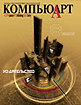
Стабильность деформационных свойств офсетных резинотканевых пластин (ОРТП) в период печати
Настоящая статья является продолжением результатов исследований, опубликованных в №1 КомпьюАрт за 2000 год. Там, в частности, отмечалось, что деформационные характеристики ОРТП, измеренные в свободном (не натянутом) состоянии, существенно отличаются от тех же характеристик, полученных в предварительно напряженном состоянии, например, после натяжения пластины с определенным усилием непосредственно на офсетном цилиндре, то есть в условиях, максимально приближенных к реальному процессу печати.
Исследования ОРТПН типов ПМН-1 и ПМН-2 при сжатии образцов 1, 2, 3 и 4 в свободном (не натянутом) состоянии не позволили определить влияние природы волокон офсетных тканей на их деформационные свойства (как показано в таблице). По показателям свойств ОРТПН, полученным в этих условиях, видно, что природа волокон офсетных тканей незначительно влияет на деформационные свойства пластин типа ПМН-1, содержащих один микропористый слой и четырехслойную резинотканевую основу, и практически не отражается на свойствах пластин типа ПМН-2, имеющих два микропористых слоя и трехслойную резинотканевую основу. И только применение в процессе исследования свойств ОРТП печатных установок, оснащенных тензометрической аппаратурой и обеспечивающих условия нагружения пластин, близкие к реальным условиям эксплуатации офсетных декелей в печатной машине, позволило не только получить их реальные характеристики при сжатии и растяжении, но и определить оптимальные свойства применяемых офсетных тканей и место расположения каждой из них в трех- или четырехслойной конструкции офсетной пластины.
Однако механизм натяжения ОРТП на офсетном цилиндре современных печатных машин не обеспечивает в полной мере стабильные условия офсетного печатного процесса, так как не компенсирует падения усилия натяжения пластины и величины давления в процессе печатания, что вызывает образование волны и снижение идентичности печатных оттисков.
Основной характеристикой ОРТП является зависимость давления от деформации сжатия р = f(e). Диаграмма сжатия позволяет определить максимальную по ширине полосы контакта деформацию для достижения технологически необходимого давления и оценить интервалы колебаний этого давления в зависимости от геометрических отклонений от номинальных размеров диаметров цилиндров, печатной формы, бумаги и самой пластины.
Предварительно напряженное состояние ОРТП на цилиндре создается уже при ее натяжении, которое возможно осуществить двумя методами.
При первом, традиционном методе, при котором пластина натягивается с заданным усилием и деформируется на определенную величину, эта деформация остается неизменной в процессе печатания, в то время как давление падает. При втором, новом методе усилие предварительно натянутой пластины сохраняется практически неизменным в процессе печатания тиража, а ее деформация несколько увеличивается.
Первый случай характеризует условия релаксации материала, вследствие чего напряжения в нем существенно снижаются, что видоизменяет его начальную характеристику сжатия. В связи с этим изменяются условия печатного контакта: падает величина необходимого давления, при которой уже не обеспечивается идентичность оттисков, что требует периодического подтягивания пластины до начального усилия и увеличения толщины декеля в офсетных машинах.
Во втором случае напряжение в материале сохраняется практически неизменным и в соответствии с условиями ползучести требуется уменьшение зазоров между цилиндрами в печатной паре. При этом предварительно напряженное состояние ОРТП сохраняется постоянным, что и обусловливает стабильность начальных характеристик материала на протяжении многих циклов нагружения, пока не начнут проявляться накапливающиеся в нем усталостные изменения, являющиеся первыми признаками его разрушения.
Проиллюстрируем эти соображения результатами экспериментов, в которых использовались российские офсетные резинотканевые пластины нового поколения (ОРТПН). На рис. 1 для четырех видов ОРТПН представлены экспериментальные зависимости снижения предварительно созданного усилия натяжения (q0 = 120 H/см) в зависимости от числа циклов его приработки. Пластины ПМН-2 (образец № 1) и ПМН-1 (образец № 3) состояли из тканей на основе смешанных (синтетических + хлопчатобумажных) волокон, пластины ПМН-2 (образец № 2) и ПМН-1 (образец № 4) были изготовлены их хлопчатобумажных офсетных тканей. Натяжение пластин на цилиндре осуществлялось жестким винтовым приспособлением (по принципиальной схеме, применяемой в современных машинах) через кольцо-динамометр (5), на которое наклеивались тензорезисторы для оценки (через усилительную электроаппаратуру) величины усилия. Приработка осуществлялась на экспериментальном стенде при скорости вращения цилиндров n = 500 циклов/мин. Диаметры формного и офсетного цилиндров одинаковы и составляли 160 мм. Благодаря специальной конструкции офсетного цилиндра удалось обеспечить между цилиндрами фрикционную связь и исключить влияние зубчатой передачи. Начальная максимальная деформация сжатия пластины в зоне контакта составляла 0,2 мм. Начальное усилие натяжения для всех образцов ОРТПН было одинаковым и составляло q0 = 120 H/см. Уже в начальный период , после 100 циклов нагружения для пластины ПМН-2 (образец № 2) усилие натяжения уменьшилось на 28% , а для пластины МПН-1 (образец № 3) — на 58%. Далее также наблюдался спад напряжений, хотя менее интенсивный, и продолжался даже после 10 000 циклов нагружения (что соответствует 5000 оборотов на машине вследствие двухразового сжатия за цикл).
Уместно отметить, что для пластины ПМН-2 (образец № 2), благодаря лучшим свойствам хлопчатобумажных волокон имеет место менее интенсивный спад напряжений и стабилизация свойств декеля наступает практически после 2000 циклов нагружения. Ниже будет показано, что постоянное падение напряжения при растяжении будет изменять характеристики пластины и при сжатии.
На рис. 2 для тех же ОРТП представлены экспериментальные зависимости удлинения (Dl) пластины в зависимости от числа циклов сжатия. Предварительное натяжение всех пластин, как и в первом случае, составляло q0 = 120 H/см и сохранялось примерно на постоянном уровне благодаря соответственно подобранной характеристике пружин (5). Таким образом, графики в полной мере отражают картину ползучести исследованных пластин, находящихся в рабочем (натянутом) состоянии и сопровождаемых циклическими нагружениями при сжатии. Как и в предыдущем случае, наиболее интенсивное удлинение наблюдается в первые 500 циклов нагружения (85-90%). Относительное удлинение после 10 000 циклов нагружения для рассматриваемых пластин составило от 0,32 до 0,65%. Наименьшее удлинение и наиболее короткий период стабилизации — у пластин типа ПМН-2 (образец №2).
На рис. 3 для пластин типа ПМН-2 (образцы № 1 и № 2) представлены экспериментальные графики изменения их толщины по окружности облегания поверхности цилиндра после приработки (10 000 циклов нагружения) для двух методов натяжения пластин: 1 и 2 — при жесткой, традиционной (рис. 1) фиксации величины деформации, 1’ и 2’ — при натяжении через пружину (рис. 2), обеспечивающую постоянное усилие в процессе приработки. Начальная толщина пластин в свободном состоянии составляла d1 = 1,98 мм и d2 = 1,99 мм. Отклонение от начального значения толщины пластины по окружности цилиндра измерялось индикатором часового типа, снабженным опорной насадкой.
Рассматривая представленные зависимости, отмечаем следующее:
-
колебания толщины по окружности цилиндра больше для пластин, натягиваемых механизмом с жесткой, традиционной фиксацией деформации, чем для тех же пластин, натягиваемых механизмом, обеспечивающим постоянство силы натяжения.
-
при одностороннем натяжении, вследствие трения (f) между поверхностями пластины и цилиндра, величина натяжения (qi) по мере увеличения угла обхвата (a) уменьшается ( qi = q0e-f), а его толщина соответственно увеличивается. Последнее убеждает в целесообразности двухстороннего натяжения, которое может быть реализовано в новом механизме натяжения ОРТП. Повышенный перепад их толщины, достигающий 0,095 мм, не обеспечивает одинакового давления по направлению скорости печатания и вследствие спада напряжений может привести к образованию опережающей волны. Это и объясняет картину графиков на рис. 1 и 2. Очевидно также, что это явление будет отрицательно влиять на качество печати. В случае применения нового метода натяжения пластин, при одностороннем их натяжении, это явление (образование волны) также будет иметь место, но в значительно меньшей степени.
На примере рассмотренных выше двух наиболее стабильных образцов ОРТПН типа ПМН-2 проанализируем влияние двух методов натяжения на диаграммы сжатия. На рис. 4 представлена зависимость d= f (lm) для пластин ПМН-2 (образцы № 1 и № 2), полученная после их приработки (в динамических условиях на стенде после 10 000 циклов нагружения) непосредственно на офсетном цилиндре: 1 и 2 — при жестком креплении пластины после натяжения, 1’ и 2’ — при упругом креплении q0 = const.
Как и следовало ожидать, диаграммы сжатия 1 и 2 , вследствие ослабления натяжения (и соответственно спада напряжения) являются более «мягкими» по сравнению с диаграммами 1’ и 2’, полученными после приработки пластин при постоянном усилии натяжения.
Однако обращает на себя внимание сравнительно незначительное различие диаграмм 2 и 2’, что объясняется и конструкцией, и свойствами резинотканевой основы, состоящей из хлопчатобумажных тканей пластин типа ПМН-2 (образец № 2), релаксация напряжений в которой происходит менее интенсивно и значительно быстрее наступает период стабилизации.
Подытоживая изложенное, констатируем:
-
для натяжения ОРТП целесообразно применение механизма, обеспечивающего постоянное натяжение пластины в течение всего периода печатания. В частности, подобные устройства могут быть реализованы по АС СССР № 1730794;
-
большая стабильность деформационных свойств ОРТП обеспечивается менее релаксируемыми материалами, входящими в состав пластин. Из шести исследованных нами типов пластин лучшими характеристиками обладает ОРТПН типа ПМН-2 (образец №2), что объясняется лучшими свойствами хлопчатобумажных волокон по сравнению с синтетическими и более совершенной технологией обработки офсетных тканей на их основе;
-
введение в конструкцию механизма натяжения ОРТП на офсетном цилиндре печатных машин нового устройства, обеспечивающего постоянное натяжение офсетного декеля, значительно повысит стабильность процесса печатания и качество печатной продукции, создает оптимальные условия эксплуатации ОРТП, повысит их тиражестойкость;
-
исключительно важное значение приобретает использование нового устройства для натяжения ОРТП, особенно с двухсторонним натяжением, при разработке новых декельных материалов для печатных машин: это позволяет не только значительно сократить время разработки, но и повысить технический уровень новых материалов.
КомпьюАрт 8'2000