированные) — в ультрафиолетовой и синей зонах; ортохроматические — в желтой и зеленой; панхроматические — во всех зонах спектра. Поэтому при измерении фотоформы денситометром используют сверхфильтр, согласованный с типом чувствительности фотослоя, который будет применяться в последующем копировальном процессе.
Обычно денситометры для работы в проходящем свете комплектуются набором из трех диафрагм диаметром 1, 2 и 3 мм. Использование диафрагм разного диаметра дает возможность точно измерять оптическую плотность на фототехнических пленках, записанных с различной разрешающей способностью, а следовательно, предназначенных для печатания с разной линиатурой полиграфического растра. Для низкой линиатуры обычно применяется больший диаметр, например 3 мм, а для высокой линиатуры — меньший. Подобный подход обусловлен статистической вероятностью попадания в поле диафрагмы растровых элементов. При измерении текстовых или иных штриховых элементов в большинстве случаев используется щелевая диафрагма.
Относительная спектральная чувствительность денситометра на отражение определяется распределением энергии в спектре источника излучения, спектральной чувствительностью фотоприемника, спектральным пропусканием светопоглощающей среды денситометра и светофильтров. В отличие от денситометров, работающих с прозрачными материалами, рассматриваемый тип измеряет коэффициент отражения и пересчитывает его в оптическую плотность.
Денситометры, работающие на отражение, так же как и денситометры на пропускание, состоят из оптикомеханической части и измерительного электронного блока. Основные отличия моделей — расположение осветителя и приемника света, использование большего количества светофильтров и применение других алгоритмов при расчете измеряемых величин. Оптикомеханическая часть представляет собой фотометрическую головку, соединенную световодом с узлом светофильтров и обычно расположенную в измерительном блоке.
Принцип работы денситометров этого типа идентичен рассмотренному выше, только свет от нормированного источника с определенной цветовой температурой проходит через светофильтры, которые выделяют спектр контролируемой на оттиске краски (например, красный фильтр выделяет голубую составляющую, зеленый — пурпурную, синий — желтую), а затем регистрируется приемником. В результате денситометрических измерений определяются цветоделенные оптические плотности, которые обычно называются зональными плотностями, а на цифровом экране денситометра воспроизводятся значения плотностей измеренных красок.
Спектрофотометры. Для объективной количественной характеристики цвета используются методы, основанные на трехцветной теории зрения и позволяющие измерять цвет приборами путем аддитивного синтеза. В основе любых цветовых измерений лежит возможность точного определения цветовых координат. Пространства цветового синтеза RGB и CMYK являются нестандартизованными и аппаратнозависимыми, поэтому было предложено цветовое пространство СIELab. Оно было стандартизовано и используется в современных системах допечатной подготовки и контроля качества.
Прибором, обеспечивающим контроль цвета, является спектрофотометр. Главная его задача — расчет цветовых координат и построение спектральной кривой измеряемого объекта. Большинство спектрофотометров для полиграфических процессов имеют возможность получать координаты цвета в международных системах XYZ, CIELab и CIE LCH.
Отличие спектрофотометрических измерений от измерений человеческим глазом состоит в том, что на показания прибора не оказывают влияния посторонние факторы, такие как индивидуальные характеристики человеческого глаза, а все условия проведения измерений стандартизованы.
Рис. 4. Блок-схема спектрофотометра
Для получения представления о воспроизводимых цветах будущего печатного издания при различном освещении в спектрофотометрах используют стандартизованные источники излучения, имеющие определенные спектральные характеристики.
Человеческий глаз замечает изменения цвета только в случае превышения так называемого цветового порога (минимального изменения цвета, заметного глазом). Применяемые в современных спектрофотометрах технологии позволяют учитывать данный фактор и определять величину отклонения цвета от оригинала, названную показателем цветовых различий ΔE:
где L, a, b — цветовые координаты оригинала, L’, a’, b’ — цветовые координаты, полученные при измерении цветопробного, печатного оттиска и т.д.
Такое измерение позволяет оперативно и точно определить возможные корректировки технологических режимов печатания, например подачу краски, увлажняющего раствора, давления в печатной паре, или внести предыскажения еще на стадии допечатной подготовки, например цветокоррекции.
На рис. 4 представлена блоксхема, а на рис. 5 — схема считывающей головки. Колориметрические измерения по приведенной схеме осуществляются следующим образом. Луч света 1 от источника света 2 (лампы с цветовой температурой, выбранной по соответствующим стандартам) проходит через коллиматор 3, который формирует узкий параллельный пучок лучей, затем через апертуру определенного диаметра 4 и попадает на оттиск 5. Отразившись от него, свет по волоконнооптическим световодам 6, 7 и 8 попадает на набор светофильтров. Считывание информации с образца происходит одновременно только по двум каналам. Этому способствуют специальные затворы 9 и 10, приводимые в движение с помощью двигателей 11 и 12.
Рис. 5. Считывающая головка спектрофотометра
После прохождения по световодам луч света попадает на комплекс фильтров, имеющих определенную полосу пропускания. Как и в случае с денситометрами на отражение, в комплект со спектрофотометрами входят различные поляризационные фильтры.
Прошедший через фильтры свет попадает на фотоэлектронный умножитель, который усиливает сигнал и посылает его на аналогоцифровой преобразователь. Тот, в свою очередь преобразует аналоговый сигнал в цифровой для последующей обработки центральным процессором прибора. После обработки информации данные индицируются на дисплее и могут быть распечатаны на принтере или введены в персональный компьютер.
В некоторых спектрофотометрах для разложения хроматического излучения (белого света) на основные цветовые компоненты используются монохроматоры, в состав которых входит призма или дифракционная решетка. При этом монохроматическое излучение с дискретным интервалом в несколько нанометров проходит через ту часть прибора, где располагается образец с исследуемой пробой.
Рис. 6. Монохроматор на основе призмы: 1 — входная щель; 2 — объектив, формирующий параллельный поток световой энергии; 3 — призма; 4 — объектив, направляющий поток энергии на экран; 5 — экран; 6 — выходная щель
Монохроматор на основе призмы (рис. 6) имеет щель 1, на которую падает хроматический поток световой энергии, находящуюся в фокальной плоскости линзы 2. Эта часть прибора называется коллиматором. Выходящий из объектива 2 параллельный поток световой энергии падает на призму 3. Вследствие дисперсии (обусловленной зависимостью показателя преломления от длины волны) свет различных длин волн выходит из призмы под разными углами. Если в фокальной плоскости линзы объектива 4 поставить экран 5, то линза сфокусирует параллельные потоки энергии для различных длин волн в разных местах экрана. Поворачивая призму 3, можно просканировать через щель 6 монохроматические потоки энергии во всем спектре излучения. Эти монохроматические потоки последовательно, с некоторым интервалом длин волн направляют на исследуемый образец. В монохроматорах другого типа применяется дифракционная решетка, которая представляет собой стеклянную или металлическую пластину с нанесенными одинаковыми параллельными штрихами. Штрихи расположены на строго одинаковом расстоянии друг от друга. На рис. 7 показана дифракционная решетка, состоящая из чередующихся, параллельных друг другу щелей одинаковой ширины b, расположенных на одном и том же расстоянии а друг от друга. Сумма а + b является периодом этой структуры и называется постоянной решетки d.
Рис. 7. Монохроматор на основе дифракционной решетки: 1 — входная щель; 2 — объектив, формирующий параллельный поток световой энергии; 3 — дифракционная решетка; 4 — объектив, направляющий поток энергии на экран; 5 — экран; 6 — выходная щель
Через входную щель 1 хроматический поток световой энергии линзой объектива 2 трансформируется в параллельный поток, который проходит через щели дифракционной решетки 3. В каждой точке на экране 5, расположенном в фокальной плоскости линзы объектива 4, соберутся лучи, которые до линзы были параллельными между собой и распространялись под определенным углом Q к направлению падающей волны. Поэтому освещенность в точке на экране 5 определяется результатом интерференции вторичных волн, распространяющихся как от разных участков одной щели, так и от разных щелей. Существует направление, распространяясь по которому вторичные волны от всех щелей будут приходить в точку экрана в одной фазе и усиливать друг друга, и направление, когда волны не совпадают по фазе и ослабляют друг друга. Таким образом, на экране наблюдается чередование светлых и темных полос. Условие формирования максимумов от дифракционной решетки, то есть когда волны усиливают друг друга при интерференции, соблюдается в том случае, если разность хода равна целому числу волн.
Если на решетку падает свет разных длин волн, то максимумы для различных длин волн располагаются под разными углами Q к первоначальному направлению распространения света. Поэтому дифракционная решетка разлагает хроматический свет в дифракционный спектр и употребляется как диспергирующий прибор.
Дифракционная решетка технологически более сложное изделие, чем призма. Большинство применяемых в настоящее время решеток изготовлены способом выжигания и голографического копирования и представляют собой пластины с большим числом параллельных штрихов — до нескольких сот на миллиметр.
Основным преимуществом использования призмы в спектрофотометре является ее низкая стоимость. Преимущество дифракционных решеток состоит в том, что они обеспечивают линейную дисперсию света на всем диапазоне видимого и УФспектров. Недостатком дифракционных решеток является их высокая стоимость в сравнении с призмами и светофильтрами.
Одна из самых важных характеристик монохроматоров — полоса пропускания, выражаемая в единицах длин волн — нанометрах.
Если интерференционные фильтры дают ширину пропускания в диапазоне 620 нм, то призмы и дифракционные решетки обеспечивают более узкую полосу — менее 5 нм, а следовательно, и большую «чистоту» (монохромность) света, падающего на исследуемый образец. Полоса пропускания является одной из важнейших характеристик спектрофотометра.