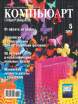
Готовим увлажняющий раствор
Увлажняющий раствор, его показатели и состав
Основные показатели увлажняющего раствора
Факторы, определяющие состав увлажняющего раствора
Если послушать печатников, то самые большие проблемы, связанные с качеством офсетной печатной продукции, возникают из-за нарушения баланса «краска — вода» в процессе печатания тиража.
Процесс печати офсетным способом зависит от того, насколько устойчиво смачиваются пробельные элементы печатной формы увлажняющим раствором, а печатающие — краской, и установлен ли оптимальный баланс «краска — вода».
Чтобы увлажнение печатной формы было устойчивым, перед нанесением красочного слоя необходимо нанести на нее увлажняющий раствор. Эта технологическая операция производится с помощью увлажняющего аппарата, обеспечивающего равномерную и достаточную подачу увлажняющего раствора на печатную форму в процессе печатания. Вроде бы никакой сложности в этом нет. Но это только иллюзия, потому что недостаточное увлажнение приводит к нарушению гидрофильности пробельных элементов и, как следствие, — к тенению печатной формы. Результатом же чрезмерного увлажнения являются разводы на оттисках, бледная печать, неравномерность наката краски, отмарывание, а также увеличение времени сушки оттисков.
Все нарушения, а названа лишь небольшая их часть, связаны с составом и режимом нанесения увлажняющего раствора. Они являются частью одной большой проблемы офсетной печати — нарушения баланса «краска — вода», что в конечном счете приводит к получению некачественной продукции, которая очень дорого обходится полиграфическому предприятию.
Для решения этой проблемы прежде всего необходимо подробно изучить составляющие этого баланса и их взаимодействие.
Итак, из чего состоит баланс? Определим его «участников», рассмотрим их по отдельности и обозначим их связи. Однако самое важное для нас — это результаты отдельных нарушений в их составе и сочетании.
Назовем «участников» печатного процесса: увлажняющий раствор, печатная краска, печатная форма и запечатываемый материал. Начнем с самого главного, ведущего «участника» — увлажняющего раствора.
Увлажняющий раствор, его показатели и состав
Увлажняющий раствор представляет собой слабокислый или слабощелочной электролит. Водопроводная вода как увлажняющий раствор имеет относительно низкую эффективность, поэтому на практике при создании увлажняющего раствора применяют различные многокомпонентные добавки. В увлажняющий раствор входят:
- вода;
- гуммиарабик — (камедь)/кислоты/соли. С его помощью происходит подтравливание формы. Наличие гуммиарабика и кислых солей необходимо для поддержания чистоты увлажняющих валиков и гидрофилизации формы без агрессивного воздействия. В настоящее время вместо фосфорного гуммиарабика чаще используются синтетические, действующие в широком диапазоне рН и кислот;
- буферная добавка. Данный компонент нужен для поддержания кислотности. Для современных форм с электрохимическим зернением и анодированием необходимо слабое воздействие кислоты. Буферная добавка обеспечивает постоянный уровень рН, что помогает избежать проблем с увлажнением, а именно, плохого высыхания краски (листовой офсет) и коррозии форм и узлов печатных машин. Буферный раствор способствует впитыванию кислот или щелочей из бумаги, краски и химикатов. Высокая карбонатная жесткость местной воды увеличивает pH;
- смачивающий реагент (поверхностноактивное вещество ПАВ) снижает поверхностное натяжение (рис. 1). Низкое поверхностное натяжение обеспечивает лучшее смачивание формы, что, в свою очередь, уменьшает расход воды для офсетной печати. Для уменьшения поверхностного натяжения применяются сурфактанты (ПАВ);
- биоциды (антибактериальные добавки) предотвращают образование бактерий. Бактерии и микроорганизмы есть в воде, бумаге, краске и воздухе. Увлажняющий раствор обеспечивает идеальную среду для размножения бактерий благодаря теплу и выделению питательных веществ гуммиарабиком, бумажными волокнами и т.п. Определенные виды бактерий выделяют газ с неприятным запахом, образуют плесень, засоряя систему циркуляции увлажняющего раствора. Наличие биоцидов в увлажнении контролирует рост бактерий в соответствующей дозировке. Чаще всего первым признаком проблемы является увеличение рН после ночных перерывов или выходных.
Рис. 1
Во избежание проблем с бактериями необходимо:
- обеспечивать правильную дозировку,
- применять двойную дозировку на ограниченные периоды,
- использовать очистители для системы,
- использовать другие добавки;
- антивспениватели необходимы для уменьшения пенообразования. Помимо загрязнения пена может являться причиной неравномерной подачи увлажняющего раствора. Причины пенообразования:
- недостаточное количество или неправильный подбор антивспенивателя,
- попадание воздуха в обратный трубопровод,
- слишком узкие трубы,
- неправильная посадка фильтров,
- слишком маленький размер сетки фильтра,
- забивание фильтров,
- сурфактант в смывке для резины;
- антивспенивающие добавки входят в состав концентрата увлажняющего раствора. Температура и поверхностное натяжение влияют на пенообразование;
- связующие кальция снижают наличие кальция в жесткой воде. Они противодействуют осаждению имеющихся в воде солей кальция на валиках и печатных формах. Отложения кальция могут сделать красочные валики гидрофильными (восприимчивыми к воде), препятствуя переносу краски с валиков на форму;
- антикоррозионные добавки (ингибиторы коррозии), минимизирующие коррозию, входят в состав концентрата увлажнения и защищают металлические части машины от коррозии. Производители печатного оборудования с особой строгостью проверяют увлажняющие растворы на низкий порог коррозийности.
От состава и рабочих свойств применяемого увлажняющего раствора во многом зависят устойчивость и стабильность гидрофильных свойств пробельных элементов печатной формы. Эти свойства могут измениться в результате износа пробельных элементов формы и в первую очередь пленок на их поверхности, созданных в процессе гидрофилизации. Увлажняющий раствор может оказывать существенное влияние и на поведение печатающих элементов, так как он разрушает адсорбционную олеофильную пленку, являющуюся их основой.
Рекомендуемые для применения в процессе печатания увлажняющие растворы включают следующие компоненты:
|
К увлажняющему раствору технологи типографий предъявляют следующие требования:
- должен хорошо смачивать гидрофильные пробельные элементы и обеспечивать постоянство их свойств в процессе печатания;
- не должен отрицательно влиять на гидрофобные слои печатающих элементов, вызывать эмульгирование печатных красок и изменять их спектральные и структурномеханические характеристики, вызывать коррозию металлов формы и деталей печатной машины;
- не быть агрессивным по отношению к бумаге и не вызывать изменения свойств ее поверхности — смачиваемости. Раствор не должен иметь запах и цвет, а также содержать токсичных веществ.
Пленка увлажняющего раствора, наносимая на поверхность пробельных элементов формы, имеет определенную толщину, обеспечивающую устойчивость пробельных элементов в течение всего периода печатания тиража. Толщина пленки зависит от структуры и материала печатной формы: для биметаллических форм она составляет 0,71,1 мкм, для монометаллических — до 2 мкм.
Следует подчеркнуть, что рабочие свойства и параметры увлажняющего раствора стабилизирует постоянный температурный режим. Температуру увлажняющего раствора в корыте увлажняющего аппарата рекомендуется поддерживать в пределах 1214 °С, конечно, если это возможно.
Большое значение имеет не только количество подаваемого увлажняющего раствора, но и качество воды и добавок, используемых при его составлении.
![]() |
![]() |
Основные показатели увлажняющего раствора
Основными показателями, определяющими эксплуатационные качества увлажняющего раствора, являются:
- кислотность;
- жесткость;
- электропроводность.
Рассмотрим эти показатели и их влияние на рабочие свойства увлажняющего раствора.
Кислотность (рН) увлажняющего раствора
Водородный показатель (рН) [power of hydrogen] — это параметр, характеризующий концентрацию ионов водорода в растворе, то есть выражающий степень его щелочности или кислотности. Показатель рН может варьироваться от 0 до 14. Раствор с рН 7 является нейтральным, ниже 7 — кислым, выше — щелочным.
В процессе печатания рН увлажняющего раствора меняется изза изменения его состава вследствие коррозии металла увлажняющего аппарата и влияния применяемых при печатании материалов — бумаги, картона, фольги, различных видов красок и добавок к ним.
Уровень рН увлажняющего раствора и бумаги имеет решающее значение для стабильности процесса офсетной печати. Величину рН увлажняющего раствора следует контролировать при помощи лакмусовых бумажек или электронного прибора как при подготовке и заливке увлажняющего раствора в печатную машину, так и в процессе печатания тиража. Кислотность бумаги проверяют в лабораторных условиях при получении новых партий.
При оценке рабочих свойств увлажняющего раствора следует учитывать, что наиболее благоприятный диапазон величин рН находится в интервале между 4,8 и 5,5 (рис. 2).
Рис. 2. Шкала кислотности
При рН менее 4,8:
- разрушается гидрофильная пленка на пробельных элементах печатной формы, что вызывает тенение;
- замедляется закрепление краски на оттисках изза нарушения процесса ее окислительной полимеризации, что может вызвать отмарывание в процессе печати;
- снижается прочность красочной пленки оттиска на истирание;
- оголяются металлические раскатные цилиндры красочного аппарата изза снижения липкости краски, что нарушает равномерность ее подачи и ведет к непропечатке мелких деталей изображения на оттиске.
- При рН более 5,5:
- происходит «омыление» печатной краски (появляется сероватый оттенок на оттиске);
- печатная краска эмульгирует и наслаивается на валиках красочного аппарата, происходит тенение печатной формы в процессе печати;
- разрушаются печатающие элементы формы, что приводит к снижению ее тиражестойкости и необходимости ее замены в процессе печати тиража.
Жесткость воды, используемой для приготовления увлажняющего раствора
Наряду с величиной рН увлажняющего раствора печатник должен обращать внимание и на жесткость воды (дН — показатель жесткости), используемой для приготовления увлажняющего раствора. Под жесткостью воды понимают содержание в ней солей кальция и магния. Различают несколько степеней жесткости.
Классификация воды по уровню жесткости (дН):
- ниже 4 — очень мягкая;
- 48 — мягкая;
- 812 — среднежесткая;
- 1218 — довольно жесткая;
- 1830 — жесткая;
- свыше 30 — очень жесткая.
Оптимальным значением показателя жесткости воды, применяемой для изготовления увлажняющего раствора, является 512. Если же он выходит за указанные пределы, то в процессе печати тиража могут возникнуть следующие проблемы:
- при показателе жесткости меньше 5 увлажняющий раствор «забирает» недостающие соли из бумаги и печатной краски, что вызывает слабое закрепление краски на оттиске;
- при показателе жесткости больше 12 образуется нерастворимый известковый осадок, оседающий на валиках, офсетном полотне, печатной форме, что приводит к нарушению печатного процесса. Соли кальция и магния взаимодействуют с жирными кислотами, содержащимися в печатных красках (то есть происходит «омыление»), и жирный слой оседает на офсетной форме, накатных и увлажняющих валиках, вызывая тенение в процессе печати.
Жесткость измеряется довольно просто при помощи специальных индикаторных палочек. При очень жесткой воде с высоким содержанием солей ее рекомендуется смягчать или полностью обессоливать.
Электропроводность увлажняющего раствора
Электропроводность увлажняющего раствора взаимосвязана с параметрами рН и дН. Она характеризует содержание в нем солей и различных добавок. Электропроводность водопроводной воды обычно колеблется от 300 до 500 мкСм (микроСименсов).Рабочая электропроводность увлажняющего раствора должна быть в пределах от 800 до 1500 мкСм:
- при электропроводности ниже 800 мкСм увлажняющий раствор начинает «забирать» соли из печатной краски и бумаги, что вызывает слабое закрепление краски на оттиске. То же наблюдается и при низкой жесткости воды. Отличие заключается в том, что причиной снижения электропроводности может быть не только жесткость воды, но и количество и химический состав добавок;
- при электропроводности выше 1500 мкСм соли, содержащиеся в увлажняющем растворе в избытке, взаимодействуют с печатной краской, что приводит к ее эмульгированию. Соли также могут оседать на валиках увлажняющего и красочного аппаратов печатной машины.
![]() |
![]() |
Факторы, определяющие состав увлажняющего раствора
Выбор состава увлажняющего раствора должен зависеть от:
- типа печатного оборудования — рулонные и листовые печатные машины работают с разными скоростями и красками, что определяет и состав увлажняющего раствора;
- системы увлажнения — традиционные (с чехлами на валиках, работающие без спиртовой добавки) или спиртовые; контактные или бесконтактные. При спиртовом увлажнении машины, как правило, снабжены системой охлаждения и рециркуляции увлажняющего раствора, позволяющей уменьшить количество спиртовой добавки, и автоматически контролирующей и поддерживающей на заданном уровне кислотность раствора и содержание в нем спирта.
Перечислим объекты контроля на печатной машине:
- исходный состав используемой водопроводной воды, то есть ее жесткость и электропроводность;
- качество и состав используемых красок. Производители увлажняющих растворов указывают, для работы с какими типами красок они предназначены;
- качество, состав и впитывающая способность запечатываемых материалов;
- тип печатных форм (характеристики основы и состава копировального слоя).
При подготовке публикации использованы: материалы из книги Н. Марогуловой и С. Стефанова «Расходные материалы»; технические данные от компании FlintGroup.
![]() |
![]() |