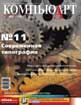
Лицо и маска увлажнения в офсетной печати
Увлажнение печатной формы в офсетной печати
Увлажняющий раствор, его показатели и состав
Взаимодействие противоположностей создает технологические процессы
Основные показатели увлажняющего раствора
Электропроводность увлажняющего раствора
Поверхностно-активные вещества (ПАВ)
Эмульгирование краски в процессе печати
Проблемы, возникающие при нарушении баланса «краска — вода»
О «мелочах», на которые стоит вовремя обращать внимание
Увлажнение печатной формы в офсетной печати
Ни для кого не секрет, что в процессе печатания тиража самые большие проблемы, связанные с качеством печатной продукции при офсетной печати, возникают из-за нарушения баланса «краска — вода» («печатная краска – увлажняющий раствор – запечатываемый материал»).
Процесс печати офсетным способом зависит от того, насколько устойчиво, равномерно и непрерывно смачиваются увлажняющим раствором пробельные элементы печатной формы, а печатающие — краской и установлен ли оптимальный баланс «краска — вода».
Для того, чтобы изображение на печатной форме было устойчивым, предварительно необходимо нанести на нее увлажняющий раствор. Эта технологическая операция производится с помощью увлажняющего аппарата, который должен обеспечивать равномерную и достаточную подачу увлажняющего раствора на печатную форму в процессе печатания. Вроде бы никакой сложности в этом и нет. Однако сложность здесь кроется в том, что недостаточное увлажнение приводит к нарушению гидрофильности пробельных элементов и, как следствие, к тенению печатной формы. Результатом же чрезмерного увлажнения являются разводы на оттисках, бледная малоконтрастная печать, неравномерность наката краски, отмарывание, а также увеличение времени сушки оттисков и пр.
Все эти нарушения связаны с составом и режимом нанесения увлажняющего раствора и с работой увлажняющего аппарата. И все они являются частью одной большой проблемы офсетной печати — проблемы баланса «краска — вода» и, в конечном счете, приводят к одному и тому же: получению некачественной продукции.
Для решения вышеуказанной проблемы необходимо прежде всего тщательно изучить составляющие печатного процесса и их взаимодействие.
Итак, назовем «участников» печатного процесса: увлажняющий раствор, печатная краска, печатная форма и запечатываемый материал, и начнем разговор с самого главного — увлажняющего раствора.
![]() |
![]() |
Увлажняющий раствор, его показатели и состав
Увлажняющий раствор представляет собой слабокислый или слабощелочной электролит. Водопроводная вода как увлажняющий раствор имеет относительно низкую эффективность, поэтому на практике при составлении увлажняющего раствора применяют различные многокомпонентные добавки.
Рекомендуемые для применения в процессе печатания увлажняющие растворы включают следующие компоненты:
- слабые кислоты и их соли (например, ортофосфорная кислота и натрий фосфорнокислый двузамещенный, лимонная, щавелевая кислота и их соли);
- вещество, предотвращающее коррозию, — ингибитор коррозии (например, нитрит натрия);
- высокомолекулярный гидрофильный коллоид в небольшой концентрации (карбоксилметилцеллюлоза или сополимер полиакриламида).
От состава и от рабочих свойств применяемого увлажняющего раствора во многом зависят устойчивость и стабильность гидрофильных свойств пробельных элементов печатной формы. Эти свойства могут быть нарушены в результате износа пробельных элементов формы и в первую очередь из-за разрушения пленок на их поверхности, созданных в процессе гидрофилизации. Увлажняющий раствор может оказывать существенное влияние и на поведение печатающих элементов, поскольку он разрушает адсорбционную олеофильную пленку, являющуюся их основой.
![]() |
![]() |
Взаимодействие противоположностей создает технологические процессы
К увлажняющему раствору предъявляются следующие требования:
- способность хорошо смачивать гидрофильные пробельные элементы и обеспечивать постоянство их свойств в процессе печатания;
- невозможность отрицательно влиять на гидрофобные слои печатающих элементов, не вызывать эмульгирование печатных красок и не изменять их спектральные и структурно-механические характеристики, не вызывать коррозию металлов формы и деталей печатной машины;
- неагрессивность по отношению к бумаге и неспособность вызывать изменение свойств ее поверхности — смачиваемости, отсутствие запаха и цвета, а также токсичных веществ.
Пленка увлажняющего раствора, наносимая на поверхность пробельных элементов печатной формы, должна иметь определенную толщину, обеспечивающую устойчивость пробельных элементов в течение всего периода печатания тиража. Толщина пленки зависит от структуры (геометрии поверхности) и материала печатной формы: для биметаллических форм она составляет 0,7-1,1 мкм, для монометаллических — до 2 мкм.
Следует подчеркнуть, что рабочие характеристики и параметры увлажняющего раствора стабилизирует постоянный температурный режим. Температуру увлажняющего раствора в корыте увлажняющего аппарата рекомендуется поддерживать в пределах 12-14 °С, конечно, если это возможно.
Большое значение имеет не только количество подаваемого увлажняющего раствора, но и качество воды и добавок, используемых при его составлении.
![]() |
![]() |
Основные показатели увлажняющего раствора
Основными показателями, которые зависят от состава увлажняющего раствора и определяют его эксплуатационные качества, являются:
- кислотность (рис. 1);
- жесткость;
- электропроводность.
Рассмотрим эти показатели и их влияние на рабочие свойства увлажняющего раствора.
![]() |
![]() |
Кислотность (или рН) увлажняющего раствора
Водородный показатель (рН) [power of hydrogen] — это параметр, характеризующий концентрацию ионов водорода в растворе, то есть обозначающий степень его щелочности или кислотности. Показатель рН может иметь значения от 0 до 14. Раствор с рН, равным 7, является нейтральным, ниже 7 — кислым, выше — щелочным.
На величину рН увлажняющего раствора в процессе печатания оказывает влияние коррозия металла увлажняющего аппарата и применяемые при печатании материалы — бумага, картон, фольга, различные виды красок и добавок к ним.
Показатели рН увлажняющего раствора и бумаги имеют решающее значение для стабильности процесса офсетной печати. Величину рН увлажняющего раствора следует контролировать при помощи лакмусовых бумажек или электронного прибора как при подготовке к заливке увлажняющего раствора в печатную машину, так и в процессе печатания тиража. Кислотность бумаги проверяют в лабораторных условиях при получении новых партий.
При оценке рабочих свойств увлажняющего раствора следует учитывать, что наиболее благоприятный диапазон величин рН — от 4,8 до 5,5 (рис. 1).
При рН менее 4,8:
- разрушается гидрофильная пленка на пробельных элементах печатной формы, что вызывает тенение;
- замедляется закрепление краски на оттисках из-за нарушения процесса ее окислительной полимеризации, что может вызвать отмарывание в процессе печати;
- снижается прочность на истирание красочной пленки на оттиске;
- оголяются металлические раскатные цилиндры красочного аппарата из-за снижения липкости краски, что нарушает равномерность ее подачи и ведет к непропечатке мелких деталей изображения на оттиске.
При рН более 5,5:
- происходит «омыление» печатной краски (появляется сероватый оттенок на оттиске);
- печатная краска эмульгирует и наслаивается на валиках красочного аппарата, происходит тенение печатной формы в процессе печати;
- разрушаются печатающие элементы формы, что приводит к снижению ее тиражестойкости и необходимости замены в процессе печати тиража.
![]() |
![]() |
Жесткость воды
Наряду с величиной рН увлажняющего раствора печатник должен обращать внимание и на жесткость воды (dH — показатель жесткости), используемой для приготовления увлажняющего раствора. Жесткость воды зависит от уровня содержания в ней солей кальция и магния. Различают несколько степеней жесткости (по dH):
- ниже 4 — очень мягкая;
- 4-8 — мягкая;
- 8-12 — среднежесткая;
- 12-18 — довольно жесткая;
- 18-30 — жесткая;
- свыше 30 — очень жесткая.
Оптимальное значение показателя жесткости воды, применяемой для изготовления увлажняющего раствора, варьируется от 5 до 12. При dH, не соответствующем указанным параметрам, в процессе печати тиража могут возникнуть следующие проблемы:
- при показателе жесткости меньше 5 увлажняющий раствор «забирает» недостающие соли из бумаги и печатной краски, что вызывает плохое закрепление краски на оттиске;
- при показателе жесткости больше 12 на валиках, офсетном полотне, печатной форме образуется нерастворимый известковый осадок, что приводит к нарушению печатного процесса. Кроме того, соли кальция и магния взаимодействуют с жирными кислотами, содержащимися в печатных красках (происходит «омыление») и жирный слой оседает на офсетной форме, накатных и увлажняющих валиках, вызывая тенение в процессе печати тиража.
Жесткость измеряется довольно просто при помощи специальных индикаторных палочек. При очень жесткой воде ее рекомендуется смягчать или полностью обессоливать.
![]() |
![]() |
Электропроводность увлажняющего раствора
Электропроводность увлажняющего раствора взаимосвязана с параметрами рН и dH. Она характеризует содержание в нем солей и различных добавок. Электропроводность водопроводной воды обычно колеблется от 300 до 500 мкСм (микросименсов), рабочая электропроводность увлажняющего раствора должна быть в пределах от 800 до 1500 мкСм.
При электропроводности меньше 800 мкСм увлажняющий раствор начинает «забирать» соли из печатной краски и бумаги, что вызывает плохое закрепление краски на оттиске. Это наблюдается и при низкой жесткости воды. Отличие заключается в том, что причиной снижения электропроводности может быть не только жесткость воды, но и количество и химический состав добавок.
При электропроводности больше 1500 мкСм соли, содержащиеся в увлажняющем растворе в избытке, взаимодействуют с печатной краской, что приводит к ее эмульгированию. Соли также могут оседать на валиках увлажняющего и красочного аппаратов печатной машины.
Факторы, определяющие состав увлажняющего раствора
Выбор состава увлажняющего раствора должен зависеть от следующих факторов:
- типа печатного оборудования. Рулонные и листовые печатные машины работают с разными скоростями и красками, что и определяет состав увлажняющего раствора;
- системы увлажнения — традиционная (с чехлами на валиках, работающая без спиртовой добавки) или спиртовая; контактная или бесконтактная. При спиртовом увлажнении машины, как правило, снабжены системой охлаждения и рециркуляции увлажняющего раствора, которая позволяет уменьшить количество спиртовой добавки и автоматически контролирует и поддерживает на заданном уровне кислотность раствора и содержание в нем спирта;
- исходного состава используемой водопроводной воды, то есть от ее жесткости и электропроводности;
- качества и состава используемых красок. Производители увлажняющих растворов указывают, для работы с какими типами красок они предназначены;
- качества, состава и впитывающей способности запечатываемых материалов;
- типа печатных форм (характеристик основы и состава копировального слоя).
![]() |
![]() |
Добавки в увлажняющий раствор
В настоящее время наряду со спиртом в увлажняющий раствор, в зависимости от его вида и от качества воды, добавляют и определенные специальные добавки. Они служат для регулирования и стабилизации величины рН, улучшения смачиваемости пробельных элементов печатной формы и ускорения процесса их гидрофилизации. Однако, и это очень важно, добавки не должны отрицательно воздействовать на закрепление печатной краски, вызывать коррозию металлов печатной формы; кроме того, они призваны препятствовать появлению в увлажняющем растворе микроорганизмов.
Добавки играют исключительно важную роль, определяя тип увлажняющего раствора и область его применения.
Добавки в увлажняющий раствор содержат комплекс веществ, стабилизирующих процесс печати:
- вещества, создающие буферные системы;
- поверхностно-активные компоненты, уменьшающие поверхностное натяжение воды (рис. 2);
- антикоррозионные вещества;
- антигрибковые вещества.
![]() |
![]() |
Буферные добавки
Все добавки, создающие буферные системы, обладают как щелочной, так и кислотной буферной емкостью, позволяющей нейтрализовать влияние кислых и щелочных веществ, содержащихся в бумаге или другом запечатываемом материале (картоне, металлизированной бумаге, фольге, многослойном самоклеящемся материале) и печатной краске. Они позволяют очень быстро достичь оптимального значения рН и удерживать его в необходимых пределах в процессе печатания тиража. Кислотность (рН) увлажняющего раствора с буферной добавкой незначительно меняется как при разбавлении, так и при добавлении небольшого количества свободной сильной кислоты или щелочи (рис. 3). Буферные добавки не могут изменить жесткость раствора, но они сводят к минимуму негативное влияние этого показателя на качество печати.
В то же время многие проблемы в офсетной печати и дефекты на оттиске возникают именно в результате неконтролируемого и чрезмерного использования добавок. Поэтому буферные добавки (как и любые другие) необходимо вводить в увлажняющий раствор в строго определенных количествах, которые всегда указываются фирмой-изготовителем. Как правило, для буферных добавок это 2-3% от увлажняющего раствора. Не исключено, что при определенных технологических условиях печатнику придется заменять одни добавки на другие. И здесь определяющее значение имеет его обучаемость, наблюдательность, заинтересованность в результате и практический опыт.
В случае передозировки буферной добавки происходит следующее:
- слишком сильно снижается поверхностное натяжение на границе вода — краска, что может вызвать эмульгирование краски;
- избыток ионов солей увлажняющего раствора взаимодействует с краской, что также вызывает эмульгирование.
При работе с металлизированными красками основные проблемы печати связаны с рабочими свойствами увлажняющего раствора, поэтому особое внимание следует обратить на увлажнение. Чтобы избежать окисления металлических пигментов (потери блеска металлизированных красок на оттиске), подача увлажняющего раствора должна быть минимальной. Для ускорения закрепления красок и сохранения их металлического блеска на оттиске рекомендуется применение ИК-сушки. Хороший результат обеспечивается при использовании качественных высокоглянцевых мелованных бумаг (рН бумаги должен быть не ниже 7,0). Существует специальная щелочная добавка, предназначенная для работы с металлизированными красками, которая увеличивает рН увлажняющего раствора до 7,1-8,0. Если же рН увлажняющего раствора меньше 7, он вступает в химическую реакцию с пигментами краски (металл + кислота), образуя соли и снижая, таким образом, интенсивность цвета краски.
![]() |
![]() |
Поверхностно-активные вещества (ПАВ)
ПАВ добавляют в увлажняющий раствор для снижения его поверхностного натяжения. Это улучшает смачивание поверхности пробельных элементов печатной формы увлажняющим раствором и в то же время уменьшает его подачу.
Молекулы ПАВ, которые можно представить в виде стерженьков, состоят из водовосприимчивых (гидрофильных) и водоотталкивающих (гидрофобных) частей. Своей гидрофильной частью они располагаются на пробельных элементах формы, смоченных увлажняющим раствором (рис. 2); молекулы, ориентированные к пробельным элементам гидрофобной частью, легко удаляются с поверхности формы и вновь переходят на накатной валик.
На печатающих элементах — наоборот: молекулы ПАВ располагаются гидрофобной частью к поверхности формы. При этом их гидрофильная часть связывает увлажняющий раствор в слое печатной краски, что может привести к эмульгированию, если концентрация ПАВ в увлажняющем растворе слишком высока. В этом случае краска начинает воспринимать увлажняющий раствор, разделение красочного слоя в процессе печатания изменяется, в результате чего происходит накапливание краски на форме и на офсетном полотне. Кроме того, при эмульгировании краски значительно снижается скорость высыхания краски на оттиске и возрастает вероятность отмарывания и перетискивания оттисков на приемном столе. Во избежание этого целесообразно вводить в увлажняющий раствор такие поверхностно-активные добавки, которые лишь незначительно снижают его поверхностное натяжение.
Чрезмерное снижение поверхностного натяжения увлажняющего раствора может привести к тенению в процессе печатания тиража: когда печатающие элементы на печатной форме закатываются краской, гидрофобные части молекул ПАВ, расположенные на поверхности пробельных элементов, склонны к восприятию печатной краски. Таким образом, пробельные элементы формы могут постепенно покрываться тонким слоем краски, которая через офсетное полотно перейдет на запечатываемый материал.
Необходимо также учитывать следующее:
- ПАВ вводятся в увлажняющий раствор в весьма ограниченном количестве. Чаще всего в качестве ПАВ используется изопропиловый спирт;
- Ранее для очистки увлажняющих валиков иногда использовался мыльный порошок. В этом случае валики увлажняющего аппарата тщательно промывались, чтобы остатки мыльного порошка, действуя в качестве ПАВ, не вызывали тенения. Используемые в настоящее время смывочные средства могут вызвать такие же проблемы, поэтому необходимо внимательно отнестись к промывке валиков после их очистки. Поверхностно-активные вещества, вводимые в увлажняющий раствор, не должны вызывать эмульгирования краски и оказывать воздействие на краску, валики и печатные формы.
В качестве ПАВ применяют изопропиловый или этиловый спирт (до 25%). Предпочтение отдают изопропиловому спирту, поскольку он медленнее испаряется и менее горюч. Вместе с тем применение спиртов может вызвать растворение некоторых пигментов краски и нарушение устойчивости печатающих элементов на форме в процессе печати тиража.
Вдобавок к относительной дороговизне, изопропиловый спирт токсичен, поэтому рабочее помещение, где он применяется, должно иметь хорошую вентиляцию. Кроме того, из-за быстрого испарения спирта увлажняющий раствор требует охлаждения, а концентрация спирта во время печатания должна контролироваться и периодически корректироваться с помощью автоматических систем. Исходя из всего вышеперечисленного применение нелетучих ПАВ является более целесообразным.
Таким образом, только оптимальное и взвешенное использование ПАВ позволяет добиться равномерного смачивания пробельных элементов печатной формы при более тонких пленках увлажняющего раствора, что является необходимым условием качественной печати и снижает до минимума вероятность возникновения проблем, связанных с отмарыванием, перетискиванием, снижением интенсивности красок, сушкой оттисков и тенением.
![]() |
![]() |
Антикоррозионные добавки
Антикоррозионные вещества (ингибиторы коррозии) уменьшают коррозию печатной формы и составных элементов печатного аппарата, взаимодействующих с увлажняющим раствором. Добавленные в небольшом количестве в коррозионно-активный раствор, эти вещества замедляют процесс разрушения поверхности металлов, с которой раствор соприкасается.
Величина рН является важной составляющей, определяющей антикоррозионные свойства увлажняющего раствора. Оптимальное значение рН увлажняющего раствора выбирают с учетом физико-химической характеристики поверхности металла, на котором создаются пробельные элементы (алюминий, никель или хром). Например, для алюминия вредны находящиеся в воде двууглекислые соли магния и кальция, которые нейтрализуются введением фосфорной кислоты, которая действует как антикоррозионная добавка.
![]() |
![]() |
Антигрибковые добавки
Содержание коллоидов в увлажняющем растворе и кислая среда способствуют появлению в системе увлажнения микроорганизмов, что крайне нежелательно.
Некоторые химические вещества обладают противомикробным действием, препятствуя развитию бактерий, водорослей и грибков, которые засоряют систему циркуляции увлажняющего раствора при длительном использовании системы увлажнения без регулярной очистки и промывки.
![]() |
![]() |
Печатная форма
При контакте увлажняющего раствора с печатной формой происходит постепенное изменение его рН, и на отдельных участках формы возникают очаги коррозии с нарушением целостности металла, в результате чего эти участки приобретают гидрофильные свойства. Таким образом, увлажняющий раствор может стать коррозионной средой, вызывающей разрушение печатающих элементов.
Уменьшению коррозии печатной формы способствует применение буферных увлажняющих растворов, состоящих из водного раствора гидрофильного коллоида, кислоты (фосфорной, лимонной, щавелевой) или ее соли и ингибитора коррозии.
![]() |
![]() |
Печатная краска
Во время печати неизбежно попадание увлажняющего раствора в краску вследствие их попеременного нанесения на печатную форму. Это приводит к смешиванию и взаимодействию краски с увлажняющим раствором, в результате чего образуется эмульсия. Этот процесс, называемый эмульгированием, особенно усиливается при большой площади печатающих элементов на форме.
![]() |
![]() |
Эмульгирование краски в процессе печати
Все растительные масла и большинство натуральных и синтетических смол, применяемых при изготовлении красок, содержат различное количество свободных жирных кислот. Они реагируют с щелочными пигментами, образуя различные по составу мыла, способствующие возникновению эмульгирования.
Образование эмульсии приводит к снижению интенсивности красок, изменению их физико-механических свойств, увеличению вязкости, вызывающему структурообразование и загустевание красок. Однако на свойства краски и качество оттиска влияет не только количество эмульгированного увлажняющего раствора, но и тип образующейся эмульсии.
В коллоидной химии различают эмульсии прямого и обратного типа в зависимости от того, что является сплошной наружной фазой эмульсии — масло или вода.
Образующаяся при взаимодействии увлажняющего раствора с краской устойчивая эмульсия типа «вода в масле», хотя и приводит к некоторым изменениям свойств краски, но не нарушает избирательного смачивания (базовое рабочее свойство печатной формы), поскольку наружной фазой, непосредственно соприкасающейся с поверхностью формы, является гидрофобное масляное связующее вещество (рис. 3). Образование такой эмульсии с содержанием увлажняющего раствора в краске от 15 до 25% считается нормой. Современные печатные машины имеют мостовой валик, который может связывать красочный и увлажняющий аппараты. Перед началом печати тиража для быстрого выхода на стабильный режим в краску вводят необходимое количество увлажняющего раствора, соединяя мостовым валиком увлажняющий и красочный аппараты.
Равновесное содержание увлажняющего раствора в краске устанавливается при печатании первых 1-3 тыс. оттисков (с мостовым валиком или без него).
Присутствие влаги в свободном состоянии или в виде эмульсии приводит к изменению физико-химических свойств краски, в частности к снижению ее растекания и повышению вязкости. Для всех красок характерно уменьшение скорости закрепления с увеличением содержания в них увлажняющего раствора.
Избыточное количество увлажняющего раствора в краске и на оттиске при пониженной температуре самого увлажняющего раствора ведет к замедлению высыхания краски на оттиске, поскольку при низкой температуре поглощаемый краской увлажняющий раствор не испаряется.
Если же при взаимодействии увлажняющего раствора с краской образуется эмульсия типа «масло в воде», то в этом случае наружной фазой является увлажняющий раствор, который хорошо воспринимается пробельными элементами, и печатная форма начинает тенить, а на оттисках появляются мелкие черные или цветные точки, хаотично расположенные на незапечатываемых участках оттиска. Происходит частичная адсорбция жирных кислот из связующего печатной краски на пробельных участках формы. Таким образом, нарушается принцип избирательного смачивания, который является базовым для способа плоской (офсетной) печати.
Для того чтобы ускорить подачу увлажняющего раствора на форму и добиться его равномерного растекания тонкой пленкой по поверхности пробельных элементов, при изготовлении увлажняющего раствора рекомендуется применение спирта, однако его передозировка может привести к возрастанию эмульгирования краски.
Для предотвращения эмульгирования в процессе печати тиража следует контролировать:
- рН увлажняющего раствора;
- его электропроводность;
- относительную влажность и температуру в печатном цехе;
- температуру увлажняющего раствора.
Очевидно, что все перечисленные факторы являются значащими и связаны с составом увлажняющего раствора или с внешними воздействиями, приводящими к его изменению.
Количество увлажняющего раствора в краске зависит от следующих факторов:
- состава увлажняющего раствора;
- металла, на котором изготовлена печатная форма (то есть от молекулярно-поверхностной природы и микрогеометрии поверхности формы, характеризующих влагоемкость). Так, например, при печатании с биметаллических форм в краске может быть до 15-25% увлажняющего раствора, с алюминиевых — до 20-25%. В последнее время в красочных аппаратах печатных машин ведущих фирм присутствует воздушный «нож» — устройство, которое способствует испарению избытка влаги в красочном аппарате. Таким образом предотвращается образование эмульсии «краска в воде»;
- природы пигмента и физико-химических свойств связующего печатной краски;
- относительной влажности воздуха в печатном цехе. Повышение влажности приводит к увеличению содержания увлажняющего раствора в краске. Это можно объяснить уменьшением скорости испарения влаги, попадающей в красочный аппарат. Оптимальная влажность воздуха в печатном цехе должна быть на уровне 55-60%. При влажности менее 40% наблюдается быстрое испарение влаги с формы, приводящее к ее тенению;
в некоторой степени — от температуры воздуха. Колебание температуры воздуха в помещении в пределах 18-30 °С не изменяет содержания влаги в краске.
На процесс увлажнения и состав увлажняющего раствора следует обратить особое внимание при работе с металлизированными красками. Из-за опасности окисления металлических пигментов (потери блеска) подача увлажняющего раствора должна быть минимальной. Кроме того, рекомендуется отказаться от кислых добавок в увлажняющий раствор и использовать специальные добавки для металлизированных красок.
![]() |
![]() |
Проблемы, возникающие при нарушении баланса «краска — вода»
Дефект оттиска в виде затеков увлажняющего раствора можно отнести к типичным и часто встречающимся дефектам на оттисках офсетной печати. Он возникает при чрезмерной подаче увлажняющего раствора на печатную форму в процессе печати тиража. До появления этого дефекта печатник, скорее всего, не обращал внимания на необходимость регулирования подачи увлажняющего раствора, хотя на печатной форме был заметен его избыток. Появление затеков на оттисках сигнализирует о невнимательном отношении печатника к увлажнению и к подаче увлажняющего раствора.
Чрезмерная подача увлажняющего раствора приводит не только к появлению затеков, но и создает ряд других проблем:
- образуется эмульсия «вода в краске», что снижает скорость высыхания краски и уменьшает ее интенсивность;
- избыток увлажняющего раствора с печатной формы попадает на красочные накатные валики, а оттуда — в печатную краску, которая начинает эмульгировать;
- возможно тенение из-за изменения свойств печатной краски, особенно при возникновении эмульсии «краска в воде»;
- может возникать перетискивание (переход печатной краски на оборотную сторону оттисков на приемном столе под воздействием веса верхних оттисков в стопе) или отмарывание (переход краски на оборотную сторону оттисков при их прохождении в машине);
- с ухудшением свойств краски снижается качество оттисков, в частности уменьшается резкость изображения;
- происходят деформации (растяжение) запечатываемого материала, что вызывает неприводку красок на оттиске.
Количество увлажняющего раствора, предназначенного для смачивания пробельных элементов и устранения возможного тенения, в процессе тиражной печати должно поддерживаться на минимальном уровне.
Печатнику следует обратить внимание и на некоторые визуальные эффекты, связанные с подачей увлажняющего раствора в процессе печатания тиража:
- при оптимальной подаче увлажняющего раствора, не содержащего спирт, поверхность печатной формы приобретает бархатистый «глянец»;
- при спиртовом увлажнении при оптимальной подаче увлажняющего раствора поверхность формы становится матовой.
![]() |
![]() |
Запечатываемый материал
Для получения хороших результатов необходимо использование качественных высокоглянцевых мелованных бумаг, при этом рН бумаги должен быть не ниже 7,0.
Однако печатание на мелованной бумаге может вызвать осложнения, связанные с тем, что в состав суспензии для мелования бумаг вводят поверхностно-активные вещества (различные смачиватели, уротропин, казеин, некаль и др.). В процессе печатания поверхность бумаги соприкасается через резинотканевую пластину с увлажняющим раствором, при этом некоторое количество ПАВ, входящего в состав суспензии для мелования бумаги, переходит в него, снижая его поверхностное натяжение и приводя к эмульгированию краски. Контроль изменения состава увлажняющего раствора проводят, как правило, измеряя специальным прибором его электропроводность, позволяет оценить количество введенной добавки.
В редких случаях, например, при печатании на невпитывающих материалах, следует отказаться от кислых добавок в увлажняющий раствор. В остальных случаях добавки следует применять осторожно, соблюдая точную дозировку и постоянно измеряя рабочие параметры увлажняющего раствора.
Печатники должны учитывать, что сиккативы, вводимые в увлажняющий раствор как добавка при печати на невпитывающих материалах, увеличивают рН увлажняющего раствора, однако его величина при этом не должна превышать 5,5.
Для получения стабильного качества и уменьшения количества дефектов наряду со стандартизацией офсетной печати в области копировальных процессов, пробной и тиражной печати необходимо разрабатывать стандарты и для процессов увлажнения. Сюда относятся автоматическое дозирование, стабилизация содержания спирта при одновременном охлаждении увлажняющего раствора, а также автоматическое дозирование добавок в увлажняющий раствор. Отсутствие стандартов делает сегодня фирменные рекомендации особенно важными. К ним следует относиться с вниманием и с пониманием применять в работе.
![]() |
![]() |
О «мелочах», на которые стоит вовремя обращать внимание
«Мелкие, незаметные явления и процессы, происходящие на каждом шагу и нами не чувствуемые по своей незначительности, накапливаясь во времени, производят самые грандиозные перевороты и изменения». Это слова философа В. Вернадского. Однако они применимы не только к жизни, но и к производственным технологиям, в частности к технологии печати.
При правильной подготовке офсетной листовой печатной машины к печатанию и хорошем качестве печатной формы весь тираж печатается без остановки машины. Перерывы в печатании тиража могут возникнуть только при смене бригады печатников или при необходимости смывки офсетного полотна и печатной формы. Даже смена стапеля в листовых печатных машинах при наличии системы «non stop» не требует остановки машины.
Процесс печатания должен проходить при минимальном увлажнении и постоянной кислотности (рН) увлажняющего раствора. Всю процедуру подготовки печатной машины к печати, получение контрольного оттиска и печатание тиража печатник проводит, контролируя и оценивая результат по изображению на оттисках и по контрольной шкале печатного процесса.
К мелочам нужно относиться со вниманием — они как сорняки: вначале едва заметны, зато потом трудно устранимы, а это приводит к браку продукции, снижению производительности и качества печати.
КомпьюАрт 11'2002