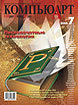
Пластины для CtP: основные типы, проблемы выбора и использования
Основные типы пластины для CtP
Сравнение процессов изготовления пластин разных типов
Из российского опыта внедрения CtP
В последние годы прогресс в области электроники и оптики привел к появлению экспонирующих устройств, управляемых по всем параметрам и учитывающих все особенности формного материала. Последующая химическая обработка пластин при правильном выборе обрабатывающей машины, режимов и химических компонентов также способствует полной реализации заложенных в конкретную технологию возможностей. Безусловно, каждая разновидность технологии прямого экспонирования форм имеет свои преимущества и недостатки, которые будут существенными для одних клиентов, но мало повлияют на результаты деятельности других.
В этой статье мы рассмотрим самые распространенные разновидности пластин и расскажем о связанных с ними особенностях производства печатных форм.
Основные типы пластины для CtP
Фотополимерные пластины
Фотополимерные пластины для CtP появились на рынке одними из первых. Экспонированные лазером участ-ки этих пластин полимеризуются, образуя после дополнительного нагрева структуры, не растворимые в проявляющих растворах; остатки неполимеризованного слоя удаляются в проявочной машине. Процесс изготовления форм с использованием фотополимерных пластин прост, надежен и позволяет довольно быстро получать печатные формы, однако следует учитывать два существенных недостатка низкое разрешение и невысокую стойкость неэкспонированных пластин к царапинам.
Причиной низкого разрешения является необходимость полимеризации светочувствительного слоя по всей толщине иначе он будет смыт проявителем из-за отсутствия контакта с алюминиевой основой. К тому же процесс полимеризации экспонированного участка идет не только вниз от засвеченных лазером центров полимеризации в верхней части слоя до подложки, но и в стороны, увеличивая размеры растровой точки.
Причиной второго свойства является склонность светочувствительного слоя полимеризоваться не только под воздействием излучения с той или иной длиной волны, но и в результате окисления атмосферным кислородом. Для защиты от окисления слой печатающих элементов покрывается тонкой пленкой водорастворимого материала, которая должна быть достаточно толстой для защиты от кислорода и в то же время прозрачной для минимизации потерь экспонирующего излучения.
Сегодня во всем мире фотополимерные пластины применяются в основном в газетном производстве, где не предъявляется высоких требований к разрешению, но должны обеспечиваться скорость и надежность процесса. Поскольку в газетных экспонирующих устройствах используется автоматическая загрузка пластин, то проблемы появления царапин из-за неаккуратного обращения оператора с материалом устраняются.
В России фотополимерные пластины тоже используются в основном для производства форм в газетном производстве. Оборудование CtP для экспонирования фотополимерных форм установлено в новых типографиях, при проектировании которых уже учтены требования к технологии помещения хорошо изолированы от света, при отделке не применяются пылящие в процессе работы материалы, а владельцы типографий заранее обучают персонал работе на новом оборудовании. В результате запуск машин, как и всего технологического процесса, на всех известных автору отечественных предприятиях проходит довольно гладко.
Термальные пластины
Хотя термальная технология, основанная на локальном тепловом воздей-ствии на материал, является, пожалуй, самой новой среди прочих технологий прямого изготовления форм, но в настоящее время именно эта разновидность технологии CtP получила наи-большее распространение. И это подтверждается не только обширным парком установленных машин, но и наибольшим числом производителей формных материалов.
Суть технологии, используемой в пластинах Agfa Thermostar, заключается в травлении щелочным проявителем печатного слоя через маску, выжженную мощным ИК-лазером. Проявитель сходен по составу, а иногда и вообще аналогичен используемому при обработке традиционных офсетных пластин. Среди достоинств термальной технологии возможность использования проявочной машины и проявителя для обычных пластин, удобство обращения с материалом при дневном освещении и высокая разрешающая способность пластин.
Однако, несмотря на совместимость некоторых термальных пластин с проявочными процессорами и химией для традиционных пластин, каждый поставщик предлагает свои реактивы и рекомендует пользоваться специализированной проявочной машиной, и делается это не для того, чтобы увеличить доходы продавца технологии, а для достижения высоких скоростей и качества изготовления форм. Следует иметь в виду, что из-за малой толщины печатного слоя при проявлении пластин Agfa Thermostar в традиционном процессоре печатающие элементы могут быть смыты щеточным валиком, используемым для проявки обычных пластин. Кроме того, обычный проявитель характеризуется слишком высокой для пластин Agfa Thermostar активностью.
Пожалуй, самым главным недостатком некоторых термальных пластин является их малая тиражестойкость всего 100-150 тыс. оттисков. Повысить тиражестойкость формы иногда можно путем ее обжига в специальной печи, но она, как известно, стоит немалых денег и потребляет довольно много энергии.
Серебросодержащие пластины
Пластины на основе галогенидов серебра можно назвать самыми первыми среди формных материалов для технологии прямого экспонирования форм. Такие материалы были разработаны компаниями Agfa и DuPont и предназначались для экспонирования красным и зеленым лазерами. В настоящее же время вследствие появления недорогих и долговечных фиолетовых лазеров серебросодержащие пластины переживают второе рождение.
Принцип образования печатающих элементов на серебросодержащих пластинах Agfa Lithostar Ultra V называется «обращаемым диффузионным переносом». Несмотря на сложное название, процесс достаточно прост и в своих общих чертах не отличается от стандартного фотографического негативного процесса. На этапе экспонирования будущие пробельные элементы засвечиваются, серебросодержащие вещества активируются и затем с помощью проявителя фиксируются в эмульсии, а на незасвеченных местах будущих печатающих элементов серебро под действием проявителя освобождается и диффундирует сквозь специальный слой к подложке из анодированного алюминия. Металлическое серебро образует тонкий слой в губчатом слое оксида, который приобретает гидрофобные свойства. Далее производится смывка всех слоев с последующим гуммированием формы специальным составом, улучшающим олеофильные свойства серебряных печатающих элементов.
![]() |
![]() |
Сравнение процессов изготовления пластин разных типов
Современные технологические процессы развиваются в сторону сокращения количества операций и общего их упрощения. Благодаря достижениям в сферах точной механики, оптики и программирования, большинство операций формного процесса отличаются очень высокой стабильностью. Исключение составляет лишь химическая обработка, которая является самым критичным участком всего процесса изготовления печатных форм. При этом стоимость оборудования для проявки составляет порядка 10% стоимости современного формного участка.
Что касается проявки, то термальные, полимерные и серебросодержащие материалы обрабатываются по-разному. И если на серебряные материалы процесс проявления влияет сравнительно слабо, то качество термальных и фотополимерных пластин компании Agfa зависит от него достаточно сильно. Собственно, в этом и состоит большой плюс «серебряной» технологии. Какой толк в том, что экспонирующее устройство может нарисовать самую жесткую точку на пластине, если проявочная машина потом все равно стравит все острые углы, да еще и подтравит печатающий элемент под маской как минимум на расстояние, равное толщине печатающего элемента (порядка 2 мкм)?
Почему же серебряные пластины гораздо менее чувствительны к процессу проявления по сравнению с остальными типами пластин? Причина этого заключается в различной структуре слоев и в ином способе формирования печатающих элементов. На рис. 1 и 2 показана структура серебросодержащих пластин Agfa Lithostar Ultra V и термальных пластин Agfa Thermostar. Несмотря на более сложную структуру слоев серебросодержащей пластины, печатающие элементы на ней формируются с большей точностью, чем на термальной.
рис.1
Чтобы понять суть этого явления, нам придется рассмотреть, хотя и несколько упрощенно, процессы образования печатающих элементов на пластинах. На рис. 3 представлена схема образования печатающего элемента на термальной пластине Thermostar. Легко видеть, что, благодаря двоичному характеру экспонирования масочного слоя, мы получаем маску очень высокого качества для травления печатающих элементов. Дальнейший процесс обработки пластины Thermostar основан на различных скоростях травления неэкспонированного масочного слоя и находящегося под ним слоя, из которого формируются печатающие элементы. Казалось бы, после травления печатающие элементы должны точно повторять рисунок маски, однако процесс травления идет одинаково во всех направлениях, а не только в направлении, перпендикулярном поверхности пластины. Таким образом, размеры печатающих элементов уменьшаются на величину, сравнимую с толщиной эмульсионного слоя на пластине, то есть на 2-4 мкм. При этом форма печатающего элемента практически не изменяется, так как травление идет одинаково по всей границе.
рис. 2 | рис. 3 |
Поскольку конечным результатом для нас является отпечаток, оценим влияние такого изменения размера. Если диаметр точки при стохастическом растрировании составляет 21 мкм, то по каждому из направлений он уменьшится на от 4-8 мкм, или на 30-60% от площади минимального печатающего элемента. Безусловно, существуют методы для компенсации эффекта бокового подтравливания печатающего элемента под маской, однако, вследствие особенностей проявочных процессоров, изменение размеров печатающих элементов по ширине и длине формы колеблется в достаточно больших пределах.
На рис. 4 изображен процесс получения печатающего элемента на негативной фотополимерной пластине, требующей предварительного нагрева. Несмотря на кажущуюся простоту и однозначность представленных на схеме этапов, практически на каждом из них происходит отклонение размера точки в ту или иную сторону. В наибольшей степени размеры будущих печатающих элементов дестабилизируются из-за предварительного нагрева, поскольку разные части пластины нагреваются по-разному. Происходит это по той причине, что перед-няя часть пластины нагревается исключительно за счет воздействия нагревательных элементов, а задняя еще и за счет теплопроводности алюминиевой подложки, которая начинает нагревать фотополимерный слой еще до его поступления в печку. Таким образом, реакция полимеризации протекает неравномерно по длине пластины, и особенно сильно этот дефект проявляется на пластинах панорамного формата, подаваемых в проявку узкой стороной.
На рис. 5 показаны этапы формирования печатающих элементов на серебросодержащих пластинах Agfa Lithostar. Очевидно, что единственным этапом, влияющим на размер печатающего элемента после экспонирования, является этап диффузии. Действительно, процесс диффузии, как и процесс травления, идет с одинаковой скоростью во всех направлениях, однако в структуру покрытия пластин Agfa Lithostar вводится барьерный слой толщиной в доли микрометра, сквозь который проникают только те частицы серебра, которые входят в него под углом близким к прямому. Поэтому изменение размеров печатающего элемента если и происходит, то не превышает толщины барьерного слоя. Все остальные операции по обработке серебросодержащей пластины сводятся к полному удалению всех слоев, за исключением печатающих элементов, состоящих из металлического серебра.
рис. 4 | рис. 5 |
Отсюда следует, что при правильной калибровке экспонирующих устройств как с фиолетовым, так и с ИК-лазером мы получаем одинаковое качество экспонирования, но разную степень зависимости качества формы от дальнейшей химической обработки. Собственно, подобная нетребовательность серебросодержащих пластин к химической обработке и служит причиной их популярности в типо-графиях с машинами малого и среднего формата, когда, помимо хороших технических показателей, важна еще и простота технологии, а также стабильность результатов.
![]() |
![]() |
Из российского опыта внедрения CtP
Увеличение количества систем прямого экспонирования офсетных форм на полиграфических предприятиях России, а также беседы с пользователями оборудования и расходных материалов для CtP убедили автора этой статьи в важности некоторых аспектов, которые следует учитывать при выборе технологии вывода форм. Российская действительность привносит во внедрение технологии прямого экспонирования форм дополнительные трудности. Многие видят в этом свой, особый путь, однако обычно эти трудности гораздо правильнее будет объяснить отсутствием должной технологической дисциплины и систематизированного обучения персонала.
Очевидно, что новые технологические процессы на новом предприятии будут запускаться не так, как на предприятии, где одна технология заменяется другой (в нашем случае традиционная пленочная на CtP). Во вновь образуемых типографиях, как правило, помещения уже спроектированы для установки в них оборудования прямого вывода форм, тогда как модернизируемое производ-ство это старые цеха, пыльные помещения и персонал, не готовый без специального обучения, эксплуатировать новое оборудование.
Поясним это на конкретных примерах. В одной типо-графии было установлено термальное экспонирующее устройство, но выведенные на нем пластины Agfa Thermostar не выдерживали даже сотни оттисков в печатной машине. В чем же дело? Ведь машины в этой типографии верой и правдой служат уже второй десяток лет и тиражестойкость форм, изготовленных из обычных пластин, соответствовала заявленным характеристиками. Оказалось, что валики системы увлажнения имели на своей поверхности небольшие абразивные отложения солей кальция, которые стирали тонкое покрытие пластин Thermostar (толщина печатающих элементов на этих пластинах всего 2 мкм, тогда как на обычных пластинах порядка 8 мкм). Можно ли считать подобные обстоятельства дефектом производственного процесса? Вряд ли, поскольку на обычных пластинах все работало вполне нормально просто новые материалы предъявляют более строгие требования к чистоте печатной машины.
Другой случай, произошедший в одной из московских типографий, помог нам диагностировать неисправность в печатной машине. Так получилось, что первую форму, изготовленную по новой технологии, установили только на одну секцию, и при тестовой печати все оттиски вышли дефектными. А когда на все секции установили такие формы, то дефект проявлялся только на одной секции на той самой, куда по иронии судьбы установили первую форму, произведенную по технологии CtP в этой типографии. Тщательное обследование секции вместе с инженерами компании производителя печатной машины позволило выявить механический дефект печатной секции, практически незаметный при работе с обычными пластинами.
![]() |
![]() |