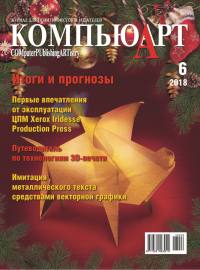
Путеводитель по технологиям 3D-печати
Интерес к 3Dпечати растет с каждым днем. Становится все больше людей, которые хотя бы раз слышали о 3Dпринтере. Так что же это такое?
Термин «3Dпечать» имеет несколько синонимов, один из которых достаточно кратко и точно характеризует сущность процесса — «аддитивное производство», то есть производство за счет добавления материала и обычно относится к инструментам быстрого прототипирования.
Термин был придуман не случайно, ибо в этом и состоит основное отличие множества технологий 3Dпечати от привычных методов промышленного производства, получивших в свою очередь название «субтрактивных технологий», то есть «отнимающих». Если при фрезеровке, шлифовке, резке и прочих схожих процедурах лишний материал удаляется с заготовки, то в случае с аддитивным производством материал постепенно добавляется до получения цельной модели.
Интересный момент — несмотря на то, что работа над созданием 3Dпринтеров велась с 1980х годов прошлого столетия, термин «3Dпечать» был создан лишь в 1995 году студентами Массачусетского технологического института. А вот понятие «3Dпринтер» официально используется с 1996 года, с момента создания машины Actua 2100 от компании 3D Systems.
Небольшой исторический экскурс
В 1984 году компания Charles Hull разработала технологию трехмерной печати для воспроизведения объектов с использованием цифровых данных, а двумя годами позже дала название и запатентовала технику стереолитографии.
Тогда же эта компания разработала и создала первый промышленный 3Dпринтер. Впоследствии эстафету приняла компания 3D Systems, разработавшая в 1988 году модель принтера для 3Dпечати в домашних условиях — SLA250.
В том же году компанией Scott Grump было изобретено моделирование плавлеными осаждениями. Через несколько лет, в 1991 году, компания Helisys разрабатывает и выпускает на рынок технологию для производства многослойных объектов, а еще через год, в 1992 году, в компании DTM выходит в свет первая система селективного лазерного спаивания.
Затем, в 1993 году, основывается компания Solidscape, которая и приступает уже к серийному производству принтеров на струйной основе, которые способны производить небольшие детали с идеальной поверхностью, причем при относительно небольших затратах.
Тогда же Массачусетский университет патентует технологию трехмерной печати, подобную струйной технологии обычных 2Dприн
теров.
Но, пожалуй, пик развития и популярности 3Dпечати все же пришелся на новый, XXI век. В 2005 году появился первый 3Dпринтер, способный печатать в цвете, — это детище компании Z Corp под названием Spectrum Z510.
Технологии
3Dпечать может осуществляться разными способами и с использованием различных материалов, но в основе любого из них лежит принцип послойного создания («выращивания») твердого объекта.
Виды технологий, применяемые для создания слоев:
- экструзия (FDM, DIW);
- фотополимеризация (SLA,DLP);
- формирование слоя на выровненном слое порошка (3DP, EBM, SLS, DMLS, SHS);
- подача проволочного материала (EBF);
- ламинирование (LOM);
- точечная подача порошка (DED);
- струйная печать (MJM).
Экструзия
Экструзия включает две технологии: моделирование методом наплавления (англ. Fused deposition modeling, FDM) и робокастинг (англ. Robocasting или Direct Ink Writing, DIW).
FDM
Моделирование методом послойного наплавления (англ. Fused deposition modeling (FDM)) — технология аддитивного производства, широко используемая при создании трехмерных моделей, при прототипировании и в промышленном производстве.
Технология FDM подразумевает создание трехмерных объектов за счет нанесения последовательных слоев материала, повторяющих контуры цифровой модели. Как правило, в качестве материалов для печати выступают термопластики, поставляемые в виде катушек нитей или прутков. Но это может быть и другой плавкий материал в виде нити, например металл, воск и пр.
FDM 3D-принтер Makerbot Replicator
Технология FDM была разработана С. Скоттом Крампом в конце 1980х и вышла на коммерческий рынок в 1990 году.
Оригинальный термин «Fused Deposition Modeling» и аббревиатура FDM являются торговыми марками компании Stratasys. Энтузиасты 3Dпечати, участники проекта RepRap, придумали аналогичный термин «Fused Filament Fabrication» («Производство способом наплавления нитей»), или FFF, для использования в обход юридических ограничений. Термины FDM и FFF равнозначны по смыслу и назначению.
В данное время технология получает всё большее распространение среди любителей, создающих принтеры с открытым исходным кодом, а также коммерческих предприятий ввиду истечения срока действия оригинального патента. В свою очередь, широкое распространение технологии привело к существенному снижению цен на 3Dпринтеры, использующие данный способ производства.
Производственный цикл начинается с обработки трехмерной цифровой модели. Модель в формате STL делится на слои и ориентируется наиболее подходящим образом для печати. Процесс подготовки модели для печати называется Slicing, в результате которого генерируется Gcode. В нем закладываются все параметры печати, перемещения экструдера, при необходимости генерируются поддерживающие структуры, необходимые для печати нависающих элементов. Некоторые устройства позволяют использовать разные материалы во время одного производственного цикла. То есть в процессе участвуют две рабочие головки: одна выдавливает на платформу рабочий материал, другая — материал поддержки. Например, возможна печать модели из одного материала с печатью опор из другого, легкорастворимого материала, что позволяет с легкостью удалять поддерживающие структуры после завершения процесса печати. В качестве альтернативы возможна печать разными цветами одного и того же вида пластика при создании единой модели.
Изделие, или «модель», производится выдавливанием («экструзией») и нанесением микрокапель расплавленного термопластика с формированием последовательных слоев, застывающих сразу после экструдирования.
Пластиковая нить разматывается с катушки и подается в экструдер — устройство, оснащенное механическим приводом для подачи нити, нагревательным элементом для плавки материала и соплом, через которое осуществляется непосредственно экструзия. Нагревательный элемент служит для нагревания сопла, которое, в свою очередь, плавит пластиковую нить и подает расплавленный материал на строящуюся модель. Как правило, верхняя часть сопла, наоборот, охлаждается с помощью вентилятора для создания резкого градиента температур, необходимого для обеспечения плавной подачи материала.
Экструдер перемещается в горизонтальной и вертикальной плоскостях под контролем алгоритмов, аналогичных используемым в станках с числовым программным управлением. Сопло перемещается по траектории, заданной системой автоматизированного проектирования. Модель строится слой за слоем, снизу вверх. Как правило, экструдер (также называемый печатающей головкой) приводится в движение шаговыми двигателями или сервоприводами. Наиболее популярной системой координат, применяемой в FDM, является прямоугольная, с осями X, Y и Z. Альтернативой является цилиндрическая система координат, используемая так называемыми дельтароботами.
Технология FDM отличается высокой гибкостью, но имеет определенные ограничения. Хотя создание нависающих структур возможно при небольших углах наклона, в случае с большими углами необходимо использование искусственных опор, как правило, создающихся в процессе печати и отделяемых от модели по завершении процесса.
В качестве расходных материалов доступны всевозможные термопластики и композиты, включая ABS, PLA, поликарбонаты, полиамиды, полистирол, лигнин и многие другие. Как правило, различные материалы предоставляют выбор баланса между определенными прочностными и температурными характеристиками.
Это единственная технология, использующая термопластики производственного класса, обеспечивающие не имеющую аналогов механическую, термическую и химическую прочность деталей.
Моделирование методом послойного наплавления (FDM) применяется для быстрого прототипирования и быстрого производства. Быстрое прототипирование облегчает повторное испытание с последовательной, пошаговой модернизацией предмета. Быстрое производство служит в качестве недорогой альтернативы стандартным способам при создании мелкосерийных партий.
FDM является одним из наименее дорогих способов печати, что обеспечивает растущую популярность бытовых принтеров, основанных на этой технологии. В быту 3Dпринтеры, работающие по технологии FDM, могут применяться для создания самых разных объектов целевого назначения, а также игрушек, украшений и сувениров.
DIW
Робокастинг (англ. Robocasting, в англоязычных источниках используется также термин Direct Ink Writing, DIW) — аддитивная технология, осуществляющая послойную 3Dпечать объекта путем экструзии «чернил» через формующее отверстие головки 3Dпринтера. Технология была впервые применена в США в 1996 году для изготовления геометрически сложных керамических предметов. 3Dобъекты, изготавливаемые при помощи САПР, в робокастинге делятся на слои таким же образом, как и в других технологиях 3Dпечати. Жидкость (обычно керамический шлам), по аналогии с технологиями обычной печати именуемая «чернила», поступает через сопло небольшого диаметра, которое перемещается в соответствии с цифровой моделью.
«Чернила» выходят из сопла в жидком состоянии, но сразу же принимают нужную форму благодаря псевдопластичности. Этим робокастинг отличается от моделирования методом наплавления, поскольку для него не требуется затвердевания или сушки «чернил», они сразу принимают нужную форму.
Печатающий узел с соплом принтера, работающего по технологии DIW
Использование технологии робокастинга начинается с создания файла формата STL с расчетом размеров диаметра формующего отверстия. Первую часть изделия, изготавливаемого путем робокастинга, получают путем экструзии нитей «чернил» в первый слой. Далее рабочая площадь смещается вниз либо формующее отверстие поднимается вверх и следующий слой наносится в требуемом месте. Это повторяется до тех пор, пока изделие не будет завершено. При использовании механизмов с числовым программным управлением, как правило, перемещения формующего отверстия регулируются прикладным программным обеспечением. Шаговые двигатели и серводвигатели обычно используются для перемещения формующего отверстия с точностью до нанометров.
После изготовления изделия методом робокастинга для придания изделию требуемых механических свойств обычно применяется сушка и другие способы.
В зависимости от состава «чернил», скорости печати и условий окружающей среды, робокастинг, как правило, позволяет изготавливать конструкции значительной длины (во много раз превышающей диаметр формующего отверстия), при этом не поддерживаемые снизу. Это дает возможность легко изготавливать 3Dконструкции довольно сложной формы, что невозможно при использовании других аддитивных технологий, что является чрезвычайно перспективным для производства фотонных кристаллов, костных трансплантатов, фильтров и т.д. Робокастинг позволяет осуществлять печать изделий любой формы и в любом положении.
Технология обеспечивает изготовление неплотных керамических изделий, которые нуждаются в обжиге перед дальнейшим использованием (по аналогии с керамическим горшком из мокрой глины), изделий самых разнообразных геометрических форм и размеров. На сегодняшний день робокастинг наиболее востребован в производстве биологически совместимых материалов для искусственных органов: путем 3Dсканирования можно определить точную форму требуемой ткани или органа, разработать ее цифровую 3Dмодель и распечатать, например, из фосфата кальция или гидроксиапатита. Другие потенциальные области применения робокастинга включают производство объектов со сложной структурой поверхности, например, многослойных катализаторов или электролитических топливных элементов.
Робокастинг также может использоваться для нанесения полимерных и гелевых чернил при диаметрах формующих отверстий менее 2 мкм, что невозможно в случае керамических чернил.
Фотополимеризация
Фотополимеризация также представлена в двух вариантах технологий.
SLA
Лазерная стереолитография (сокр. SLA и STL от англ. Stereolithography) — одна из технологий быстрого прототипирования. Аппарат для стереолитографии впервые был запатентован Чаком Халлом в 1984 году.
Технология лазерной стереолитографии основана на фотоинициированной лазерным излучением или излучением ртутных ламп полимеризации фотополимеризующейся композиции (ФПК).
Данный метод отличается от других тем, что в нем используют в качестве «строительного материала» не порошки, а фотополимеры в жидком состоянии. В емкость с жидким фотополимером помещается сетчатая платформа (элеватор), на которой осуществляется «выращивание» прототипа.
SLA 3D-принтер Formlabs
С помощью этой технологии спроектированный на компьютере трехмерный объект синтезируется из жидкой ФПК последовательными тонкими (0,050,2 мм) слоями, формируемыми под действием лазерного излучения на подвижной платформе. Как правило, процессор формирования горизонтальных сечений предварительно преобразует описание 3Dмодели будущего объекта из формата STLфайла в совокупность послойных сечений с требуемым шагом по высоте, массив которых записывается в исполнительный файл с расширением SLI. Данный файл представляет собой набор двумерных векторных данных, обеспечивающих последовательное управление ориентацией луча лазера посредством зеркал в процессе синтеза объекта, команды на включение лазера, перемещение платформы и т.д.
Далее включается лазер, воздействующий на те участки полимера, которые соответствуют стенкам целевого объекта, вызывая их отверждение. После этого вся платформа погружается чуть глубже, на величину, равную толщине слоя. Также в этот момент специальная щетка орошает участки, которые могли остаться сухими вследствие некоторого поверхностного натяжения жидкости. По завершении построения объект погружают в ванну со специальными составами для удаления излишков и очистки. И наконец, происходит финальное облучение мощным ультрафиолетовым светом для окончательного отверждения. Как и многие другие методы 3Dпрототипирования, SLA требует возведения поддерживающих структур, которые вручную удаляются по завершении печати.
Лазерная стереолитография позволяет в кратчайшие сроки (от нескольких часов до нескольких дней) пройти путь от конструкторской или дизайнерской идеи до готовой модели детали.
Особенности:
- изза выборочного отверждения на компоненты и технологию процесса налагаются жесткие двусторонние ограничения. Например, чем гуще смола изначально, тем легче ее перевести в полимерное состояние, но и тем хуже ее гидромеханические качества. Для чрезмерно жидкого полимера требуется больше времени на успокоение его поверхности после перемещения платформы;
- чем мощнее введенный в смолу фотоинициатор, тем меньше времени нужно слабому лазеру для засветки, но и тем меньшее время жизни у всего объема смолы, так как он подвержен фоновой засветке.
Основным отличием производителей лазерных стереолитографов являются указанные выше характеристики, так как в целом устройство и принцип действия таких машин идентичны. В любой SLAмашине возможно применение любого расходного материала после соответствующей настройки.
Одно из преимуществ 3Dпечати методом SLA — скорость, составляющая в среднем 47 мм/ч по высоте модели (зависит от загрузки рабочей платформы и шага построения).
Один из производителей оборудования для стереолитографии — компания 3D Systems (США), — предлагает машины с размерами камеры синтеза от 250×250×250 до 1500×750×500 мм. А бельгийская компания Materialise создала аппарат, способный создавать объекты размером до 2 м.
Среди недостатков SLA обычно называют высокую стоимость как оборудования, так и расходного материала.
Области применения:
- создание конструкторских и дизайнерских прототипов, макетов различных изделий и сборок;
- изготовление формообразующей оснастки при различных видах точного литья. Создание моделей для изготовления формообразующей оснастки из других материалов;
- создание мастермодели при изготовлении электродов для электроэрозионной обработки;
- восстановление объектов по данным рентгеновской, акустической или ЯМРтомографии в медицине, криминалистике, археологии и др.;
- изготовление микрооптики из прозрачных пластических материалов.
DLP
Метод 3Dпечати DLP — альтернативный метод SLA, вместо лазерных установок использующий светодиодные проекторы, которые в разы снижают стоимость 3Dпринтеров.
В отличие от SLA, которая сканирует одной или несколькими лазерными головками поверхность материала, DLP 3Dпринтеры проецируют изображение целого слоя до отверждения полимерной смолы, после чего и наносится следующий слой строительного материала — таким образом, слой за слоем, формируется будущий прототип. 3Dпринтеры, работающие по технологии DLP, показывают высокие результаты, сопоставимые по точности и качеству с оригинальной технологией лазерной стереолитографии (SLA).
Рабочее пространство DLP 3D-принтера AnyCubic Photon
DLP 3Dпринтеры составляют большую конкуренцию SLA 3Dпринтерам. Применяются DLP 3Dпринтеры в стоматологии, ювелирной промышленности, машиностроении, а также в дизайне и производстве сувениров.
Плюсы и минусы: DLP 3Dпринтеры имеют высокие показатели точности печати — минимальная толщина слоя может достигать 12 микрон. Но практически разрешение зависит от скорости построения слоев, то есть технология позволяет получить и более высокие показатели, и более высокую точность путем снижения скорости печати. Материал построения, он же фотополимер или фотополимерные смолы, имеют широкий диапазон механических характеристик: от твердых пластиков до резины. Главный недостаток метода DLP — высокая стоимость фотополимерной смолы.
Формирование на выровненном слое порошка
Данный тип 3Dпечати представлен такими технологиями, как 3D Printing (3DP), электроннолучевая плавка (англ. Electronbeam melting, EBM), селективное лазерное спекание (англ. Selective laser sintering, SLS), прямое лазерное спекание металла (англ. Direct metal laser sintering, DMLS) и выборочное тепловое спекание (англ. Selective heat sintering, SHS).
3DP
Струйная трехмерная печать (3DP) — один из старейших методов аддитивного производства. Эта технология была разработана в Массачусетском технологическом институте (MIT) в 1993 году. Технология получила коммерческое распространение в 1995 году с помощью компании Z Corporation, в 2012 году приобретенной корпорацией 3D Systems.
Как и другие технологии аддитивного производства, струйная трехмерная печать подразумевает послойное построение физических объектов на основе цифровой трехмерной модели. В качестве расходных материалов используются всевозможные порошки, наносимые последовательными тонкими слоями. Контуры модели вычерчиваются печатной головкой, наносящей связующий материал (клей). Таким образом, частицы каждого нового слоя склеиваются между собой и с предыдущими слоями до образования готовой трехмерной модели.
Готовое изделие в устройстве ZPrinter 650
Оригинальные устройства использовали в качестве расходного материала гипс, что обусловливает обиходное название технологии — «гипсовая трехмерная печать». Печатные головки экструдировали воду, склеивающую материал. Со временем технология прогрессировала и теперь включает возможность добавки различных агентов: красителей, уплотнителей и пр.
В настоящее время помимо гипса используются самые разные материалы, в том числе пластики, песчаные смеси и даже металлы. Технология способна создавать трехмерные модели из любого порошкового материала, а добавление красителей в связующий материал позволяет осуществлять цветную печать.
Практичность же моделей зависит от последующей обработки. Например, изделия, созданные из металлического порошка, будут иметь вид, схожий с необработанными металлическими изделиями. С другой стороны, их прочность будет напрямую зависеть от связующего материала, то есть, по всей вероятности, будет невысокой. Для улучшения механических свойств можно прибегнуть к обжигу с помощью гончарных печей. Во избежание деформации моделей обжиг, как правило, подразумевает не спекание, а выплавку изначального связующего материала с пропиткой более твердой субстанцией. Например, возможна выплавка или выжигание связующих пластиков с одновременной пропиткой стальной модели медью или бронзой.
Готовые изделия будут иметь высокую долговечность, но их механические характеристики все равно окажутся недостаточными для применения в качестве функциональных прототипов деталей механизмов. Как правило, модели, изготовленные по технологии 3DP, используются в качестве сувениров, украшений или макетов — любых моделей высокой геометрической сложности, не подверженных серьезным механическим нагрузкам.
Стоит отметить экономичность технологии: остаточный порошок может быть собран из рабочей камеры по завершении печати и использован в следующем производственном цикле.
Технология 3DP пользуется широкой популярностью и применяется в самых различных отраслях, зачастую теряя свое оригинальное обозначение. Так, в сфере биопечати используется вариант технологии, известный как «капельная/струйная печать» или DOD (Drop on Demand). Этот метод применяется для послойного нанесения живых клеток с целью построения органических тканей.
Одним из наиболее ярких методов применения 3DP стало создание кондитерских принтеров ChefJet, строящих трехмерные съедобные модели из сахаросодержащих продуктов, склеивая частицы материала водой, наподобие оригинальных «гипсовых» принтеров.
EBM
Электроннолучевая плавка (англ. Electron Beam Melting, или EBM) — метод аддитивного производства, схожий с селективным лазерным спеканием (SLS), но использующий вместо лазера луч высокоэнергетических электронов в вакууме. Первопроходцем и по совместительству лидером в производстве аппаратов EBM является шведский концерн Acram.
Как и в случае с SLS, расходным материалом для EBM, как правило, является порошок, измельченный до консистенции пудры при помощи шаровых мельниц. В качестве материала обычно используется титан, сплавы на его основе и некоторые марки стали.
Ацетабулярные чашки эндопротеза,
отпечатанные по технологии EBM на 3D-принтере Arcam Q10plus
Однако инженеры разработали специальный материал — металлоглину. Металлическая глина, используемая в качестве чернил во время электроннолучевой плавки, изготавливается из смеси органического клея, металлической стружки и определенного количества воды. Для того чтобы превратить такие чернила в твердый объект, его нужно нагреть до температуры, при которой клей и вода выгорят, а стружка сплавится в монолит.
Нужно сказать, что данный метод обеспечивает высокое качество печати и отличную прорисовку мелких деталей.
При электроннолучевой плавке загрязнение материала посторонними примесями почти отсутствует. Благодаря наличию высокого вакуума имеется возможность удаления примесей из материала.
Легкость управления мощностью электронного пучка позволяет использовать разнообразные режимы плавки. Возможна даже температура расплава, превышающая температуру плавления.
К недостаткам технологии можно отнести наличие рентгеновского излучения, которое возникает при бомбардировке электронами металлов (так называемое «тормозное излучение»). Эта особенность требует установки в рабочей камере специального поглощающего покрытия.
В целом технология EBM более сложна, чем SLS, однако ее производственный потенциал более высок. Так, концерн Acram добился больших успехов в производстве различных авиационных деталей и ортопедических имплантов. В авиационной промышленности метод EBM используется для изготовления жаростойких форсунок и лопаток газовых турбин. Что же касается ортопедических имплантов, то они привлекательны своей легкостью и прочностью. К тому же, эта технология позволяет создавать полые и пористые структуры.
К сожалению, метод электроннолучевой плавки доступен только в промышленных масштабах. На сегодняшний день полноценного домашнего 3Dпринтера, работающего по этой технологии, не существует.
SLS
Селективное лазерное спекание — это метод аддитивного производства, который заключается в спекании мелкодисперсного порошкового (обычно металлического) материала с помощью лазера. Процесс нацеливания лазера осуществляется автоматически по заранее созданной 3Dмодели, которая может быть создана в графическом редакторе.
Метод селективного лазерного спекания был разработан и запатентован в результате совместной работы доктора Карла Декарда и научного руководителя, доктора Джо Бимана в Техасском университете в Остине в середине 1980х годов при поддержке Агентства по перспективным оборонным научноисследовательским разработкам США.
Декард и Биман участвовали в создании компании для продвижения технологии селективного лазерного спекания на рынок, однако фирма была выкуплена в 2001 году конкурентами — компанией 3D Systems. С 2014 года технология является общедоступной в связи с истекшим сроком последнего заявленного патента.
Для создания изделия путем селективного лазерного спекания на поверхность подложки наносится слой порошка, поступающий из емкости подачи, и равномерно распределяется с помощью устройства выравнивания. Включается лазер, луч которого, направляемый подвижными зеркалами и фокусирующей линзой, по сгенерированным 3Dмоделям сканирует поверхность нанесенного слоя порошка и формирует первичный слой печатаемого объекта методом спекания. В результате оказываются спеченными те области, которые соответствуют текущему срезу изделия.
Готовые изделия в поддоне SLS 3D-принтера
По завершении сканирования подвижное дно рабочей камеры опускается на толщину наносимого слоя порошка, тем самым переходя к следующему срезу изделия. При необходимости на поверхность сканирования добавляется порошок, так как в процессе работы он расходуется. Дойдя до верхней точки модели, процесс останавливается, платформа с готовым изделием поднимается для очистки от неиспользованного порошка.
В качестве порошка для изготовления изделий селективным лазерным спеканием могут использоваться как однокомпонентные материалы, так и порошковые смеси. По сравнению с другими методами аддитивного производства, селективным лазерным спеканием можно изготавливать детали из относительно широкого диапазона коммерчески доступных порошкообразных материалов. К ним относятся полимеры, такие как нейлон (чистый, стеклонаполненный или с другими наполнителями), полистирол, керамика, стекло, металлы, включая сталь, титан, смеси сплавов, композиционные материалы.
Селективное лазерное спекание используется по всему миру, так как позволяет легко и быстро производить изделия сложной формы на основе цифровых данных.
Первоначально подобным способом создавались прототипы и модели на раннем этапе конструирования, однако сейчас метод широко используется в производстве окончательных продуктов. Сфера применения 3Dпечати методом селективного лазерного спекания обширна: детали силовых установок, авиастроение, машиностроение, космонавтика. В последнее время технология используется для создания предметов искусства и дизайна.
DMLS
DMLS — это аббревиатура от англ. Direct Metal Laser Sintering, что в переводе означает «прямое лазерное спекание металлов». Технологию разработала немецкая компания EOS.
Чтобы смоделировать будущий объект, в качестве чертежей используются 3Dмодели STLформата. При компьютерной обработке модель в виртуальном режиме разделяется на слои в той толщине, которую может осуществить сам 3Dпринтер. В итоге оператор создает файл с определенным набором чертежей для печати.
Нагревательными элементами для спекания являются оптоволоконные лазеры мощностью 200 Вт. Для достижения более высокой производительности можно использовать лазеры с повышенной скоростью лазерного луча.
Готовое изделие, отпечатанное с помощью DMLS 3D-принтера. Впечатляет качество изготовленной детали
Как все работает? Порошкообразный расходник из металла поступает в рабочую камеру в объеме, необходимом для печати одного слоя. Специальный валик разглаживает порошок поровну по всей поверхности, при этом удаляя из камеры излишки. Лазер спекает свежий материал с имеющимся слоем согласно изначальной модели. Этот процесс длится до тех пор, пока печать предмета не будет завершена.
Особенность такого метода — это высокое разрешение печати (до 20 мкм). Что касается бытовых принтеров, то их разрешение достигает 100 мкм. Помимо этого, при печати не нужно создавать опору для нависающих деталей конструкции. Порошок, который не был задействован, остается на рабочей площадке, потому все слои, кроме первого, имеют готовую опорную поверхность.
Для уменьшения необходимой для спекания энергии температура рабочей камеры обычно поддерживается на уровне чуть ниже точки плавления рабочего материала, а для предотвращения окисления процесс проходит в бескислородной среде.
Разумеется, в любой технологии есть свои положительные и негативные стороны. В данном случае преимуществ всё же больше, а именно:
- можно печатать предметы любой геометрической сложности;
- если сравнивать с литьевым методом, то при DMLS предметы получаются легче;
- высокая прочность изготавливаемых предметов;
- дешевизна печати;
- безотходное производство.
Недостатки:
- по сравнению с аналогичными методами скорость печати ниже;
- ограниченное количество 3Dпринтеров, которые поддерживают данный метод.
Технологию прямого лазерного спекания металлов используют для изготовления небольших и среднего размера объектов для стоматологии, медицины, аэрокосмической отрасли. Очень удобно использовать метод для быстрого прототипирования, производства небольших партий товаров или изделий сложной геометрической формы.
Расходными материалами для DMLS могут быть практически любые металлы и сплавы в виде порошка. Среди тех, которые применяются сегодня наиболее часто, — сплавы из кобальта и хрома, нержавейка и пр.
SHS
Selective Heating Sintering (выборочное тепловое спекание) — одна из современных технологий 3Dпечати, в основе которой — плавка слоев термопластика или металлического порошка посредством теплового излучения. Особенность метода заключается в том, что все слои запекаются сразу, так как излучение попадает через специальную маску, которая направляет тепло в те точки, где необходимо закрепить слой.
По сравнению с другими технологиями, в SHS используется не лазер, а тепловое излучение, проходящее через специальную маску: действие лазера заменено на инфракрасное излучение.
Особенность ИКизлучения состоит в том, что человек его не видит, а в зависимости от длины волны излучения свет будет либо отражаться, либо поглощаться. Поэтому для такого метода можно подобрать два вида материалов: первый будет отвечать за пропуск тепла, а второй — за его отражение.
SHS 3D-принтер Blue Printer
Смысл процесса таков: берется пластина из кварцевого стекла, на которую печатается определенная картинка, которая должна соответствовать инвертированному сечению модели. Печать производится не лазером, как в других технологиях, а специальным аппаратом, отражающим излучение.
Эта пластина помещается между рабочей платформой и источником излучения. Части детали, которые не касаются принтинга, пропускают тепло, чем запекают расходный материал, а другие области просто отражают тепло.
Для работы с новым слоем необходимо полностью очистить стекло. Длительность работы с одним слоем — несколько секунд. Для сравнения: лазер запекает один слой около 10 с.
В результате выборочного теплового спекания получается прочное изделие, обладающее хорошими свойствами для последующей работы. Более того, в процессе печати с поверхности деталей удаляются все газы и разные примеси.
Преимущества:
- невысокая стоимость печати;
- наименьшая толщина слоя — 1 мм;
- возможность печати объектов сложной конструкции;
- высокий уровень детализации;
- остатки материала могут использоваться для следующих объектов;
- вариативность устройств для печати.
Недостатки:
- низкая энергоотдача;
- для готовых изделий необходим дополнительный процесс обжига;
- используется один вид расходного материала.
Главный расходный материал выборочного теплового спекания — это термопластичный или металлический порошок. Особенность этого «расходника» — в его структуре: он пористый, поэтому можно изготавливать объекты, где могут меняться физикохимические и механические свойства. Изделия пористой структуры печатаются от однократного спекания, получаются с меньшей тепло и электропроводностью. При каждом следующем спекании изделия будут более прочными.
EBF3
Electron Beam Freeform Fabrication — изготовление изделия произвольной формы в вакууме методом электроннолучевой плавки, где в качестве расходного материала используется проволока из того или иного металла. Осуществляется по аналогии с EBM, а отличие состоит в том, что металл подается в зону электроннолучевого плавления, как было сказано, в виде проволоки, а не порошка.
Данная технология была продемонстрирована на алюминиевых и титановых сплавах, представляющих интерес для аэрокосмического использования. По мнению экспертов, она может быть также распространена на сплавы на основе никеля и железа.
Технология разработана NASA.
Как вариант данной технологии можно упомянуть так называемую EBAM от компании Sciaky. Аббревиатура EBAM означает «Аддитивное производство с использованием электронных пучков». Однако, несмотря на схожесть названия, эта технология не имеет почти ничего общего с EBM или электроннолучевой плавкой от компании Arcam. Дело в том, что метод EBM аналогичен лазерному спеканию и плавке, с той лишь разницей, что для построения изделия применяются электронные пучки вместо лазеров. Но и в том, и в другом случае в качестве расходных материалов используются порошки. В то же время, EBAM в качестве материала служат прутки, применяемые для нанесения последовательных слоев. После каждого прохода печатающей головки остается полоса металла шириной около 10 мм и толщиной 3 мм, но разрешение можно улучшить. Наиболее высоким показателем на данный момент является ширина в 1 мм и толщина в 0,3 мм.
3D-принтер Sciaky’s 110 EBAM metal и готовое изделие
Фирменной особенностью систем Sciaky является возможность создания крупногабаритных моделей из тугоплавких металлов. Технология позволяет наносить до 10 кг металла в час в зависимости от используемого сплава и геометрии конечной модели. Размер изделий ограничивается только размером вакуумных рабочих камер, которые Sciaky сооружает в соответствии с требованиями конкретного заказа. Самые большие агрегаты на сегодняшний день способны производить части размером 7,2×1,5×1,5 м.
Ламинирование
LOM
Laminated Object Manufacturing (LOM) — технология аддитивного производства, использующая листовой тип сырья. Изготовление объектов методом ламинирования подразумевает поэтапное склеивание листов бумаги, пластика или металлической фольги с последующим формированием контура при помощи лазерной резки или режущего инструмента.
Методика LOM была разработана в середине 1980х годов Михаилом Фейгеном. Патент на ее использование получен компанией Helisys, Inc. в 1998м. Однако уже в 2000 году предприятие прекратило существование и его преемником в отрасли стала компания Cubic Technologies.
Болт и гайки, отпечатанные на LOM 3D-принтере SD300 от Cubic
Процесс трехмерного ламинирования мало чем схож с прочими аддитивными методиками. Изготовление объектов методом ламинирования (LOM) происходит следующим образом:
- цифровая 3Dмодель изделия загружается в LOMаппарат;
- лист расходного сырья протягивается с подающего вала разогретым роликом над рабочей платформой;
- лазерный луч вычерчивает контуры слоя;
- обработанный лист опускается;
- новый лист с клейким покрытием поступает в рабочую камеру;
- процедура повторяется, и все последующие слои склеиваются между собой, образуя однородную субстанцию;
- после постройки модели по вычерченному лазером контуру удаляется весь лишний материал;
- механическая постобработка может включать шлифовку, сверление и др.
LOMпечать с помощью лазера всегда сопровождается большим дымовыделением, а также появлением локализованного источника огня. Поэтому для работы потребуется герметичная защита и система дымоотвода.
Из явных достоинств технологии можно отметить общедоступность материалов. При этом изделия, напечатанные при использовании бумажных листов, по физическим характеристикам напоминают древесину, благодаря чему можно проводить соответствующую постобработку.
Разрешение при LOMпечати уступает высокоточным аддитивным методикам вроде стереолитографии (SLA).
Основная сфера применения LOMпринтеров — прототипирование техники и создание архитектурных макетов. Технология также применяется в сферах образования и дизайна, так как позволяет создавать изделия с минимальной себестоимостью.
И все же она более популярна в сфере производства объектов на заказ, чем для персонального или промышленного использования. Это обосновано тем, что при невысокой стоимости сырья сами LOMаппараты гораздо дороже тех же FDMпринтеров.
Если некоторые модели FDMустройств можно приобрести даже меньше чем за 1000 долл., то за LOMпринтеры SD300 от Cubic нужно выложить около 15 000 долл.
Как мы упоминали выше, LOMтехнология — одна из немногих, в которых используется листовое сырье. Для печати пригодны следующие материалы:
- пластики;
- композиты;
- металлическая фольга;
- керамика;
- бумага;
- полимерная пленка.
Точечная подача порошка
DED
Directed Energy Deposition — один из аддитивных процессов, согласно которому строительный материал и энергия для его сплавления подводятся одновременно в место построения изделия.
В начале технологического процесса изготовления создается компьютерная 3Dмодель изделия в САПР.
«Печатная головка» DED 3D-принтера
Специальное программное обеспечение формирует из данной модели множество слоев (сечений), которые параллельны плоскости рабочего стола установки и соответствуют послойному распределению порошка в устройстве. Порошковый материал при помощи специального устройства расстилается тонким слоем порядка нескольких десятков микрон на рабочем столе установки в соответствии с полученной 3Dмоделью. И происходит это фактически одновременно со спеканием. Иными словами, здесь не формируется слой строительного материала, а материал подается в конкретное место, куда в данный момент подводится энергия и где идет процесс формирования детали. Подобно тому, как сварщик вводит материал (электрода) в то место, где за счет электрической дуги формируется зона расплава.
Струйная печать
MJM
Струйная печать в данном контексте может выглядеть многовариантно — через головку может подаваться как материал, так и связующее.
Обычно, когда речь заходит о струйной 3Dпечати, подразумевается технология MJM (Multi Jet Мodeling — метод многоструйного моделирования). Особенность данной технологии — в возможности получения окрашенных и прозрачных моделей, отличающихся механическими свойствами: мягких, как резина, или твердых, как пластик.
MJM 3D-принтер ObJet 1000 и готовое изделие
Впервые о технологии MJM заговорили в компании 3D Systems, которая внедряла ее на основе профессиональных принтеров ProJet. Суть процесса заключается в том, что при многоструйном моделировании изготавливаются качественные модели и прототипы, которые отличает высокая точность. Полученные изделия используются при проведении экспериментов, функциональных тестирований, производстве основных шаблонов в различных сферах. Технология MJM имеет ряд особенностей:
- универсальность, поскольку для создания изделий используются различные расходные материалы;
- возможность производства объемных моделей, которые будут отличаться большой точностью;
- возможность создания объектов со сложной геометрией, при этом толщина слоя минимальна;
- пользоваться принтером может как любитель, так и профессионал;
- разнообразие сфер применения.
Основа технологии многоструйного моделирования — в уникальной печатающей головке. В ней содержатся тонкие сопла в количестве до 448 штук максимум. Принцип действия MJM — послойное нанесение материала на рабочую зону. Количество сопел может варьироваться, от чего зависит подача основного и вспомогательного материалов.
Работа 3Dпринтера ведется на основе воска или фотополимерной смолы. Они распыляются в соответствии с заданным алгоритмом послойно, при этом каждый из них закрепляется ультрафиолетовой лампой. Поддерживающий материал необходим для заполнения пустот, помогая сохранить целостность конструкции печатающегося объекта. После того как моделирование закончилось, поддерживающий материал может быть удален. В некоторых случаях моделирование может выполняться на основе особого прозрачного или полупрозрачного пластика, стойкого к механическим воздействиям и высоким температурам.
При печати в MJMпринтере часто используется медицинский пластик, на основе которого создаются качественные имплантаты. Кстати, в ранних моделях устройств чаще всего применялись обычные термопластики, но благодаря совершенствованию материалов термопластики заменили воском и фотополимерами.
В принтерах ProJet применяются материалы марки VisiJet, которые отличаются различными механическими свойствами. Например, VisiJet DentCast используется в стоматологии при создании коронок, челюстных моделей, протезов, VisiJet X применяется при проектировании сложных технических деталей, а VisiJet Crystal — эластичный и прочный материал, который нужен при создании дизайнмоделей.
По своей сути MJM работает как струйный принтер, при этом позволяет создавать полноценные объекты в трехмерном формате. Они характеризуются отличными физическими свойствами и высоким качеством поверхности.
Технология MJM — это сочетание методов 3Dпечати, струйной трехмерной печати, послойного наплавления и стереолитографии. Если используются вспомогательные восковые структуры, то после того, как печать закончилась, готовую модель помещают в печь, где она нагревается до температуры 60 °С, — пока воск не выплавится.
Если используется фотополимерная печать, то сначала на специальную платформу наносится слой жидкого полимера. Платформа слой за слоем опускается, и формируется сечение модели лазером или ультрафиолетовым излучением.
Преимущества:
- модели получаются высокой или сверхвысокой четкости в зависимости от режима, в котором работает 3Dпринтер;
- толщина слоя — до 16 микрон (клетка крови — 10 микрон);
- высокое качество детализации напечатанного объекта на выходе;
- построение модели выполняется точно и прочно (учитывается прочность на разрыв);
- полное соответствие детали заданным параметрам;
- высокая скорость печати, так как жидкость можно наносить очень быстро;
- наружная поверхность моделей гладкая, а потому простая в обработке.
Единственный недостаток — цена 3Dпринтеров довольно высокая, а дешевые модели подойдут лишь для непрофессионального использования: дорогой пластик, как правило, чувствителен к УФ и достаточно хрупкий.
Технология многоструйного моделирования востребована в тех отраслях, где требуется создание деталей высокого качества и разрешения. Самое широкое применение MJM нашла в стоматологии, ювелирном деле, промышленном и архитектурном дизайне, разработке электронных компонентов.
При создании функциональных моделей для различных тестов используются принтеры марки ProJet. Благодаря этим устройствам получение прототипов и моделей выполняется легко, быстро, экономично с применением пластика — он позволяет получить точные сведения о механических свойствах будущего изделия.
Прототипирование — это возможность корректировки изделий еще на стадии проектирования, что позволяет снизить затраты времени и средств на производство. Дизайнмодель — это уменьшенная копия будущего изделия, которая передает особенности его внешнего вида и оформления. Такие макеты часто используются в учебных целях.
Перспективные разработки
Исследователи из Томского государственного университета разрабатывают технологию 3Dпечати на основе ультразвуковой левитации. В случае успеха акустический 3Dпринтер можно будет использовать для работы с химически агрессивными растворами и разогретыми до высоких температур веществами.
Звуковое поле будет применяться для манипуляции группой частиц с управляемым осаждением в заданные места для построения слоев объемных моделей. Ожидается, что бесконтактная методика позволит использовать в качестве расходников химически агрессивные и тугоплавкие материалы.
Опытный 3Dпринтер планируется создать к 2020 году — после того, как будет отработана методика контролируемой левитации.
Один принтер — одна технология
Если вы осилили текст статьи полностью, то, конечно, поняли, что технологии 3Dпечати настолько радикально отличаются друг от друга, что совместить их в одном устройстве почти невозможно. Мы говорим «почти», оставляя небольшой процент допущения для безумных или гениальных изобретений.
Но сегодня принтеры для трехмерной печати отличаются друг от друга так же, как и технологии, в соответствии с которыми они работают. Если у вас принтер, работающий по SLA, то технологию SLS на нем применить будет невозможно, то есть каждый принтер создан только под определенную технологию печати.
* * *
Как видим, возможности, которые открывает 3Dпечать практически во всех сферах деятельности человека, поистине безграничны.
Принтеры, создающие кулинарные шедевры, воспроизводящие протезы и органы человека, игрушки и наглядные пособия, одежду и обувь — уже не плод воображения писателейфантастов, а реалии современной жизни.
Объемы 3Dпечати настолько велики, что, например, компания Voodoo Manufacturing, которая специализируется на создании промышленных прототипов и управляет минифабрикой из 160 3Dпринтеров в Бруклине, недавно приобрела робота, который позволил предприятию ввести ночную производственную смену без единого сотрудника. То есть работа ведется круглосуточно.
А какие еще горизонты откроются перед человечеством в ближайшие годы — мы пока даже представить себе не можем!