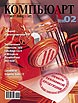
Формирование и регистрация изображения в выводных устройствах
Любое выводное устройство для экспонирования фотоформ или печатных форм имеет некоторую погрешность. Так, растровая точка с относительной площадью 50% в файле может воспроизвестись на пленке или форме с относительной площадью 48 или 52%. Существует система мер, направленных на минимизацию погрешности, вносимой собственно экспонирующим устройством. Эти меры принято называть линеаризацией и калибровкой. После правильно выполненной линеаризации относительная площадь растровой точки на пленке или форме и в файле не должна отличаться более чем на единицу.
Для печати с линиатурой до 300 lpi минимальный размер точки должен быть 10-12 мкм, а до 200 lpi 15-20 мкм. Разрешение экспонирования должно быть согласовано с разрешением фотопленки и формных пластин, а также с настройками формного оборудования и возможностями печатного процесса. Например, даже для качественных формных пластин время экспозиции копировальной рамы настраивается примерно на 12 мкм, то есть более тонкие линии и детали на пластину скопированы не будут.
Большое значение имеет качество растровой точки на фотоформе. Для того чтобы растровая точка была хорошо скопирована на печатную форму и четко напечатана, она должна быть жесткой, то есть неравномерность оптической плотности по ее площади должна быть минимальной. Жесткость растровой точки в значительной степени зависит от метода регулировки размера пятна лазера. В аппаратах с переменной апертурой регулировка размера выполняется изменением диаметра луча D (рис. 1).
Выбор линиатуры определяется возможностями формного и печатного оборудования. Общий принцип достаточно прост: увеличение линиатуры приводит к улучшению внешнего вида полутоновых иллюстраций, но требует более качественного оборудования и большей точности при изготовлении печатных форм и при печати. Для журнальной продукции наиболее распространенной линиатурой является 150, реже 175 lpi. Художественные журналы и альбомы печатаются с линиатурой 175-200 lpi, плакатная продукция 133 lpi, цветные газеты 100-150 lpi.
Получение изображения шрифтовых знаков, штриховых и полутоновых растровых изображений в фотовыводных и некоторых формовыводных устройствах основано на фотографическом действии светового излучения на светочувствительный слой формного материала в процессе экспонирования. При этом под экспонированием понимается воздействие дозированного излучения на регистрирующую среду. Светочувствительный слой черно-белого фотографического материала в основном состоит из взвеси микрокристаллов галогенида серебра в тонкой желатиновой пленке, нанесенной на подложку. Подложка пленочного фотоматериала изготавливается из триацетата целлюлозы или лавсана, а основа формного материала представляет собой электрохимически зерненную и анодированную алюминиевую пластину. Микрокристаллы в слое тем крупнее, чем больше светочувствительность материала. С увеличением размеров микрокристаллов соответственно увеличиваются толщина светочувствительного слоя и масса галогенида серебра, приходящаяся на единицу поверхности материала.
Галогенид серебра является полупроводником, в котором под действием света появляются свободные электроны: по одному на каждый поглощенный квант света. Эти электроны, соединяясь с ионами серебра, имеющимися в междоузлиях кристаллической решетки, образуют атомы серебра. Соединение происходит на небольших дефектах решетки, которые называются центрами светочувствительности. При этом происходит образование скрытого фотографического изображения. Затем фотоматериал подвергают фотохимической обработке проявлению и фиксированию.
Если на центре светочувствительности образовалось более трех атомов серебра, то при погружении слоя в проявитель они катализируют процесс восстановления всего микрокристалла до металлического серебра, то есть эта группа атомов является центром проявления.
После химической обработки светочувствительный слой воспроизводит оптическое изображение в виде некоторого распределения оптической плотности D , которая определяется выражением
где коэффициент пропускания материала (изображения на прозрачной основе) (рис. 2а), характеризующий его способность поглощать световой поток Ф0;
коэффициент отражения (рис. 2б), характеризующий способность материала (изображения на непрозрачной основе) отражать световой поток Ф0; Ф1 и Фp соответственно световой поток, прошедший материал, и световой поток, отраженный от материала.
Оптическая плотность D зависит от экспозиции Н , причем
H=E't,
где E' освещенность изображения, лк; t время экспонирования, с.
Если освещенность E' , создаваемая на светочувствительном слое, меняется со временем, то экспозиция определяется выражением
где t1 и t2 моменты времени, соответствующие началу и окончанию экспонирования.
Зависимость оптической плотности D от экспозиции для данного светочувствительного слоя выражается характеристической кривой (рис. 3), представляющей собой график зависимости D = f(lgH) . Каждая характеристическая кривая выражает свойства конкретного фотоматериала. Ее положение относительно начала координат, угол наклона, крутизна отдельных участков для различных фотоматериалов могут меняться.
Оптическая плотность D0 химически обработанного светочувствительного слоя, не подвергаемого воздействию света, называется оптической плотностью вуали.
Светочувствительность слоя определяется в единицах ГОСТа по формуле
.
Таким образом, светочувствительность слоя есть величина, обратная экспозиции Н1, при которой оптическая плотность D1 фотографического изображения превышает плотность вуали D0 на 0,85 (точка В на характеристической кривой). Участок АВ характеристической кривой называется областью недодержек, ВГ прямолинейным участком характеристической кривой, участок за точкой Г является областью передержек.
Тангенс угла наклона прямолинейного участка характеристической кривой называется коэффициентом контрастности
:
На практике иногда удобнее пользоваться уравнением прямолинейного участка характеристической кривой в виде
где Hi экспозиция, соответствующая точке инерции (точка пересечения продолжения прямолинейного участка с осью абсцисс).
Световой поток, несущий элемент изображения, проходит оптическую систему и попадает на светочувствительный слой. Оптическая плотность изображения на этом слое после его проявления будет тем больше, чем больше экспозиция. Значение экспозиции (лк·с) Hтр , требуемое для создания изображения с заданной оптической плотностью Dиз , может быть определено аналитически
или графически по характеристической кривой фотоматериала.
Как всякая система регистрации и передачи информации, светочувствительный слой воспроизводит информацию с искажениями. Возникают три основных вида искажений:
• искажения тональной передачи, выражающиеся в том, что почернения в фотографическом изображении непропорциональны количеству света, действовавшему на слой;
• потери резкости, выражающиеся в утрате четкости деталей, содержащихся в оптическом изображении;
• шумовые искажения, проявляющиеся в возникновении в фотографическом изображении случайной структуры так называемой зернистости.
Все три вида искажений, в общем, обусловлены одной и той же причиной: дискретным строением светочувствительного слоя и связанным с этим механизмом образования фотографического изображения.
Потери резкости изображения вызваны рассеянием света в светочувствительном слое. Рассеяние света в слое обусловлено его дифракцией и отражением на эмульсионных микрокристаллах. Какой из процессов преобладает, зависит от размеров микрокристаллов. В слоях с микрокристаллами, имеющими поперечный размер больше длины волны света, определяющим является отражение, а в мелкозернистых слоях дифракция.
Рассеяние света в эмульсионном слое зависит не только от собственно светорассеяния, но и от степени поглощения актиничного света слоем. Поглощение же зависит в первую очередь от количества микрокристаллов в единице объема и их общей массы.
Количество рассеянного света в единице объема изменяется с глубиной слоя. Непосредственно у поверхности количество рассеянного света минимально, затем быстро возрастает до максимального значения и далее снова уменьшается. Максимум возникает из-за отражения света в обратную сторону от микрокристаллов, лежащих в глубине слоя, и отражения света от поверхности раздела «эмульсионный слой воздух». Уменьшение количества рассеянного света с глубиной результат поглощения света в слое.
Таким образом, рассеяние света в фотографическом слое зависит от большого числа причин, взаимодействующих между собой: размеров и формы микрокристаллов, коэффициентов преломления и спектральных свойств образующих светочувствительный слой веществ и их концентрации в слое.
В обычных фотоматериалах с разрешающей способностью R =150-200 мм-1 световой квант, попавший на светочувствительный слой, из-за рассеяния поглощается порой на весьма значительном расстоянии от места попадания на эмульсионный слой. Однако на высокоразрешающих ( R >400 мм-1) слоях, к которым относятся практически все фототехнические пленки, дело обстоит значительно лучше. Эмульсионный слой этих пленок очень тонок и прозрачен. Поэтому большая доля регистрируемого слоем светового потока не рассеивается. Значительная часть почернения строится теми световыми квантами, которые поглотились микрокристаллами.
В современных выводных устройствах для записи изображения на светочувствительные материалы используются газовые, твердотельные и полупроводниковые лазеры (лазерные диоды). В качестве газовых лазеров применяются аргонионные (Ar+) и гелий-неоновые (Не-Ne), которые имеют достаточно короткую длину волны 488 и 633 нм соответственно. Газовые лазеры с непрерывным излучением дают пучок излучения с гауссовым профилем интенсивности в любом сечении вдоль направления луча. Этот пучок обладает высокой направленностью и сохраняет свои свойства при прохождении через элементы фокусирующей оптики, то есть распределение интенсивности света в любом поперечном сечении пучка может быть описано выражением типа
где r координата радиуса поперечного сечения пучка; K коэффициент ослабления уровня мощности излучения на поверхности фоторецептора (0 < K < 1); ? параметр, определяющий меру ширины гауссова распределения. Принято считать, что значение ? равно половине радиуса сечения гауссова пучка, на котором мощность излучения падает в e2 раз.
Преобразованный оптической системой лазерный луч имеет в области фокусировки вид гиперболоида вращения с диаметром d0 перетяжки (шейки) пучка, определяемой соотношением
где длина волны излучения лазера; f фокусное расстояние объектива; D ширина лазерного пучка, входящего в фокусирующий объектив.
Картина изменения распределения амплитуды гауссова пучка при его распространении в однородной среде представлена на рис. 4.
Перетяжка может характеризоваться и продольным распределением b , в пределах которого диаметр пучка изменяется незначительно:
где D диаметр гауссова пучка на входе в оптическую систему.
Параметр b можно рассматривать как глубину фокусировки или глубину резкости фокусирующей системы, при которой относительная величина допустимого изменения диаметра пучка определяется значением .
.
Из полупроводниковых лазеров в современных выводных устройствах применяются лазерные диоды инфракрасного и видимого красного излучения (длина волны соответственно 780 и 670-680 нм). Из твердотельных лазеров используют неодимовый лазер на иттрий-алюминиевом гранате с удвоенной частотой FD Nd-YAG с длиной волны 532 нм. Чем меньше длина волны, тем более четкое пятно (точку) на светочувствительном материале можно получить при записи. Такие точки изображения, у которых оптическая плотность на краях очень резко изменяется от максимального до минимального значения, называют жесткими, а точки с более плавным изменением оптической плотности на краях мягкими (рис. 5). В связи с тем что растровая точка изображения формируется из некоторого количества мягких или жестких микроточек (рис. 6), понятие жесткости применимо и для растровых точек (рис. 7).
При записи изображения с невысокими линиатурами растра (133, 150 lpi) влияние жесткости точки практически неуловимо, а с учетом погрешностей собственно печатного процесса и вовсе исчезает. Для печати при высокой линиатуре «жесткость» луча начинает играть принципиальную роль, так как для достижения таких линиатур требуется адекватное уменьшение диаметра сканирующего лазерного пятна.
Для определения мощности лазерного излучения, необходимой для работы выводного устройства, экспонирующего светочувствительный фотографический или формный материал, проводят светоэнергетический расчет. При определении мощности лазера следует учитывать линейную скорость сканирования изображения и параметры оптической системы, которые характеризуют световые потери на отражение на преломляющих поверхностях, на поглощение и рассеяние внутри массы стекла.
Большинство современных выводных устройств, предназначенных для работы со светочувствительными материалами, могут осуществлять запись изображения на печатные формы.
Технология регистрации изображения на современных светочувствительных пластинах для офсетной печати подразделяется на два основных типа: фотополимеризация и внутренний диффузионный перенос серебра.
Фотополимерные пластины (например, пластины N91 фирмы Agfa), структура которых представлена на рис. 8, обеспечивают получение 2-98% точки при 175 lpi, тиражестойкость 300 тыс. оттисков без обжига формы, а их светочувствительность составляет от 180 до 240 мкДж/см2.
Технологический процесс получения изображения на фотополимерной пластине состоит из четырех основных операций (рис. 9): а экспонирования; б термообработки; предварительной промывки; г проявления. При экспонировании лазером с длиной волны 488, 633 или 532 нм происходит сшивание полимера на участках формирования изображения. При термообработке в результате кратковременного нагревания усиливается процесс полимеризации и обеспечивается полная потеря способности участков изображения растворяться в проявителе. Во время предварительной промывки удаляется защитное покрытие. В процессе проявления удаляются все неэкспонированные участки и остаются только элементы изображения. После этого пластина готова к окончательной промывке и нанесению защитного покрытия.
В формных пластинах офсетной печати, содержащих галогенсеребряные слои, на бумажной, полимерной или металлической подложке после экспонирования и химической обработки на поверхности слоя образуются печатающие и пробельные элементы. Полученные офсетные печатные формы на бумажной основе выдерживают тиражи до 5 тыс. экземпляров, однако из-за пластической деформации увлажненной бумажной основы в зоне контакта формного и офсетного цилиндров штриховые элементы и растровые точки сюжета искажаются, поэтому бумажные формы могут быть использованы только для однокрасочной печати. Формы на полимерной основе, например полиэстровой, имеют максимальную тиражестойкость до 20 тыс. оттисков хорошего качества с линиатурой до 175 lpi и градационным диапазоном 3-97%.
Основой технологии является полиэстровый рулонный светочувствительный материал, работающий на основе принципа внутреннего диффузионного переноса серебра. На рис. 10 представлена структура полиэстровых форм. В процессе экспонирования происходит засветка галогенида серебра. При химической обработке осуществляется диффузионный перенос серебра из незасвеченных областей в верхний слой, в дальнейшем восприимчивый к краске. Этот технологический процесс требует негативного экспонирования. Формные пластины на металлической подложке содержат чувствительный к определенному участку спектра серебросодержащий слой, под которым находится слой физического проявления. Основанием служит алюминиевая пластина.
Попадание света на слой галогенида серебра вызывает диффузию серебра в слой физического проявления, что приводит к созданию на алюминиевой поверхности пластины изображения. После проявления такое изображение становится олеофильным способным удерживать печатные краски). При этом остальные области становятся гидрофильными, то есть не восприимчивыми к печатным краскам, но восприимчивыми к увлажняющему раствору.
Серебросодержащий слой очень чувствителен, поэтому пластины этого типа экспонируются быстрее, чем фотополимерные или термальные, причем растровая точка воспроизводится точно в диапазоне от 1 до 99%.
Пластины имеют широкий диапазон чувствительности и могут экспонироваться как аргонионным лазером (длина волны 488 нм), так и FD YAG-лазером (длина волны 532 нм). Пластины этого типа могут выпускаться и в версии, чувствительной к красному свету, для экспонирования лазерным диодом с длиной волны 670 нм. Обычно тиражестойкость серебросодержащих пластин составляет около 250 тыс. оттисков.
В последние годы все большее применение находят пластины, светочувствительные к фиолетовой области спектра излучения (400-430 нм). Структура пластин Lithostar Ultra V фирмы Agfa приведена на рис. 11.
Последовательность обработки пластин Lithostar Ultra следующая. В процессе экспонирования луч фиолетового лазера активизирует серебросодержащие частицы на пробельных элементах. Незасвеченные участки после обработки проявителем формируют печатающие элементы. Во время проявления серебросодержащие частицы активизируются, при этом у них возникают устойчивые связи с желатином. Частицы, которые не были засвечены, остаются подвижными и способными к диффузии. На следующей стадии не подвергшиеся засветке ионы серебра диффундируют из эмульсионного слоя через барьерный слой на поверхность алюминиевой основы, формируя на нем печатающие элементы. После того как изображение полностью сформировано, желатиновая фракция эмульсии и растворимый в воде барьерный слой полностью удаляются во время смывки, оставляя на алюминиевой основе только печатные элементы в виде осажденного серебра.
Эти пластины обеспечивают получение 2-98% точки при 250 lpi, их тиражестойкость находится в диапазоне от 200 тыс. до 350 тыс. отт. Энергия лазера, необходимая для засветки, находится в интервале от 1,4 до 3 мкДж/см2.
Регистрация изображения на термочувствительных материалах в выводных устройствах осуществляется под действием инфракрасного лазера, который используется в качестве источника теплового воздействия, способного не только нагреть вещество до любой требуемой температуры, но и даже расплавить и испарить. Установлено, что длительность процессов передачи энергии при тепловом воздействии лазерного излучения лежит в диапазоне 10-11 …10-8 с. В процессах записи изображения в выводных устройствах при допустимой неточности воспроизведения краев штриховых изображений 5-10 мкм максимальная длительность нарастания и спада температуры нагрева на краях штрихов должна иметь порядок 10-7 с. Следовательно, минимальное значение времени, требуемого для нагрева материала лазерным излучением и обеспечения качественной записи, по крайней мере на порядок больше характерного времени обмена энергией между лазерным излучением и обрабатываемым материалом.
Таким образом, при расчетах результатов теплового воздействия лазерного излучения на вещество в процессе регистрации изображения можно считать, что при падении на вещество это излучение мгновенно выделяет в нем теплоту, образуя внутренний источник энергии, характер которого зависит от прозрачности вещества. При прохождении излучения через прозрачное вещество не происходит выделения тепловой энергии, если не считать потерь на локальных неоднородностях, снижающих лучевую стойкость материала и определяющих качество оптических материалов.
При падении излучения на непрозрачное вещество некоторая часть энергии этого излучения отражается от поверхности материала, а остальная часть выделяется в виде теплоты в слое, толщина которого зависит от степени поглощения излучения данным веществом. При малой скорости поглощения излучения вещество является полупрозрачным, теплота выделяется в нем в объеме, пронизываемом лазерным лучом, и распространяется от этого объема в стороны за счет теплопроводности. При значительной скорости поглощения излучения его воздействие приводит к поверхностному нагреву материала с распространением его в толщу по экспоненциальному закону.
Во всех случаях важно оценить, какая часть энергии излучения отражается от облучаемой поверхности, а какая поглощается в виде теплоты. Установлено, что при облучении неметаллов этот факт не имеет практического значения, если лазерное излучение направляется примерно перпендикулярно к поверхности материала. В таком случае подавляющая часть энергии излучения поглощается и только небольшая ее часть (порядка 10%) отражается. При падении лазерного излучения под небольшим углом к поверхности коэффициент отражения заметно возрастает, но этот случай обычно не имеет практического значения в реальных процессах нагрева веществ лазерным излучением. Таким образом, можно считать, что при нагреве неметаллических материалов лазерным излучением почти вся энергия этого излучения расходуется на нагрев материала.
Значение коэффициента отражения излучения от металлической поверхности очень сильно зависит от длины волны излучения. Минимальные отражения характерны для ультрафиолетовой области спектра. При переходе в инфракрасную область коэффициент отражения практически для всех металлов достигает 90% и более. Поэтому использовать для нагрева металлов излучение лазеров на углекислом газе с длиной волны около 10 мкм экономически нецелесообразно, несмотря на то что эти лазеры характеризуются относительно большим значением коэффициента полезного действия.
При нагреве материалов различают следующие степени их нагрева:
• умеренный нагрев до наступления относительно энергоемких физико-химических превращений вещества (фазовые переходы, химические реакции, полимеризация, разрушение структурных связей и т.д.);
• плавление;
• разрушение (абляция) вещества (главным образом испарение).
В современных выводных устройствах можно получать изображения на термочувствительных материалах на пленках для дальнейшего изготовления печатных форм методом контактного копирования, и непосредственно на печатной пластине.
В первом случае использовались так называемые сухие пленки, не требующие традиционной мокрой химической обработки после экспонирования. Для этой технологии применялись специальные, иногда достаточно сложные материалы и фотовыводные устройства с повышенной мощностью лазера. На рис. 12 представлены схемы различных технологических процессов записи изображения на сухих пленках.
В первом процессе (рис. 12а) на основу пленки нанесен слой красителя специального состава. Для работы с этой пленкой используется экспонирующее устройство с лазерным лучом высокой мощности. Во время экспонирования луч лазера испаряет краситель с поверхности пленки. В негативном режиме очищаются участки, занимаемые изображением, в позитивном участки без изображения. На участках, не обрабатываемых лазерным лучом, оптическая плотность остается высокой. После того как экспонирование изображения закончено, никакой дальнейшей обработки уже не требуется пленка готова для изготовления форм.
Изображение, полученное вышеописанным способом, очень четкое и имеет резкую границу.
Принцип, на основе которого функционирует второй процесс (рис. 12б) заключается в следующем. Между двумя листами носителем и основой нанесен тончайший (толщиной менее 1 мкм) непрозрачный слой угольных частичек. Под действием лазерного луча повышенной мощности частицы переходят с листа-носителя на лист-основу. Затем два листа необходимо механически разделить.
Изображение, полученное на пленке, также требует повышенной по сравнению с обычным ФНА мощности лазера и отличается очень высоким разрешением и четким контуром растровой точки. Другим важным достоинством является то, что пленка сравнима по своим оптическим параметрам с традиционными серебросодержащими фотопленками и может быть использована в любой комбинации на одном монтажном листе.
В основе третьего процесса лежит электрофотографический принцип получения изображения. В этом случае пленка состоит из трех слоев: майларовой основы, проводящего промежуточного слоя и слоя термопластика. В термопластике содержатся микрочастицы селена, который является именно тем ингредиентом, благодаря которому работает материал. Пленка не светочувствительна до тех пор, пока ее не зарядят в специально предназначенном для этого коротроне. Частицы селена будут удерживать статический заряд до тех пор, пока пленка не будет обработана лазером выводного устройства.
После экспозиции пленка как бы проявляется нагреванием приблизительно до 100 °С. Во время нагрева термопластик размягчается и засвеченные лазером селеновые частицы смещаются в нем по направлению к проводящему слою. Перемещаясь через нагретый термопластик, частицы селена становятся случайно ориентированными. Это увеличивает рассеивающий и поглощающий факторы селена и, как следствие, увеличивает оптическую плотность пленки. Селен в областях пленки, не обработанных лазерным лучом фотонаборного устройства, никуда не смещается, а следовательно, эти области остаются относительно прозрачными после нагрева.
Основной недостаток такой пленки заключается в том, что участки пленки с низкой оптической плотностью кажутся достаточно темными по сравнению с аналогичными участками на обычной фотопленке, то есть пленка внешне не похожа на фотопленку. Разность в плотностях между участками с изображением и без него составляет чуть более 2,0 (у обычной пленки 3,0-4,0), что достаточно в случае изготовления форм для некоторых видов печатных работ.
Поскольку материалы экспонируются при помощи инфракрасного лазера, они не чувствительны к дневному свету и для работы не требуется затемненное помещение.
В формных пластинах с термослоями печатающие и пробельные элементы формируются под действием лазерного инфракрасного излучения с длиной волны 830 нм и выше. При этом печатающие и пробельные элементы печатной формы могут формироваться по принципу непосредственного теплового воздействия на термослой, в котором экспонированные участки переходят из гидрофильного в гидрофобное состояние либо по принципу диффузионного переноса изображения в многослойных структурах, либо по принципу двойного слоя, при котором после воздействия ИК-излучения печатающие и пробельные элементы формируются в разных слоях, образуя микрорельеф изображения. Термопластины нечувствительны к дневному свету, а их разрешающая способность может обеспечить запись изображения с линиатурой до 330 lpi, что соответствует получению однопроцентной точки размером 4,8 мкм. При этом тиражестойкость полученных печатных форм достигает 250 тыс. экземпляров без обжига и 1 млн. экземпляров с обжигом.
Процесс обработки этих пластин (рис. 13) после экспонирования состоит из трех ступеней:
1. Предварительный обжиг . Поверхность формы подвергается обжигу примерно в течение 30 с при температуре 130-145 °С. Этот процесс укрепляет печатающие (чтобы они не смогли раствориться в проявителе) и размягчает пробельные элементы. Предварительный обжиг является обязательной операцией. После предварительного обжига, перед тем как попасть в проявочный процессор, пластина проходит через охлаждающий конвейер.
2. Проявление . Стандартный позитивный проявочный процесс: погружение, обработка щетками, фильтрация и рециркуляция, гуммирование и, наконец, форсированная воздушная сушка.
3. Обжиг . После обработки пластина подвергается обжигу в течение 2,5 мин при температуре от 200 до 220°С, чтобы обеспечить ее прочность и большую тиражестойкость.
В настоящее время на российском рынке представлен широкий ассортимент термочувствительных пластин, в том числе и пластин нового поколения, которые не требуют предварительного нагрева для обработки. К ним относятся следующие пластины: Lastra LT-2, Fuji LH-PIE, Kodak Electra Excel, Agfa Thermostar. В большинстве своем они обеспечивают получение 1-99% точки при линиатуре растра 200 lpi, тиражестойкость 150 тыс. оттисков без обжига, а светочувствительность у них различается, находясь в интервале от 110 до 200 мДж/см2.
Для получения высококачественной печатной продукции основополагающее значение имеет растрирование полутоновых иллюстраций и растровых полей. В цифровой допечатной технологии растровая точка создается при помощи вычислений по различным формулам в программе. Физически же в CtP-технологии растровая точка впервые появляется только на формной пластине и создает основу для результата процесса печати. Если растровая точка подвержена отклонениям и в процессе печати нельзя сохранить ее физическое увеличение или ясно определить ограничения по краске и увлажнению, то эти отклонения будут усиливаться в ходе печатного процесса. Искаженное представление растровой точки, а именно то, какой она получается на форме и какой она воспроизводится на печатном оттиске, называют растискиванием. Растискивание является главной причиной отклонения процесса печати от нормального хода и ухудшения качества продукции.
Процессы изготовления печатных форм на термочувствительных пластинах основаны на лазерной обработке тонких пленок, покрывающих поверхность формного материала. В качестве покрытий используются полимеры или металлы.
Лазерная обработка тонкой пленки производится следующим образом:
• короткие импульсы лазерного излучения фокусируются на поверхности пленки;
• энергия поглощается пленкой;
• в результате поглощения пленка нагревается, плавится и/или испаряется;
• за счет поверхностного натяжения удаляется вещество;
• происходит отвод тепла главным образом из-за теплопроводности подложки.
Приняв два упрощающих предположения, можно получить в аналитическом виде решение, выражающее увеличение температуры пленки как функцию времени, прошедшего после начала поглощения излучения. Эти предположения, уменьшая сложность конечного результата, физически хорошо обоснованы и справедливы в большинстве представляющих практический интерес случаев. Во-первых, предполагается, что толщина пленки и ее температуропроводность таковы, что температура во всех точках пленки одинакова в любой момент времени данного процесса. Во-вторых, считается, что радиальными потоками тепла как в пленке, так и в подложке можно пренебречь. Это позволяет считать задачу переноса тепла одномерной. Энергия, переданная подложке, пренебрежимо мала, поэтому подложка никак не влияет на температуру пленки.
При определении мощности потока лазерного излучения, падающего на формный материал, необходимо учесть коэффициент отражения, который показывает, какая часть падающего излучения отражается от поверхности и не участвует в ее нагреве.
Для удаления полимерных или металлических тонких покрытий с формного материала при изготовлении форм офсетной или высокой печати применяются лазеры, мощность которых составляет 15-20 Вт.