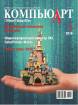
Современные технологии 3D-печати
3Dпринтеры, существующие на данном этапе их развития, способны создавать не только вкусные блюда и всякие приятные мелочи. Например, выяснилось, что экономически выгодно получать таким методом ракетные двигатели. Подобные проекты имеют место быть — например, такой принтер уже существует у NASA. Однако 3Dпринтер применяют пока только для создания составных частей подобных двигателей. Тем не менее эксперты единогласно утверждают, что через четырешесть лет такие принтеры будут использоваться повсеместно.
Япония сегодня переживает настоящий бум, связанный с 3Dпринтерами и печатью — повсеместные печатные фотографии постепенно заменяет 3Dпечать. Например, в Токио, Осаке находятся 3Dфотобудки, позволяющие вместо обычной бумажной фотографии получить объемную, трехмерную статуэткуфотографию с прекрасным точным исполнением даже мелких деталей.
Набирает популярность и сервис «объемного фотошопа», когда вас «нарядят» в виртуальную одежду какойнибудь исторической эпохи или изобразят отважным рыцарем, получив трехмерную модель вашего облика при предварительном сканировании.
Этот симбиоз завоевывает все большее место в искусстве. Так, на выставке 3D Print Show демонстрировались самые невероятные экспонаты, полученные в результате 3Dпечати: от необычных музыкальных инструментов до удивительных решений мебели, компьютерных гаджетов, и даже человеческих органов.
Голливуд испытывает настоящий бум в связи с использованием технологий 3Dмоделирования. Например, в фильме «Агент 007» машина главного героя настолько совершенна, что ее просто не существует. Это очередное детище 3Dпечати и сопутствующих ей технологий (рис. 1). Традиционное производство в разы дороже, более наукоемкое и медлительное по сравнению с 3Dпечатью.
Рис. 1. Машина Джеймса Бонда, напечатанная на 3D-принтере
Возможности 3Dпечати не имеют границ. На британском авиашоу в Фарнборо был представлен большой беспилотный самолет, большая часть которого была воспроизведена методом трехмерной печати. Самолет Polecat — это летающий прототип, способный продемонстрировать работоспособность новой технологии 3Dпечати. К достоинствам такого получения деталей относится не только скорость, но и низкая цена подобных деталей, а это — главная цель.
Согласно данным компании IDC, к 2017 году поставки 3Dпринтеров увеличатся в 10 раз, а ежегодные темпы роста продаж составят 29%. В связи с положительной статистикой многие компании и фирмы начинают осваивать 3Dтехнологии.
3D-печать в рекламе и маркетинге
Человек воспринимает мир пространственно, то есть в трех измерениях, где восприятие фиксируется на одном объекте под разными углами, изображение обрабатывается на основе расстояния между глазами и так формируется трехмерный эффект.
3Dпечать нашла практическое применение в рекламе. Главной задачей рекламы является информирование о товарах и услугах потребителей и создание спроса на продукцию. Какого типа ни была бы реклама (информационная, напоминающая, подкрепляющая или престижная), задержать взгляд человека традиционными средствами сегодня становится все труднее.
3Dрекламу используют такие всемирно известные фирмы, как CocaCola, Adidas, Cavalli, Ferrero, McDonalds и др. Трехмерная реклама может существовать в различных формах: в сувенирной продукции, отделке интерьеров фирм, использовании наружной рекламы, печатных изданиях и т.д.
Основными преимуществами 3Dрекламы являются высокая степень заметности, форма новизны, запоминаемость, длительный срок службы без потери внешнего вида. Доказано, что даже боковым зрением покупатель заметит необычность форм и обратит свое внимание на рекламируемый объект.
Промышленные 3Dпринтеры открывают массу новых возможностей для реализации нестандартных проектов в разных сферах бизнеса, в частности в маркетинге и модной индустрии. С помощью 3Dпринтеров можно создавать всевозможные нестандартные подарки, статуэтки, премии, промоматериалы, декоративные элементы и проводить громкие рекламные акции.
Рис. 2. Кубки авторам твита о крекерах Belvita
Мировая практика уже сейчас насчитывает множество интересных примеров использования 3Dпечати в маркетинге. Вот некоторые из них:
- Для продвижения своих новых минибутылок в Израиле компания CocaCola объединилась с маркетинговым агентством Gefem TelAviv для соввместной разработки специального мобильного приложения, в котором пользователи могли создать собственную виртуальную миникопию и ухаживать за ней, как за Тамагочи. Среди всех пользователей приложения несколько человек выиграли поездку на завод CocaCola, где прошли 3Dсканирование и получили в подарок свою миникопию, напечатанную из полноцветного гипса на 3Dпринтере. О проведенной кампании был снят видеоролик, который набрал огромное количество просмотров и помог CocaCola Mini приобрести чрезвычайную популярность.
- Для рекламы крекеров Belvita американские креативные агентства Droga5 и Fake Love предложили пользователям Твиттера постить утренние твиты со специальным хэштегом. Затем специально приглашенные актеры принимали позу, ярко характеризующую описываемые тем или иным пользователем события. Актеры сканировались с помощью 3Dсканера, а полученная модель распечатывалась на 3Dпринтере в виде своеобразного кубка и вручалась автору твита (рис. 2). После этого в Интернет был выложен остроумный видеоролик, рассказывающий об этой кампании. Ролик набрал более 80 млн откликов в различных соцсетях, а компания Belvita увеличила объем продаж на 100%.
- Чтобы вызвать интерес к программам 3Dпроектирования, компания Loft рассылала пользователям информационные брошюры в комплекте с напечатанным на гипсовом 3Dпринтере минидиваном. В качестве интерьера для диванов использовалась коробка, в которую упаковывалась посылка. А мюнхенская мебельная компания АerisImpulsmöbel GmbH & Co. KG вместе с рекламными буклетами рассылала покупателям 3Dпечатные образцы своих стульев.
- Британская благотворительная организация Barnardos и рекламное агентство BBH London, чтобы привлечь внимание к проблеме бездомных и напомнить всем, как важно иметь крышу над головой, в канун Рождества провели кампанию Home for Xmas. В рамках кампании каждый день выбирали дом одного из филантропов и на 3Dпринтере печатали его гипсовую миниатюру, которую затем размещали в стеклянном шаре и отправляли «хозяину» со словами благодарности. Видеоролик, рассказывающий об этой акции, стал вирусным, а количество денежных перечислений в фонд Barnardos увеличилось в несколько раз.
- Автомобильный концерн Volkswagen и DDB Copenhagen провели кампанию The Polo Principle. Покупателям предлагалось разработать дизайн автомобиля и разместить проект на сайте производителя. Сорок лучших идей были напечатаны на 3Dпринтере и представлены на выставке в Копенгагене, после чего вручены их разработчикам. Дизайн победителя был использован в производстве автомобиля VW Polo.
Рис. 3. Диваны от компании Loft
Рис. 4. Одна из моделей, присланных на конкурс The Polo Principle
Преимущества применения 3D-принтеров в рекламе и дизайне
Вопервых, с помощью 3Dпечати вы получаете возможность создавать изделия любой геометрии, ваша фантазия ничем не ограничена. Любой каприз заказчика теперь можно визуализировать за несколько часов. При этом, благодаря современным 3Dпринтерам, вы можете создавать яркие полноцветные изделия, передающие любые цветовые решения.
Стадия производства и продвижения товара играет важнейшую роль в создании имиджа бренда и маркетинговой стратегии. Именно поэтому товар не сразу выводится на рынок — сначала производится визуальный анализ пробной модели, анализ эргономики, исследование фокусгруппы. За время разработки и тестирования модель может несколько раз видоизмениться, поэтому экономичнее и практичнее будет создать макет товара на 3Dпринтере.
3Dпринтеры позволяют изготавливать макеты упаковок, флаконов и бутылок оригинальной формы, дизайнерские изделия, мебель, прототипы электроприборов и многое другое. При этом готовые изделия могут включать все элементы дизайна, в том числе этикетки, штрихкоды, фирменные знаки. Преимущества 3Dпрототипов очевидны: заказчик может подержать проект в руках, оценить его фактуру, текстуру, цветовое оформление и другие характеристики.
Материалами для прототипа могут служить гипс, фотополимеры или ABSпластик — в зависимости от свойств изделия. С помощью 3Dпечати можно не только передать форму будущего объекта, но и выгодно показать его лучшие стороны и скрыть недостатки. Цветная печать, высокая детализация и качество поверхностей позволяют быстро получить нужный результат.
Технологии 3D-печати
В настоящее время существует множество технологий для материализации реальных объектов из созданных виртуальных 3Dмоделей. Наиболее распространенная и доступная технология — это печать пластиком.
Далее приводится классификация технологии печати с описанием каждой из них.
В настоящее время технологии 3Dпечати разделяются на четыре основные категории:
- Экструдирование — выдавливание расплавленного материала.
- Фотополимеризация — отверждение полимера УФ или лазерным излучением.
- Печать методом спекания и плавления материалов.
- Ламинирование — склеивание слоев материала с последующим вырезанием.
Помимо этого существуют другие технологии, промежуточные или не попавшие в вышеуказанные категории по тем или иным причинам.
Экструдирование
Моделирование методом наплавления (Fused Deposition Modeling, FDM)
Наиболее распространенная технология 3Dпечати, особенно среди персональных и настольных 3Dпринтеров.
Технология работает по принципу наплавления материала слоями. Пластиковые или металлические нити разматываются из рулона (картриджа) и поступают в печатающую головку (экструдер). Экструдер разогревает нити до жидкого состояния и выдавливает материал через сопло, перемещаясь в горизонтальном и вертикальном направлениях, формируя объект слой за слоем.
Преимущества технологии 3Dпечати по технологии FDM:
- скорость и простота изготовления моделей;
- доступность;
- безопасность, экологическая чистота и нетоксичность большинства материалов;
- точность построения;
- простота использования и обслуживания;
- прочность деталей;
- простота утилизации.
Материал для печати: термопластики (PLA, ABS, PVA, HIPS и т.п.), легкоплавкие металлы и сплавы. Плюс различные кулинарные принтеры, которые используют глазурь, сыр, тесто, а также медицинские, которые печатают «живыми чернилами» (набор живых клеток помещается в специальный медицинский гель).
Моделирование методом напыления с последующим фрезерованием слоя (Drop On Demand Jet, DODJet)
В этой технологии 3Dпечати используется два вида материалов: модельный и материал поддержки.
Печатающая головка одновременно распыляет оба типа «расходников». Затем специальная фрезеровочная головка производит охлаждение распыленного слоя и его механическую обработку. Технология DODJet позволяет строить высокоточные модели с абсолютно гладкой поверхностью. Так как распыление рабочего слоя происходит за счет механической движущейся головки, то скорость изготовления прототипа во многом зависит от сложности печатной модели.
Материал для печати: литейный воск.
Рис. 5. Изделия, напечатанные способом Fused Deposition Modeling
Фотополимеризация
Лазерная стереолитография (Laser Stereolithography, SLA)
Технологию изобрел Чарльз Халл. Получив патент на нее, Халл основал компанию 3D Systems, которая и сегодня остается ведущей компаниейпроизводителем SLAмашин.
Технология предполагает использование специального фотополимера — светочувствительной смолы в качестве модельного материала. Основой в данном процессе является ультрафиолетовый лазер, который последовательно переводит поперечные сечения модели на поверхность емкости со светочувствительной смолой. Фотополимер отверждается только в том месте, где прошел лазерный луч. Затем новый слой смолы наносится на отвержденный слой, и новый контур намечается лазером. Процесс повторяется до завершения построения модели.
Рис. 6. Стереолитография
Стереолитография — наиболее популярная технология быстрого прототипирования для получения высокоточных моделей. Она охватывает практически все отрасли материального производства — от медицины до тяжелого машиностроения. SLAтехнология позволяет быстро и точно построить модель изделия практически любых размеров. Качество поверхностей зависит от шага построения. Современные машины обеспечивают шаг построения 0,0250,15 мм.
Материалы в 3D-печатиСтеклопластикСтеклопластик является композиционным материалом, состоящим из стеклянного наполнителя и специального синтетического полимерного связующего компонента. Как правило, в качестве наполнителя служат стеклянные волокна в виде тканей, матов, жгутов, нитей или рубленых волокон. Связующие компоненты — эпоксидные, фенолформальдегидные, кремнийорганические, полиэфирные смолы, а также полиамиды, поликарбонаты, полиимиды и т.п. Характеристики стеклопластика — это сочетание высоких диэлектрических и прочностных показателей с относительно низкой плотностью и теплопроводностью. В этот перечень необходимо добавить еще и значительную влаго-, термо- и атмосфероустойчивость данного материала. Его механические свойства определяют характеристики наполнителя, а условия обработки и эксплуатации — особенности связующего материала. Наибольшая жесткость и прочность характерна для стеклопластиков, содержащих непрерывные, ориентировано расположенные волокна. В качестве примера изделий из стеклопластиков можно привести корпуса катеров и яхт, автомобильные кузова и цистерны, детали ракетных двигателей и радиопрозрачные обтекатели, плавательные бассейны и многое другое. ПенополиуретанПенополиуретан — это тугоплавкая, термореактивная, жесткая масса, имеющая ярко выраженную ячеистую структуру. Твердая основа этого материала составляет лишь 3% его объема и образует жесткий каркас из стенок и ребер. Подобная кристаллическая структура наделяет пенополиуретан значительной механической прочностью. Оставшиеся 97% приходятся на долю заполненных фторхлорметаном полостей и пор. Газ фторхлорметан характеризуется низкой теплопроводностью, а доля замкнутых пор, в которых он содержится, достигает 95%. В сравнении с прочими теплоизоляционными материалами, пенополиуретан имеет оптимальное сочетание свойств тепло- и влагоизоляции и наиболее низкий показатель коэффициента теплопроводности, в сочетании с высокими прочностными и термическими характеристиками. Пенополиуретаны нашли широкое применение в изготовлении различных моделей, в силу своих уникальных физических свойств. Практически не насыщаемые влагой и в то же время «дышащие» (то есть пропускающие избыток влажности в помещениях в окружающую среду) полиуретановые изделия почти не подвержены износу и разложению, не привлекательны для грызунов (даже в качестве строительного материала), имеют высокие прочностные характеристики. zp131zp131 — это высококомпозиционный материал 4-го поколения, основу которого составляет гипс. zp131 был создан на базе материала zp130, который успел великолепно зарекомендовать себя в сфере 3D-печати. Но zp131 выгодно отличается от zp130 возросшей на 50% прочностью и на 115% — увеличенными возможностями цветового охвата. Тестирование композиционного материала zp131 со всей ясностью показало, что детали, имеющие стержневые элементы диаметром 0,4-0,5 мм, обладают достаточно высокой прочностью конструкции. Это позволяет создавать максимально детализированные изделия для многих отраслей коммерческой и промышленной деятельности. В качестве простого примера применения zp131 можно привести создание модели жилого дома с внутренними стенами белого цвета. При использовании материала zp130 стены обязательно приобретут бежево-желтоватый оттенок или цвет слоновой кости, что не является браком, но, тем не менее, выглядит в проекте «неаккуратно». zp131позволил решить данную проблему, ведь в его состав, кроме порошковой основы, входит новая клеящая масса, обеспечивающая возможность широкого выбора цветов и способная к максимально точной их передаче в готовом виде. ABS-пластикСамым популярным расходным материалом является ABS-пластик. Особая структура этого вида «расходника» позволяет выдерживать сильное механическое воздействие. Такой пластик относится к ударопрочной группе, и если сравнить ABS с обыкновенным полистиролом, то он в значительной степени превосходит другие аналоги в плане механической прочности и жесткости. Среди других достоинств можно отметить тот факт, что данный вид пластика выдерживает температурную нагрузку в 100 °С. Этот расходный материал также можно использовать для нанесения гальванического покрытия, в сфере вакуумной металлизации и даже для спайки контактов. Он отлично подходит для сварки или точного литья. Материал обладает высокой размерной стабильностью. Распечатанные объекты имеют блестящую поверхность (уровень блеска можно регулировать). Среди огромного списка достоинств можно отметить стойкость к щелочи, смазке, кислоте, углеводороду, жиру и даже бензину. Однако он прекрасно растворяется в ацетоне, эфире, бензоле, этилхлориде, этиленхлориде, анилине и анизоле. Основной недостаток — чувствительность к воздействию ультрафиолетовых лучей и атмосферных осадков. Данный материал характеризуется низким уровнем электроизоляции. Практически не поглощает влагу. Воспламеняется при температуре в 395 °С. PLA-пластикPLA-пластик, или полилактид, является самым экологически чистым и подходящим расходным материалом для трехмерной печати. Данный вид пластика представляет собой термопластичный полиэфир, который создается из биологических отходов (сахарная свекла или силос кукурузы). Его мономером является молочная кислота. Распечатанные объекты имеют отличный уровень скольжения (из такого пластика даже можно производить подшипники скольжения). Чаще всего такой материал используется для изготовления детских игрушек, потому что PLA обладает минимальным уровнем токсичности. Единственным недостатком полиактида является недолговечность и постепенное разложение. Отметим, что если не трогать распечатанное изделие, то оно может простоять около 20 лет (если температура материала не будет превышать 50 °С). Однако если подвергать его постоянной эксплуатации, то вскоре объект потеряет свой первоначальный вид. Материал отлично подходит для большой и маленькой печати. Стоит заметить, что для повышения прочности изделия полиактид можно смешать с ABS-пластиком, тем более что они имеют сравнительно одинаковую стоимость. Если вы захотите расплавить PLA-пластик, то достаточно поместить модель в ультразвуковой резервуар с небольшим количеством каустической соды. Более простой способ расплавления — положить объект в воду, нагретую до температуры 80 °С. PVA-пластикНа российском рынке PVA-пластик появился в 2012 году. PVA — это тот же самый поливинилацетат, то есть клей ПВА. Основным достоинством (или недостатком) этого материала является быстрая растворимость в воде. Данный вид расходного материала часто используется в качестве разделителя. Например, если пользователю нужно распечатать гайку с болтом, то PVA помогает разделить эти два объекта, чтобы после распечатки гайка смогла свободно крутиться на болте. Конечно же, распечатывать объекты при помощи PVA-пластика может показаться нерациональным. Его основное предназначение — поддержка в процессе создания объектов с уникальным дизайном. ФотополимерыЕще одним популярным расходным материалом для современных принтеров являются фотополимеры. На самом деле у данного материала достаточно много разновидностей, однако все они имеют общую черту — фотополимеры меняют свою форму под воздействием солнечного света. Такой расходный материал применяется для печати на принтерах SLA и PJET. Подобные «расходники» могут быть жидкими или твердыми. Объекты, которые были распечатаны при помощи фотополимеров, обладают высокой прочностью, устойчивостью к солнечному свету и воде. Металлический порошокМеталлический порошок также часто используется в трехмерной печати. В качестве исходного материала можно применять золото, медь, алюминий или сплав. Даже пластик ABS не может сымитировать блеск настоящего металла. Данный вид расходного материала широко применяется в производстве драгоценностей. К тому же модели из металла обладают более высокой прочностью по сравнению с другими видами расходных материалов для 3D-принтеров. Стоимость порошка зависит от его ценности. НейлонНейлон очень похож на самый популярный расходный материал — ABS-пластик. Однако он обладает лучшей сопротивляемостью высокой температуре печати и способен впитывать влагу. Недостатком нейлона является более высокий срок застывания и необходимость откачки воздуха из экструдера. Нейлон считается токсичным материалом. Данный вид расходного материала отлично подходит для печати шестерней, рычагов и даже запчастей для медицинских аппаратов. Стоит заметить, что сегодня большинство владельцев принтеров используют такой материал, как Nylon 618, который обладает гораздо меньшей токсичностью. * * * * * Современные виды расходных материалов для 3D-принтеров обладают необходимым запасом прочности. Конечно же, большинство счастливых обладателей 3D-принтеров предпочитают использовать ABS- или PLA-пластик. Однако пластик не всегда может удовлетворить потребности владельца. На самом деле разновидностей «расходников» для 3D-принтеров гораздо больше. Например, некоторые модели принтеров могут использовать шоколад или лед. Все зависит от фантазии владельца и типа принтера! В качестве примера можно упомянуть новый материал от компании Filamentarno, которая предложила пользователям два филамента, имитирующих керамику. Новые расходные материалы для 3D-печати получили название CERAMO и CERAMO-TEX (актуальность новости — конец сентября текущего года). CERAMO — это гладкая версия с высокой плотностью, напоминающая фаянс — вплоть до веса и звука при ударах. Материал хорошо поддается шлифовке, обладает низкой усадкой при остывании и хорошо схватывается между слоями. CERAMO-TEX обладает высокой твердостью при низкой плотности. По информации компании, плотность изделий, напечатанных со 100-процентным наполнением, может составлять 0,75-0,8 г/см³. |
SLAтехнология дает наилучший результат при изготовлении мастермоделей для последующего изготовления силиконовых форм и литья в них полимерных смол, а также используется для выращивания ювелирных мастермоделей.
В зависимости от необходимых свойств конечного объекта модель запекают в так называемых ультрафиолетовых духовках.
Рис. 7. Щетка, целиком напечатанная за один сеанс по технологии PolyJet
Фотополимер зачастую бывает токсичным, поэтому при работе с ним нужно пользоваться средствами защиты и респираторами. Содержать и обслуживать такой принтер дома — сложно и дорого.
Преимущества: быстрота и точность (точность — до 10 микрон). Для спекания фотополимера достаточно лазера от проигрывателя Bluray, благодаря чему на рынке появляются дешевые и при этом точные принтеры, работающие по такой технологии.
Материал для печати: фотополимерная смола.
Цифровая обработка светом (Digital Light Processing, DLP)
Аналог SLAтехнологии. В отличие от традиционной технологии стереолитографии, использующей сканирующий ультрафиолетовый лазер для того, чтобы сделать жидкий материал твердым, DLPпринтер работает по схожему принципу, однако использует DLPпрожектор, который воздействует на каждый слой. Как только первый слой застывает на платформе, она опускается немного глубже в резервуар со смолой, а прожектор засвечивает новое изображение, чтобы затвердел следующий слой.
Материал для печати: жидкая смола.
Технология MJM (Multi-Jet-Modeling)
Технология разработана и запатентована компанией 3D Systems. В основе MJMтехнологии 3Dпечати лежит послойное сечение СADфайла на горизонтальные слои, которые последовательно отправляются на 3Dпринтер.
Каждый слой формируется печатающей головкой, которая через группы сопел выпускает на горизонтальную движущуюся платформу расплавленный (температура около 80 °C) фотополимер или расплавленный воск. Материал расплавляется в системе подачи до того, как попадает в печатающую головку.
Если 3Dпечать выполняется из фотополимера, то после печати каждого слоя платформа, на которой выращен слой, отъезжает за печатающую головку под ультрафиолетовую лампу. Вспышка ультрафиолетовой лампы вызывает реакцию, вследствие которой материал твердеет. После этого платформа отъезжает опять под печатающую головку и цикл формирования слоя повторяется. Печатающая головка образует новый слой.
Особенностями технологии MJM является возможность воспроизводить 3Dмодели с высокой точностью. В процессе 3Dпечати используется материал поддержки — воск (поставляется отдельными картриджами). Если 3Dпечать выполняется из фотополимера, то материал поддержки удаляется посредством высокой температуры: деталь с поддержкой помещается в печь с температурой ~60 °C. Если 3Dпечать выполняется из воска, то поддержка удаляется с помощью специального раствора.
Немаловажно и то, что в клей можно добавлять красящие вещества, а следовательно, есть возможность получить не только объемную модель, но и разноцветную.
Материал для печати: фотополимерная смола, акриловый пластик, литейный воск.
Полиструйная технология (PolyJet, PJET)
Технология представлена в 2000 году компанией Objet, которая затем, в 2012 году, была приобретена компанией Stratasys.
Трехмерная печать PolyJet похожа на струйную печать документов, но вместо струйной подачи чернил на бумагу 3Dпринтеры PolyJet выпускают струи жидкого фотополимера, который образует слои на модельном лотке и мгновенно фиксируется ультрафиолетовым излучением. Тонкие слои ложатся последовательно и образуют точную трехмерную модель или прототип. Модели готовы к использованию сразу по извлечении из 3Dпринтера, при этом не требуется никакая дополнительная фиксация.
Помимо выбранного модельного материала 3Dпринтер также выпускает струи гелеобразного вспомогательного материала, предназначенного для поддержки выступов и сложных геометрических форм. Его легко удалить вручную или с помощью воды.
Технология трехмерной печати PolyJet обладает множеством преимуществ для оперативного прототипирования, быстро и точно образуя потрясающе тонкие детали и гладкие поверхности.
Важной особенностью, отличающей PolyJet от стереолитографии, является возможность печати различными материалами. Технология использует широкий ряд материалов, в том числе жесткие непрозрачные материалы сотен ярких цветов, прозрачные и цветные полупрозрачные тона, гибкие эластичные материалы и специализированные фотополимеры для 3Dпечати в стоматологической и медицинской отраслях, а также в производстве товаров широкого потребления.
Преимущества технологии: толщина слоя — до 16 микрон (клетка крови — 10 микрон), высокая скорость печати, так как жидкость можно наносить очень быстро. Недостатки технологии: печатает только с использованием фотополимера — узкоспециализированного, дорогого пластика, как правило, чувствительного к УФ и достаточно хрупкого.
Материал для печати: фотополимерная смола.
Рис. 8. Процесс лазерного спекания по технологии Selective Laser Sintering
Непрерывная межфазная жидкая печать (Continuous Liquid Interface Production technology, CLIP)
Группа химиков под руководством Жозефа Десимоне (Университет Северной Каролины в ЧепелХилл) создала усовершенствование для фотолитографической печати, в десятки раз ускоряющее процесс послойного создания деталей из жидкого полимера, отверждаемого ультрафиолетом.
На объект, печатаемый по SLA или Polyjetтехнологии за три часа, а SLSметодом — за 11 часов, принтеру технологии CLIP требуется всего 6 минут. Ускорение от 30 до 100 раз!
Рис. 9. Печать по технологии LENS
Очевидно, что рентабельность такого принтера вырастет фантастически, а себестоимость изделий немедленно упадет. При этом усовершенствование не представляет собой чегото особо сложного либо дорогостоящего. Суть изобретения — в создании на самом дне ванны с полимером, поверх проекционного окна, тончайшего слоя жидкости, ингибированного кислородом и не застывающего под воздействием ультрафиолета. Таким образом, отверждение происходит выше, в слое, не касающемся дна ванны и отделенном от него прослойкой жидкого полимера. Классическая SLAтехнология отверждает слой, лежащий на дне ванны, и поэтому его можно поднимать на следующий шаг не раньше, чем он полностью застынет, то есть имеется длительная неустранимая пауза на каждом слое. В технологии CLIP подъем платформы происходит немедленно, как только очередной слой засвечен, что и создает такую скорость построения. Кислород же, ингибирующий реакцию в придонном слое, подается путем диффузии прямо сквозь материал, из которого изготовлено дно ванны. Собственно, это кислородпроницаемое дно и составляет главное нововведение в конструкцию SLAпринтера.
Система MultiFab работает с рекордным количеством материаловТехнология трехмерной печати хоть и развивается семимильными шагами, тем не менее, по-прежнему нуждается в дополнительном вмешательстве со стороны человека. Даже если устройство способно напечатать отдельные детали какого-то объекта, собрать его сможет только человек. Другая серьезная проблема аддитивного производства — это ограничение по количеству материалов, с которыми может работать один принтер. Существующие на сегодняшний день модели способны работать с тремя различными материалами, а стоимость такой мультифункциональной машины может достигать 250 тыс. долл. Однако команда ученых из Лаборатории информатики и искусственного интеллекта (CSAIL) Массачусетского технологического института представила новый 3D-принтер, который, по словам создателей, лучше, дешевле и более удобен, чем все существующие аналоги. Устройство работает сразу с десятью различными материалами и использует методику 3D-сканирования, которая позволяет экономить время и деньги во время производства. Разрешение печати составляет 40 микрометров, что вдвое меньше толщины человеческого волоса. Система MultiFab оснащена технологией самостоятельной калибровки, что избавляет человека от необходимости производить настройку самостоятельно. Накладывая каждый новый слой в конструкцию, устройство сравнивает его с 3D-моделью в компьютере и генерирует так называемые поправочные маски. Этот подход позволяет использовать недорогое аппаратное оборудование, сохраняя высокую точность печати. Кроме того, MultiFab дает пользователям возможность внедрять непосредственно в тело объекта сложные компоненты, такие как схемы и датчики. А это означает, что на новом 3D-принтере можно будет печатать целые устройства с движущимися частями и встроенной электроникой. В отличие от обычных 3D-принтеров, принцип работы которых основан на экструзии, новая технология опирается не несколько более утонченный процесс. Экструзия в обычных 3D-принтерах представляет собой выдавливание материала из специальных шприцов — очень похоже на выдавливание декоративной глазури или крема на торт из кондитерского шприца. Это приводит к тому, что детали печатаются с довольно низким разрешением, из-за чего конечный продукт получается грубым. (Диаметр отверстия не может быть уменьшен до микроскопических значений, так как поверхностное натяжение не позволит выдавить каплю вещества). Система MultiFab действует по-другому. Она смешивает микроскопические капельки фотополимеров, которые затем отправляются через струйные печатающие головки, похожие на те, что встроены в конструкцию обычного офисного принтера. Так обеспечивается высокое разрешение послойного нанесения материалов и качество конечного продукта. Общая стоимость материалов, использованных для конструирования принтера MultiFab, составила всего 7 тыс. долл., что почти в 20 раз дешевле существующих аналогов. |
Технология позволяет использовать огромный спектр расходных материалов для различных сфер применения: от изготовления спортивной обуви до автомобильной и других видов промышленности.
Печать методом спекания и плавления материала
Селективное лазерное спекание (Selective Laser Sintering, SLS)
Метод SLS был изобретен Карлом Декартом (Carl Deckard) в 1986 году. По данной технологии модели создаются из порошковых материалов за счет эффекта спекания при помощи энергии лазерного луча. В отличие от SLAпроцесса, в данном случае лазерный луч является не источником света, а источником тепла. Попадая на тонкий слой порошка, лазерный луч спекает его частицы и формирует твердую массу в соответствии с геометрией детали. В качестве материалов используются полиамид, полистирол, песок и порошки некоторых металлов.
Существенным преимуществом SLSпроцесса является отсутствие так называемых поддержек при построении модели. В процессах SLA и MJM при построении нависающих элементов детали используются специальные поддержки, предохраняющие свежепостроенные тонкие слои модели от обрушения. В SLSпроцессе в таких поддержках нет необходимости, поскольку построение ведется в однородной массе порошка. После построения модель извлекается из массива порошка и очищается.
Ведущими производителями SLSмашин являются компании Concept Laser (Германия), 3D Systems (США) и EOS GmbH (Германия).
Материал для печати: термопластик, металлический порошок, керамический порошок, стеклянный порошок.
Прямое металлическое лазерное плавление (Direct Metal Selective Laser Melting, SLM)
SLM — разновидность технологии SLS. Эта технология похожа на SLS, их иногда даже путают, но при этом они имеют кардинальные различия. Но, если в технологии SLS частицы порошка спекаются друг с другом, то здесь металлические частицы доводятся до состояния расплавления и свариваются друг с другом, образуя жесткий каркас.
Материалом выступают металлы и сплавы в виде порошка. Для печати доступны следующие металлы и сплавы: сталь, нержавеющая сталь, инструментальная сталь, алюминий, сплав кобальтхром, титан.
Тонкие слои качественного порошка металла равномерно распределяются с использованием специального покрывающего механизма. Платформа, на которой расположен порошок, при этом может опускаться по вертикали. Весь процесс происходит внутри камеры, которая поддерживает жесткий контроль атмосферных инертных газов, таких как аргон, азот, кислород, уровень которых не превышает 500 частей на миллион. Затем каждый слой формируется путем избирательного воздействия лазеров на поверхность порошка с помощью двух высокочастотных сканеров X и Y осей. Система фокусировки направляет высокомощный лазер на металлические частицы, расплавляя и сваривая их между собой. По контурам сечения проходит сплошная сварка, а внутренности стенок объекта могут свариваться в соответствии с паттерном заполнения. Кстати, порошок, оставшийся от изготовления детали, может повторно использоваться для печати следующей модели.
Материал для печати: практически любой металлический сплав в виде гранул, крошки, порошка.
Электронно-лучевая плавка (Electron Beam Melting, EBM)
Эта технология была разработана компанией Arcam AB в Швеции. Технология представляет собой изготовление деталей путем плавления металлического порошка, наносимого слой за слоем, мощным электронным пучком в вакууме. В отличие от некоторых методов спекания металла, части получаются без пустот, очень прочными.
EBM является наиболее совершенной среди других технологий 3Dпечати.
Технология позволяет изготавливать детали любой геометрической формы с параметрами используемого материала. Машина EBM считывает данные из модели 3D, расположенной, как правило, в CADфайле, и последовательно формирует ее слой за слоем. Эти слои сплавляются вместе с использованием электронного пучка, управляемого компьютером. Таким образом он строит целые части. Процесс происходит в вакууме, что делает его подходящим для изготовления деталей из материалов, сильно подверженных влиянию кислорода, например титана.
Важным преимуществом является то, что порошок представляет собой чистый конечный материал без каких бы то ни было наполнителей, а следовательно, напечатанную деталь не нужно подвергать дополнительной термической обработке.
EBM работает при температуре, находящейся обычно между 700 и 1000 °С. Детали получаются готовыми практически сразу же после остывания.
Сочетание вакуума и общей высокой температуры позволяет добиться явления так называемой разгрузки внутреннего напряжения. Сталевары, очевидно, знакомы с этим термином, а для всех остальных просто скажем, что финальное изделие получает прочность, сопоставимую с коваными сплавами.
Титановые сплавы, как уже отмечалось выше, без труда обрабатываются с помощью этой технологии, что делает ее подходящим выбором для рынка медицинских имплантатов.
Материал для печати: сплавы титана.
Выборочное тепловое спекание (Selective Heat Sintering)
SHS — аналог селективного лазерного спекания (SLS), однако в данной технологии вместо высокоточного лазера применяется направленное определенным образом тепло. Специальная лампа закрывается маской, за счет чего появляется возможность выборочно воздействовать на исходный материал.
Для возможности управления тепловым потоком в этой технологии используются специальные ультрафиолетовые лампы.
Одним из основных преимуществ является то, что для данной длины волны ИКизлучения возможно подобрать два вида материала: один будет пропускать тепло, а другой — отражать. Также одним из основных свойств ИК излучения является возможность подобрать такую длину волны, при которой конкретный материал будет поглощать или отражать все излучение.
Интересно отметить, что один слой толщиной 100 микрон (0,1 мм) печатается всего за 12 секунды. Данная технология — это настоящий прорыв в скоростной печати. Важно подчеркнуть, что модель формируется из порошка, причем весь неиспользованный порошок можно использовать повторно.
Данная технология позволяет изготавливать модели самых сложных геометрических форм, а также печатать несколько деталей одновременно.
Материал для печати: термопластичный порошок.
Технология лазерного спекания распыляемого порошкового материала (Laser Engineered Net Shaping, LENS)
Материал в виде порошка выдувается из сопла и попадает на сфокусированный луч лазера. Часть порошка пролетает мимо, а та часть, которая попадает в фокус лазера, мгновенно спекается и слой за слоем формирует трехмерную деталь. Именно по такой технологии печатают стальные и титановые объекты.
Поскольку до появления этой технологии печатать можно было только объекты из пластика, к 3Dпечати особенно серьезно никто не относился, а эта технология открыла двери для 3Dпечати в «большую» промышленность. Порошки различных материалов можно смешивать и получать таким образом сплавы, как говорится, на лету.
Применение: например, титановые лопатки для турбин с внутренними каналами охлаждения. Производитель оборудования: Optomec.
Послойное распределение клеящего вещества по гипсовому порошку (Powder bed and inkjet head 3d printing, Plaster-based 3D printing, 3DP)
3DP — это специфическая аддитивная технология производства, основанная на использовании порошка и связующего материала. Данная технология запатентована в 1993 году в Массачусетском технологическом институте (MIT) и продана в 1995 году компании Z Corporation, которая, в свою очередь, была приобретена компанией 3D Systems в январе 2012 года.
3DP применяет порошковый метод производства, аналогичный SLS, но вместо спекания или плавления порошка используется связующее вещество (клей), которое вводится в порошок. Для этих целей служит печатающая головка, аналогичная головке струйного 3Dпринтера.
Технология очень проста: есть слой порошка, по нему сверху проходит печатающая головка и избирательно (по форме сечения) наносит специальную связующую жидкость. Свежий слой порошка распространяется по всей поверхности модели, и процесс повторяется. Когда модель готова, несвязанный порошок автоматически удаляется.
Преимущества:
- так как используется клей, в него можно добавить краску и печатать цветные объекты;
- технология относительно дешевая и энергоэффективная;
- можно использовать в условиях дома или офиса;
- для печати можно использовать порошок стекла, костный порошок, переработанную резину, бронзу и даже древесные опилки.
Используя похожую технологию, можно печатать съедобные объекты, например, из сахара или шоколадного порошка. Порошок склеивается специальным пищевым клеем, в клей может добавляться краситель и ароматизатор.
Недостатки:
- на выходе получается достаточно грубая поверхность, с невысоким разрешением — ~ 100 микрон;
- материал нужно подвергать постобработке (запекать), чтобы придать ему необходимые свойства.
Материал для печати: гипс, композит на основе гипса, гипсовый порошок и пр.
Full colour 3D printing, или Цветная трехмерная печать
Дополнение к предыдущему пункту (3DP) — единственная технология, позволяющая получить объект во всем диапазоне возможных цветов. Окрашивание происходит сразу во время построения. Эта технология дает возможность получить фотореалистичные объекты, поэтому она очень интересна дизайнерам, так как ее можно использовать в разработке декоративных моделей и дизайнерских прототипах.
В качестве исходного материала используют порошок на основе гипса. Специальными роликами и щетками сначала формируется тонкий ровный слой порошка. Затем подвижная головка перемещается в горизонтальной плоскости и наносит на нужные участки микроскопические капли клееобразного вещества, по составу напоминающего цианокрилат. Но предварительно вещество окрашивается в соответствии с точным значением цвета в данной точке. Так сооружается слой за слоем. Платформа постепенно опускается, пока объект не будет готов до самой «макушки». Получение необходимого цвета обычно достигается примесью из четырех возможных цветов — почти как в домашних струйных принтерах. По окончании объект обмакивается целиком в цианоакрилат для придания прочности и блеска.
Объекты, созданные при помощи цветной трехмерной печати, не отличаются прочностью и поэтому не используются в качестве деталей механизмов. Еще одна особенность — объекты боятся воды: при контакте с влагой цвета тускнеют. Поэтому при выборе материала важно учитывать назначение предмета.
Рис. 10. Пример цветной 3D-печати
Изготовление объектов с использованием ламинирования (Laminated Object Manufacturing, LOM)
В этой технологии модель изготавливается из тонких слоев полимерной пленки. Предварительно каждый слой будущего изделия вырезается из рабочего материала лазером или механическим резаком. Готовые формы слоев размещаются в установленном порядке и склеиваются. Послойное соединение может происходить разными способами — при помощи местного нагрева, прессованием под давлением или обычным химическим склеиванием.
Материал для печати: бумага, металлическая фольга, полиэтиленовая пленка.
3D-печать от Mcor Technologies
Недавно появившаяся технология, которая позволяет печатать изделия из обычной бумаги формата А4. Резец из твердосплавной стали вырезает каждый слой будущей модели из листа бумаги. Затем слои проклеиваются обычным канцелярским клеем на водной основе. Такую технологию печати использует инновационный 3Dпринтер MATRIX 3000.
Материал для печати: стандартная офисная бумага.
Контурное изготовление (Contour Crafting, CC)
Изобрел технологию профессор Бехрох Хошневис (Behrokh Khoshnevis) из университета Южной Калифорнии. СС — это строительная технология, и оборудование для «печати» можно назвать 3Dпринтером лишь с некоторой натяжкой.
Устройство для печати больше похоже на козловой кран. Вместо многотонного крюка находится распыляющая бетонную смесь головка со встроенными пневматическими формирователями поверхностей. Мгновенно застывающий бетонный раствор слой за слоем наносится на основу дома. Стены, вместе с проемами, вентиляционными отверстиями, дымоходами в прямом смысле этого слова растут на глазах. На возведение полой «коробки» одного коттеджа площадью 100 м2 уходит примерно восемь часов непрерывной работы.
Материал для печати: бетонная смесь.