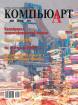
Калибровка широкоформатной печати
В начале сентября компания X-Rite совместно с компаниями Apostrof и «Смарт-Т» провела семинар, на котором обсуждался контроль качества цифровой печати. На базе приборов (рис. 1), программного обеспечения X-Rite и широкоформатного оборудования (рис. 2), которое установлено в демонстрационном зале московской компании «Смарт-Т», решались типовые задачи точного воспроизведения цвета.
В ходе практического семинара проводились цветокалибровка цифровых печатных устройств и построение ICC-профилей для различных типов материалов, в том числе бэклитов (печать на пленочных носителях) и текстиля.
Теория
С чем обычно сталкиваются заказчики типографии или печатного салона? С банальными проблемами при воспроизведении красочных изображений и с несоблюдением такого важного параметра, как баланс по серому, — всегда видно, когда серый оттенок «падает» в другие оттенки. Крайним в этой цепочке почемуто является печатник. На самом деле это происходит изза отсутствия на производстве системы управления цветом, которая предназначена для решения следующих задач:
- воспроизводимость результата и его повторяемость;
- сокращение брака, трудовых затрат и времени на изготовление заказа.
В любом случае в споре с заказчиком выстроенная система управления цветом в типографии является весомым аргументом.
Кроме того, возникает путаница в терминах «управление цветом» и «калибровка печатного процесса». Калибровка — это манипуляции с печатной машиной, ее настройка. Управление цветом — это технология, относящаяся в первую очередь к препрессу. Калибровка является основой для системы управления цветом. Ее задачи (а в данной публикации, напомним, речь идет о широкоформатной печати) — это достижение оптимальной подачи количества чернил (плюс их экономия), исключение растекания, при этом рулон не должен слипаться. Заказчика при этом должна радовать отличная тоновая передача (плавное приращение тона), стабильный и воспроизводимый результат, получение естественных цветов и градации серого.
Рис. 1. Новый уровень точности воспроизведения цвета для допечатных и печатных процессов обеспечивают приборы i1Pro 2 (для калибровочных процессов) — а; портативный спектрофотометр/денситометр eXact (X-Rite) для измерения в отраженном свете (контроль оттисков на печатном производстве) — б
Несколько советов при подготовке принтера к линеаризации и построению ICC-профилей:
Перед проведением процедуры линеаризации и построения ICC-профиля температура предварительного нагрева должна соответствовать той, на которой будет осуществляться коммерческая печать на этом материале. |
Практика
На семинаре настройку «идеальной печати» предлагалось произвести на «трудном» материале — глянцевой самоклейке, которая повсеместно используется, и с ней больше проблем по сравнению с матовой: более значительное растекание чернил и слипание в рулоне.
Рис. 2. Сублимационный плоттер Mimaki TS34-1800A специально разработан для рынка термотрансферной печати и производит высокоскоростную струйную печать (скорость до 83 м2) фотографического качества по полиэфирным тканям, самоклейке и другим материалам
Для калибровки использовался растровый процессор Wasatch SoftRIP (7я версия), который считается одним из лучших среди растровых процессоров для цифровой печати (рис. 3). Файлы тестовых изображений поставляются с программным обеспечением. Калибровка начинается с подготовительного этапа. Проверяется, полностью ли исправна печатная машина (принтер), все ли дюзы работают, отсутствует ли полошение и т.д. Затем нужно правильно определиться с режимом печати и выбрать нужное разрешение печати — в нашем случае 720 на 1080 точек; вид растрирования — стохастика. Это начало первого этапа работы.
Рис. 3. Интерфейс RIP’а широкоформатного плоттера
Рис. 4. Ведущий семинара, менеджер-технолог ООО «Апостроф» Дмитрий Кобзарь показывает первую тестовую шкалу, отпечатанную на неоткалиброванном печатном устройстве
Итак, тестовая шкала на сублимационном плоттере Mimaki TS341800A распечатана (рис. 4). На ней было заметно растекание чернил в розетках и плашках, везде завалы черного цвета — практически отсутствует разница между 80 и 100процентными плашками. Красный цвет имеет наплывы чернил, то есть при 100процентной заливке явный перебор количества «мадженты» и желтой краски, а получившаяся с зеленосинем оттенком розетка в реальности должна быть серой.
После анализа этого распечатка в настройке «Трансформации цвета» убираются цвета (или уменьшается подача чернил каждого цвета) до 85% (рис. 5). При этом теряется насыщенность цветов, но нужно учитывать, что «циан» и «маджента» в изображениях в чистом виде практически отсутствуют. Желтая краска фактически «слепая». Теперь в RIP поступили данные о сокращении подачи чернил на 15%. В результате принтер будет лить ровнее. При нашем «зарезании» краска больше не течет. По тесту видно, что последние в градационной шкале краски отличаются друг от друга.
Для примера возьмем CMYK-плоттер, который печатает четырьмя цветами. Теоретически при печати плотностью 1% плоттер должен лить 1/100 от максимальной плотности данного цвета, при печати 5% — 1/20 от максимальной плотности, при печати 50% — 1/2 от максимальной плотности данного цвета. То есть зависимость должна быть линейной. Но на практике это далеко не так. Что дает линеаризация? Самое главное — учет нелинейности подачи чернил при изменении плотности печати. Практическое применение названной особенности трудно переоценить. С помощью распечатки линеаризации оборудование вычисляет нелинейность подачи чернил во время печати и с учетом полученных данных строит персональные тестовые шкалы, которые способны более точно воспроизвести цветовой профиль. Если в Adobe Photoshop открыть стандартную тестовую шкалу CMYK с 400-процентной заливкой, а рядом ту же шкалу, но сгенерированную с учетом данных, полученных после линеаризации, с плотностью заливки также в 400%, то можно заметить, что практически все ячейки изменены по цвету и существенно осветлены. С практической точки зрения линеаризация печатного устройства дает следующее:
Линеаризация — это процесс замера расхода краски для базовых цветов CMYK. Изначально, в отсутствие профиля, принтер печатает в зависимости от внутренних настроек: либо переливая, либо недоливая чернила. В офсетной печати все производители красок выпускают свой продукт по определенному стандарту: плотность, вязкость и т.д. В принципе, получаются «одинаковые» краски, которые, естественно, отличаются по качеству, цене, а поэтому «любимые» и «не любимые» печатниками. В широкоформатной печати ситуация иная. Каждый производитель старается сделать свои краски более яркими. Стандарты при этом отсутствуют, но в результате должна получиться идеальная прямая, наклоненная под углом в 45°, — соответствие исходного файла отпечатку. Изначально, если не проводить линеаризацию, принтер нальет либо выше этой прямой, либо ниже и оригинал будет воспроизведен неточно. То есть, к примеру, когда задается 50% заливки, то на выходе имеются все 70%, поскольку краска растекается. В офсете похожее явление определяется термином «растискивание растровой точки на бумаге» и тоже корректируется соответствующими инструментами. |
Рис. 5. Меню настройки RIP’а печатного оборудования. Специалисты рекомендуют при печати на глянцевых материалах сдвинуть параметры литья чернил до 85%, а при печати на прозрачных — до 90-95%
Рис. 5. График результатов процесса линеаризации
Начинаем построение линеаризации. Получившаяся с уже урезанным расходом чернил CMYK на 15% тестовая шкала промеряется спектрофотометром (результат показан в виде графика на рис. 5). На нем черной линией под углом в 45° показано, как должны расходоваться чернила идеального печатающего устройства (цвета оригинала соответствуют цветам оттиска), которое не нужно калибровать. Другими цветами показаны реальные плотности соответствующих красок — CMYK. Как видно, эти линии изогнуты и далеки от «прямого» идеала. На практике это означает неточный расход чернил, а при изменении носителя меняется впитываемость краски и соответственно меняется кривизна «линейности подачи чернил» (рис. 6).
Рис. 6. Результат процесса линеаризации. Получившийся тест (только плашки градационной шкалы) промеряем прибором i1Pro 2. Уже нет залитых плашек, которые наблюдались до линеаризации, но все равно серый элемент, обведенный красной линией имеет синий оттенок
Второй этап работы — профилирование, или построение ICCпрофилей. Это практически та же самая линеаризация, только для смеси цветов. Мешаем желтую с «маджентой» — линеаризуем красный, мешаем голубую с желтой — зеленый. Так, программное обеспечение i1Profiler дает возможность получить тестовые плашки максимум с 6 тыс. оттенков (рис. 7). Но нужно иметь в виду, что количество плашек находится в прямой зависимости от качества печати принтера. Если принтер печатает некачественно, то большее количество плашек, похожих друг на друга, «сбивают» работу программы профилирования.
Рис. 7. Русифицированный интерфейс программы i1Profiler. Возможен синтез тестовых шкал различных конфигураций. Практика показывает, что оптимальное количество плашек должно находиться в пределах от 1000 до 2500. Максимальное количество — 6000 плашек
Процесс построения профиля принтера сводится к печати и замеру тестовых оттенков с целью определения диапазона цветов, достижимых на данном устройстве. Для принтеров тестовая таблица представляет собой стандартную выборку СМYKоттенков, отпечатанных на данном устройстве.
Измерения, сделанные прибором i1Pro 2, поступают в программу i1Profiler, которая продается с русифицированной версией. Фактически линеаризация позволит программе i1Profiler впоследствии узнать, с каким печатным оборудованием идет работа — то есть каковы краски и тоновая передача, сколько машина не доливает или переливает. На основе этих данных создается оптимальная таблица для построения профиля.
В отличие от калибровки широкоформатных принтеров, калибровка офсетной печати гораздо более сложная и трудоемкая и производится на нескольких видах оборудования:
- проверка действующих параметров вывода печатных форм, - линеаризация выводного устройства, - вывод тестовых печатных форм линейно (без компенсации);
Затем проходит калибровка технологического процесса офсетной печати: замер полей на применяемых шкалах тиражных оттисков с печатных машин для выяснения идентичности качества печати; печать тестовых изображений; определение оптимальных значений расходования применяемых красок CMYK:
Подробности см. в публикации КомпьюАрт № 7 и 8 за 2012 год. |
При выборе задачи запускается пошаговый мастер ее выполнения (рис. 8), при этом на каждом шаге опытный пользователь может скорректировать параметры работы, а новичок в большинстве случаев может оставить изначальные значения параметров, хотя некоторая внимательность все же потребуется, так как не всегда достаточно просто нажимать на кнопку «Далее».
Рис. 8. Одна из иконок показывает, что на процесс профилирования влияет освещенность помещения, уровень которой тоже нужно измерить
Цветовая калибровка принтеров осуществляется спектрофотометром, а результаты обрабатываются в прилагаемом программном обеспечении. В процессе калибровки устройство настраивается таким образом, чтобы полученный на нем отпечаток совпадал со значениями, указанными в программе. Когда речь идет о цветном принтере, калибровка обеспечивает вывод необходимого количества чернил CMYK.
Типичное тестовое изображение при этом состоит из нескольких рядов монохромных плашек — по одному ряду для каждого основного цвета. В каждом ряду проставляется несколько плашек с разным процентным содержанием одного и того же цвета — обычно с шагом в 5 или 10%, начиная со сплошного и заканчивая нулевым покрытием.
Далее проводится замер распечатанных шкал и вычисляется линейность устройства, то есть его способность точно выводить тот процент, который задан калибровочной программой (рис. 9). Измерение перемешанных шкал с разделителем дает более точные результаты профилирования. Лучший результат измерений достигается, когда плашки с большой насыщенностью цвета не находятся рядом (специальной опцией задается порядок следования тона плашек). Результаты замеров отправляются обратно в программу, где выполняются внутренние перенастройки PostScriptкоманд, управляющих цветовыми значениями, посылаемыми выводному устройству.
Рис. 9. Замер тестовой шкалы на специальном столе производится прибором i1Pro 2. Программа также позволяет создавать как последовательные, так и перемешанные по цвету шкалы
Программное обеспечение для профилирования принтеров использует состоящее из 400 или более цветных плашек тестовое изображение, которое выводится на принтер. Затем отпечаток замеряется, и по полученным колориметрическим данным вычисляется цветовое пространство данного конкретного принтера и определяется его соответствие пространству СIELAB. Эта информация становится основным компонентом индивидуального профиля данного принтера.
Поскольку в процессе профилирования выявляются возможности принтера воспроизводить полный диапазон различных цветов (а не отдельных плотностей конкретных красителей), для сбора информации и проведения замеров необходимо использовать спектрофотометр.
Рис. 10. Рассматривая распечатанные тестовые шкалы на глянцевой (слева) и прозрачной основе, можно сделать вывод, откалиброван ли принтер и может ли он начать работу над коммерческими заказами
Задача профилёра i1Profiler — расчет нужного количества триадных красок, которые наносятся на определенный вид материала для получения на нем необходимого оттенка цвета (рис. 10). Из файла оригинала изображения берется информация из каждой его точки, которая преобразуется в координаты пространства Lab, потом эти цифры из него, согласно построенному уже выходному профилю, преобразуются в нужное количество краски. При этом профилёр вычисляет кривую между похожими оттенками (плашками). Если в макете характеристики цвета абсолютно совпадают с параметрами плашки тестового изображения, то, по сути, происходит идеальная печать. Когда же цифры, определяющие цвет, находятся между тестовыми плашками, нужное количество чернил рассчитывается математически (рис. 11).
Рис. 11. «Каменная» модель готового профиля (а). Существует возможность показа «профиля в профиле» (б)