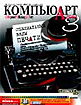
Структурно-механические свойства бумаги
Формирование структурно-механических свойств бумаги начинается задолго до образования влажного бумажного полотна на сеточной части бумагоделательной машины и его сушки на сушильных цилиндрах. В основе бумажного листа лежит сетчатая структура, состоящая из единичных волокон, соединенных межволоконными связями. Единичное волокно является основным элементом — «атомом» бумаги, имеющим сложные структуру и химический состав.
В.В. Левшина и А.В. Бывшев — ученые из Сибирского государственного технологического университета (Красноярск, Россия) — обобщили но-вые подходы к формированию структурно-механических свойств бумаги, основанные на изучении системы «армирующий компонент — наполнитель». Ими представлено математическое описание прочности единичного целлюлозного волокна, проанализированы значение прочности связи волокна в листе и их изменение под воздействием процесса размола. Определена длина волокон, являющихся армирующим компонентом бумажного полотна.
Известно, что целлюлозное волокно можно сравнить с армированным бетоном, в котором фибриллы являются прочными стрежнями, а лигнин — прочным на сжатие наполнителем. Отсюда следует, что прочность волокон определяется структурой и ориентацией фибрилл, а химический состав волокна на нее (прочность) не влияет. Выдвинутая Левшиной и Бывшевым гипотеза получила экспериментальное подтверждение в проведенных исследованиях: прочность волокна может быть описана как функция степени упорядоченности целлюлозы и угла наклона фибрилл в слое S2.
Прочность единичного волокна прежде всего формируется за счет морфологических особенностей древесины и претерпевает значительные изменения в процессах делигнификации и отбелки, которые более всего влияют на молекулярную и надмолекулярную структуру волокна.
Учеными было установлено, что размол целлюлозы уже на первой стадии разрушает более слабые ранние волокна, упрочняя при этом армирующий компонент бумажного полотна.
Прочность единичного волокна не изменяется в процессе размола до появления дефектов в слое S2, что происходит при достижении степени помола 60–70°ШР. Это — экспериментальное подтверждение известной трактовки изменения значений разрывной длины в зависимости от степени помола, которая гласит:
«Разрывная длина быстро растет в первой стадии размола, достигает максимума при степени помола 60–70°ШР, а затем начинает снижаться. Точка перегиба достигается тогда, когда дальнейшее развитие сил связи уже не может компенсировать падение прочности за счет снижения средней длины волокна в бумаге и снижения прочности самого волокна, ослабленного размолом».
Однако следует отметить, что до 60–70°ШР возрастают прочность армирующих волокон и их вклад в механизм разрыва бумаги, а уже после данной точки в армирующих волокнах появляются дефекты и их прочность снижается. То есть, как показали исследования, до 60–70°ШР разрывная длина увеличивается не только вследствие возрастания числа межволоконных связей, но и за счет увеличения прочности и числа армирующих волокон.
Межволоконные связи являются важнейшим фактором, формирующим структурно-механические свойства бумаги. Установлено, что в бумажном листе из неразмолотых волокон силы связи между ними на 80% обусловлены силами трения и Ван-дер-Ваальса, 20% — водородными; из размолотых — в среднем 40 и 60% соответственно. Известно, что водородные силы связи возникают при сближении свободных гидроксильных групп, находящихся на поверхности целлюлозы. Как показали исследования, прессование влажных отливок бумаги приводит к увеличению ее объемной массы и при этом пропорционально ей увеличивается прочность связи единичного волокна в листе вследствие уплотнения структуры листа.
Величина водородных сил связи зависит от числа свободных гидроксильных групп, которая увеличивается по мере раскрытия внешней поверхности волокна. Поэтому на прочность связи волокна в листе оказывает влияние величина внешней поверхности целлюлозы. Это видно на примере размола сульфатной и сульфитной целлюлозы в ролле Валлея и дисковой мельнице (рис. 1–2). В проведенных исследованиях внешняя поверхность волокна косвенно характеризовалась степенью поврежденности наружных слоев клеточной стенки.
Для сульфитной и сульфатной целлюлоз значение этого показателя изменяется в зависимости от степени ее помола примерно одинаково и отличается при размоле на различном размалывающем оборудовании: ролле или дисковой мельнице.
Прочность связи волокна в листе определяется отношением силы связи волокна к его боковой поверхности. Боковая поверхность является функцией его диаметра и длины, но поскольку диаметр намного меньше длины, то им можно пренебречь и говорить о преобладающем воздействии последней. Но в связи с тем, что в процессе размола длина волокон снижается, особенно для сульфитной целлюлозы, размолотой в дисковой мельнице, прочность связи волокна в листе может замедлять свой рост при увеличении степени помола целлюлозы (см. рис. 1).
На величину прочности связи волокна в листе оказывает влияние взаимодействие, которое возникает в системе «армирующий компонент —наполнитель». Известно, что наполнитель — это короткие волокна с хорошо развитой внешней поверхностью. Установлено, что для беленых целлюлоз армирующий компонент, который представлен длинными волокнами, не требует воздействия процесса размола при получении массовых видов бумаг, так как поверхность этих волокон имеет достаточную величину и раскрыта уже под действием варочного и отбельного процессов. При получении бумаги из небеленой целлюлозы армирующему компоненту необходим размол (до 20°ШР) с целью дополнительного увеличения внешней поверхности и гибкости волокон, так как в противном случае физико-механические показатели бумаги будут иметь значение, несоответствующее стандарту. В качестве армирующего компонента предпочтительнее целлюлоза хвойных пород, состоящая из длинных волокон. Лучшим наполнителем является целлюлоза лиственных пород, но может быть использована и целлюлоза хвойных, подвергнутая размолу с доминирующим рубящим воздействием.
С помощью разработанной учеными модели бумажного листа получены результаты, подтверждающие данные Д. Ван ден Аккера: для неразмолотой целлюлозы в зоне разрыва листа разрывается 1/3 волокон , а для размолотой — 3/4. Проведенная количественная оценка вклада прочности волокон в прочность бумажного листа доказывает важность прочности волокон для физико-механических свойств бумаги. Следовательно, при выборе волокнистого материала для получения бумаги требуемого уровня качества необходимо обращать внимание на величину этого показателя и факторы, его формирующие.
При изучении механизма разрыва бумаги возникает вопрос: если мы считаем, что она является композиционным материалом, то какие волокна считать наполнителем, а какие армирующим компонентом? При апробации модели бумаги испытатели принимали, что процентное содержание армирующих волокон от общего числа волокон в модели равно процентному содержанию разорванных волокон. Успешная апробация модели может служить подтверждением этого предположения. Поэтому, опираясь на полученные результаты по изменению длины волокон при размоле целлюлозы, было решено углубить изучение этого вопроса.
Изменение фракционного состава по длине волокон для сульфитной и сульфатной целлюлоз представлено на рис. 3, из которого видно возрастание в процессе размола мелкой фракции (волокна длиной менее 1 мм) и одновременное снижение крупной фракции (свыше 3 мм). Процесс перераспределения волокон по длине по мере роста степени помола можно также изучить с помощью гистограмм.
В результате для всех исследуемых образцов была определена длина армирующих волокон, минимальное значение которой примерно равно средней длине волокон (см. табл.). Было также установлено, какая фракция по длине волокон будет служить армирующим компонентом. Как видно из таблицы, армирующим компонентом в листе бумаги являются волокна, длина которых в основном больше их средней длины. Они представлены в большей мере волокнами крупной и средней фракции, реже (свыше 50°ШР) — частью мелкой.
Здесь требуют объяснения противоречия, возникающие при сопоставлении вышеизложенных положений с расчетами критической длины. Учеными было определено, что при растяжении могут разрываться волокна, длина которых больше критической. Ее величина изменяется от 1,3 до 0,4 мм для сульфатной целлюлозы и от 0,6 до 0,2 мм — для сульфитной и в основном значительно ниже, чем минимальная длина армирующих волокон. Армирующий компонент — это волокна, которые вносят вклад в усилие разрыва бумаги, то есть вырываются или разрываются. На месте разрыва бумаги видна «бахрома» достаточно длинных волокон и прилипших к ней коротких волокон.
Следовательно, можно предположить, что мелкие волокна (наполнитель), обволакивающие армирующие, вряд ли сами смогут участвовать в разрыве, а вырвутся или разорвутся вместе с длинными волокнами.
Обобщая вышеизложенное, можно утверждать, что в листе бумаги из неразмолотых волокон число армирующих волокон мало' (30%). Это длинные волокна, являющиеся крупной и средней фракциями. Наполнитель представлен частью средней и малочисленной мелкой фракцией. Его волокна имеют слабо развитую поверхность и не создают сомкнутую структуру, поэтому снижается вероятность образования большого числа контактов между ним и армирующим компонентом. Бумажный лист из размолотых волокон состоит из более прочных армирующих волокон, так как из его состава под действием размола удалены более слабые ранние волокна. Но длина армирующих волокон уменьшилась вследствие их рубки. Наполнитель представлен хорошо фибриллированными многочисленными короткими волокнами, образующими сомкнутую структуру с армирующими волокнами. Это приводит к увеличению числа волокон, участвующих в процессе разрыва бумаги в качестве арматуры.
Представленные результаты позволяют расширить представления о формировании структурно-механических свойств бумаги в процессе ее производства и могут найти применение при выборе технологических параметров, оборудования и исходного сырья с целью управления качеством продукции.
КомпьюАрт 3'2001