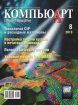
Настройка подачи краски в печатных машинах
Эффективность печатного процесса зависит не только от технических характеристик машины и мастерства печатников, но и от соотношения затрат времени непосредственно на печать тиража и на подготовку к процессу печатания. Особенно значительным оказывается время на подготовку к печати многокрасочной продукции, а упомянутое соотношение существенно ухудшается при малых тиражах. Да и в процессе печатания производительным можно считать только время печати оттисков, соответствующих требованиям, предъявляемым к качеству продукции. В основном эти требования имеют четкие критерии оценки и поддаются инструментальному контролю. Общеизвестны номиналы и допустимые отклонения таких параметров, как оптическая плотность, площадь растровой точки, совмещение красок и др.
Индикаторы и органы зональной регулировки подачи краски на пульте управления листовой печатной машины японской фирмы RYOBI (на выставке drupa 2012)
Осуществляя подготовку к тиражированию, печатник старается настроить машину в соответствии с заданными требованиями. Одной из ответственных операций подготовки машины к работе является настройка красочных аппаратов печатных секций и, в частности, их краскоподающих узлов. Если полиграфист сделал предварительную настройку краскоподающих узлов «на глазок», то синтезируемые на оттисках цвета могут быть далеки от эталона и ему придется корректировать подачу краски в секциях по ходу печати. При этом будут печататься оттиски, не соответствующие требуемому качеству продукции, а при малых тиражах процесс корректировки, возможно, так и не будет доведен до оптимального. Наилучшей будет ситуация, при которой одинаковым печатающим площадям на оттиске соответствует одинаковая оптическая плотность и, соответственно, одинаковое количество краски, нанесенное на эти участки запечатываемого материала (рис. 1).
Рис. 1. Примерная схема передачи краски через красочный аппарат
Следовательно, если известны площади печатающих элементов в каждой красочной зоне, то может быть заранее вычислена и необходимая зональная подача краски. Правда, при этом надо учитывать некоторые особенности выхода краски из краскоподающего узла. В частности, чтобы краска на стекала с торцов дукторного цилиндра (а затем по ходу раската краски в красочном аппарате с торцов валиков и раскатных цилиндров) подача краски в крайних зонах искусственно ограничивается, вплоть до полного закрытия зазора между поверхностями дукторного цилиндра и регулирующего элемента — кромки красочного ножа, шибера, эксцентрика и т.п. Поэтому необходимые в данных зонах порции краски должны учитываться при расчете подачи в соседних с ними зонах. Краскоподающие узлы со сплошным красочным ножом (применяемые в большинстве отечественных машин) диктуют свою специфику — при зональной регулировке красочного зазора жесткость кромки ножа увязывает между собой параметры настройки соседних зон: уменьшение или увеличение зазора в одной зоне приводит к сужению или расширению зазора в двухтрех соседних зонах с каждой стороны. Чтобы избавиться от этой зависимости, многие фирмы внесли в конструкцию краскоподающих узлов своих машин изменения, заменив сплошной нож на разрезной, или вовсе отказались от ножа в пользу, например, эксцентричных цилиндрических элементов [1], шиберов [2] (рис. 2) или иных решений.
Рис. 2. Механизм зональной настройки краскоподающих узлов Colortronic фирмы КВА
Расчет программы настройки осложняют и другие обстоятельства, о которых следует упомянуть. Речь идет о раскате краски и инерционных свойствах красочного аппарата. При большой разнице по толщине красочного слоя в соседних зонах (обусловленной соответствующими площадями печатающих элементов на форме) в результате осевого раската краска будет уходить из зон, подающих толстые слои в соседние зоны с более тонкими слоями, и тем самым нарушать первоначальные соотношения зонального профиля краски, поступившего в раскатную систему.
Некоторая доля неконтролируемости процесса настройки красочного аппарата делает длительными переходные режимы при изменении подачи краски, что обусловлено не только транспортным запаздыванием передачи слоя краски через валики и цилиндры, но и инерцией установления баланса между приходом и расходом краски в каждой регулировочной зоне. Если сравнить красочный аппарат с инерционным звеном, реализованным на простой электрической RCцепочке (где R — сопротивление, а C — емкость), то роль емкости в красочном аппарате выполняют красконесущие поверхности валиков и цилиндров, а роль сопротивления — совокупность участков контакта этих поверхностей между собой (как электрический ток ограничивается сопротивлением резисторов, так и поток краски зависит от пропускной способности участка контакта). Например, если накатной валик входит в контакт с пробельным элементом формы, то краска не может перейти с накатного валика на форму (что эквивалентно разрыву контакта или, в приведенной аналогии, — бесконечно большому сопротивлению). Как было установлено исследованиями, проведенными во ВНИИ полиграфии [3], наибольшее значение в этом смысле имеет относительная площадь печатающих элементов: чем меньше эта площадь, тем большее сопротивление встречает на своем пути к оттиску красочный поток, а следовательно, тем дольше длится переход к состоянию баланса между приходом и расходом краски в данной зоне.
Рис. 3. Влияние относительной площади печатающих элементов на длительность переходных процессов передачи краски через красочный аппарат. А — момент увеличения подачи краски; В — момент уменьшения подачи краски; а — переходный процесс в зоне 100-процентной площади длится менее 50 печатных циклов; в — в зоне 40-процентной площади он длится около 120 печатных циклов; с — в зоне 5-процентной площади — почти 250 печатных циклов
Позднее этот вывод подтвердился в результатах исследований [4] института FOGRA (Forschungsgesellscaft fur Druck und Reproduktionstechnologie — Немецкая исследовательская ассоциация по технологиям печати и репродуцирования). Специалисты FOGRA установили [5], что с точки зрения динамики реакции оптической плотности оттисков на изменение подачи краски (рис. 3) длительность переходных процессов в красочных аппаратах зависит от площади заполнения формы печатающими элементами: чем меньше печатающих элементов, тем длительнее переходный процесс (см. также [3, 6]), а следовательно, тем большее число оттисков (от 40 до 500) не будет соответствовать эталонным показателям качества. Были выработаны рекомендации, которые предусматривают после изменения подачи краски печатание определенного количества оттисков (см. таблицу) с целью получения результатов этих изменений перед принятием решения о дальнейших корректировках.
Еще один возмущающий фактор — увлажнение пробельных элементов офсетной формы, что также необходимо учитывать при настройке подачи краски. Технологические исследования во ВНИИ полиграфии [6] позволили установить закономерности взаимодействия краски и влаги в процессе печати, которые свидетельствуют, что при одной и той же подаче краски можно получить как качественный оттиск, так и оттиск с теми или иными дефектами, если не следить за подачей увлажняющего раствора (рис. 4).
Рис. 4. Диаграмма влияния подачи краски и увлажняющего раствора на качество оттисков при офсетной печати
Центр диаграммы соответствует нормальной подаче краски и влаги, при которых оптические плотности плашек (Dп) и контрольных растровых полей (Dр) имеют стандартные номинальные значения. Радиус диаграммы равен 0,4 от номинала. По периферии диаграммы явно проявляются дефекты — при избытке краски и недостатке влаги появляется запечатка пробелов, при избытке влаги и недостатке краски — заливка печатающих элементов водой, при недостаточной подаче краски — непропечатка. Собственно по появлению этих дефектов печатник и судит о нарушении баланса «краска/влага» (при отсутствии средств объективного контроля) и старается вести процесс печати в жестко ограниченной бездефектной области.
Зависимость длительности переходных режимов от площади печатающих элементов
Относительная площадь запечатываемой поверхности, % |
Рекомендуемое число оттисков между регулировками |
|
при больших изменениях |
при малых изменениях |
|
5 |
500 |
200 |
15 |
400 |
150 |
30 |
350 |
120 |
50 |
300 |
100 |
100 |
250 |
80 |
Эллиптические зоны вокруг центра очерчивают примерные границы изменения подачи краски и влаги, при которых оптические плотности будут находиться в допустимых пределах. По мере удаления от оптимальных значений подачи краски и влаги параметры выходят за поля допусков, что на диаграмме отражено эквипотенциальными линиями (сплошные обозначают одинаковые значения Dп, а пунктирные — Dр). Эти линии свидетельствуют о том, что если изменяется только подача краски, то оптические плотности плашек и растровых полей меняются пропорционально, а при избытке или недостатке влаги на форме эта пропорциональность нарушается (эквипотенциальные сплошные и пунктирные линии расходятся, удаляясь влево и вправо от вертикальной оси), что может быть выражено в изменении величины контраста: Кк = (Dп – Dр)/Dп.
Рис. 5. Зависимость контраста от изменения подачи влаги
При трансформации диаграммы зависимость контраста Kк (рис. 5) от величины подачи увлажняющего раствора Y отчетливо заметна — коэффициент Kк максимален при оптимальной подаче увлажняющего раствора. Поскольку для вычисления Kк нужно знать только соответствующие величины Dп и Dр, то эти данные можно получить путем измерения денситометром оптических плотностей плашек и растровых меток соответствующих цветов по контрольным шкалам на оттиске.
Перечисленные факторы серьезно осложняют процесс настройки подачи краски в печатной машине, что выражается в потерях времени, расходных материалов, снижении качества продукции. Существенную помощь печатнику в решении этих вопросов оказывают современные системы автоматизированной настройки машины перед печатью. Большинство фирм — производителей листовых и рулонных печатных машин (Heidelberg, KBA, KOMORI и др.) предлагают технические и программные средства для выполнения настройки подачи краски в автоматическом режиме.
Если форма делается по выклеенному фотомонтажу, то еще до ее установки в печатной машине она сканируется на плейтсканере (рис. 6), который выдает исходные данные для определения относительных площадей печатающих элементов в каждой зоне регулирования подачи краски и расчета программы предварительной настройки краскоподающих узлов, которая затем реализуется через пульт управления печатной машины.
Рис. 6. Плейтсканер Scantronic фирмы КВА
Рис. 7. Пульт управления машины Rapida фирмы КВА
Рис. 8. Пример реализации программы зональной настройки подачи краски
При компьютерной верстке полос будущего издания данные о значениях относительных печатающих площадей могут быть получены программным путем еще в издательстве (при этом отпадает необходимость измерения форм на плейтсканере) и рассчитанная по заданным алгоритмам программа настройки органов регулировки подачи краски может быть заранее передана на пульт управления (рис. 7) соответствующей печатной машины. Три дисплея (один из них — уоллскрин — позволяет представлять оттиск в натуральную величину) обеспечивают печатника максимально полной информацией о печатном процессе, в том числе и о подаче краски.
На рис. 8 приведен пример оптимальной настройки по данным о зональных относительных площадях, реализованной в программном пакете Heidelberg CPC Simulation [7]. По результатам измерений осуществляется сравнение текущих значений с номиналами и допусками, а выявленные отклонения индицируются на экране дисплея и могут устраняться в автоматическом или ручном режиме.
Практика показывает, что около 70% работы по настройке подачи краски можно выполнить до начала печати тиража, а тонкую регулировку закончить уже в процессе печати. Особенно актуально это для крупноформатных машин (рис. 9).
Рис. 9. На выставке drupa 2012 печатники демонстрируют форму из машины GOSS Sunday
При работе на многосекционных печатных машинах системы настройки красочных аппаратов дают значительную экономию времени, позволяют сократить отходы в брак и повысить качество печатной продукции. Одним из лидеров в области автоматизации процессов подготовки машины к печати является японская фирма KOMORI. На листовой офсетной печатной машине этой фирмы LS 26/29 процесс переналадки на новый тираж длится всего 6 мин (рис. 10). При этом 2,5 мин отводится на смену форм, установку формата листа и передачу данных об изображении, 52 с — на предварительный накат краски и печать 30 приладочных листов, всего 45 с — на коррекцию приводки и подачи краски, в течение 1 мин 29 с осуществляется печать 200 тиражных листов и удаление красочного профиля, а за 24 с производится смывка офсетного полотна [8].
Рис. 10. Временные затраты на осуществление приладки листовых печатных машин KOMORI LS 26/29
Еще более оперативно происходит переход с тиража на тираж на рулонных многосекционных машинах KOMORI System 38S [9]. Во время выставки drupa на этой рулонной машине демонстрировались уникальные возможности печатания малых тиражей (2000 экз.) при чрезвычайно коротких промежутках времени на переналадку (3 мин 30 с на переход от одного тиража к другому) благодаря полностью автоматической одновременной смене восьми форм и компьютерному управлению настройкой машины на печать. Собственно процесс печати тиража длился менее двух минут на скорости более 10 м/с (60 тыс. экз./ч).
При столь быстром тиражировании продукции печатник только раскладывал новые формы по кассетницам устройств автоматической смены форм и следил за мониторами, практически не вмешиваясь в процесс печати — всё управление осуществлялось автоматическими системами. Важнейшими среди них являются устройства автоматической стабильной подачи расходных материалов (краска, бумага, увлажняющий раствор) и поддержания качества оттисков.
Литературные источники информации
- Штоляков В.И. Печатные системы фирмы Heidelberg. Офсетные печатные машины / Штоляков В.И., Федосеев А.Ф., Зирнзак Л.Ф., Егоров И.А., Вартанян С.П., Артыков Э.С. — М.: МГУП, 1999. 216 с.
- Штоляков В.И. Листовые офсетные печатные машины КВА / Перова А.А., Штоляков В.И., Федосеев А.Ф., Вартанян С.П. — М.: МГУП, 2007. 140 с.
- Вартанян С.П. Особенности динамики красочных систем. Статья в сборнике трудов ВНИИПП, т. 22, вып. 2. — М.: ВНИИПП, 1972. С. 3945.
- Dr.Haas, FOGRA Report 3.279 Regeltechnische Charakterisierung der Farbwerke von Bogenoffset maschinen. — Munchen, FOGRA, 1994.
- Spectral Quality Measurement and Control // KBA Report 2000. No. 14. p. 2022.
- Батюшко А.Л. Проблемы автоматизации офсетного печатного процесса / Батюшко А.Л., Вартанян С.П., Избицкий Э.И., Каган Б.В., Шахмундес Л.А. — М.: Книга, 1978. 96 с.
- Heidelberg Computer Print Control Simulation. — D69019, Heidelberg, Heidelberger Druckmaschinen AG, 1993. 36 p.
- LITHRONE S26/S29. — M.: YAM International, 2006. 20 p.
- SYSTEM 38S. — M.: YAM International, 2004. 16 p.