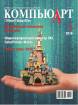
Современные технологии производства мелованных бумаг
Сегодня мелованная бумага составляет подавляющую часть потребляемых типографиями материалов для печати. Чаще всего клиенты заказывают рекламную или представительскую продукцию с использованием мелованной бумаги: листовки, флаеры, буклеты, журналы, каталоги. Такая бумага привлекает потребителей возможностью получить готовую продукцию с более яркими, насыщенными красками по сравнению с печатью на офсетной бумаге без покрытия, а также обладающую приятными тактильными свойствами.
Мелованная бумага — это бумага с пигментированноклеевым покровным слоем (мелованным), нанесенным на волокнистую чистоцеллюлозную или содержащую древесную массу бумагуоснову для получения микропористой и микрошероховатой поверхности.
Важнейшим печатным свойством мелованной бумаги является избирательное впитывание. Пористость ее составляет порядка 30%, а размер пор не превышает 0,03 мкм. Под действием сил капиллярного давления микропоры поверхностного слоя бумаги преимущественно впитывают лишь маловязкий растворитель, входящий в состав печатной краски, а пигмент и пленкообразователь остаются на поверхности бумаги. Это обеспечивает получение на мелованной бумаге яркого, четкого красочного изображения.
Различают одно и двукратное мелование с одно и двусторонним покрытием мелованным слоем. Мелование производится методом покрытия бумажной основы каолином или подобным ему веществом для придания поверхности белизны и гладкости. Мелованная бумага характеризуется наибольшей белизной и гладкостью, которые обеспечивают высокое качество текстовой и изобразительной продукции (многокрасочные репродукции из художественных изданий, книги, альбомы, журналы, реклама).
Основа, то есть бумага под покрытием, также может быть различной: от дешевой с механическим помолом до дорогой, не содержащей частиц древесины, что соответствующим образом сказывается на качестве бумаги.
А теперь поговорим о производстве мелованной бумаги более подробно.
Производство мелованных видов бумаги и картона
Технология начального этапа производства мелованной бумаги практически не отличается от стандартного процесса получения бумаги. Целлюлозная масса наносится на быстро движущуюся сетку бумагоделательной машины. В этот момент в смеси содержится примерно 57% целлюлозы и 9395% воды. По мере прохождения сетки через машину вода удаляется и формируется бумажное полотно. Отсюда возникли понятия «лицевой» и «сеточной» стороны бумаги.
На наиболее современных бумагоделательных машинах (действующих, к примеру, на производствах компаний Sappi, UPMKymmene, MReal, StoraEnso) применяется «двухсеточная» система формирования полотна — целлюлозная масса подается между двух сеток, а также применяется вакуумная система сушки. Поэтому у мелованной бумаги сеточная сторона практически не отличается от лицевой.
Производство мелованной бумаги в Коряжме
В процессе изготовления мелованная бумага обязательно проклеивается либо в массе, либо на стадии отделки. Для уменьшения степени впитываемости связующего печатных красок производится обработка бумаги, придающая ей гидрофобные свойства. При этом поверхностная проклейка снижает вероятность выщипывания волокон из бумажного полотна при типографской печати.
Нанесение на бумагу покрытий позволяет улучшить ее эксплуатационные свойства, в том числе и печатные.
При нанесении меловальных покрытий макропористая поверхность бумаги становится микропористой. Это повышает гладкость бумаги в несколько раз и улучшает ее печатные свойства. Пигментное покрытие снижает прозрачность бумаги, в связи с чем появляется возможность снизить массу и толщину бумаги, а также заменить часть целлюлозы древесной массой без ущерба для свойств бумаги.
Значительное преимущество мелованной бумаги для печати заключается в возможности изменения ее печатных свойств в широком диапазоне за счет изменения композиционного состава пигментного покрытия. Мелование бумаги и картона позволяет повысить полиграфическое качество продукции, увеличить красочность изданий.
Классификация мелованной бумаги
Мелованные бумаги классифицируются:
- по содержанию волокнистых полуфабрикатов;
- по отделке поверхности;
- по количеству сторон и слоев мелования;
- по массе мелованного покрытия;
- по формату.
По компонентному составу мелованные бумаги подразделяются:
- на чистоцеллюлозные, в которых содержание механической древесной массы (МДМ) не превышает 10%;
- на бумаги с содержанием МДМ до 25%.
Бумаги, содержащие МДМ, обладают большей непрозрачностью и гладкостью, чем чистоцеллюлозные, но меньшей белизной и глянцем.
Мелованные виды писчепечатной бумаги:
а) бумаги, содержащие МДМ:
- легкомелованная бумага — LWC (light weight coated) — бумагаоснова массой 2642 г/м2, масса покрытия 712 г/м2;
- печатная бумага — MWC (medium weight coated) — бумагаоснова массой 4275 г/м2; масса покрытия 1115 г/м2;
- печатная бумага с мелованием на БДМ — MFC (mashine finished coated), содержание МДМ — 4565%.
б) бумаги, не содержащие МДМ:
- печатная бумага для копира — WF (woodfree printing paper grades) массой 7080 г/м2; содержание наполнителя — 522 г/м2.
Покрытие бумаги меловальной пастой может быть произведено однократно или многократно. Двукратное покрытие, как правило, происходит в два этапа: сначала слой наносится на встроенной в бумагоделательную машину (БДМ) меловальной установке, а затем на отдельном меловальном оборудовании.
Однако существуют и БДМ, в которых непосредственно выполняется двойное покрытие меловальной пастой. При этом второе покрытие может наноситься на высушенный первый слой (метод «влажным по сухому») или прямо на влажный (метод «влажным по влажному»). Бумага после мелования имеет матовую поверхность, которая после каландрирования приобретает лоск.
Мелование подразделяется на легкое, полное и литое. При различных видах обработки не только варьируется количество наносимой меловальной пасты, но и изменяется характер ее проникновения в структуру бумажного полотна. Глубина проникновения может быть как значительной, так и небольшой.
Масса первого слоя, наносимого на БДМ, невелика — 46 г/м2. Масса второго слоя, который наносится в меловальной установке, больше — 2025 г/м2 (может быть до 40 г/м2). При шаберном меловании избыток пасты удаляется гибким ножом (шабером), а при литом слой напыляется с помощью форсунок, что обеспечивает более равномерное нанесение пасты на бумажное полотно.
Виды мелованной бумаги
Бумага мелованная книжно-журнальная
Применяется для производства иллюстрированных журналов, проспектов, рекламных каталогов и книг с многокрасочной печатью. Ее отличительной особенностью является низкая масса (5080 г/м2).
Тонкая мелованная бумага вырабатывается с использованием механической, термомеханической (ТММ) и химикотермомеханической (ХТММ) древесной массы, чем объясняются высокие показатели непрозрачности (9296%), деформационной устойчивости и перерабатываемости тонкой мелованной бумаги. Бумага с легким (710 г/м2) покрытием (LWC) имеет белизну 6878% (ISO), глянец 4068% (HUNTER), плотность 1,11,2 г/см3. Печать осуществляется на ролевых офсетных и глубокопечатных машинах с принудительной сушкой.
Бумага мелованная для высокохудожественных изданий
Для высокохудожественных изданий выпускают три типа бумаги: глянцевая, высокоглянцевая и матовая (с двух или трехкратным мелованием). Для отделки глянцевой и высокоглянцевой мелованной бумаги используют суперкаландры, а для отделки матовой мелованной бумаги — специальные каландры.
Бумага мелованная этикеточная
В качестве этикеточной выпускаются три вида мелованной бумаги. Чистоцеллюлозная невлагостойкая этикеточная бумага трехслойного мелования лицевой стороны, высокоглянцевая, используется для печати особенно ответственной этикеточной и упаковочной продукции для предметов элитарного назначения. Глянец — 90%, белизна — 86%, непрозрачность — 8287%. Масса бумаги — 80 г/м2.
Бумага мелованная этикеточная
Чистоцеллюлозная влагощелочестойкая этикеточная бумага двухслойного мелования лицевой стороны обладает высокими показателями пухлости, белизны, непрозрачности, истирания во влажном состоянии, стабильностью размеров. Применяется для этикеток на бутылки, в том числе возвратные, а также в производстве подарочной упаковки. Шероховатая сторона обеспечивает беспроблемное приклеивание. Отсутствие эффекта слипания этикеток позволяет использовать ее на высокоскоростных упаковочных линиях. Бумага может поставляться гладкой и с тиснением. Глянец — 40%, белизна — 91%, непрозрачность — 86%. Масса бумаги — 7075 г/м2.
Чистоцеллюлозная глянцевая влагостойкая бумага двухслойного мелования лицевой стороны предназначена для офсетной и флексопечати, может подвергаться различным методам последующей обработки: ламинированию, тиснению, лакированию. Превосходная гладкость и хорошие оптические свойства позволяют добиться исключительных результатов печати.
Применяется при изготовлении высококачественных традиционных этикеток, этикеток на разовую тару, пэтбутылки, жестяные банки, а также при производстве упаковки для шоколада, печенья, сигарет, мыла. Не содержит вредных химических добавок, поэтому применяется для упаковки пищевых продуктов. Глянец — 70%, белизна — 92%, непрозрачность — 86%. Масса бумаги — 7080 г/м2.
Основные характеристики некоторых видов этикеточной бумаги приведены в табл. 1.
Таблица 1. Основные характеристики этикеточной бумаги
Показатель |
Значение показателя |
Метод испытаний |
|
Масса 1 м2 бумаги, г |
80±3 |
70±3 |
ISO 536-1995 |
Толщина, мкм |
76±3 |
82±4 |
ISO 534-2005 |
Влажность, % |
5,5±0,5 |
5,5±0,5 |
ISO 287-1985 |
Разрывное усилие, кН/м: - в машинном направлении - в поперечном |
5,3>4,5 3,0>2,3 |
5,0>3,8 3,8>2,0 |
ISO1924-2-1994 |
Поверхностная впитываемость воды при одностороннем смачивании сеточной стороны по Кобб60, г/м2 |
30 |
17 |
ISO 535-1991 |
Сопротивление раздиранию, мН - в машинном направлении - в поперечном |
500>430 550>450 |
400>300 450>350 |
ISO 1974-1990 |
Глянец (HUNTER 75), % |
60±5 |
60±5 |
ISO 8254-1-1999 |
Шероховатость (PPS 10), мкм |
1,1<1,4 |
1,1<1,4 |
ISO 8791-4-1992 |
Белизна, % ISO |
88,0±2,0 |
85,0±2,0 |
ISO 2740-1999 |
Непрозрачность, % |
87,0+85,0 |
84,0+82,0 |
ISO 2471-1998 |
Картон мелованный для высокохудожественных изданий
Для высокохудожественных изданий выпускаются следующие виды мелованного картона:
- высококачественный беленый полиграфический картон типа «хромэрзац» с двусторонним мелованным покрытием и различными видами тиснения массой 170270 г/м2;
- односторонний картон литого мелования высокоглянцевый, чистоцеллюлозный массой 250, 300, 400 г/м2;
- односторонний металлизированный чистоцеллюлозный картон массой 250 г/м2. Текстура — серебро;
- чистоцеллюлозный картон с двухслойным мелованным покрытием лицевой стороны и пигментированием оборотной стороны массой 190300 г/м2;
- мелованный картон с содержанием механической массы и двухслойным мелованным покрытием лицевой стороны и однослойным мелованным покрытием оборотной стороны массой 215305 г/м2;
- трехслойный картон с односторонним мелованием, добавлением макулатурной массы и отбеленным оборотом массой 250400 г/м2;
- упаковочный картон хромэрзац (GC2) из первичных волокон с двухслойным мелованным покрытием лицевой стороны и белым оборотом массой 220350 г/м2;
- упаковочный картон хромэрзац из первичных волокон с крафтоборотом, повышенной жесткости и массой 230325 г/м2.
Особенности технологии мелованной бумаги
Требования к бумаге-основе
Требования для бумагиосновы определяются условиями нанесения покрытия, назначением готовой продукции и способом печати. Важнейшими свойствами бумагиосновы являются: механическая прочность, пористость, впитывающая способность, влажность, жесткость, белизна, непрозрачность, гладкость и степень проклейки.
Прочность бумагиосновы в общем случае определяется прочностью, размерами и химическим составом волокна. Механическая прочность бумагиосновы необходима для выдерживания напряжения при прохождении бумаги через узел нанесения покрытия, при последующей сушке и суперкаландрировании бумаги.
Свойства бумагиосновы подбираются в зависимости от способа печати. При листовой и офсетной печати возникают значительные усилия, направленные перпендикулярно плоскости листа. В связи с этим основа должна обладать высоким сопротивлением к расслаиванию и высокой связанностью волокон. При нанесении покрытия бумагаоснова вступает в контакт с водными меловальными составами и вода всасывается капиллярами основы, разрушая связи между ними. При увлажнении невлагопрочная бумага теряет до 90% первоначальной прочности в воздушносухом состоянии. Поэтому прочность бумаги во влажном состоянии имеет очень большое значение.
Бумагаоснова должна иметь разрывную длину в машинном направлении не менее 5 км и сопротивление излому не менее 20 двойных перегибов (в поперечном направлении).
Пористость бумагиосновы обусловливает такие свойства, как сжимаемость, прочность и впитывающая способность. Пористость бумаги зависит от упаковки и ориентации волокон в плоскости и объеме листа, поэтому она неодинакова на лицевой и сеточной сторонах. Значительное влияние на пористость оказывает степень помола волокна. При увеличении степени помола уменьшаются пористость и средний диаметр внутренних пор. Каландрирование повышает гладкость бумаги и уменьшает поверхностную пористость.
Впитывающая способность имеет максимальное значение в машинном направлении, а в поперечном она в два раза меньше. Впитывающая способность зависит от пористости верхнего слоя и степени проклейки. Основа должна иметь такую впитывающую способность, которая обеспечила бы надежное закрепление покрытия на поверхности, но в то же время ограничивала бы проникновение жидкости со связующим глубоко внутрь бумагиосновы, так как жидкость ослабляет силы сцепления пигмента с основой. Впитываемость основы при одностороннем смачивании должна находиться в пределах 1560 г/м2.
Жесткость бумаги — это ее способность сопротивляться деформациям под действием собственной массы и внешних сил. С увеличением степени помола наблюдается повышение жесткости. Мокрое прессование и сушка, особенно уплотнение структуры во время сушки, повышают жесткость бумаги. При повышении влажности с 0 до 78% происходит снижение жесткости на 3040%. Влажность бумагиосновы должна быть в пределах 57%.
Белизна бумагиосновы имеет большое значение, так как определяет белизну большинства видов готовой мелованной бумаги. Это обусловлено тем, что масса наносимого покрытия, как правило, недостаточна для полного исключения влияния бумагиосновы. Нанесение покрытий массой 58 г/м2 практически не изменяет белизну мелованной бумаги. Желательно, чтобы степень белизны бумагиосновы была не менее 8285% без оптическиотбеливающих веществ.
Для повышения непрозрачности мелованной бумаги массой 5060 г/м2 в композицию основы вводится рафинерная или дефибрерная древесная масса, что позволяет поддерживать непрозрачность основы на уровне 90%.
Гладкость бумагиосновы, как и равномерная влажность, является обязательным условием. Основа должна иметь гладкую поверхность и равномерную влажность. Однако гладкость бумагиосновы не должна превышать определенного предела (примерно 70 с), выше которого наблюдается ухудшение закрепления покрытия на поверхности бумаги.
Дефекты бумаги-основы
Наиболее часто встречающимся дефектом бумагиосновы является облачный просвет, вызывающий недостаточную гладкость мелованной бумаги и недостаточный глянец технических видов бумаги. Для устранения дефекта необходимо привести в соответствие режим подготовки бумажной массы и отлива полотна, повысить степень помола бумажной массы, снизить ее концентрацию и проверить работу напорного ящика.
Недостаточная гладкость мелованной бумаги может быть вызвана маркировкой полотна от отсасывающих валов, прессовых сукон, ровнителя. Для устранения маркировки необходимо заменить сетки и изношенные прессовые сукна, повысить сухость бумажного полотна, поступающего в прессовую часть.
Ворсистость бумагиосновы устраняется путем снижения температуры первых сушильных цилиндров.
Дефектом основы также является большая пористость изза повышения содержания воздуха в бумажной массе и костричности древесной массы. Улучшение сортировки древесной массы и деаэрация массы перед бумагоделательной машиной позволяют устранить этот дефект.
Качество намотки бумаги и качество рулонов. Дефектные рулоны с неравномерной намоткой, имеющие мягкие или перетянутые кромки, слабую намотку, плохо перерабатываются, вызывая повышенную обрывистость.
Непригодными для переработки являются рулоны, имеющие косые резаные складки и трещины на кромках рулонов от ударов при транспортировке и разгрузке, а также рулоны, в бумажном полотне которых имеется большое количество сквозных отверстий, связанных с засмолением сетки, наличием слизи в бумажной массе, загрязнением машины, плохой работой машинного каландра.
Меловальные составы
Основными компонентами меловальных составов являются пигменты, связующие и вспомогательные вещества (диспергирующие, стабилизирующие гидрофильность, смазывающие, антивспенивающие, отверждающие, оптическиотбеливающие вещества).
Пигменты
Поверхностное покрытие бумаги минеральными пигментами применяется для придания бумаге гладкой и впитывающей печатные краски поверхности, скрытия или изменения цвета бумагиосновы и придания бумаге непрозрачности. Пигменты составляют обычно от 70 до 90% массы покровного слоя мелованной бумаги. Основной целью мелования является придание поверхности микропористой структуры. Это значит, что если до нанесения полимернопигментного покрытия размер пор составлял 110 мкм, то после нанесения не превышает 0,10,6 мкм.
Разработка залежей каолина
Придание поверхности бумаги гладкости и хороших печатных свойств зависит не только от качества и способов покрытия и вида связующего, но и от вида и степени дисперсности применяемого пигмента.
Каолин является основным пигментом, используемым в бумажной промышленности. Это связано с его большими природными запасами, относительно невысокой стоимостью, высокими потребительскими свойствами. Каолин — это «белая глина», основным компонентом которой является каолинит Аl2O3·2SiO2·2H2O.
Количество частиц, имеющих размеры 2 мкм и меньше, служит критерием качества каолина для мелования, в зависимости от содержания которых каолин делят на три категории:
1й сорт — 9295% частиц до 2 мкм;
2й сорт — 80% частиц до 2 мкм;
3й сорт — 72% частиц до 2 мкм.
Изготовители мелованной бумаги всегда стремились получить высокодисперсный каолин для обеспечения трех важных оптических характеристик: белизны, лоска, непрозрачности. Также важным критерием является гранулометрическое распределение частиц между 2 мкм и 0,1 мкм.
Из всех пигментов, применяемых в бумажной промышленности, каолин является наиболее легко диспергируемым пигментом благодаря высокой удельной поверхности и почти полному отсутствию растворимых солей. Минимальное количество химических солей или ионов, адсорбированных частицами каолина, наличие свободных валентных связей на поверхности частиц, появившихся в результате химического или механического разрушения минеральных кристаллов исходного каолина, обусловливают вязкость и тиксотропию каолиновых дисперсий, а также характер взаимодействия каолина с дефлокулирующими реагентами и другими компонентами меловальных составов.
Карбонат кальция (СаСО3) с количественной точки зрения является вторым по значению пигментом для мелования. Он обеспечивает белизну, непрозрачность, хорошую впитывающую способность, снижение вязкости меловальных составов и низкую себестоимость покрытия.
Диоксид титана обладает способностью придавать высокую непрозрачность и белизну бумагам с покрытием. Способность диоксида титана к поглощению ультрафиолетовых лучей делает его незаменимым пигментом при изготовлении упаковки для пищевых продуктов. Размеры частиц обычно находятся в пределах 0,20,5 мкм. Диоксид титана является труднодиспергируемым пигментом. Обычно для диспергирования используют чистые полифосфаты, которые лучше проявляют себя в комбинации с силикатом натрия и едким натром. Характерной особенностью дисперсий диоксида титана является их низкая стабильность при хранении. Наиболее эффективным диспергирующим средством для диоксида титана являются также полиакрилаты натрия.
Барий сернокислый в качестве пигмента для бумажной промышленности характеризуется показателями высокой (до 98%) белизны, высокой дисперсности (размер частиц 0,5 мкм), высокой степени чистоты, нерастворимостью в воде и в большинстве щелочей и кислот, имеет большую удельную массу (4,3 г/см3), а кроме того, отличается высокой стоимостью. Сульфат бария (бланфикс) — синтетический пигмент, получаемый различными способами. Бланфикс хорошо диспергируется гексаметафосфатом натрия, несколько хуже — полифосфатом натрия и отлично — полиакрилатом натрия или аммония.
Сатинвайс — белый пигмент, получаемый при взаимодействии гашеной извести с сульфатом алюминия, имеет общую формулу 6СаО·Аl2О3·3SО4·32Н2О. Основными компонентами для получения сатинвайса являются известь СаО и алюминий, содержащий такие соли, как Al2(SО4)3·18Н2О и квасцы алюмокалиевые KAl(SО4)2·12Н2О. Частицы сатинвайса представляют собой иглообразные пластинки сульфоалюмината кальция размером 0,10,3 мкм.
Сатинвайс используется в покрытиях благодаря своему яркобелому цвету, высокому лоску, который он сообщает бумаге при каландрировании, а также тому, что он способствует получению водоустойчивых покрытий.
Люминесцентные пигменты производят из сульфидов цинка и кадмия или сульфидов кальция и стронция. Люминесцентные пигменты подразделяют на две группы:
1 — флюоресцентные;
2 — фосфоресцентные.
Флюоресцентные пигменты излучают видимый свет только в течение времени, когда они подвергаются воздействию возбуждающего источника света, излучающего энергию в области, близкой к ультрафиолетовым лучам, а фосфоресцентные применяются в основном изза их свечения в течение довольно длительного (до 12 ч) времени после возбуждения. Флюоресцентные пигменты довольно устойчивы и применяются для покрытия или наполнения бумаги. При возбуждении они дают флюоресцентные цвета — от оранжевокрасного до желтого, зеленого, синего и голубого.
Фосфоресцентные пигменты большого периода свечения (612 ч) производятся из смеси сульфидов кальция и стронция, а с коротким периодом свечения (0,52,0 ч) — из смеси сульфидов цинка и кадмия.
Органические пигменты, под которыми обычно подразумеваются органические полимеры на основе полистирола или полиметилола, характеризуются низкой (около 1,5 г/см3) удельной массой, очень высокой (около 99%) белизной и высокой проницаемостью к ультрафиолетовому излучению, что благоприятно сказывается на эффективности действия оптических отбеливателей. Наиболее широко для диспергирования органических пигментов используют полиакрилаты натрия.
Связующие
Связующее вводят в меловальный состав после диспергирования пигментов. Для получения равномерного слоя необходимо, чтобы пигменты были связаны как между собой, так и с бумагойосновой. Эти две функции выполняет связующее. Связующее должно обеспечить меловальному составу следующие свойства:
- желаемый уровень вязкости и совместимость со всеми компонентами покрытия;
- высокую когезионную силу, чтобы связывать между собой макромолекулы, и высокую адгезионную способность — для обеспечения прочной связи покрытия с основой;
- высокую степень удержания воды — для равномерного распределения пигментов на бумаге;
- устойчивость в коллоиднодисперсном виде и высокую прочность связи с пигментом;
- дополнительные к пигментам оптические свойства;
- пористость, способствующую одновременно ускоренной сушке и последующей хорошей адгезии типографской краски.
При приготовлении меловальных составов нужно точно знать необходимое количество связующего, так как оно определяет качество печатных свойств бумаги и ее цену.
Связующее в покрытии распределяется следующим образом: одна часть связующего непосредственно примыкает к основе, другая окружает частицы пигмента, третья занимает промежутки между частицами.
При производстве мелованной бумаги применяют несколько видов связующих.
Упаковки крахмала на складе
Крахмал довольно широко используется в меловальных составах вследствие своей низкой цены: возможно получение меловальных составов с высоким содержанием сухих веществ.
Кpaxмал является углеводным запасом клеток некоторых растений и находится или в зернах (кукуруза) или в корнях и клубнях (картофель). Природный крахмал состоит из зерен или гранул с диаметром от 20 до 40 мкм, нерастворимых в воде. Форма гранул зависит от происхождения продукта.
При нагревании до температуры 6080 °С дисперсия крахмала резко густеет: нагретая вода проникает в зерна крахмала и они разбухают, то есть происходит желатинизация или образование крахмальной загустки. Обычно зерна крахмала имеют незначительную твердость и макромолекулы его делятся на линейные (амилоза) и с ответвлениями (амилопектин).
Амилоза и амилопектин имеют химическую формулу, близкую к целлюлозе, но структура гранул крахмала менее прочна, чем у целлюлозы. В крахмале молекулы объединены в кристаллические зоны, соединенные внутри зон аморфными областями. Макромолекулы связаны водородными связями групп ОН соседних макромолекул. Вода разрушает эти связи, и при нагревании происходит растворение крахмала.
Свойства крахмала определяются соотношением амилозы и амилопектина. Раздельное изучение свойств амилозы и амилопектина показало следующее:
- вязкость меловальных составов на основе амилозы выше, чем на основе амилопектина;
- линейные молекулы склонны к необратимому гелеобразованию (явление ретроградации);
- молекулы амилопектина труднее объединяются друг с другом и обеспечивают лучшую связующую способность, чем линейные цепи, когда степень полимеризации ниже 200;
- в тех случаях, когда нужно получить «цепь — цепь», чтобы усилить определенные характеристики (например, нерастворимость), лучшие результаты получаются с цепями амилозы.
Для того чтобы использовать крахмал в меловальных составах в качестве связующего, из него варят клей. Природный крахмал даже небольшой концентрации дает очень вязкие клеи, и для использования в меловальных составах вязкость необходимо снизить действием кислот, щелочей, энзимов. Такое снижение вязкости получается в результате уменьшения длины цепей амилозы и амилопектина.
Для снижения степени полимеризации наиболее широко используются следующие способы:
- гидролиз минеральными кислотами, в результате которого получается модифицированный крахмал с большим содержанием амилозы, слабыми клеящими и плохими реологическими свойствами;
- лекстринизация, то есть обработка сухого крахмала в присутствии кислоты и при относительно низкой температуре;
- окисление;
- энзиматический гидролиз (варка крахмала в присутствии энзимов с разделением цепей амилозы и амилопектина).
Казеин. В настоящее время применение казеина ограничивается покрытиями с низким содержанием сухого вещества и низкой вязкостью для специальных видов мелованной продукции. Связывающая способность казеина и устойчивость к истиранию во влажном состоянии весьма хорошие. Просохшая пленка — «твердая», и казеин обычно применяется в сочетании с латексом.
При использовании казеина необходимо регулировать адсорбцию печатной краски, которая при больших количествах покровного слоя и связующих веществ легко оказывается слишком низкой, создавая в числе других проблемы склеивания боковых швов. В числе неудобств, связанных с применением казеина, можно назвать проблемы запаха, вспенивания и невыгодную реологию при низком содержании сухого вещества.
Поливиниловый спирт (ПВС) получают действием едкого натра на раствор поливинилацетата в метаноле.
Сорта ПВС, применяемые в покрытиях, являются почти полностью гидролизованными. Молекулярная масса ПВС — от 5000 до 250 000. Содержание сухого вещества в растворах ПВС обычно составляет 510%. Порошок ПВС подается в холодную воду, после чего растворение происходит при температуре 90100 °С.
ПВС придает бумаге с покрытием превосходную поверхностную прочность. Вследствие того что количество добавок при этом может быть низким, достигается хорошая адсорбция красок. Оптические свойства, яркость/белизна, глянец, лоск и непрозрачность такой бумаги имеют лучшие, по сравнению с применением натуральных связующих веществ, показатели. Плохая способность к удержанию влаги создает трудности при прогоне на быстроходных машинах с нанесением покрытия ножевым шабером, когда содержание сухих веществ пасты высокое, что является, вместе с высокой стоимостью, основным недостатком ПВС.
Натрий карбоксиметилцеллюлоза. Наиболее широко применяется растворимая NaКМЦ со степенью полимеризации 3001500. Вязкость растворов зависит от рН среды. NaКМЦ применяют в виде пасты, способной хорошо удерживать воду, что придает ей высокие реологические свойства. Вследствие этого достигается равномерность нанесения NaКМЦ на поверхность бумаги. Так как дозы применения NaКМЦ небольшие, то влияние ее на оптические свойства незначительно.
Латексы занимают первое место среди дисперсий, применяемых в качестве связующих веществ при изготовлении высококачественных печатных изделий. По сравнению с природными связующими веществами латексы имеют следующие преимущества:
- снижают вязкость кроющих материалов, способствуют повышению концентрации сухих веществ;
- обладают большой силой адгезии, способствуют улучшению водостойкости и глянца при каландрировании;
- хорошо удерживают краски, способствуют повышению глянца при печати;
- придают мелованной бумаге эластичность, обеспечивают незначительное закручивание концов бумаги и высокую стабильность размеров;
- поверхность мелованной бумаги имеет более высокие показатели гладкости, лоска, впитывающей способности, сопротивления выщипыванию и истиранию.
Вспомогательные вещества
Диспергирующие вещества. Для взаимной репульсии (отталкивания) частиц при диспергировании и хранении меловальных растворов (паст) используют следующие вещества: анионные полимеры (виниловые кислоты или их соли); полифосфаты; силиконы, лигносульфонаты; КМЦ, крахмал.
Вещества, влияющие на свойства гидрофильности:
NaКМЦ, полиакрилаты, альгинаты.
Смазывающие вещества. Оказывают влияние на внутреннее трение покровной смеси. Используют стеараты кальция, эмульсии воска, полиэтилена.
Антивспениватели — вещества, снижающие пенообразование: масляные кислоты, пеногасители, силиконы.
Нанесение меловальных покрытий
Рецептура покрытий
Основными факторами, учитываемыми при разработке рецептур, являются:
- свойства бумагиосновы;
- технические требования к качеству готовой мелованной продукции;
- оборудование и устройства для нанесения покрытий, сушки и отделки.
Составы для нанесения в клеильном прессе (для упрочнения поверхности бумаги, снижения пыления и выщипывания), в массных частях: крахмал окисленный — 90; мочевиноформальдегидная смола — 10; пластификатор — 1. Масса покрытия — 23 г/м2.
Состав для нанесения на офсетную бумагу воздушным шабером: каолин — 90; мел природный тонкодисперсный — 10; NaOH — 0,1; диспергатор — 0,1; латекс — 16; NaКМЦ — 2; оптический отбеливатель — 0,4. Толщина слоя — 7,532 г/м2.
В последние годы устройства для мелования и каландрирования включают в состав сушильной части БДМ. Основное преимущество таких конструктивных решений заключается в существенной экономии производственных площадей. Включение установок для мелования в состав БДМ стало возможным после разработки валкового устройства пленочного типа, с помощью которого покровную пасту наносят одновременно на обе стороны бумажного полотна при сохранении контурного профиля бумаги. Конструкции меловального устройства имеют два вала, к каждому из которых примыкает дозирующий вал, вращающийся со скоростью, которая отличается от скорости наносящего вала, благодаря чему в пленке наносимого покровного состава возникают усилия сдвига, обеспечивающие стабильность пленки при высокой скорости.
Современная машина для нанесения меловальных составов включает следующие устройства: раскат, узел нанесения, узлы сушки и отделки покрытия, накат. Специфической частью является узел нанесения, выполняющий три операции:
1. Нанесение меловального состава на бумагуоснову.
2. Дозировка количества наносимого состава.
3. Разравнивание нанесенного состава.
Устройства для нанесения меловальных покрытий
Выбор устройства определяется структурой покрытия, массой 1 м2 и свойствами конечного продукта. Масса покрытия может изменяться от 12 до 2530 г и более на 1 м2. От одних покрытий требуется строгая равномерность толщины, от других — ровность поверхности. Покрытия бывают однослойные и многослойные.
Наиболее распространенные типы меловальных устройств и их технические характеристики представлены в табл. 2.
Таблица 2. Техническая характеристика меловальных устройств
Показатель |
Тип устройства |
||||
Клеильный пресс |
Вращающийся шабер |
Вращающийся стержень |
Воздушный шабер |
Ножевой шабер |
|
Масса 1 м2 покрытия, г |
1-6 |
2-6 |
3-10 |
8-35 |
6-30 |
Содержание сухих веществ, % |
30-45 |
35-55 |
40-55 |
35-50 |
55-73 |
Вязкость, Пас |
до 400 |
50-1400 |
100-2000 |
5-500 |
1000-8000 |
Максимальная скорость, м/мин |
500 |
400 |
700 |
450 |
1500 |
Способ сушки (И — инфракрасная; А — аэрофонтанная; Ц — цилиндровая) |
А+Ц ли И+Ц |
И или А+Ц |
А или И+Ц |
А+Ц или И+А+Ц |
А+Ц или И+А+Ц |
Способы нанесения покрытий
Клеильный пресс состоит из двух валов: твердого (резина, стонит, бронза) и мягкого (резина). Состав вязкостью 0,010,02 Пас наносится на бумагу и разравнивается за одну операцию. Между валами клеильного пресса при помощи гидравлики или пневматики создается линейное давление 13 Н/м. Твердость резиновой рубашки мягкого вала подбирается в зависимости от рабочей скорости, диаметра валов, линейного давления, реологических свойств меловальных составов, влажности основы и свойств бумаги с покрытием. Меловальный состав подается на одну или обе стороны полотна бумаги при помощи спрысков. Твердый вал устанавливают, как правило, для верхней стороны полотна. На клеильном прессе может наноситься покрытие массой 16 г/м2 при скорости до 500 м/мин.
Клеильный пресс
По взаимному расположению валов различают вертикальный, горизонтальный и наклонный прессы.
Наклонный клеильный пресс является оптимальным вариантом. Угол между межосевой плоскостью валов и горизонтальной плоскостью составляет 45°, благодаря чему операция заправки бумаги оказывается более простой, чем у горизонтального пресса. При работе пресса бумага охватывает нижний вал, поэтому нагрузка от избытка меловального состава на полотно и попадание воздуха в зазор уменьшаются, что снижает возможность обрыва полотна в прессе.
Устройства с воздушным шабером для нанесения покрытия на бумагу и особенно на картон получили наиболее широкое распространение.
Принцип действия устройства состоит в следующем: меловальный состав наносится в избытке на одну сторону полотна бумаги. Бумага всасывает воду из граничащих с ней слоев суспензии, в результате концентрaция и вязкость состава в этих слоях повышается. Верхние слои меловального состава остаются во влажном состоянии и снимаются струей воздуха. Одновременно покрытие разравнивается. Струя воздуха создается и направляется воздушным шабером, состоящим из камеры с повышенным давлением и направляющих пластин, которые образуют регулируемое сопло в виде щели одинаковой ширины. Расход воздуха в шабере и его скорость на выходе из сопла зависят от размера сопла и давления воздуха и наряду с температурой являются важнейшими характеристиками.
Устройства с механическим шабером отличаются тем, что дозировка и разравнивание меловального состава осуществляются металлическим гибким шабером, представляющим собой заточенную пластину толщиной
0,30,5 мм. Повышение жесткости разравнивающего тела по сравнению с воздушной струей и обрезиненными валиками позволило повысить содержание сухих веществ в составе до 6570%, а скорость машины — до 10001500 м/мин.
Устройствами с механическим шабером широко оснащаются бумагоделательные машины и отдельно стоящие установки, что обусловлено высоким качеством структуры поверхности покрытия и высокой производительностью.
В настоящее время известно большое количество конструкций меловальных устройств с использованием металлического шабера. Главными узлами устройства являются встречный валик, наносящий валик с ванной, а также несущие и прижимные устройства лезвия. Обрезиненный наносящий валик должен иметь подходящую бомбировку, чтобы зазор в захвате между ним и встречным валиком был одинаковым в поперечном направлении машины. Захват между наносящим и встречным валиками, а также скорость наносящего валика подбираются в каждом отдельном случае таким образом, чтобы на бумагуоснову поступало достаточное количество меловальной пасты.
Обычно зазор в захвате составляет около 1 мм, а окружная скорость наносящего валика — около 20% от скорости меловальной машины. Несущие и прижимные устройства лезвия должны допускать точное регулирование прижима и угла наклона лезвия во время работы. При небольших количествах наносимого покрытия угол обычно составляет 50°, а при больших количествах покрытия — 1540°.
При меловании бумаги в установке с ножевым шабером бумажное полотно проводится через захват между двумя валиками, вращающимися в разных направлениях, нижний наносящий валик подает в захват меловальный состав. После захвата полотно уходит по упорному валику, а на полотне находится избыток меловального состава, который снимается с помощью шабера, прижатого к полотну и упорному валику.
Сегодня используется несколько способов мелования бумаги. Перспективным является метод шторного мелования. В устройстве для его осуществления отсутствуют механические элементы для разравнивания пасты по поверхности полотна. Паста вытесняется через узкую щель напускной камеры и под действием силы тяжести падает на полотно в виде шторы. В точке соприкосновения с полотном штора изменяет направление движения и растягивается, образуя на поверхности бумаги тонкую пленку, которая высушивается воздухом.
Недостатком метода шторного мелования является то, что покрытие наносится только на одну сторону полотна. Масса покровного слоя регулируется скоростью движения бумажного полотна и шторы, а также содержанием сухого вещества в пасте. Дозирование пасты завершается до момента ее контакта с полотном, благодаря чему равномерность толщины слоя не зависит от неровностей поверхности полотнаосновы. В результате обеспечивается высокая степень равномерности покрытия полотна в машинном и поперечном направлениях, а отсутствие механических деталей, соприкасающихся с полотном, снижает требования к прочности бумажного полотна и уменьшает количество обрывов.
Мелование посредством хромированного цилиндра применяется для получения бумаги односторонней гладкости. Влажное бумажное полотно прижимается к поверхности хромированного большого цилиндра, нагретого до высокой температуры.
В системе мелования хромированным цилиндром используют тот же принцип: бумага, на которую нанесен дозированный слой влажного мелованного покрытия, прижимаясь к хромированному цилиндру, шлифуется поверхностью цилиндра, приобретая зеркальную поверхность. Этот метод, особенно пригодный для тяжелой бумаги и полукартона, называется также «литым мелованием» (castcoaling).
Сушка мелованной бумаги
Мелованная бумага является капиллярнопористым материалом, сушка которого представляет собой взаимодействие процессов массо и теплообмена. Бумага содержит следующие виды влаги: влага намокания, капиллярная, осмотическая, адсорбционная или гидратационная влага, химически связанная влага. Мелованную бумагу сушат следующими способами: контактным, воздушным, инфракрасной сушкой.
Суперкаландр типа Kleinewefers
Отделка мелованной бумаги
Важным этапом производства является каландрирование — обработка поверхности бумаги, позволяющая повысить ее прочность, гладкость и лоск.
Каландрирование — это прохождение полотна бумаги между валами с эластичной или твердой поверхностью, которое происходит под давлением и при высокой температуре. Чем сильнее бумага спрессована валами каландра, тем она менее пухлая и более прозрачная. При производстве высококачественной мелованной бумаги следует соблюдать баланс гладкости бумагиосновы и непрозрачности; особенно это важно для тонких бумаг, в которых содержание веществ, необходимых для получения мелованного покрытия, сравнимо с содержанием волокна. Для отделки мелованной бумаги применяются суперкаландры. На суперкаландре полотно бумаги обрабатывается между металлическим и эластичным валами. Количество валов обычно составляет 1012 штук.
Суперкаландр имеет раскат, накат и устройство для натяжения бумажного полотна. Максимальная скорость суперкаландра — 1500 м/мин.
Для получения бумаги с одинаковой гладкостью обеих сторон посередине каландра устанавливаются два набивных вала, нижний и верхний валы делаются большего диаметра и имеют бомбировки. Валы с бумажной набивкой для каландрирования тонкой мелованной и некоторых технических бумаг набиваются бумагой, содержащей волокна шерсти, а для высокосортной мелованной бумаги — специальными сортами хлопка. В целях улучшения лоска при каландрировании мелованной бумаги прибегают к паровой обработке.
Основными факторами, определяющими эффективность суперкаландрирования, являются: линейное давление, температура и влажность, а также продолжительность пребывания полотна на суперкаландре.
Готовая мелованная бумага направляется на резку, сортирование и упаковку.